Global Metal Injection Molding in Aerospace and Military Applications Market Size, Production, Sales, Average Product Price, Market Share, Import vs Export – United States, Europe, APAC, Latin America, Middle East & Africa
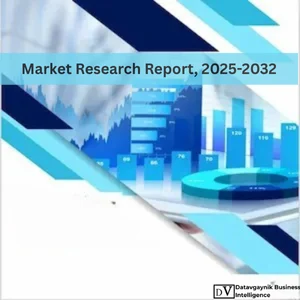
- Published 2025
- No of Pages: 120+
- 20% Customization available
Global Metal Injection Molding in Aerospace and Military Applications Market Revenue Size and Production Analysis, till 2032
Global Metal Injection Molding in Aerospace and Military Applications Market Size is expected to grow at an impressive rate during the timeframe (2024-2032). Metal Injection Molding in Aerospace and Military Applications demand is growing due to
- High Precision and Complex Geometries
- MIM allows for the production of intricate and highly precise components that would be difficult or expensive to manufacture using traditional methods.
- Aerospace and military industries often require complex, small parts with tight tolerances, making MIM an ideal solution.
- Material Versatility and Performance
- MIM can utilize a variety of metal powders, including stainless steel, titanium, and superalloys, which are essential in aerospace and military applications for their strength, durability, and resistance to extreme conditions.
- These materials are suitable for components that must endure high stress, temperature, and corrosion, meeting stringent industry standards.
- Weight Reduction
- In aerospace, reducing weight is crucial for improving fuel efficiency and overall performance. MIM enables the creation of lightweight, high-strength parts, replacing traditionally bulkier machined parts.
- For military applications, lighter components contribute to the enhanced mobility and functionality of weapons and equipment.
- Cost Efficiency
- MIM is cost-effective for producing high-volume, complex parts with minimal waste, reducing the need for expensive machining and finishing processes.
- The ability to mass-produce small and intricate components lowers overall manufacturing costs, making it attractive for aerospace and defense sectors, which often require batch production of small, precise parts.
- Enhanced Mechanical Properties
- MIM parts have excellent mechanical properties, such as high tensile strength, fatigue resistance, and hardness, which are essential for the demanding environments faced by aerospace and military components.
- These properties help in meeting rigorous performance standards and prolonging the lifespan of critical parts.
- Design Flexibility and Prototyping Capabilities
- MIM offers significant design flexibility, allowing engineers to innovate and create parts with complex shapes that are challenging to achieve with traditional manufacturing.
- It also enables rapid prototyping, allowing faster development cycles and testing of new designs, which is crucial in aerospace and military R&D projects.
- Increased Demand for Advanced Weaponry and Aerospace Components
- With the growing need for advanced and miniaturized weaponry, electronics, and unmanned systems (like drones), the demand for precise, small-scale metal components is increasing.
- The aerospace sector’s expansion, including the rise in commercial air travel and space exploration, is also driving the need for high-performance metal parts that MIM can efficiently produce.
- Compliance with Industry Standards
- MIM technology has advanced to meet stringent aerospace and military standards (such as AS9100 for aerospace quality management), making it a reliable choice for critical applications.
- Parts manufactured through MIM often undergo rigorous testing and inspection to meet the quality and safety requirements of these industries.
United States Metal Injection Molding in Aerospace and Military Applications Market Recent Developments and Business Opportunities
Key factors contributing to this growth include:
- Technological Advancements: The adoption of new alloy materials and powder metallurgy techniques has improved the quality and performance of MIM parts, making them suitable for high-stress environments typical in aerospace and military applications. The focus on reducing the weight of aircraft and military equipment has further driven the demand for these components, as MIM can produce intricate shapes that are otherwise challenging with traditional manufacturing processes.
- Increasing Use in Aerospace: MIM is increasingly utilized to manufacture parts for jet engines, landing gear, and various structural components. The demand for fuel-efficient and lightweight aircraft has pushed manufacturers to integrate MIM parts that offer both reduced weight and high durability, contributing to the growing market share of this technology in the aerospace industry.
- Military Applications: In the military sector, MIM components are being adopted for firearms, ammunition, and complex mechanical parts in defense systems due to their high strength-to-weight ratio and precision. The use of MIM has also expanded into the production of various tactical and navigation components that require fine detailing and durability.
- Market Expansion and Investments: The U.S. market is seeing increased investments in research and development aimed at enhancing MIM processes and expanding their applications. Companies are focusing on digitalization, incorporating Industry 4.0 technologies, and enhancing additive manufacturing techniques to further refine the capabilities of MIM.
Europe Metal Injection Molding in Aerospace and Military Applications Market Recent Developments and Business Opportunities by Country
Germany has significantly increased its defense spending, including large-scale contracts for weapon systems and military vehicles. This surge in investment is catalyzing the demand for advanced manufacturing techniques like MIM, known for producing complex, durable parts with high precision, making it ideal for aerospace and military applications. The country’s established industrial base and focus on precision engineering further bolster this trend.
In France, ongoing military modernization efforts are generating new opportunities for MIM. The country is investing heavily in upgrading its defense systems, including the procurement of advanced weaponry and aircraft. This emphasis on high-quality, lightweight components is driving demand for innovative MIM solutions, particularly in aerospace, where weight reduction and performance are critical factors.
The UK also plays a pivotal role in the European MIM market, particularly in aerospace. The nation’s strong aerospace industry, with leading companies like Rolls-Royce and BAE Systems, is increasingly incorporating MIM to produce intricate components for aircraft engines and other critical systems. The focus is on enhancing fuel efficiency and reducing manufacturing costs, making MIM an attractive solution due to its ability to produce lightweight, high-strength parts at scale.
Middle East Metal Injection Molding in Aerospace and Military Applications Market Recent Developments and Business Opportunities by Country
The Middle East market for Metal Injection Molding (MIM) in aerospace and military applications is seeing steady growth, driven by increasing demand for high-precision, lightweight metal components. This demand is influenced by regional defense sector expansions, especially in countries like Saudi Arabia and the UAE. These nations are investing heavily in military and aerospace projects, with a focus on adopting advanced manufacturing technologies such as MIM to enhance the performance and durability of components.
In Saudi Arabia, the MIM market is benefiting from the country’s Vision 2030 initiative, which aims to localize military manufacturing. The adoption of MIM technology is gaining traction due to its ability to produce complex, small, and lightweight parts, which are crucial in military applications like firearms and aerospace components. There is also a growing emphasis on reducing reliance on imports by developing local manufacturing capabilities, which is providing new business opportunities for MIM suppliers and manufacturer.
The UAE is also witnessing similar trends, with significant investments in the aerospace sector. The country is focusing on diversifying its economy and establishing itself as a hub for advanced manufacturing. The implementation of MIM in producing critical aerospace components is expected to increase due to its cost-effectiveness and precision capabilities, which are essential for maintaining the high standards required in aerospace engineering.
Asia Pacific Metal Injection Molding in Aerospace and Military Applications Market Recent Developments and Business Opportunities by Country
China stands out as a dominant player in the region, focusing heavily on MIM for both aerospace and defense industries. The country is leveraging its strong manufacturing capabilities and advancements in material science to produce high-quality MIM components. Additionally, government initiatives aimed at enhancing domestic defense production are boosting the adoption of MIM technology.
In Japan, the focus has been on integrating advanced MIM processes to meet the stringent requirements of the aerospace sector. Japanese manufacturers are known for their emphasis on precision and innovation, often collaborating with aerospace firms to create bespoke components that meet exacting standards. The market in Japan is expected to grow further as it continues to embrace new materials and technologies to increase efficiency and performance.
India has been expanding its MIM capabilities, especially in military applications, to reduce dependence on imports. The “Make in India” initiative has encouraged local manufacturers to adopt MIM technologies for producing parts used in defense equipment, aircraft, and drones. This shift not only aims to enhance the self-reliance of the defense sector but also opens up new business opportunities for local and international investors.
Australia has shown a growing interest in adopting MIM technology, particularly for aerospace applications. The country’s focus is on increasing the performance of aircraft components while reducing weight, making MIM a suitable choice. Australia’s efforts in modernizing its defense capabilities and investing in advanced manufacturing technologies have positioned it as a promising market for MIM.
Global Metal Injection Molding in Aerospace and Military Applications Analysis by Market Segmentation
1. Material Segmentation
- Stainless Steel and Alloy Steel: These materials are commonly used for MIM parts due to their strength, corrosion resistance, and durability, making them suitable for components like brackets and structural parts.
- Titanium Alloys: With excellent strength-to-weight ratios, titanium alloys are increasingly used in aerospace for lightweight components.
- High-Temperature Alloys: These are utilized for parts requiring enhanced performance in extreme conditions, such as in jet engines or high-heat environments.
2. End-Use Industry Segmentation
- Aerospace Sector: The aerospace industry employs MIM for producing small, complex parts like connectors, fasteners, and brackets, focusing on weight reduction and material efficiency. The growing demand for lightweight components in aircraft to improve fuel efficiency is a key driver.
- Military Applications: The military sector uses MIM to manufacture precise and durable parts for weapons systems, communication devices, and tactical equipment. The demand is propelled by the need for high-performance materials and intricate designs that enhance reliability in critical applications.
3. Application Segmentation
- Structural Components: MIM is used to manufacture load-bearing components in aerospace and military devices, where material strength and precision are paramount.
- Electronic Components: MIM is increasingly adopted for producing miniature parts in electronic systems, such as connectors and housings, where complex geometries are needed.
- Engine Parts: The method’s capability to produce high-precision, lightweight parts is valuable for engine components that require exact tolerances and high durability.
4. Regional Segmentation
- North America: The largest market due to the extensive aerospace and defense manufacturing base, with key players focusing on advanced MIM techniques to meet stringent performance standards.
- Europe: Driven by robust aerospace industries in countries like Germany and France, the region emphasizes innovation in high-strength alloys and environmentally friendly manufacturing processes.
- Asia Pacific: Growth in this region is fueled by increasing military expenditures and expanding aerospace manufacturing, particularly in China and India, where demand for advanced materials and cost-effective production solutions is rising.
- Middle East: Investments in defense and aerospace sectors, coupled with a focus on localizing parts manufacturing, are spurring the demand for MIM technologies.
Overall, the global MIM market is set to expand significantly due to the demand for lightweight, high-precision components in aerospace and military applications. Innovations in materials and process automation are expected to provide new growth opportunities while addressing environmental and supply chain challenges. The market’s forecast growth highlights the potential for companies to invest in research and development to enhance material properties and optimize production efficiency.
Metal Injection Molding in Aerospace and Military Applications Production and Import-Export Scenario
Production Trends: MIM production is concentrated in regions with advanced manufacturing capabilities like North America, Europe, and Asia-Pacific. The technology’s ability to produce intricate and small metal components cost-effectively has made it increasingly popular in the aerospace and defense sectors. The key applications include making parts for aircraft engines, missile components, and other precision hardware where high strength-to-weight ratios are critical.
Import-Export Dynamics: In recent years, the Asia-Pacific region, particularly China and Japan, has seen substantial growth in both production and export of MIM components due to lower production costs and the availability of raw materials. North America and Europe, on the other hand, are significant importers, given their strong aerospace industries’ demand for high-quality, precision parts.
Challenges in the global MIM market include high raw material costs and stringent regulations, especially for military applications. However, increasing investments in R&D and a push towards sustainable manufacturing practices are likely to boost production efficiency and trade volumes further. The emergence of new suppliers in emerging economies and collaborations between international players are also contributing to a more interconnected supply chain.
Market Scenario, Demand vs Supply, Average Product Price, Import vs Export, till 2032
- Global Metal Injection Molding in Aerospace and Military Applications Market revenue and demand by region
- Global Metal Injection Molding in Aerospace and Military Applications Market production and sales volume
- United States Metal Injection Molding in Aerospace and Military Applications Market revenue size and demand by country
- Europe Metal Injection Molding in Aerospace and Military Applications Market revenue size and demand by country
- Asia Pacific Metal Injection Molding in Aerospace and Military Applications Market revenue size and demand by country
- Middle East & Africa Metal Injection Molding in Aerospace and Military Applications Market revenue size and demand by country
- Latin America Metal Injection Molding in Aerospace and Military Applications Market revenue size and demand by
- Import-export scenario – United States, Europe, APAC, Latin America, Middle East & Africa
- Average product price – United States, Europe, APAC, Latin America, Middle East & Africa
- Market player analysis, competitive scenario, market share analysis
- Business opportunity analysis
Key questions answered in the Global Metal Injection Molding in Aerospace and Military Applications Market Analysis Report:
- What is the market size for Metal Injection Molding in Aerospace and Military Applications in United States, Europe, APAC, Middle East & Africa, Latin America?
- What is the yearly sales volume of Metal Injection Molding in Aerospace and Military Applications and how is the demand rising?
- Who are the top market players by market share, in each product segment?
- Which is the fastest growing business/ product segment?
- What should be the business strategies and Go to Market strategies?
The report covers Metal Injection Molding in Aerospace and Military Applications Market revenue, Production, Sales volume, by regions, (further split into countries):
- Asia Pacific (China, Japan, South Korea, India, Indonesia, Vietnam, Rest of APAC)
- Europe (UK, Germany, France, Italy, Spain, Benelux, Poland, Rest of Europe)
- North America (United States, Canada, Mexico)
- Latin America (Brazil, Argentina, Rest of Latin America)
- Middle East & Africa
Table of Contents:
- Product Overview and Scope of Metal Injection Molding in Aerospace and Military Applications
- Metal Injection Molding in Aerospace and Military Applications Segment Analysis by Product Category
- Global Metal Injection Molding in Aerospace and Military Applications Revenue Estimates and Forecasts (2019-2032)
- United States market size, production, sales, average price, import vs exports
- Europe market size, production, sales, average price, import vs exports
- Asia Pacific market size, production, sales, average price, import vs exports
- Latin America market size, production, sales, average price, import vs exports
- Middle East & Africa market size, production, sales, average price, import vs exports
- Metal Injection Molding in Aerospace and Military Applications Production Estimates and Forecasts (2019-2032)
- Market Competition by Manufacturers
- Global Metal Injection Molding in Aerospace and Military Applications Production by Manufacturers
- Global Metal Injection Molding in Aerospace and Military Applications Revenue Market Share by Manufacturers (2019-2023)
- Production Analysis
- Metal Injection Molding in Aerospace and Military Applications Production, Revenue, Price and Gross Margin (2019-2024)
- Metal Injection Molding in Aerospace and Military Applications Production VS Export
- Metal Injection Molding in Aerospace and Military Applications Consumption VS Import
- Consumption Analysis
- Metal Injection Molding in Aerospace and Military Applications Consumption by Region
- Metal Injection Molding in Aerospace and Military Applications Consumption by Product
- Metal Injection Molding in Aerospace and Military Applications Consumption Market Share by Product
- Global Production of Metal Injection Molding in Aerospace and Military Applications by Product (2019-2024)
- Revenue Market Share by Product (2019-2024)
- Production, Revenue, Price and Gross Margin (2019-2024)
- Metal Injection Molding in Aerospace and Military Applications Manufacturing Cost Analysis
- Metal Injection Molding in Aerospace and Military Applications Key Raw Materials Analysis
- Key Raw Materials
- Key Suppliers of Raw Materials
- Proportion of Manufacturing Cost Structure
- Metal Injection Molding in Aerospace and Military Applications Industrial Chain Analysis
- Marketing Channel, Distributors and Customers
- Metal Injection Molding in Aerospace and Military Applications Distributors List
- Metal Injection Molding in Aerospace and Military Applications Sales Partners
- Metal Injection Molding in Aerospace and Military Applications Customers List
- Production and Supply Forecast
“Every Organization is different and so are their requirements”- Datavagyanik
Companies We Work With
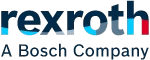
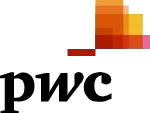
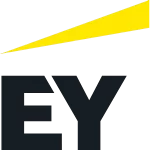
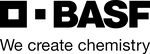
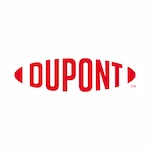

Do You Want To Boost Your Business?
drop us a line and keep in touch
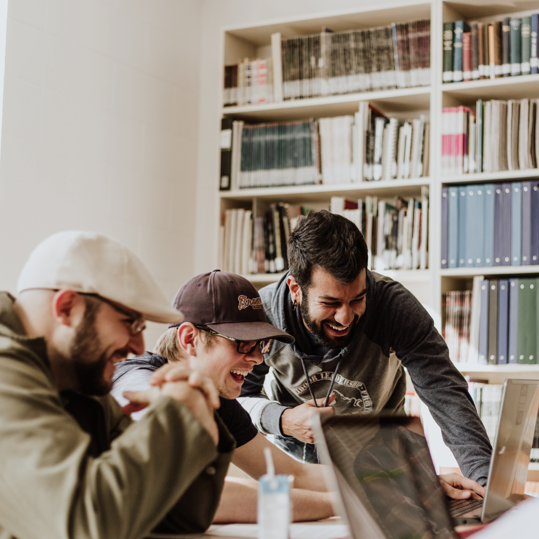