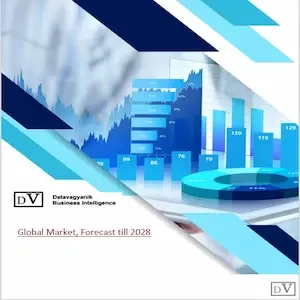
- Published 2024
- No of Pages: 200
- 20% Customization available
Global Diamond Like Carbon (DLC) Coatings Market Size, Production, Sales, Average Product Price, Market Share, Import vs Export
Global Diamond Like Carbon (DLC) Coatings Market Revenue Size and Production Analysis, till 2032
Global Diamond Like Carbon (DLC) Coatings Market Size is expected to grow at an impressive rate during the timeframe (2024-2032). Diamond Like Carbon (DLC) Coatings demand is growing due to:
- Increased Focus on Wear and Friction Reduction:
- DLC coatings provide exceptional wear resistance and a low coefficient of friction, making them ideal for applications requiring enhanced durability and efficiency.
- Industries such as automotive, aerospace, and industrial machinery rely on DLC coatings to extend component lifespan and reduce energy losses caused by friction.
- Growth of the Automotive Industry:
- Automotive manufacturers are increasingly adopting DLC coatings for engine components, such as pistons, camshafts, and fuel injectors, to reduce wear and improve fuel efficiency.
- With the rise of electric vehicles (EVs), DLC coatings are being used in drivetrains, bearings, and other components to enhance performance and reliability.
- Rising Demand in the Aerospace Sector:
- Aerospace applications benefit from DLC coatings for their lightweight, durable, and low-friction properties, which are essential for reducing maintenance costs and improving fuel efficiency in high-stress environments.
- Components such as bearings, hydraulic systems, and turbine blades utilize DLC coatings to ensure reliable performance under extreme conditions.
- Expansion of the Medical and Healthcare Sector:
- DLC coatings are increasingly used in medical devices, surgical instruments, and implants due to their biocompatibility, corrosion resistance, and durability.
- Applications include joint replacements, stents, and diagnostic tools, where smooth surfaces and resistance to wear are critical.
- Growing Adoption in Electronics and Semiconductors:
- DLC coatings are used in electronic components to protect against wear, reduce friction, and improve thermal conductivity.
- In semiconductors, DLC coatings are applied to protect precision tools and equipment from wear during the manufacturing process.
- Renewable Energy Sector Growth:
- Wind turbines, solar panels, and energy storage systems use DLC coatings to reduce wear and enhance the efficiency of moving parts exposed to harsh environmental conditions.
- The global push toward renewable energy adoption is driving demand for durable and low-maintenance coatings like DLC.
- Advancements in Tooling and Industrial Applications:
- DLC coatings are widely applied to cutting tools, molds, and industrial equipment to increase operational efficiency, extend tool life, and improve machining precision.
- Their ability to resist heat and maintain a smooth surface makes them ideal for high-performance industrial applications.
- Demand for Aesthetic and Durable Coatings:
- DLC coatings are used in consumer goods, such as watches, jewelry, and optical lenses, to provide a durable, scratch-resistant, and visually appealing finish.
- Their combination of aesthetics and functionality makes them a preferred choice for high-end products.
- Focus on Energy Efficiency and Sustainability:
- DLC coatings contribute to energy efficiency by reducing friction and wear in mechanical systems, lowering energy consumption and emissions.
- Industries are adopting these coatings to meet sustainability goals and regulatory requirements for environmental impact reduction.
- Ongoing Technological Innovations:
- Advancements in DLC coating technologies, such as hybrid or multilayer coatings, have expanded their applications across new industries.
- These innovations are addressing challenges like adhesion and performance under extreme conditions, further driving adoption.
United States Diamond Like Carbon (DLC) Coatings Market Recent Developments and Business Opportunities
The United States Diamond-Like Carbon (DLC) coatings market is experiencing robust growth, driven by increasing demand across industries such as automotive, aerospace, medical devices, industrial machinery, and electronics. Known for their exceptional wear resistance, low friction, and biocompatibility, DLC coatings are becoming integral in high-performance applications where durability and efficiency are paramount. In the automotive sector, DLC coatings are widely used for critical engine components such as pistons, camshafts, and fuel injectors to reduce friction, enhance fuel efficiency, and minimize emissions. With the rapid growth of the electric vehicle (EV) market in the U.S., the adoption of DLC coatings is accelerating for use in drivetrains, bearings, and other EV-specific components, where reducing wear and improving efficiency are essential. As automakers ramp up EV production and focus on improving energy efficiency, the demand for advanced coating technologies like DLC is expected to rise significantly.
In the aerospace industry, DLC coatings are being adopted to improve the performance and reliability of components exposed to extreme conditions, such as bearings, hydraulic systems, and turbine blades. The U.S., as a global leader in aerospace innovation and manufacturing, is investing heavily in materials that enhance fuel efficiency, reduce maintenance costs, and extend the operational lifespan of aircraft components. DLC coatings play a critical role in achieving these objectives, and their use in the defense sector further expands the market, where applications include wear-resistant coatings for military vehicles, weapons systems, and high-performance equipment.
The medical and healthcare sector in the U.S. is another major driver of DLC coatings demand. Medical devices, surgical instruments, and implants benefit from DLC coatings for their biocompatibility, corrosion resistance, and wear protection. Joint replacements, stents, and minimally invasive surgical tools rely on these coatings to improve durability, reduce friction, and enhance patient safety. With the growing focus on advanced medical technologies and the expansion of healthcare infrastructure, the U.S. market for DLC coatings in this sector is poised for significant growth.
The industrial machinery sector is also a key contributor to the U.S. DLC coatings market, where these coatings are applied to cutting tools, molds, and high-precision equipment to extend tool life, improve efficiency, and reduce maintenance costs. The growing adoption of automation and precision manufacturing technologies further drives demand for DLC coatings in industrial applications. Additionally, the renewable energy sector is creating new opportunities for DLC coatings, particularly in wind turbines and solar panels, where they are used to reduce friction, enhance durability, and protect components exposed to harsh environmental conditions.
The electronics industry in the U.S. is increasingly adopting DLC coatings to protect electronic components, improve thermal conductivity, and extend the lifespan of high-precision devices. Applications include semiconductors, optical lenses, and data storage devices, where wear resistance and low friction are critical. The country’s leadership in semiconductor manufacturing and advancements in consumer electronics are driving further adoption of DLC coatings in this sector.
Recent developments in the U.S. DLC coatings market include advancements in deposition techniques, such as plasma-enhanced chemical vapor deposition (PECVD) and physical vapor deposition (PVD), which have improved coating adhesion, uniformity, and performance. Companies are investing in R&D to develop customized DLC coating solutions for specific industry needs, such as hybrid coatings for aerospace or biocompatible coatings for medical devices. Additionally, the push for sustainability and energy efficiency has further highlighted the role of DLC coatings in reducing energy consumption and extending component life.
In conclusion, the United States DLC coatings market is witnessing significant growth across a wide range of industries. With strong demand from automotive, aerospace, healthcare, industrial, and electronics sectors, coupled with ongoing advancements in coating technologies, the market offers substantial business opportunities for manufacturers and suppliers. As industries continue to prioritize efficiency, durability, and sustainability, DLC coatings are set to play a critical role in the U.S. industrial landscape.
Europe Diamond Like Carbon (DLC) Coatings Market Recent Developments and Business Opportunities by Country
The Europe Diamond-Like Carbon (DLC) coatings market is witnessing strong growth, driven by their increasing adoption across automotive, aerospace, medical devices, industrial machinery, and electronics sectors. DLC coatings, known for their exceptional wear resistance, low friction, and biocompatibility, are becoming integral in advanced manufacturing and high-performance applications. Germany, as Europe’s largest automotive and industrial hub, leads the DLC coatings market in the region. German automakers, including BMW, Volkswagen, and Mercedes-Benz, are utilizing DLC coatings to enhance the efficiency and durability of engine components, such as fuel injectors, pistons, and camshafts. With the shift toward electric vehicles (EVs), German manufacturers are increasingly applying DLC coatings to EV-specific components, such as drivetrains, bearings, and thermal management systems, to reduce wear and improve energy efficiency. Germany’s advanced industrial machinery sector also relies on DLC coatings for cutting tools, molds, and high-precision equipment, further driving market growth.
France is another key market for DLC coatings, particularly in the aerospace and defense sectors. As home to leading aerospace companies like Airbus and Dassault Aviation, France leverages DLC coatings to enhance the performance and reliability of critical aircraft components, such as hydraulic systems, bearings, and turbine blades. These coatings improve wear resistance, reduce friction, and ensure durability in extreme operating conditions. In the defense sector, DLC coatings are used in military vehicles, weapons systems, and high-performance equipment, where durability and low friction are critical. France’s growing EV market and investments in renewable energy projects, such as wind and solar power, further create opportunities for DLC coatings in energy systems and components exposed to harsh environmental conditions.
The United Kingdom also plays a significant role in Europe’s DLC coatings market, driven by its aerospace, automotive, and healthcare industries. British aerospace manufacturers use DLC coatings in high-stress applications, such as landing gear and fuel systems, to improve performance and reduce maintenance requirements. The U.K.’s automotive sector, with a growing focus on EV production, is adopting DLC coatings to enhance the efficiency and reliability of electric drivetrains and battery systems. Additionally, the U.K.’s healthcare sector is a major consumer of DLC coatings, which are applied to medical devices, surgical instruments, and implants to improve biocompatibility, reduce friction, and enhance durability. The expansion of healthcare infrastructure and the demand for advanced medical technologies further drive market growth.
Scandinavian countries, particularly Sweden and Denmark, are emerging markets for DLC coatings, driven by their focus on renewable energy and advanced manufacturing. Sweden’s leadership in EV production and battery technology, supported by companies like Northvolt, drives the adoption of DLC coatings in energy storage and automotive components. Denmark’s renewable energy projects, particularly offshore wind farms, rely on DLC coatings to improve the performance and longevity of turbine components in harsh environments.
Eastern European countries, including Poland and Hungary, are also contributing to the growth of the DLC coatings market. These countries are becoming hubs for automotive and industrial manufacturing, attracting investments from global manufacturers. The use of DLC coatings in automotive components, industrial tools, and precision equipment is growing as these economies expand their industrial base.
In conclusion, the Europe DLC coatings market is growing rapidly, with Germany, France, and the U.K. leading demand, and emerging contributions from Scandinavia and Eastern Europe. The region’s strong focus on EV adoption, aerospace innovation, renewable energy projects, and healthcare advancements drives the need for DLC coatings in diverse applications. With ongoing technological advancements and the increasing emphasis on durability, efficiency, and sustainability, Europe offers significant business opportunities for DLC coating manufacturers and suppliers. As industries prioritize high-performance materials, DLC coatings are set to play a crucial role in Europe’s industrial and technological growth.
Asia Pacific Diamond Like Carbon (DLC) Coatings Market Recent Developments and Business Opportunities by Country
The Asia Pacific Diamond-Like Carbon (DLC) coatings market is witnessing rapid growth, driven by increasing adoption across automotive, electronics, aerospace, industrial machinery, and medical sectors. DLC coatings, renowned for their exceptional wear resistance, low friction, and chemical inertness, are becoming indispensable in high-performance applications. China leads the Asia Pacific DLC coatings market, leveraging its massive industrial base and dominance in the automotive and electronics industries. The country’s rapid adoption of electric vehicles (EVs) has significantly boosted demand for DLC coatings, which are used to enhance the performance and durability of EV-specific components, such as drivetrains, bearings, and thermal management systems. Additionally, China’s expanding semiconductor industry, driven by government support for technological self-reliance, relies on DLC coatings to protect precision tools and equipment from wear during high-purity manufacturing processes. The use of DLC coatings in industrial machinery, cutting tools, and molds is also growing as China modernizes its manufacturing capabilities and focuses on energy efficiency.
Japan is another major contributor to the Asia Pacific DLC coatings market, driven by its advanced automotive, electronics, and aerospace industries. Japanese automakers are increasingly adopting DLC coatings for critical engine components, such as pistons, camshafts, and fuel injectors, to improve fuel efficiency and reduce emissions. With the country’s strong focus on hybrid and electric vehicles, DLC coatings are gaining traction for use in EV components to enhance performance and longevity. Japan’s aerospace sector, which prioritizes lightweight and durable materials, uses DLC coatings in aircraft components, such as hydraulic systems and bearings, to reduce friction and ensure reliability in extreme conditions. The electronics industry in Japan also benefits from DLC coatings, which are applied to semiconductors, optical lenses, and display components to improve durability and thermal conductivity.
South Korea, home to leading automotive and electronics manufacturers like Hyundai, Samsung, and LG, is another key market for DLC coatings in the region. The country’s growing EV production and investments in battery technology have driven demand for DLC coatings in energy storage systems and automotive components. South Korea’s semiconductor industry, a global leader in memory and processing chips, relies on DLC coatings for high-precision tools and equipment, ensuring durability and operational efficiency. Additionally, DLC coatings are used in the consumer electronics sector to protect high-end devices, such as smartphones, tablets, and wearables, from wear and tear.
India is an emerging market for DLC coatings, supported by rapid industrialization, growing automotive production, and investments in renewable energy. Indian automakers are adopting DLC coatings to improve the efficiency and reliability of vehicle components, while the government’s push for electric mobility under the FAME (Faster Adoption and Manufacturing of Hybrid and Electric Vehicles) initiative is creating opportunities for DLC coatings in EV applications. India’s expanding healthcare and medical device sectors also utilize DLC coatings for surgical instruments, implants, and diagnostic tools, where biocompatibility and wear resistance are essential.
Southeast Asian countries, including Thailand, Vietnam, and Indonesia, are also contributing to the growth of the DLC coatings market. Thailand, as a regional automotive hub, uses DLC coatings in manufacturing high-performance automotive components. Vietnam and Indonesia, with their growing industrial and renewable energy sectors, are increasingly adopting DLC coatings in machinery, tools, and energy systems to improve efficiency and durability.
In conclusion, the Asia Pacific DLC coatings market is expanding rapidly, with China, Japan, South Korea, India, and Southeast Asia driving demand. The region’s leadership in automotive production, electronics manufacturing, and renewable energy adoption creates significant business opportunities for DLC coating manufacturers and suppliers. With ongoing investments in high-tech industries and advancements in DLC coating technologies, the Asia Pacific region is poised to remain a critical growth market for high-performance coatings across diverse applications.
Middle East Diamond Like Carbon (DLC) Coatings Market Recent Developments and Business Opportunities by Country
The Middle East Diamond-Like Carbon (DLC) coatings market is steadily growing, driven by the region’s increasing focus on industrial diversification, advancements in manufacturing, and the adoption of renewable energy projects. Known for their exceptional wear resistance, low friction, and chemical inertness, DLC coatings are being adopted in high-performance applications across industries such as oil and gas, automotive, aerospace, industrial machinery, and healthcare. The United Arab Emirates (UAE) is at the forefront of the DLC coatings market in the Middle East, leveraging its advanced infrastructure and position as a hub for innovation. The UAE’s expanding automotive sector, coupled with its push toward electric vehicles (EVs), is creating demand for DLC coatings in drivetrain components, bearings, and other high-performance parts to improve efficiency and extend durability. Additionally, the country’s growing aerospace industry is adopting DLC coatings for critical components such as hydraulic systems, bearings, and fuel systems to enhance durability and reduce maintenance in extreme conditions. The UAE’s ambitious renewable energy projects, such as the Mohammed bin Rashid Al Maktoum Solar Park, also use DLC coatings to protect components in solar panels and wind turbines from wear and corrosion.
Saudi Arabia is another key market for DLC coatings, driven by its Vision 2030 initiative, which emphasizes economic diversification and investments in advanced technologies. The kingdom’s thriving oil and gas sector is a major consumer of DLC coatings, which are used in drilling equipment, pumps, and valves to minimize wear and improve operational efficiency. Additionally, Saudi Arabia’s automotive industry is growing, with a focus on developing local electric vehicle production facilities. DLC coatings are being increasingly adopted for EV components and high-performance automotive parts to enhance energy efficiency and reduce friction. Saudi Arabia’s investments in renewable energy, including large-scale solar and wind projects, further create opportunities for DLC coatings in energy systems requiring durability and resistance to harsh environmental conditions.
Qatar, with its focus on infrastructure development and sustainable energy, is emerging as a promising market for DLC coatings. The country’s growing aerospace and defense industries are adopting DLC coatings for use in high-stress applications, such as aircraft components and military equipment, where wear resistance and low friction are critical. Qatar’s chemical processing and industrial sectors also rely on DLC coatings to improve the efficiency and longevity of machinery and tools exposed to corrosive substances and high temperatures. Additionally, the healthcare sector in Qatar is utilizing DLC coatings in medical devices, implants, and surgical instruments for their biocompatibility, durability, and smooth surface properties.
Israel, known for its advanced technology and innovation-driven economy, is leveraging DLC coatings in high-tech applications, including semiconductors, electronics, and renewable energy. The country’s focus on electric vehicles and renewable energy systems has created demand for DLC coatings in energy storage solutions and EV components, where their properties enhance performance and reduce wear.
Smaller markets such as Oman and Bahrain are also adopting DLC coatings for industrial and renewable energy applications. Oman’s oil and gas industry, along with its investments in renewable energy, drives demand for DLC coatings in high-performance equipment and energy systems. Bahrain’s infrastructure modernization efforts and focus on sustainability are further supporting the adoption of DLC coatings in various sectors.
In conclusion, the Middle East DLC coatings market is steadily expanding, with significant opportunities across countries such as the UAE, Saudi Arabia, Qatar, Israel, Oman, and Bahrain. The region’s emphasis on renewable energy, industrial growth, and advanced manufacturing is driving the adoption of DLC coatings in diverse applications. As investments in clean energy infrastructure, automotive production, and aerospace innovation grow, the Middle East offers substantial business opportunities for DLC coating manufacturers and suppliers to cater to the region’s evolving industrial landscape.
Global Diamond Like Carbon (DLC) Coatings Analysis by Market Segmentation
- By Type of DLC Coatings:
- Hydrogenated DLC (a-C:H):
- Contains hydrogen to improve adhesion and flexibility.
- Widely used in automotive and industrial applications for components like engine parts and cutting tools due to its enhanced mechanical properties.
- Non-Hydrogenated DLC (a-C):
- Pure carbon-based coatings with superior hardness and wear resistance.
- Preferred for high-stress applications in aerospace and medical industries where durability and scratch resistance are critical.
- Doped DLC Coatings:
- Includes dopants like silicon, fluorine, or metal elements to enhance specific properties such as thermal stability or lubricity.
- Commonly used in electronics, semiconductors, and specialized industrial applications.
- By Deposition Technique:
- Physical Vapor Deposition (PVD):
- A widely used method that provides high-quality, uniform coatings with excellent adhesion.
- Common in the automotive, aerospace, and electronics industries for components requiring precise surface finishes.
- Chemical Vapor Deposition (CVD):
- Offers superior wear resistance and is ideal for coating intricate geometries.
- Preferred in medical, industrial, and semiconductor applications due to its ability to create durable and high-purity coatings.
- Plasma-Enhanced Chemical Vapor Deposition (PECVD):
- Combines the benefits of PVD and CVD and is suitable for high-temperature applications.
- Used in aerospace and energy systems requiring thermal stability and corrosion resistance.
- By Application:
- Automotive:
- DLC coatings are used in engine components (pistons, camshafts, fuel injectors) to reduce friction, improve fuel efficiency, and enhance durability.
- Increasingly applied to electric vehicle (EV) components such as drivetrains, bearings, and battery systems to improve performance.
- Aerospace and Defense:
- Applied to aircraft components like hydraulic systems, turbine blades, and bearings to ensure durability under extreme conditions.
- Used in defense equipment and weapons systems to enhance wear resistance and operational reliability.
- Medical Devices:
- DLC coatings are biocompatible and used in surgical instruments, implants (e.g., joint replacements, stents), and diagnostic tools to reduce friction and improve wear resistance.
- High demand driven by advancements in minimally invasive surgery and medical device innovation.
- Electronics and Semiconductors:
- Protects precision tools and components in semiconductor manufacturing from wear and contamination.
- Used in electronic devices (smartphones, tablets) for scratch-resistant coatings and thermal management.
- Industrial Machinery:
- Widely used in cutting tools, molds, and high-precision equipment to increase tool life, reduce maintenance, and improve efficiency.
- Adopted in manufacturing and automation for enhanced performance under high stress.
- Renewable Energy:
- DLC coatings are used in wind turbine bearings and solar panel systems to reduce friction and protect components from wear and corrosion in harsh environmental conditions.
- Consumer Goods:
- Applied to high-end watches, jewelry, and optical lenses to provide a scratch-resistant, aesthetic, and durable finish.
- By End-Use Industry:
- Automotive:
- The largest consumer of DLC coatings, driven by the shift toward electric vehicles and stricter fuel efficiency regulations.
- Aerospace & Defense:
- High adoption due to stringent requirements for lightweight, durable, and low-friction materials.
- Healthcare:
- Expanding applications in implants, surgical tools, and diagnostic equipment due to biocompatibility and wear resistance.
- Electronics:
- Growing use in protective coatings for high-tech devices and semiconductors.
- Industrial:
- Increasing adoption in manufacturing tools and machinery to enhance productivity and longevity.
- Renewable Energy:
- Rapid growth in wind and solar energy systems creates demand for durable and low-maintenance coatings.
- By Region:
- Asia Pacific:
- The largest market, driven by the dominance of automotive, electronics, and semiconductor manufacturing in China, Japan, South Korea, and India.
- North America:
- Strong demand in aerospace, medical, and automotive industries, supported by advancements in EVs and renewable energy systems.
- Europe:
- High adoption in automotive, aerospace, and healthcare industries, with Germany, France, and the U.K. leading the market.
- Middle East & Africa:
- Emerging demand for DLC coatings in oil & gas, renewable energy, and infrastructure development.
- Latin America:
- Growth driven by mining, industrial machinery, and renewable energy projects.
- By Performance Characteristics:
- Wear Resistance:
- DLC coatings are favored for their ability to significantly reduce wear in high-friction applications, extending component life.
- Low Friction:
- Their low coefficient of friction makes them ideal for automotive, aerospace, and industrial machinery components.
- Thermal Stability:
- Ensures performance in high-temperature environments, critical for aerospace, energy, and semiconductor applications.
- Biocompatibility:
- Essential in medical applications such as implants and surgical tools, ensuring compatibility with human tissues.
- Corrosion Resistance:
- Key for applications in oil & gas, renewable energy, and industrial machinery exposed to harsh environmental conditions.
Diamond Like Carbon (DLC) Coatings Production and Import-Export Scenario
The production and import-export scenario for Diamond-Like Carbon (DLC) coatings reflects the growing global demand for high-performance materials in industries such as automotive, aerospace, medical devices, industrial machinery, and electronics. DLC coatings are primarily produced in regions with advanced manufacturing capabilities, including Asia Pacific, North America, and Europe. The Asia Pacific region leads global DLC coating production, with countries like China, Japan, and South Korea dominating the market due to their strong industrial base, advanced technological expertise, and leadership in automotive and electronics manufacturing. China is the largest producer of DLC coatings, supported by its massive automotive industry and the increasing adoption of electric vehicles (EVs). Chinese manufacturers also cater to the domestic and international markets, exporting DLC coatings to North America, Europe, and Southeast Asia for use in automotive components, industrial tools, and renewable energy systems. The country’s investments in advanced manufacturing and innovation have further strengthened its position as a global supplier of DLC coatings.
Japan and South Korea are also significant producers, specializing in high-quality DLC coatings for precision applications. These countries leverage their expertise in semiconductors, electronics, and automotive manufacturing to produce DLC coatings that meet the stringent requirements of these industries. Japan, for instance, exports a significant volume of DLC coatings to Europe and North America, where demand is driven by the aerospace, automotive, and medical sectors. Similarly, South Korea’s leadership in EV and battery manufacturing, coupled with its advanced semiconductor industry, has made it a key exporter of DLC coatings for energy storage and electronics applications.
In North America, particularly the United States, DLC coating production is driven by strong demand from the automotive, aerospace, and medical sectors. While the U.S. has significant domestic production capabilities, it also imports DLC coatings and related technologies from Asia and Europe to meet the increasing demand for high-performance applications. Recent developments in the U.S. market, including investments in EV manufacturing and renewable energy projects, have spurred growth in local DLC coating production. Additionally, advancements in deposition technologies, such as physical vapor deposition (PVD) and plasma-enhanced chemical vapor deposition (PECVD), have enabled U.S. manufacturers to produce DLC coatings for diverse applications. The U.S. also exports DLC-coated components and tools to other regions, particularly Europe and Latin America, for use in industrial and automotive applications.
Europe is a major consumer and producer of DLC coatings, with countries like Germany, France, and the United Kingdom leading the regional market. Germany’s automotive and aerospace industries are key drivers of DLC coating demand, while France’s aerospace and defense sectors contribute significantly to the market. European manufacturers produce and export high-performance DLC coatings for specialized applications, including medical devices and renewable energy systems. However, Europe also imports DLC coatings from Asia, particularly for cost-sensitive applications and to meet the growing demand from renewable energy and industrial sectors.
Emerging markets in the Middle East, Africa, and Latin America are increasingly importing DLC coatings to support their growing automotive, industrial, and renewable energy sectors. The Middle East, with its focus on oil and gas and renewable energy projects, relies on imported DLC coatings for equipment and energy systems. Similarly, Latin America’s expanding industrial base and renewable energy initiatives drive demand for DLC coatings, particularly for machinery and energy storage systems.
In conclusion, the production and trade of DLC coatings are dominated by Asia Pacific, with China, Japan, and South Korea leading global production and exports. North America and Europe are significant consumers and producers but also rely on imports to meet growing demand. Emerging markets in the Middle East, Africa, and Latin America are increasingly adopting DLC coatings for industrial and energy applications, contributing to the global expansion of the market. As industries continue to prioritize efficiency, durability, and sustainability, the DLC coatings market is poised for sustained growth across all regions.
Market Scenario, Demand vs Supply, Average Product Price, Import vs Export, till 2035
- Global Diamond Like Carbon (DLC) Coatings Market revenue and demand by region
- Global Diamond Like Carbon (DLC) Coatings Market production and sales volume
- United States Diamond Like Carbon (DLC) Coatings Market revenue size and demand by country
- Europe Diamond Like Carbon (DLC) Coatings Market revenue size and demand by country
- Asia Pacific Diamond Like Carbon (DLC) Coatings Market revenue size and demand by country
- Middle East & Africa Diamond Like Carbon (DLC) Coatings Market revenue size and demand by country
- Latin America Diamond Like Carbon (DLC) Coatings Market revenue size and demand by
- Import-export scenario – United States, Europe, APAC, Latin America, Middle East & Africa
- Average product price – United States, Europe, APAC, Latin America, Middle East & Africa
- Market player analysis, competitive scenario, market share analysis
- Business opportunity analysis
Key questions answered in the Global Diamond Like Carbon (DLC) Coatings Market Analysis Report:
- What is the market size for Diamond Like Carbon (DLC) Coatings in United States, Europe, APAC, Middle East & Africa, Latin America?
- What is the yearly sales volume of Diamond Like Carbon (DLC) Coatings and how is the demand rising?
- Who are the top market players by market share, in each product segment?
- Which is the fastest growing business/ product segment?
- What should be the business strategies and Go to Market strategies?
The report covers Diamond Like Carbon (DLC) Coatings Market revenue, Production, Sales volume, by regions, (further split into countries):Â
- Asia Pacific (China, Japan, South Korea, India, Indonesia, Vietnam, Rest of APAC)
- Europe (UK, Germany, France, Italy, Spain, Benelux, Poland, Rest of Europe)
- North America (United States, Canada, Mexico)
- Latin America (Brazil, Argentina, Rest of Latin America)
- Middle East & Africa
Table of Contents:
- Introduction to Diamond Like Carbon (DLC) Coatings
- Overview of DLC Coatings and Their Unique Properties
- Key Benefits of DLC Coatings in Various Industries
- Chemical Composition and Structure of DLC Coatings
- Molecular and Atomic Structure of DLC Films
- Key Characteristics: Hardness, Wear Resistance, and Lubricity
- Global Market Overview for DLC Coatings
- Market Trends, Growth Drivers, and Technological Innovations
- Impact of DLC Coatings on Performance and Efficiency
- Market Size, Share, and Forecast (2019-2035)
- Global Market Value and Projected Growth
- Market Segmentation and Forecast by Region and Application
- Regional Market Insights
- North America: Key Developments and Industry Adoption
- Europe: Technological Advancements and Market Dynamics
- Asia Pacific: Market Growth, Leading Producers, and Consumption
- Latin America: Emerging Markets and Adoption Trends
- Middle East & Africa: Opportunities and Market Potential
- Manufacturing and Application Techniques for DLC Coatings
- Overview of DLC Coating Deposition Methods (e.g., PECVD, HIPIMS)
- Key Innovations in Coating Technologies and Their Impact
- Leading Manufacturers and Their Market Strategies
- Raw Materials and Sourcing for DLC Coatings
- Materials Used in DLC Coating Production
- Sourcing and Supply Chain Considerations
- Key Suppliers and Regional Raw Material Availability
- Price Trends and Market Influences
- Pricing Analysis for DLC Coatings (2019-2035)
- Factors Affecting DLC Coating Prices
- Regional Price Disparities and Economic Factors
- End-Use Applications of DLC Coatings
- Automotive Industry: Increasing Durability and Performance
- Aerospace: Use in High-Performance Components
- Medical Devices: Biocompatibility and Wear Resistance
- Electronics: Reducing Friction in Semiconductors and Hard Drives
- Industrial Applications: Cutting Tools, Bearings, and Machinery
- Competitive Landscape of the DLC Coatings Market
- Market Share Analysis and Key Players in the DLC Coatings Industry
- Competitive Strategies and Innovations by Leading Companies
- Mergers, Acquisitions, and Strategic Partnerships
- Demand and Consumption Trends
- Key Drivers of Demand Across Different Industries
- Regional Consumption Patterns and Forecasts
- The Impact of Consumer Behavior on DLC Coating Adoption
- Technological Advancements in DLC Coatings
- Innovations in Coating Properties and Deposition Techniques
- Advanced DLC Coatings for Specific Applications
- Research and Development Focus Areas in DLC Coatings
- Challenges in the DLC Coatings Market
- Production Challenges and Cost Constraints
- Environmental Concerns and Sustainability Issues
- Technological Barriers and Competition from Alternative Coatings
- Environmental and Sustainability Considerations
- Environmental Impact of DLC Coating Production
- Recycling and Disposal Considerations for DLC-Coated Products
- Sustainable Manufacturing Practices and Green Technologies
- Regulatory and Compliance Factors
- Industry Regulations Affecting DLC Coating Production and Use
- Environmental Compliance and Industry Standards for DLC Coatings
- Market-Specific Regulations in Automotive, Aerospace, and Medical Sectors
- Investment Opportunities in DLC Coatings Market
- Investment Trends and High-Growth Areas in DLC Coatings
- Business Expansion Strategies for Key Market Participants
- Investment Potential in Emerging Markets and New Applications
- Future Trends and Innovations in DLC Coatings
- Long-Term Market Projections and Emerging Growth Areas
- Innovations in DLC Coating Materials and Techniques
- Potential Applications and New Market Opportunities
- Strategic Recommendations for Stakeholders
- Actionable Insights for Manufacturers and Suppliers
- Best Practices for Market Entry and Expansion
- Strategic Recommendations for Policymakers and Industry Leaders
“Every Organization is different and so are their requirements”- Datavagyanik
Companies We Work With
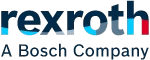
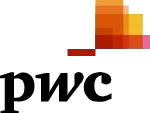
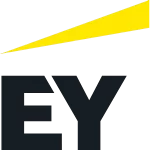
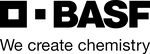
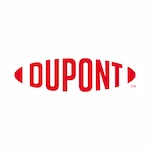

Do You Want To Boost Your Business?
drop us a line and keep in touch
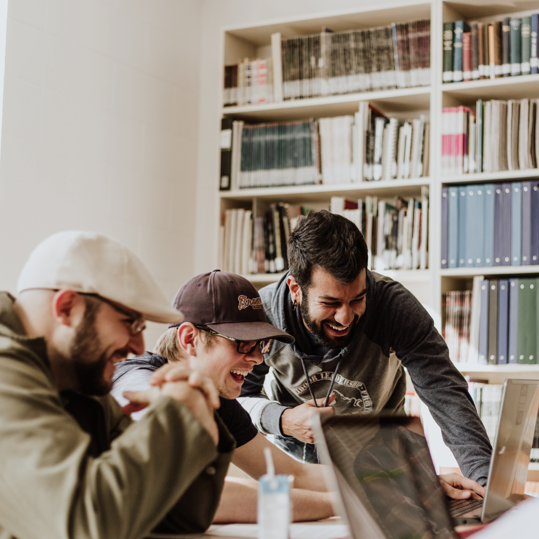