Advanced Heat Exchangers for Refineries Market Size, Production, Sales, Average Product Price, Market Share, Import vs Export
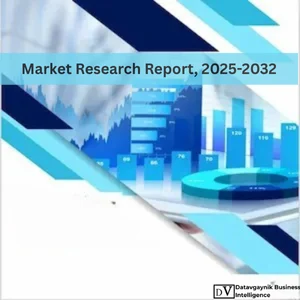
- Published 2025
- No of Pages: 120+
- 20% Customization available
Rising Demand for Thermal Efficiency Propels Advanced Heat Exchangers for Refineries Market
The advanced heat exchangers for refineries market is undergoing a transformative phase, driven by the critical need to improve thermal efficiency and reduce energy consumption in modern refining operations. Refineries are among the most energy-intensive industries, consuming approximately 6%–8% of total global industrial energy, according to Datavagyanik. With energy prices remaining volatile and environmental compliance becoming increasingly stringent, advanced heat exchangers have emerged as indispensable components for refinery efficiency and sustainability.
For instance, shell-and-tube and plate-type heat exchangers have demonstrated up to 30% higher heat recovery rates in distillation and hydroprocessing units. These systems are enabling refiners to recover waste heat from flue gases and product streams, which would otherwise be lost, and repurpose it to preheat feedstocks. As a result, operating costs are significantly reduced while greenhouse gas emissions are minimized. The advanced heat exchangers for refineries market size is expanding steadily, with global installations forecast to rise by 6.8% CAGR between 2024 and 2032, supported by widespread industry modernization.
Environmental Mandates Driving Innovation in Advanced Heat Exchangers for Refineries Market
Environmental regulations are acting as a primary catalyst for the growth of the advanced heat exchangers for refineries market. Refineries across North America, Europe, and Asia-Pacific are under increasing pressure to reduce emissions, in line with policies such as the European Union’s Green Deal and the United States’ Clean Air Act. For example, the U.S. Environmental Protection Agency (EPA) mandates sulfur content in fuels to be below 15 ppm, necessitating enhanced desulfurization operations that rely heavily on efficient heat transfer equipment.
Advanced heat exchangers, especially those integrated with smart monitoring systems, are critical in meeting these standards. By recovering thermal energy during catalytic reforming and hydrocracking processes, these exchangers help lower fuel consumption and emissions. According to Datavagyanik, refineries that deploy IoT-enabled heat exchangers have reduced their CO₂ emissions by up to 18% while improving energy recovery by 25%–35%. This dual benefit of compliance and cost savings is creating a surge in demand, particularly for stainless steel and alloy steel exchangers that can withstand corrosive and high-pressure environments.
Datavagyanik also covers related markets such as the Waste Heat Recovery Systems for Refineries Market, the Expanded Graphite in Heat Exchangers Market, and the Isobutane for Refineries Market. These markets reflect the interconnectedness of industrial forces that define the growth and direction of the primary topic.
Refinery Upgrades and Capacity Expansion Bolster Advanced Heat Exchangers for Refineries Market
Global refinery expansion and modernization projects are injecting new momentum into the advanced heat exchangers for refineries market. For example, India’s Paradip Refinery and China’s Zhanjiang Petrochemical Complex have incorporated advanced heat exchanger systems as part of billion-dollar infrastructure upgrades aimed at improving crude throughput and fuel quality. These projects are not isolated; over 20 major refinery upgrades are expected across Asia and the Middle East by 2027.
Datavagyanik estimates that over 60% of planned capacity additions in developing regions will involve the integration of energy recovery technologies such as compact plate heat exchangers and air-cooled systems. These systems offer better scalability, easier maintenance, and superior heat transfer coefficients compared to conventional designs. As refining becomes more complex with high-sulfur crude and integrated petrochemical production, the need for tailored, high-performance heat exchange systems is only expected to grow.
Technological Advancements Fuel Competitive Edge in Advanced Heat Exchangers for Refineries Market
Technological innovation is reshaping the competitive landscape of the advanced heat exchangers for refineries market. Modern exchangers are now being manufactured using corrosion-resistant alloys such as titanium and duplex stainless steel, allowing them to withstand extreme temperatures and highly acidic process streams. In addition, compact heat exchanger designs are gaining traction due to space constraints in brownfield refinery sites.
For instance, printed circuit heat exchangers (PCHEs) are being adopted in hydrogen production units due to their ability to operate under pressures exceeding 200 bar while delivering up to 95% thermal efficiency. Moreover, smart heat exchangers integrated with AI and IoT capabilities enable predictive maintenance, minimizing unplanned shutdowns and extending operational lifespans. Datavagyanik reports that refineries leveraging data-driven performance monitoring have reduced maintenance costs by 20% while increasing uptime by over 15%. This blend of materials innovation and digital integration is setting a new benchmark for performance and reliability.
Surging Petrochemical Demand Spurs Growth in Advanced Heat Exchangers for Refineries Market
The global boom in petrochemical production is a major driver of the advanced heat exchangers for refineries market. With ethylene, propylene, and aromatics serving as essential feedstocks for plastics, textiles, and packaging industries, refineries are increasingly integrating petrochemical units into their operations. As a result, thermal management becomes more complex and critical.
For instance, ethylene crackers require precise temperature control to ensure product yield and process stability. In such applications, high-performance heat exchangers ensure that temperature differentials are maintained across reactors, separators, and condensers. The market is witnessing strong demand for heat exchangers with rapid response times and high fouling resistance, especially in the Asia-Pacific region, where petrochemical capacity is projected to grow by 7% CAGR through 2030. Datavagyanik highlights that advanced heat exchangers can reduce energy intensity in steam cracking units by up to 12%, offering both economic and environmental benefits.
Post-Pandemic Refinery Utilization Boosts Advanced Heat Exchangers for Refineries Market
The post-COVID-19 resurgence in fuel demand has significantly increased refinery utilization rates, particularly in the United States, Middle East, and Southeast Asia. As utilization climbs beyond 80% in many regions, the need for energy optimization becomes paramount. Heat exchangers are playing a central role in this recovery by ensuring that higher throughput is matched with efficient thermal management.
For example, in Texas and Louisiana, U.S. Gulf Coast refineries are reporting throughput levels exceeding 95% of pre-pandemic levels. This has driven the installation of air-cooled and plate heat exchangers that can handle high volumes while maintaining tight process control. Datavagyanik states that refineries operating above 85% utilization experience up to 40% higher stress on their heat management systems, accelerating demand for advanced exchangers with high mechanical integrity and adaptive control features.
Energy Transition and Clean Fuels Accelerate Advanced Heat Exchangers for Refineries Market
The global pivot toward cleaner fuels is driving refiners to upgrade their processing units, which in turn is expanding the advanced heat exchangers for refineries market. With governments pushing for ultra-low sulfur diesel (ULSD), biofuels, and hydrogen, the refining landscape is shifting towards more environmentally responsible operations. For example, the International Maritime Organization’s sulfur cap regulation has triggered massive investments in desulfurization units worldwide.
In such settings, advanced heat exchangers are indispensable. Hydrotreaters and hydrogen plants demand systems that can operate at high pressures with minimal thermal losses. Datavagyanik notes that the use of compact, high-efficiency exchangers in desulfurization units has cut energy usage by 15% while maintaining strict quality control of fuel specifications. Furthermore, the integration of biofuel production into refinery setups has opened new application areas, where thermal integration is critical to maintaining the viability of alternative fuels.
Surge in Emerging Market Refineries Drives Advanced Heat Exchangers for Refineries Market Penetration
Emerging markets are becoming hotspots for refinery development, significantly influencing the trajectory of the advanced heat exchangers for refineries market. Countries such as Vietnam, Nigeria, and Kazakhstan are investing in new refining infrastructure to meet growing domestic fuel demand and to tap into export opportunities. For example, Vietnam’s Nghi Son refinery and Nigeria’s Dangote refinery, among the largest in their respective regions, have embedded advanced heat exchanger technologies into their designs to maximize process efficiency from the outset.
Datavagyanik identifies that over 70% of greenfield refinery projects in emerging economies are specifying advanced heat exchangers as critical systems in early-stage design. This is particularly notable in areas where water scarcity and energy infrastructure limitations necessitate the use of air-cooled or hybrid exchanger systems. These solutions not only provide greater operational resilience but also align with environmental and resource constraints in these regions.
“Track Country-wise Advanced Heat Exchangers for Refineries Production and Demand through our Advanced Heat Exchangers for Refineries Production Database”
-
-
- Advanced Heat Exchangers for Refineries production database for 28+ countries worldwide
- Advanced Heat Exchangers for Refineries Powder sales volume for 32+ countries
- Country-wise Advanced Heat Exchangers for Refineries production capacity and production plant mapping, production capacity utilization for 28+ manufacturers
- Advanced Heat Exchangers for Refineries production plants and production plant capacity analysis for top manufacturers
-
North America Continues to Lead Global Advanced Heat Exchangers for Refineries Market
The advanced heat exchangers for refineries market in North America is witnessing sustained growth, anchored by the modernization of legacy refinery assets and increasing adoption of clean fuel technologies. The United States, in particular, dominates regional demand, with over 130 operational refineries, many of which are undergoing upgrades to meet higher environmental standards. Datavagyanik highlights that over 40% of U.S. refinery investments between 2020 and 2024 included the installation of high-efficiency shell-and-tube and plate heat exchangers.
For example, Gulf Coast refineries in Texas and Louisiana have adopted advanced heat exchangers to optimize hydroprocessing and naphtha reforming units, which are critical for producing low-sulfur fuels. The advanced heat exchangers for refineries market in the U.S. is further propelled by the shale oil boom, as newer refineries adapt to processing lighter, unconventional crudes that demand more precise thermal control. Additionally, Canada’s investments in oil sands upgrading and green hydrogen integration are generating further demand for robust heat exchanger systems designed to operate under extreme pressure and high sulfur conditions.
Europe’s Decarbonization Strategy Fuels Demand in Advanced Heat Exchangers for Refineries Market
Europe presents a unique growth trajectory in the advanced heat exchangers for refineries market, driven by its aggressive decarbonization agenda. Countries such as Germany, the United Kingdom, France, and the Netherlands are prioritizing energy efficiency and emissions reduction across refining operations. Datavagyanik data shows that European refiners have achieved a 22% improvement in thermal efficiency since 2015, largely due to the adoption of next-generation heat exchanger technologies.
For instance, Germany’s refineries are investing in compact, corrosion-resistant exchangers for processes like hydrodesulfurization and aromatic recovery. These technologies are critical for meeting EU regulations such as REPowerEU and the Fit for 55 package. In the UK, heat exchangers with integrated IoT systems are enabling predictive maintenance, reducing unplanned downtime by up to 30%. As Europe continues to lead in refinery transformation and green hydrogen production, demand for high-performance heat exchangers is expected to grow at a 6.3% CAGR through 2030.
Asia Pacific Emerges as the Fastest Growing Advanced Heat Exchangers for Refineries Market
Asia Pacific is currently the fastest-growing region in the advanced heat exchangers for refineries market, fueled by rapid industrialization, urbanization, and a surge in fuel and petrochemical demand. Datavagyanik forecasts a compound annual growth rate of 7.8% in the region through 2032, underpinned by capacity expansions in China, India, South Korea, and Southeast Asia.
For example, China’s refining capacity surpassed 17 million barrels per day in 2023, with new mega-refineries in Zhoushan and Yantai integrating advanced heat exchanger systems to manage large-scale energy flows. In India, major players like Reliance Industries and Indian Oil Corporation are installing air-cooled and plate-type exchangers to improve efficiency in fluid catalytic cracking (FCC) and hydrocracking units. Meanwhile, South Korea’s focus on petrochemical integration is generating demand for highly specialized exchangers in steam cracking and reforming applications.
The advanced heat exchangers for refineries market in Asia Pacific is also benefiting from government-led energy transition initiatives. For instance, India’s National Hydrogen Mission and China’s carbon neutrality goals are pushing refiners to adopt advanced systems that reduce process heat losses and emissions.
Middle East Expands Refinery Infrastructure, Boosting Advanced Heat Exchangers for Refineries Market
The Middle East is making strategic investments to scale up refining capacity and integrate advanced technologies, positioning itself as a key player in the global advanced heat exchangers for refineries market. Saudi Arabia, UAE, and Qatar are leading this transformation. Datavagyanik identifies over $100 billion in refining and petrochemical projects underway in the region, many of which include the deployment of state-of-the-art heat exchangers for heat recovery and thermal optimization.
For example, Saudi Aramco’s Jazan Refinery has adopted compact heat exchangers for hydrogen production units, achieving a 17% increase in energy utilization efficiency. Similarly, ADNOC in the UAE has implemented advanced exchangers in its Ruwais complex to support clean fuel initiatives. In Qatar, the North Field Expansion has driven demand for exchangers in LNG processing, where precise thermal control is essential to liquefaction.
The Middle East’s harsh climate and water scarcity also make air-cooled heat exchangers especially relevant. These systems reduce water dependency while maintaining high thermal performance in ambient temperatures exceeding 50°C.
Advanced Heat Exchangers for Refineries Market Segmentation by Technology and Application
Segmentation in the advanced heat exchangers for refineries market reveals how different exchanger types cater to specific process needs. Shell-and-tube heat exchangers continue to dominate due to their robustness and adaptability in high-pressure environments. Datavagyanik notes that over 45% of all new refinery projects in 2024 have specified shell-and-tube configurations for crude distillation and catalytic reforming units.
Plate heat exchangers, on the other hand, are gaining traction in space-constrained refinery environments. These units are especially effective in cooling circuits and desulfurization units, where compact design and high thermal conductivity are priorities. Meanwhile, air-cooled exchangers are increasingly used in hydroprocessing and distillation units in arid regions, especially in the Middle East and parts of Asia.
From an application standpoint, crude distillation accounts for the highest share of demand, followed by hydrocracking, hydrotreating, and petrochemical production. Datavagyanik highlights that steam reforming and gas sweetening units are emerging as new high-growth segments, particularly in refineries integrating hydrogen production and natural gas processing.
Material-Based Trends in Advanced Heat Exchangers for Refineries Market
Material selection plays a critical role in the advanced heat exchangers for refineries market, directly impacting durability, efficiency, and cost. Stainless steel remains the most widely used material, especially in hydrotreaters and sulfur recovery units. Its resistance to corrosion and high temperatures makes it ideal for handling aggressive fluids.
Alloy steel, including grades with chromium, molybdenum, and nickel, is seeing increased adoption in deep hydrocracking and delayed coking units. These exchangers can handle extreme pressure and thermal cycling, reducing maintenance intervals and downtime. Titanium and copper alloys, though more expensive, are used selectively in high-performance exchangers where superior thermal conductivity and corrosion resistance are required—such as in aromatics extraction and isomerization units.
Datavagyanik points out that the material mix is shifting toward premium alloys in regions like North America and the EU due to stricter emissions regulations, while cost-effective carbon steel still dominates in emerging markets.
Production Hubs and Global Trade Dynamics in Advanced Heat Exchangers for Refineries Market
Production of advanced heat exchangers for refineries is concentrated in industrially advanced countries with strong metallurgical and manufacturing capabilities. The United States, Germany, Japan, and China are the leading producers, supplying over 70% of global demand. These countries benefit from well-established supply chains, technical expertise, and R&D capabilities.
For instance, U.S. companies produce customized shell-and-tube exchangers for Gulf Coast refiners, while Germany’s precision engineering supports demand for plate-type units across Europe and the Middle East. Japan, known for innovation in compact heat exchanger design, exports extensively to Southeast Asia and the Pacific Rim. Meanwhile, China is becoming a competitive exporter by scaling up production of low-cost, corrosion-resistant exchangers.
Datavagyanik highlights that international trade in heat exchangers is closely tied to refinery project timelines. Asia Pacific and the Middle East are net importers, sourcing high-performance systems from North America and Europe. Latin America and Africa, undergoing refinery expansions, also contribute to growing import volumes.
Advanced Heat Exchangers for Refineries Price Trend and Cost Factors
The advanced heat exchangers for refineries price trend reflects a balance between rising raw material costs and technological improvements. Stainless steel and alloy steel prices have increased by 8%–12% year-on-year due to supply chain disruptions and increased global demand. As a result, the average advanced heat exchangers for refineries price has risen by approximately 9% over the past 18 months.
However, manufacturers are offsetting some of these costs through improved design efficiencies and modular construction. For instance, modular plate heat exchangers with integrated sensors reduce lifecycle costs by 20%, despite higher initial prices. Datavagyanik reports that the advanced heat exchangers for refineries price varies widely by type—ranging from $5,000 for small double-pipe units to over $100,000 for large shell-and-tube systems designed for FCC units.
Geographically, the advanced heat exchangers for refineries price trend shows higher pricing in Europe due to regulatory requirements and higher labor costs, while Asia Pacific offers more competitive pricing due to large-scale production capabilities and favorable manufacturing economics.
Price Forecast and Investment Outlook in Advanced Heat Exchangers for Refineries Market
Looking forward, the advanced heat exchangers for refineries price trend is expected to stabilize by 2026, as raw material supply chains normalize and new manufacturing technologies improve efficiency. Datavagyanik projects that heat exchanger prices will rise moderately at a CAGR of 2.5% through 2030, with premium products seeing higher price elasticity based on performance gains.
The investment outlook for the advanced heat exchangers for refineries market remains bullish. With over 300 planned refinery projects worldwide—many of them incorporating green hydrogen, biofuels, and petrochemicals—demand for high-efficiency heat exchangers will continue to surge. In particular, demand for smart heat exchangers with real-time monitoring features is expected to triple by 2032, reshaping how thermal systems are integrated into future refinery operations.
“Advanced Heat Exchangers for Refineries Manufacturing Database, Advanced Heat Exchangers for Refineries Manufacturing Capacity”
-
-
- Advanced Heat Exchangers for Refineries top manufacturers market share for 28+ manufacturers
- Top 8 manufacturers and top 18 manufacturers of Advanced Heat Exchangers for Refineries in North America, Europe, Asia Pacific
- Production plant capacity by manufacturers and Advanced Heat Exchangers for Refineries production data for 28+ market players
- Advanced Heat Exchangers for Refineries production dashboard, Advanced Heat Exchangers for Refineries production data in excel format
-
Key Players Dominating the Advanced Heat Exchangers for Refineries Market
The advanced heat exchangers for refineries market is characterized by the presence of several global and regional manufacturers, each contributing with specialized technologies and extensive product portfolios tailored for high-performance refinery applications. The market is moderately consolidated, with the top ten players accounting for over 60% of the global revenue share. These manufacturers play a critical role in driving innovation, material advancements, and process-specific solutions across the refining industry.
Alfa Laval – A Global Leader in Advanced Plate and Welded Exchangers
Alfa Laval remains one of the most influential players in the advanced heat exchangers for refineries market. The company commands approximately 13% of global market share and offers a wide portfolio of plate heat exchangers, welded exchangers, and air-cooled systems. Its Compabloc and AlfaNova product lines are widely adopted in distillation and hydrocracking applications, where space efficiency and high resistance to fouling are crucial.
Alfa Laval’s exchangers are often deployed in sulfur recovery and hydrogen production units due to their robust design and thermal optimization features. The company has also integrated smart diagnostics and performance tracking into select models, allowing predictive maintenance and real-time monitoring of heat transfer efficiency in refineries.
Kelvion – Specializing in Air-Cooled and Plate Heat Exchanger Solutions
Kelvion holds around 8% of the advanced heat exchangers for refineries market share, with a strong focus on air-cooled and gasketed plate heat exchangers. Its K°Flex and K°Bloc series are widely used in cooling circuits and gas treatment applications in refineries, particularly in regions with water scarcity where air-based cooling is vital.
Kelvion has gained significant traction in the Middle East and Asia, where its modular and corrosion-resistant designs provide operational resilience in harsh environments. The company has recently expanded its production capacity in India to cater to rising demand from regional refinery expansion projects.
API Heat Transfer – Known for Tailor-Made Thermal Systems
API Heat Transfer is a key manufacturer with a 6%–7% share in the advanced heat exchangers for refineries market, particularly in North America and parts of Europe. Its Basco and Airtech brands are known for customized shell-and-tube exchangers, engineered specifically for high-pressure hydroprocessing and thermal cracking units.
The company specializes in design-to-order systems that meet exact process conditions, especially where high viscosity or corrosive fluids are involved. API Heat Transfer is also exploring smart monitoring integrations in its product lines to offer advanced operational intelligence in refinery applications.
SWEP – Leading in Compact Brazed Plate Heat Exchangers
SWEP has carved a niche in the compact heat exchanger segment, with an estimated 5% market share. Its B-series brazed plate heat exchangers are gaining popularity in refineries transitioning toward more modular, high-efficiency systems, especially for smaller-scale thermal processes such as condensate recovery, heat tracing, and auxiliary cooling.
SWEP’s units offer excellent heat transfer-to-footprint ratios, making them suitable for retrofitting existing refinery setups with limited space availability. These systems are also increasingly being used in renewable energy-integrated refinery models where energy recapture is prioritized.
Hisaka Works – High Performance in Asian Refinery Projects
With a stronghold in Asia, Hisaka Works accounts for approximately 4% of the global market, with a growing presence in Japan, China, and Southeast Asia. The company’s UX Series of plate heat exchangers are known for their high turbulence flow design and ability to handle chemically aggressive media, particularly in catalytic reforming and desulfurization units.
Hisaka has been a preferred supplier for refineries that require compact solutions with quick maintenance features. The brand has also emphasized environmentally friendly refrigerants and fluids in its designs, aligning with Asia’s push toward sustainable refining.
HRS Heat Exchangers – Emerging Force in Custom-Built Systems
HRS Heat Exchangers is gaining momentum, especially in custom and hybrid heat exchanger solutions. The company’s DTA Series and HRS MI Series feature corrugated tube designs that improve heat transfer in viscous and particulate-laden fluids, suitable for bitumen blending and heavy oil refining.
Although HRS commands a smaller 3% market share globally, it has become a go-to solution provider for niche refinery applications, particularly where off-the-shelf systems fail to meet complex process requirements. Its expanding footprint in Latin America and the Middle East is contributing to its rising profile in the industry.
Chart Industries – Dominance in Cryogenic Heat Exchange Systems
Chart Industries is a leader in cryogenic and LNG-compatible heat exchangers, with significant relevance in refineries incorporating natural gas processing and hydrogen production. Its Cold Box systems and Brazed Aluminum Heat Exchangers (BAHX) are particularly used in gas separation and liquefaction units.
Chart holds approximately 4% of the global advanced heat exchangers for refineries market and has recently partnered with several hydrogen infrastructure projects to deliver integrated thermal systems. Its technology is vital for achieving the ultra-low temperatures required in advanced refinery operations focused on LNG and clean fuels.
Advanced Heat Exchangers for Refineries Market Share Distribution by Manufacturer
The market share breakdown among key manufacturers reflects both geographic specialization and technology focus. Alfa Laval leads due to its dominance in plate and welded exchangers globally, while Kelvion and API Heat Transfer remain strong in specific regions and segments. Emerging players like HRS and SWEP are growing due to innovations in compact and custom designs.
Here is a representative breakdown of manufacturer market share:
- Alfa Laval – 13%
- Kelvion – 8%
- API Heat Transfer – 6.5%
- SWEP – 5%
- Hisaka Works – 4%
- Chart Industries – 4%
- HRS Heat Exchangers – 3%
- Others (regional and niche players) – 56.5%
The “Others” category includes numerous regional suppliers, especially in Asia and Latin America, who offer localized and cost-effective solutions for small and mid-sized refineries.
Recent Developments and Industry News in Advanced Heat Exchangers for Refineries Market
- January 2024 – Alfa Laval announced a $60 million investment into expanding its heat exchanger manufacturing plant in Sweden, aiming to increase production of its Compabloc and SpiralHeat series used in refinery revamps across Europe and the Middle East.
- March 2024 – Kelvion launched its next-gen K°Eco Plate Series with enhanced fouling resistance coatings designed specifically for sulfur-rich refinery streams. The launch targets refineries upgrading their sulfur recovery units.
- May 2023 – Hisaka Works secured a major contract to supply high-efficiency plate exchangers for a new hydrogen-integrated refinery project in Vietnam. The systems are expected to be operational by mid-2025.
- September 2023 – API Heat Transfer introduced a predictive maintenance software integration into its Basco exchangers, offering cloud-based analytics for real-time performance tracking. Early adopters in U.S. refineries report improved reliability and reduced service costs.
- November 2023 – Chart Industries signed a supply agreement with a Middle Eastern energy major to deliver cryogenic exchangers for a large-scale LNG and gas-to-liquid (GTL) refinery under development in Oman, expected to be completed by 2026.
These developments reflect a growing industry trend toward smart technology integration, sustainable manufacturing, and specialized thermal management systems designed for the evolving needs of global refineries.
“Advanced Heat Exchangers for Refineries Production Data and Advanced Heat Exchangers for Refineries Production Trend, Advanced Heat Exchangers for Refineries Production Database and forecast”
-
-
- Advanced Heat Exchangers for Refineries production database for historical years, 10 years historical data
- Advanced Heat Exchangers for Refineries production data and forecast for next 7 years
-
Market Scenario, Demand vs Supply, Average Product Price, Import vs Export, till 2035
- Global Advanced Heat Exchangers for Refineries Market revenue and demand by region
- Global Advanced Heat Exchangers for Refineries Market production and sales volume
- United States Advanced Heat Exchangers for Refineries Market revenue size and demand by country
- Europe Advanced Heat Exchangers for Refineries Market revenue size and demand by country
- Asia Pacific Advanced Heat Exchangers for Refineries Market revenue size and demand by country
- Middle East & Africa Advanced Heat Exchangers for Refineries Market revenue size and demand by country
- Latin America Advanced Heat Exchangers for Refineries Market revenue size and demand by
- Import-export scenario – United States, Europe, APAC, Latin America, Middle East & Africa
- Average product price – United States, Europe, APAC, Latin America, Middle East & Africa
- Market player analysis, competitive scenario, market share analysis
- Business opportunity analysis
Key questions answered in the Global Advanced Heat Exchangers for Refineries Market Analysis Report:
- What is the market size for Advanced Heat Exchangers for Refineries in United States, Europe, APAC, Middle East & Africa, Latin America?
- What is the yearly sales volume of Advanced Heat Exchangers for Refineries and how is the demand rising?
- Who are the top market players by market share, in each product segment?
- Which is the fastest growing business/ product segment?
- What should be the business strategies and Go to Market strategies?
The report covers Advanced Heat Exchangers for Refineries Market revenue, Production, Sales volume, by regions, (further split into countries):
- Asia Pacific (China, Japan, South Korea, India, Indonesia, Vietnam, Rest of APAC)
- Europe (UK, Germany, France, Italy, Spain, Benelux, Poland, Rest of Europe)
- North America (United States, Canada, Mexico)
- Latin America (Brazil, Argentina, Rest of Latin America)
- Middle East & Africa
Table of Contents:
Advanced Heat Exchangers for Refineries Market:
- Introduction to the Advanced Heat Exchangers for Refineries Market
- Overview of Heat Exchanger Technology in Refining Processes
- Importance of Advanced Heat Exchangers in Improving Efficiency and Sustainability
- Historical Development and Evolution of Heat Exchanger Systems in Refineries
- Types of Advanced Heat Exchangers Used in Refineries
- Shell and Tube Heat Exchangers
- Plate Heat Exchangers
- Air-cooled and Double Pipe Heat Exchangers
- Compact and Multi-stream Heat Exchangers
- Selection Criteria Based on Refining Process and Requirements
- Key Components and Materials of Advanced Heat Exchangers
- Materials Used for High-temperature and Corrosive Environments
- Heat Transfer Efficiency and Surface Area Considerations
- Customization for Specific Refinery Applications and Flow Configurations
- Applications of Advanced Heat Exchangers in Refineries
- Use in Crude Oil Distillation and Hydroprocessing Units
- Role in Catalytic Cracking and Refining of Petrochemicals
- Heat Recovery Systems and Their Impact on Energy Savings
- Emerging Applications in Renewable Fuel Production and Green Technologies
- Market Segmentation by Product Type and End-Use Industry
- By Product Type: Shell and Tube, Plate, Air-cooled, and Others
- By End-Use Industry: Oil & Gas Refining, Petrochemicals, Renewable Energy, and Others
- By Geography: North America, Europe, Asia-Pacific, and Emerging Markets
- Market Dynamics and Key Growth Drivers
- Growing Demand for Energy Efficiency and Cost Reduction in Refining Operations
- Technological Advancements in Heat Exchanger Design and Materials
- Increasing Pressure for Regulatory Compliance on Emissions and Energy Use
- Expanding Refinery Capacities and Modernization Projects
- Regional Market Insights
- North America: Technological Leadership and Market Trends
- Europe: Energy Efficiency Regulations and Their Impact on Market Growth
- Asia-Pacific: Rising Demand for Advanced Heat Exchangers in Expanding Refineries
- Latin America: Opportunities in Refinery Upgrades and New Construction
- Middle East & Africa: Investments in Oil & Gas Infrastructure and Energy Efficiency
- Market Size, Share, and Forecast (2023-2035)
- Global Market Overview and Projected Growth in the Refining Sector
- Regional Breakdown and Market Share Analysis
- Long-term Market Forecast for Advanced Heat Exchangers in Refineries
- Competitive Landscape and Key Market Players
- Leading Manufacturers of Advanced Heat Exchangers for Refineries
- Competitive Strategies and Market Positioning
- Analysis of Mergers, Acquisitions, and Partnerships in the Heat Exchanger Industry
- Technological Innovations in Advanced Heat Exchangers
- Developments in Heat Transfer Efficiency and Performance Optimization
- Integration of Digitalization and IoT for Monitoring and Control
- Innovations in Material Science for Enhanced Durability and Corrosion Resistance
- Pricing Trends and Market Valuation
- Price Dynamics and Key Factors Affecting Heat Exchanger Costs
- Historical Pricing Trends for Advanced Heat Exchangers in the Refining Industry
- Future Price Forecast and Economic Impact on Refinery Operations
- Sustainability and Environmental Considerations
- The Role of Advanced Heat Exchangers in Reducing Energy Consumption
- Compliance with Environmental Standards in Refineries
- Advancements in Eco-friendly Heat Exchanger Technologies
- Challenges and Barriers in the Advanced Heat Exchangers Market
- High Initial Investment and ROI Challenges in Refinery Projects
- Technological Barriers in Heat Exchanger Integration and Efficiency
- Regulatory Challenges and Standardization Issues Across Regions
- Investment Opportunities in the Advanced Heat Exchangers Market
- Key Investment Areas in the Oil & Gas and Petrochemical Sectors
- Emerging Markets and High-growth Areas for Heat Exchanger Adoption
- Strategic Insights for Investors in the Refining Industry
- Supply Chain and Distribution Networks
- Overview of the Advanced Heat Exchanger Supply Chain
- Key Suppliers and Global Distribution Strategies
- Trends in Sourcing Materials and Components for High-performance Heat Exchangers
- Risk Assessment and Mitigation Strategies
- Identifying Risks in Heat Exchanger Design, Manufacturing, and Operation
- Mitigation Strategies for Operational and Environmental Risks
- Risk Management Practices in Large-scale Refinery Projects
- Market Forecast (2025-2035)
- Long-term Growth Projections for Advanced Heat Exchangers in Refineries
- Technological Developments Shaping Future Market Trends
- Regional Growth Forecasts and New Opportunities in Refinery Operations
- Regulatory Framework and Compliance
- Key Regulations Affecting the Design and Operation of Heat Exchangers in Refineries
- Industry Standards and Certifications for Heat Exchanger Performance
- Compliance Challenges and Opportunities for Manufacturers and Operators
- Consumer Trends and Adoption Rates
- Growing Adoption of Advanced Heat Exchanger Systems in Refining
- Shifting Consumer Preferences for Energy-efficient and Sustainable Solutions
- Trends in Digital Integration and Automation in Refining Operations
- Conclusion and Strategic Recommendations
- Key Insights and Takeaways from the Advanced Heat Exchanger Market
- Strategic Recommendations for Refinery Operators, Manufacturers, and Investors
- Future Directions for Technological Innovation and Market Expansion
“Every Organization is different and so are their requirements”- Datavagyanik
Companies We Work With
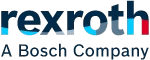
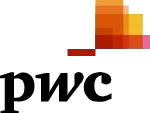
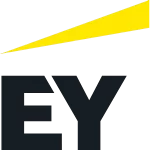
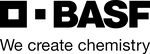
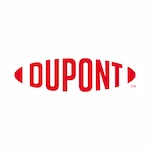

Do You Want To Boost Your Business?
drop us a line and keep in touch
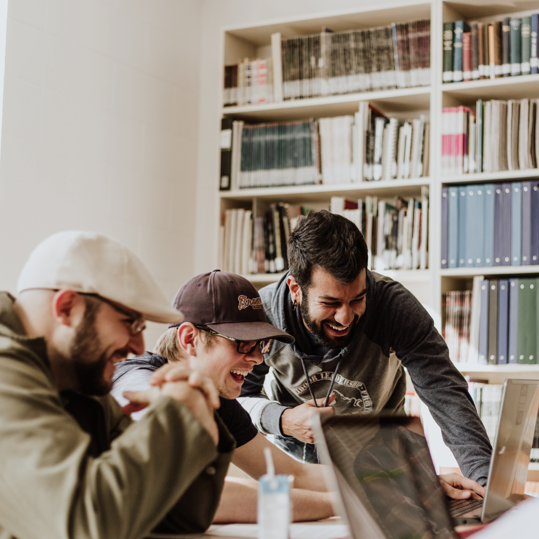