Manganese-Copper Alloys for Non-Magnetic Tools Market Size, Production, Sales, Average Product Price, Market Share, Import vs Export
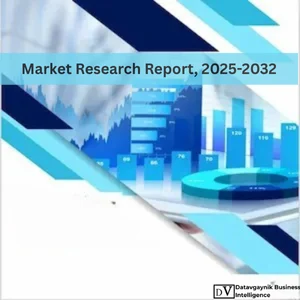
- Published 2025
- No of Pages: 120+
- 20% Customization available
Industrial Innovation Fueling Growth in the Manganese-Copper Alloys for Non-Magnetic Tools Market
The Manganese-Copper Alloys for Non-Magnetic Tools Market is experiencing a sharp upward trajectory, driven by the expanding use of non-magnetic tools in industries where magnetic interference cannot be tolerated. This includes applications in aerospace, semiconductor fabrication, medical diagnostics, and precision manufacturing. Each of these sectors demands tools with exceptional mechanical strength, high durability, and most critically, zero magnetic influence.
For instance, magnetic resonance imaging (MRI) facilities, a cornerstone of modern diagnostics, rely entirely on non-magnetic instruments to ensure accurate imaging. The global MRI market, valued at over 7.1 billion USD in 2023, is projected to grow at a compound annual growth rate (CAGR) of 6.5 percent through 2028. This growth directly impacts the Manganese-Copper Alloys for Non-Magnetic Tools Market, as the alloy is preferred for producing forceps, clamps, and adjustment tools used in MRI environments.
Semiconductor Industry Emerges as a Key Demand Driver in the Manganese-Copper Alloys for Non-Magnetic Tools Market
The semiconductor industry, fueled by increasing global demand for computing power, continues to be a major growth engine for the Manganese-Copper Alloys for Non-Magnetic Tools Market. Semiconductors are becoming smaller, more powerful, and more complex. As a result, the tools used in assembly and testing environments must eliminate any possibility of electromagnetic interference.
In 2023, global semiconductor revenues exceeded 600 billion USD, and projections suggest growth will continue toward 800 billion USD by 2027. Semiconductor foundries and electronics assembly lines require precise, non-magnetic tweezers, screwdrivers, and manipulation tools. Manganese-copper alloys are extensively used in these settings due to their proven performance in cleanroom conditions and their ability to retain form and functionality over prolonged use.
Datavagyanik also covers related markets such as the Non-Stick Coatings for Food Industry Tools Market. Exploring these markets offers a broader view of the industry landscape and how adjacent sectors influence the main topic.
Rising Aerospace Investments Strengthen the Manganese-Copper Alloys for Non-Magnetic Tools Market
Aerospace manufacturing demands an extraordinary level of precision and safety. In environments where magnetic instruments can disrupt avionics systems or navigation electronics, non-magnetic tools made from manganese-copper alloys are indispensable. The global aerospace industry exceeded 875 billion USD in spending in 2023, and its dependency on non-magnetic tooling continues to grow.
Aircraft manufacturers such as Boeing, Airbus, and Lockheed Martin increasingly use manganese-copper alloy tools during assembly and maintenance of critical components. For example, when fitting fuel delivery systems or wiring high-sensitivity sensor units, even minor magnetic disruption could cause severe operational faults. Manganese-copper alloys offer the resilience, strength, and neutrality that aerospace engineers depend on.
Electric Vehicle Expansion Accelerating Growth in the Manganese-Copper Alloys for Non-Magnetic Tools Market
The electric vehicle segment continues to revolutionize the automotive industry. Global EV sales reached 14 million units in 2023 and are projected to surpass 17 million by 2025. This transition requires new manufacturing methods and tools that are compatible with advanced electronics, battery management systems, and high-voltage wiring—all of which are sensitive to magnetic interference.
Manganese-copper alloys are widely adopted in EV assembly lines for their non-magnetic qualities and resistance to corrosion. Assembly of lithium-ion battery modules, motor windings, and inverter systems all rely on tools that must not influence the sensitive circuitry. The shift to electric mobility, supported by government subsidies and environmental regulations, is expected to increase the Manganese-Copper Alloys for Non-Magnetic Tools Market size significantly over the next decade.
Marine and Mining Sectors Expanding Use Cases in the Manganese-Copper Alloys for Non-Magnetic Tools Market
The marine, offshore, and mining industries operate in some of the harshest environments on the planet. Equipment must endure saltwater corrosion, high pressures, and fluctuating temperatures, all while avoiding interference with navigation and measurement instruments. Non-magnetic tools are not just preferred—they are required for safety and compliance.
In these sectors, manganese-copper alloys are ideal for tools such as torque wrenches, hammers, and pliers used in environments that are both corrosive and sensitive to magnetic fields. The global offshore drilling market alone is projected to reach 70 billion USD by 2027, expanding at a CAGR of 5.8 percent. As demand increases for subsea construction and maintenance, so too will the requirements for non-magnetic tooling, solidifying the role of manganese-copper alloys.
Medical Technology Driving Precision in the Manganese-Copper Alloys for Non-Magnetic Tools Market
The medical sector is a significant and growing contributor to the Manganese-Copper Alloys for Non-Magnetic Tools Market. As healthcare infrastructure expands, particularly in emerging economies, the demand for MRI-compatible surgical and diagnostic tools is rising. Manganese-copper alloys are the material of choice in medical environments because they do not interfere with magnetic imaging or sensitive electronics in diagnostic devices.
For example, precision tools used in neurosurgery, orthopedic procedures, and robotic-assisted surgeries are often required to be non-magnetic. In 2023, global medical device spending exceeded 570 billion USD. With MRI machines being installed at a CAGR of 7 percent globally, the downstream demand for compatible instruments is driving continued growth in manganese-copper alloy applications.
Growth in Additive Manufacturing Enhancing the Manganese-Copper Alloys for Non-Magnetic Tools Market
Advanced manufacturing technologies such as 3D printing are introducing new possibilities in tool production. Additive manufacturing enables the design and fabrication of custom non-magnetic tools for unique applications, particularly in medical, aerospace, and electronics sectors. Manganese-copper alloys are now being adapted for additive processes to meet the demand for complex geometries and high-precision tools.
The global additive manufacturing market reached 20 billion USD in 2023 and is projected to exceed 35 billion USD by 2028. Industries are turning to 3D-printed non-magnetic tools for prototype development, maintenance kits, and low-volume custom tools. This trend is directly feeding into the Manganese-Copper Alloys for Non-Magnetic Tools Market, creating new opportunities for alloy formulation and high-performance metallurgy.
Regulatory Standards and Safety Compliance Stimulating Market Demand
Industrial safety standards and stringent compliance protocols in sectors like aviation, nuclear energy, and explosives handling are increasing reliance on tools made from non-magnetic materials. Manganese-copper alloys meet these criteria due to their spark-resistant and corrosion-resistant nature, along with their structural reliability in high-stress environments.
For example, nuclear power facilities often require tools that will not generate magnetic fields near radiation sensors or automated robotic equipment. With over 440 nuclear reactors in operation globally and more under construction, the need for compliant tools is expected to rise. The same applies in the petrochemical sector, where hazardous material management depends on equipment that eliminates the risk of magnetic interference or accidental ignition.
Regional Markets Strengthening the Global Manganese-Copper Alloys for Non-Magnetic Tools Market Size
The Manganese-Copper Alloys for Non-Magnetic Tools Market size is seeing strong expansion across North America, Europe, and Asia Pacific. In the United States, the focus on aerospace and medical instrumentation continues to push domestic demand. European nations such as Germany, France, and the United Kingdom are investing in advanced automotive and electronics manufacturing, where non-magnetic tooling is essential.
Meanwhile, Asia Pacific—led by China, Japan, South Korea, and India—has emerged as the fastest-growing region. In 2023, Asia Pacific accounted for over 40 percent of the global electronics manufacturing output, making it a key region for non-magnetic tools demand. This has led to increased manganese-copper alloy production across the region, improving both availability and cost-efficiency for manufacturers.
“Track Country-wise Manganese-Copper Alloys for Non-Magnetic Tools Production and Demand through our Manganese-Copper Alloys for Non-Magnetic Tools Production Database”
-
-
- Manganese-Copper Alloys for Non-Magnetic Tools production database for 28+ countries worldwide
- Manganese-Copper Alloys for Non-Magnetic Tools Powder sales volume for 32+ countries
- Country-wise Manganese-Copper Alloys for Non-Magnetic Tools production capacity and production plant mapping, production capacity utilization for 28+ manufacturers
- Manganese-Copper Alloys for Non-Magnetic Tools production plants and production plant capacity analysis for top manufacturers
-
Asia Pacific Leads Global Expansion in the Manganese-Copper Alloys for Non-Magnetic Tools Market
Asia Pacific has become the central hub of demand in the Manganese-Copper Alloys for Non-Magnetic Tools Market, driven by the explosive growth of high-tech manufacturing, electronics, automotive, and medical equipment industries. Countries such as China, Japan, South Korea, and India are collectively responsible for over 45% of the global demand for non-magnetic tools.
For instance, China’s electronics production exceeded USD 2.2 trillion in 2023, reflecting its dominance in the global supply chain. With semiconductor plants expanding in regions like Shenzhen and Suzhou, the need for non-magnetic tools made from manganese-copper alloys has accelerated. Japanese companies such as Panasonic, Sony, and Toshiba rely on precision instruments made from non-magnetic materials for assembling microchips, sensors, and cleanroom systems.
South Korea’s emphasis on electric vehicle production, with Hyundai and Kia ramping up EV assembly lines, has added another layer of demand. India, which is positioning itself as a global electronics assembly hub through initiatives like “Make in India,” has seen domestic demand for non-magnetic tools grow at a CAGR of over 8% between 2020 and 2024.
North America Driving Strategic Growth in the Manganese-Copper Alloys for Non-Magnetic Tools Market
In North America, the United States remains a powerhouse for aerospace, medical, and defense manufacturing—all sectors where non-magnetic tools are essential. The region accounted for over 25% of the global Manganese-Copper Alloys for Non-Magnetic Tools Market in 2023 and is expected to maintain this momentum due to its high investment in innovation and infrastructure.
For example, the U.S. defense budget exceeded USD 840 billion in 2023, much of which is allocated toward advanced aircraft systems, radar technology, and communication systems. These applications require magnetic field-sensitive equipment, making non-magnetic tools indispensable. Medical institutions across the U.S. performed more than 40 million MRI procedures in 2023, creating consistent demand for manganese-copper alloy-based surgical and diagnostic tools.
Canada, though smaller in scale, contributes through mining and medical device manufacturing, particularly in Ontario and Quebec. Its focus on clean technologies and advanced materials is enhancing domestic consumption of non-magnetic alloys.
Europe Diversifies Applications in the Manganese-Copper Alloys for Non-Magnetic Tools Market
Europe’s diversified industrial economy is creating new opportunities across automotive, energy, and precision engineering sectors. Germany, France, and the United Kingdom are at the forefront, using manganese-copper alloys in automotive electronics, aircraft manufacturing, and cleanroom tools.
Germany’s automotive exports, valued at over USD 230 billion annually, rely heavily on tools that meet precision and safety standards, especially for electric drivetrains and digital dashboards. Manganese-copper alloys provide the needed mechanical reliability and non-magnetic characteristics. France, with its advanced nuclear and medical infrastructure, is among the leading importers of MRI-compatible surgical instruments, often built using copper-manganese blends.
Meanwhile, the UK aerospace industry, with companies like Rolls-Royce and BAE Systems, continues to invest in high-tolerance assembly techniques that depend on non-magnetic tools for calibration and maintenance.
Emerging Markets Contributing to Global Momentum in the Manganese-Copper Alloys for Non-Magnetic Tools Market
Beyond the traditional powerhouses, regions such as Latin America, the Middle East, and Africa are gradually increasing their stake in the Manganese-Copper Alloys for Non-Magnetic Tools Market. Brazil’s aerospace and oil extraction sectors, for instance, are steadily adopting non-magnetic tooling due to increased focus on offshore drilling safety and avionics manufacturing.
Saudi Arabia, through its Vision 2030 initiative, is investing in advanced healthcare infrastructure, including diagnostic imaging centers. The UAE is developing nuclear capabilities, which require precision tools with no magnetic properties. South Africa’s mining operations—accounting for over 7% of GDP—depend on non-magnetic tools in geological exploration, especially where magnetometers are used for mineral detection.
These emerging markets not only consume imported manganese-copper alloy products but also present opportunities for new manufacturing setups closer to end-use industries.
Global Production Trends Reshaping the Manganese-Copper Alloys for Non-Magnetic Tools Market
Global production of manganese-copper alloys is highly concentrated in Asia, particularly China, Japan, and South Korea, which together supply over 55% of global volumes. China leads in both raw material extraction and alloy production, exporting significant volumes to Europe and North America.
In 2023, China produced more than 480,000 metric tons of copper-manganese alloys, fueled by low-cost labor, advanced smelting facilities, and vertically integrated electronics manufacturing. Japan focuses on precision-grade alloys suited for medical and aerospace tooling. South Korea, meanwhile, leads in exporting high-performance non-magnetic alloys for electronics and EV applications.
India has recently expanded its domestic capacity, with state-run and private metallurgical firms increasing annual output to meet the rising demands from domestic EV, medical, and nuclear sectors.
Segmented Demand Reflects Diversification of the Manganese-Copper Alloys for Non-Magnetic Tools Market
The Manganese-Copper Alloys for Non-Magnetic Tools Market is segmented across multiple dimensions—application, industry, and material composition—each contributing differently to growth and demand behavior.
From an application standpoint, medical imaging tools and semiconductor assembly tools account for the largest market share, contributing nearly 38% combined as of 2023. Tools used in explosive environments, such as anti-spark hammers and screwdrivers, represent a growing niche segment, with increasing demand in military and chemical processing plants.
Material composition also varies—high manganese variants are typically used in rugged, corrosion-prone environments like mining, while copper-manganese-silicon combinations are popular in aerospace for their enhanced conductivity and temperature resistance.
From an end-user perspective, electronics remains the dominant sector, followed by aerospace, automotive, and medical. Collectively, these segments are projected to push the market CAGR beyond 6.7% through 2030.
Analyzing the Manganese-Copper Alloys for Non-Magnetic Tools Price Trend Across Regions
The Manganese-Copper Alloys for Non-Magnetic Tools Price has shown consistent upward movement since 2020, primarily due to increased demand, raw material volatility, and supply chain realignments post-pandemic. Between Q1 2021 and Q4 2023, average prices rose by nearly 18%, with fluctuations driven largely by global copper price surges.
For example, copper prices reached USD 9,200 per metric ton in early 2023, the highest in nearly a decade. Since manganese is often imported by alloy manufacturers, particularly in Europe and the U.S., exchange rate volatility and geopolitical factors have further influenced production costs.
The Manganese-Copper Alloys for Non-Magnetic Tools Price Trend also reflects growing customization in alloy compositions. Specialty grades for medical and aerospace use command premiums of 10% to 20% over standard grades due to stringent testing, certification, and higher performance benchmarks.
Future Outlook on the Manganese-Copper Alloys for Non-Magnetic Tools Price and Cost Efficiency
The Manganese-Copper Alloys for Non-Magnetic Tools Price is expected to stabilize over the next 3 to 5 years as new production capacity comes online and recycling technologies improve. Smelters in India and Southeast Asia are scaling operations with cleaner processes, potentially reducing production costs by 12% to 15% by 2027.
Additionally, advancements in alloy formulation—such as incorporating trace elements for improved machinability—are likely to enhance performance without drastically raising material costs. Manufacturers are also investing in automation for alloy processing, which may help offset labor costs in developed markets.
The Manganese-Copper Alloys for Non-Magnetic Tools Price Trend will likely remain sensitive to raw copper prices, which are influenced by global infrastructure spending, EV battery production, and geopolitical supply chain risks.
Import-Export Dynamics Supporting Global Distribution in the Manganese-Copper Alloys for Non-Magnetic Tools Market
Global trade in manganese-copper alloys is robust, with China, South Korea, and Japan being the leading exporters. North America and Europe are net importers, with the United States and Germany among the largest buyers due to their dependence on imported alloys for aerospace, automotive, and medical device production.
In 2023, exports from Asia to Europe grew by 11%, particularly for specialized medical-grade alloys. Meanwhile, India’s exports to Africa and Latin America increased by 14% year-on-year, signaling growing outreach to emerging markets with rising healthcare and industrial tooling needs.
Trade is expected to intensify as regional production remains insufficient in high-growth markets like Brazil, UAE, and Indonesia. The Manganese-Copper Alloys for Non-Magnetic Tools Price in these regions tends to be 8% to 12% higher due to import duties, logistics costs, and limited local refining capacity.
“Manganese-Copper Alloys for Non-Magnetic Tools Manufacturing Database, Manganese-Copper Alloys for Non-Magnetic Tools Manufacturing Capacity”
-
-
- Manganese-Copper Alloys for Non-Magnetic Tools top manufacturers market share for 28+ manufacturers
- Top 8 manufacturers and top 18 manufacturers of Manganese-Copper Alloys for Non-Magnetic Tools in North America, Europe, Asia Pacific
- Production plant capacity by manufacturers and Manganese-Copper Alloys for Non-Magnetic Tools production data for 28+ market players
- Manganese-Copper Alloys for Non-Magnetic Tools production dashboard, Manganese-Copper Alloys for Non-Magnetic Tools production data in excel format
-
Leading Manufacturers Driving the Manganese-Copper Alloys for Non-Magnetic Tools Market
The Manganese-Copper Alloys for Non-Magnetic Tools Market is shaped by a mix of global industrial metallurgists, specialty alloy producers, and vertically integrated manufacturing giants. These companies are setting benchmarks in alloy quality, production scalability, and precision tool applications across aerospace, medical, electronics, and energy sectors. Their focus on proprietary compositions, corrosion-resistant blends, and cleanroom-compatible grades has pushed the market toward customized, high-performance offerings.
Mitsubishi Materials Corporation
Mitsubishi Materials has long held a commanding position in the Manganese-Copper Alloys for Non-Magnetic Tools Market. Known for its MMAC non-magnetic alloy range, the company serves aerospace and precision electronics markets extensively. Its copper-manganese series exhibits high mechanical strength while offering minimal magnetic permeability, making them ideal for tool manufacturing in avionics assembly and MRI maintenance environments.
The company holds a significant market share in East Asia and supplies to both domestic and international OEMs. Mitsubishi’s alloys are widely used in the production of MRI-compatible forceps and instruments for semiconductor cleanrooms. The firm’s 2023 expansion of its Tsukuba plant has boosted its annual non-magnetic alloy output by 15%, supporting its export to North America and Europe.
Hitachi Metals (A Proterial Group Company)
Hitachi Metals, now part of the Proterial portfolio, has made a name for itself with its low-permeability, corrosion-resistant non-magnetic alloys tailored for tools used in nuclear power facilities, aerospace repair kits, and anti-explosive environments. Its product line under the Neomax Tooling Series integrates copper-manganese-nickel alloys optimized for high fatigue resistance.
The firm’s market share is particularly strong in Japan and Southeast Asia, accounting for approximately 9–11% of the global Manganese-Copper Alloys for Non-Magnetic Tools Market. It continues to lead in providing materials used in robotic surgical toolsets and cleanroom-grade tweezers.
Materion Corporation
Based in the United States, Materion Corporation is a dominant player in North America’s Manganese-Copper Alloys for Non-Magnetic Tools Market. Its product portfolio includes Brush Wellman non-magnetic copper alloys, specifically designed for aerospace and defense applications.
Materion’s Alloys C17510 and C17500 are extensively used in tool-making for avionics systems, particularly in environments requiring high thermal conductivity and dimensional stability. The company has built strong supply chains with Lockheed Martin and Raytheon, reinforcing its role in defense-grade tooling applications. Materion holds an estimated 13–15% market share in the North American segment, with strong prospects in electric vehicle battery plant tooling.
Luvata Group
Luvata, with production hubs in Finland and the United States, has emerged as a specialist in precision non-magnetic alloy production, catering to manufacturers of non-magnetic tools used in semiconductor and optical device assembly. Its Luvata NM Series, a copper-manganese blend with enhanced ductility, is favored for tools that require micrometer-level precision.
Luvata controls roughly 7–9% of the global Manganese-Copper Alloys for Non-Magnetic Tools Market and has established itself as a preferred supplier to European medical device manufacturers. Its alloys are also widely applied in anti-spark hand tools used in gas detection and chemical handling.
POSCO
South Korea’s POSCO, one of the world’s largest steelmakers, has extended its reach into specialty alloys, including non-magnetic copper-manganese variants. The company’s industrial-grade alloys serve toolmakers in electronics and shipbuilding, particularly for anti-spark and high-resilience tools. POSCO’s emphasis is on large-volume industrial contracts, supplying alloy billets and forgings to downstream tool manufacturers across Asia.
By volume, POSCO holds nearly 10% of the Asia-Pacific Manganese-Copper Alloys for Non-Magnetic Tools Market. Its recent investment in automated alloy casting lines in Pohang has expanded its production capacity, meeting growing demand from EV assembly and marine instrumentation sectors.
DOWA Metaltech
DOWA, a Japanese metallurgical firm, has steadily gained traction with its Dowa-NM grade, a specialized copper-manganese alloy with superior non-magnetic and wear-resistant properties. The firm focuses on low-batch, high-precision alloys used in tools for aerospace assembly lines and MRI tool kits. DOWA’s key advantage lies in its customization capabilities and integration with OEM requirements for robotic tool interfaces.
DOWA’s market share remains niche, accounting for 4–6%, but it is widely recognized for its high-grade materials used in specialized instruments. Its alloys are found in cleanroom-rated toolsets used in chip packaging and wafer processing units.
Indian Players Entering the Manganese-Copper Alloys for Non-Magnetic Tools Market
In recent years, Indian metallurgical firms such as Hindalco and Mishra Dhatu Nigam (MIDHANI) have begun to explore the Manganese-Copper Alloys for Non-Magnetic Tools Market, particularly as the country pushes forward with EV and defense industrialization. These manufacturers are developing copper-manganese alloy rods and billets for local toolmakers, especially for use in power electronics and mining tools.
Though currently contributing under 5% of global market share, Indian producers are rapidly scaling production. New smelting and alloying facilities in Gujarat and Telangana are expected to raise output by over 20% year-on-year through 2026.
Manganese-Copper Alloys for Non-Magnetic Tools Market Share Overview
As of 2024, the top five manufacturers—Materion, Mitsubishi Materials, Hitachi Metals (Proterial), POSCO, and Luvata—collectively control over 55% of the global Manganese-Copper Alloys for Non-Magnetic Tools Market. Materion leads in North America, Mitsubishi dominates East Asia, and POSCO maintains a strong foothold across bulk tooling applications in the Asia Pacific region.
Emerging players in India and Southeast Asia are gradually challenging the legacy hold of traditional suppliers, but the technical complexity of alloy customization remains a high barrier to entry, preserving the dominance of established global producers.
Recent Developments in the Manganese-Copper Alloys for Non-Magnetic Tools Market
- In January 2024, Mitsubishi Materials announced the commercial rollout of a new ultra-low permeability copper-manganese alloy for aerospace-grade tool manufacturing. The material offers 25% higher fatigue resistance than its predecessor.
- In March 2024, Materion began construction of a new alloy processing facility in Arizona, aimed at supplying high-conductivity, non-magnetic alloys to electric vehicle OEMs in the southwestern United States.
- POSCO, in Q4 2023, launched a collaboration with Samsung Electronics to develop alloy toolsets for smart factory environments, optimizing for robotic integration and magnetic field neutrality.
- DOWA Metaltech expanded its research lab in Nagoya in February 2024 to develop alloys for next-generation surgical robots used in MRI-guided procedures.
- Hindalco Industries initiated pilot production of manganese-copper billets in February 2024, targeting the growing demand for EV powertrain assembly tools within India.
“Manganese-Copper Alloys for Non-Magnetic Tools Production Data and Manganese-Copper Alloys for Non-Magnetic Tools Production Trend, Manganese-Copper Alloys for Non-Magnetic Tools Production Database and forecast”
-
-
- Manganese-Copper Alloys for Non-Magnetic Tools production database for historical years, 10 years historical data
- Manganese-Copper Alloys for Non-Magnetic Tools production data and forecast for next 7 years
-
Market Scenario, Demand vs Supply, Average Product Price, Import vs Export, till 2035
- Global Manganese-Copper Alloys for Non-Magnetic Tools Market revenue and demand by region
- Global Manganese-Copper Alloys for Non-Magnetic Tools Market production and sales volume
- United States Manganese-Copper Alloys for Non-Magnetic Tools Market revenue size and demand by country
- Europe Manganese-Copper Alloys for Non-Magnetic Tools Market revenue size and demand by country
- Asia Pacific Manganese-Copper Alloys for Non-Magnetic Tools Market revenue size and demand by country
- Middle East & Africa Manganese-Copper Alloys for Non-Magnetic Tools Market revenue size and demand by country
- Latin America Manganese-Copper Alloys for Non-Magnetic Tools Market revenue size and demand by
- Import-export scenario – United States, Europe, APAC, Latin America, Middle East & Africa
- Average product price – United States, Europe, APAC, Latin America, Middle East & Africa
- Market player analysis, competitive scenario, market share analysis
- Business opportunity analysis
Key questions answered in the Global Manganese-Copper Alloys for Non-Magnetic Tools Market Analysis Report:
- What is the market size for Manganese-Copper Alloys for Non-Magnetic Tools in United States, Europe, APAC, Middle East & Africa, Latin America?
- What is the yearly sales volume of Manganese-Copper Alloys for Non-Magnetic Tools and how is the demand rising?
- Who are the top market players by market share, in each product segment?
- Which is the fastest growing business/ product segment?
- What should be the business strategies and Go to Market strategies?
The report covers Manganese-Copper Alloys for Non-Magnetic Tools Market revenue, Production, Sales volume, by regions, (further split into countries):
- Asia Pacific (China, Japan, South Korea, India, Indonesia, Vietnam, Rest of APAC)
- Europe (UK, Germany, France, Italy, Spain, Benelux, Poland, Rest of Europe)
- North America (United States, Canada, Mexico)
- Latin America (Brazil, Argentina, Rest of Latin America)
- Middle East & Africa
Table of Contents:
Manganese-Copper Alloys for Non-Magnetic Tools Market
- Introduction to Manganese-Copper Alloys
-
- Overview of Manganese-Copper Alloys
- Importance in Non-Magnetic Applications
- Key Characteristics of Manganese-Copper Alloys
-
- Non-Magnetic Properties
- High Strength and Corrosion Resistance
- Thermal and Electrical Conductivity
- Applications of Manganese-Copper Alloys
-
- Non-Magnetic Tools for Hazardous Environments
- Applications in Oil & Gas, Aerospace, and Medical Sectors
- Use in Electronic and Scientific Equipment
- Market Overview and Trends (2020–2035)
-
- Global Market Dynamics and Drivers
- Emerging Trends in Non-Magnetic Materials
- Segmentation by Alloy Type
-
- High Manganese Content Alloys
- Low Manganese Content Alloys
- Custom Alloy Compositions
- Regional Market Analysis: North America
-
- Demand from Key Industries
- Production and Consumption Trends
- Regional Market Analysis: Europe
-
- Growth of Non-Magnetic Tool Manufacturing
- Impact of Regulatory Standards
- Regional Market Analysis: Asia-Pacific
-
- Manufacturing Hubs and Emerging Players
- Applications in High-Growth Sectors
- Regional Market Analysis: Latin America
-
- Adoption of Non-Magnetic Tools in Mining and Oil Industries
- Market Opportunities and Barriers
- Regional Market Analysis: Middle East & Africa
- Role in Petrochemical and Energy Industries
- Challenges in Material Availability
- Advancements in Manganese-Copper Alloy Production
- Innovations in Alloy Formulation
- Improvements in Manufacturing Techniques
- Supply Chain and Raw Material Analysis
- Sourcing of Manganese and Copper
- Global Supply and Distribution Networks
- Cost Structure of Manganese-Copper Alloys
- Raw Material Costs
- Processing and Manufacturing Expenses
- Price Trends and Influences
- Non-Magnetic Tools: Key Applications and Demand Drivers
- Safety Tools for Explosive Environments
- High-Precision Tools for Scientific Research
- Competitive Landscape and Key Players
- Major Manufacturers and Market Shares
- Strategies for Market Expansion
- Environmental and Sustainability Considerations
- Recycling of Manganese-Copper Alloys
- Environmental Impact of Alloy Production
- Market Regulations and Standards
- Safety and Quality Standards for Non-Magnetic Tools
- Regional Compliance Requirements
- Technological Innovations in Non-Magnetic Tools
- Advanced Designs Using Manganese-Copper Alloys
- Integration with Cutting-Edge Manufacturing Processes
- Global Trade and Export Dynamics
- Exporting Nations and Key Import Markets
- Impact of Trade Agreements on the Market
- Price Analysis and Forecast (2020–2035)
- Historical and Current Price Trends
- Regional Variations and Future Projections
- Emerging Applications of Manganese-Copper Alloys
- Role in Renewable Energy Systems
- Use in Advanced Medical Equipment
- Adoption Trends in High-Risk Industries
- Oil & Gas Exploration
- Defense and Aerospace Applications
- Challenges in the Market
- Material Availability and Cost Fluctuations
- Competition from Alternative Materials
- Investment and R&D in Manganese-Copper Alloys
- Funding for New Alloy Development
- Research Collaborations Between Academia and Industry
- Opportunities in Emerging Economies
- Market Growth in Developing Regions
- Government Support for Local Manufacturing
- Distribution and Sales Channels
- Key Distribution Networks
- Strategies for Market Penetration
- Consumer Preferences and Insights
- Demand for Durable and Safe Non-Magnetic Tools
- Industry-Specific Requirements
- Impact of Automation and AI on Alloy Manufacturing
- Smart Factories and Process Optimization
- Role of AI in Material Testing and Development
- Future Market Trends and Opportunities
- Growth in High-Tech Industries
- Role of Sustainable Manufacturing Practices
- Global Production and Consumption Forecast (2025–2035)
- Regional Insights and Production Capacities
- Consumption Trends Across Key Industries
- Case Studies of Manganese-Copper Alloy Applications
- Success Stories in Non-Magnetic Tool Design
- Industry-Specific Performance Examples
- Risk Management and Market Challenges
- Mitigating Supply Chain Risks
- Addressing Technological and Market Barriers
- Strategic Recommendations for Stakeholders
- Growth Strategies for Manufacturers
- Recommendations for End-User Adoption
- Conclusion and Long-Term Market Outlook
- Summary of Key Insights
- Projections for Market Growth and Innovation
“Every Organization is different and so are their requirements”- Datavagyanik
Companies We Work With
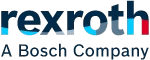
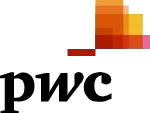
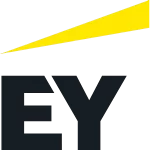
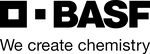
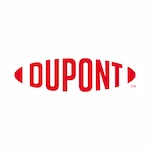

Do You Want To Boost Your Business?
drop us a line and keep in touch
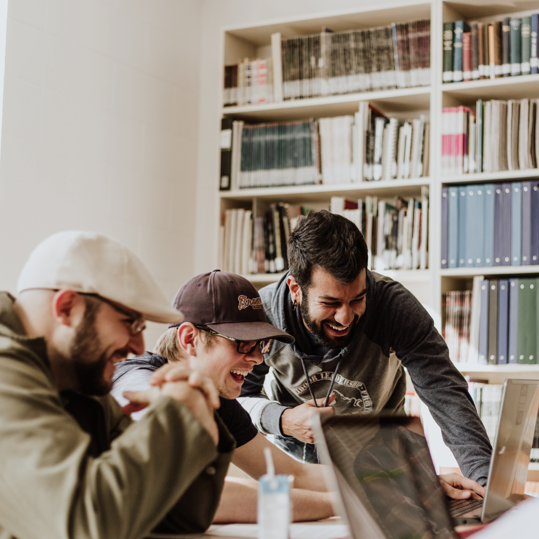