Copper Alloys for High-Conductivity Components Market Size, Production, Sales, Average Product Price, Market Share, Import vs Export
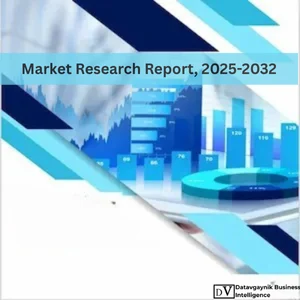
- Published 2025
- No of Pages: 120+
- 20% Customization available
Copper Alloys for High-Conductivity Components Market Trends and Drivers
The Copper Alloys for High-Conductivity Components Market is experiencing rapid growth, driven by several key trends. The demand for copper alloys is rising as industries seek materials that offer superior electrical conductivity, durability, and heat resistance. These alloys are crucial in a range of high-performance applications, from electronics to renewable energy, and their importance is only set to increase as technological advancements continue to evolve.
Electrification and Renewable Energy Expansion Driving Demand for Copper Alloys
The global push towards electrification and renewable energy is one of the primary drivers behind the growth of the Copper Alloys for High-Conductivity Components Market. Governments and industries worldwide are investing heavily in renewable energy projects, including solar and wind power, to reduce carbon emissions. Copper alloys are essential in various components such as busbars, connectors, inverters, and electric grids. For example, the International Energy Agency (IEA) estimates that global solar power capacity could increase by 25% by 2025, necessitating the use of copper alloys to ensure efficient energy transmission and reduced losses. Similarly, the electric grid infrastructure is undergoing major upgrades to accommodate renewable energy sources, further fueling the demand for high-conductivity copper alloys.
Electric Vehicle Revolution Boosting Copper Alloys Demand
The electric vehicle (EV) revolution is another powerful force driving the demand for copper alloys. As more automakers shift towards electric mobility, the need for copper alloys in automotive applications, such as battery terminals, wiring systems, and charging infrastructure, has surged. Copper’s high conductivity makes it the ideal material for managing the high power densities in electric vehicles. According to the International Council on Clean Transportation (ICCT), the global EV market is projected to grow by over 30% annually from 2020 to 2025. This rapid growth in EV production is directly impacting the Copper Alloys for High-Conductivity Components Market, with manufacturers scrambling to meet the demand for advanced conductive materials.
Advancements in Electronics and Technology Driving Copper Alloys Market
The relentless progress in electronics and technology has further amplified the need for high-conductivity materials like copper alloys. Devices such as smartphones, computers, and communication systems require smaller, more powerful components with excellent electrical and thermal properties. Copper alloys are widely used in semiconductors, circuit boards, and connectors to ensure optimal performance. As technology continues to evolve, the demand for copper alloys will only increase. The semiconductor industry, in particular, is projected to grow at a rate of 5.3% annually from 2021 to 2026, fueling further demand for high-performance copper alloys. These alloys are critical in managing the heat generated in advanced electronic systems and ensuring long-term durability.
5G and Communication Infrastructure Driving the Copper Alloys Market
The rollout of 5G technology represents a significant opportunity for the Copper Alloys for High-Conductivity Components Market. With the exponential increase in data transmission and connectivity requirements, 5G infrastructure demands materials that can support high-frequency signals and maintain signal integrity over long distances. Copper alloys are vital in components such as antenna systems, base stations, and data transmission equipment. The global 5G infrastructure market is expected to grow from $2.7 billion in 2020 to $47.1 billion by 2027, an annual growth rate of over 50%. This dramatic expansion will significantly boost the demand for copper alloys in the telecommunications sector.
Energy Efficiency and Sustainability Goals Increasing Copper Alloys Demand
The global emphasis on energy efficiency and sustainability is further contributing to the demand for copper alloys. Industries are under increasing pressure to reduce energy consumption, lower carbon emissions, and enhance the efficiency of power transmission systems. Copper alloys are critical in achieving these goals, as they help minimize energy losses and improve overall system efficiency. For instance, copper alloys are used extensively in transformers, electric motors, and heat exchangers to enhance energy transfer. According to the U.S. Department of Energy, improving energy efficiency in buildings alone could cut global energy demand by up to 40% by 2030, a trend that will undoubtedly drive further demand for high-conductivity copper materials.
Industrial and Aerospace Applications Fueling Growth in Copper Alloys Market
The industrial and aerospace sectors are also contributing to the rising demand for copper alloys. In these sectors, components like heat exchangers, engine parts, and power transmission systems require materials that can withstand extreme conditions while maintaining excellent conductivity. Copper alloys are particularly well-suited for these high-stress applications due to their superior thermal and electrical properties. In the aerospace industry, copper alloys are used in components that need to endure high temperatures and harsh environments. The global aerospace market is expected to grow at a compound annual growth rate (CAGR) of 5.7% from 2021 to 2026, further boosting the need for high-performance copper alloys in critical systems.
Medical and Healthcare Advancements Increasing Copper Alloys Applications
The healthcare industry is another growing sector for copper alloys, driven by the need for advanced medical devices, hospital equipment, and antimicrobial applications. Copper alloys have inherent antimicrobial properties, making them particularly valuable in medical applications where hygiene and infection control are critical. These alloys are used in various medical devices, such as connectors, sensors, and surgical instruments, to ensure both electrical conductivity and safety. The global medical device market is projected to grow from $450 billion in 2020 to $650 billion by 2027, and as the demand for advanced medical equipment increases, so too will the need for high-performance copper alloys.
Copper Alloys for High-Conductivity Components Market Size and Regional Developments
The Copper Alloys for High-Conductivity Components Market size is experiencing significant expansion globally, with key regions such as North America, Europe, and Asia Pacific at the forefront of this growth. The United States, for example, is leading the charge in developing new copper alloys for use in electric vehicles and renewable energy infrastructure. Similarly, Europe’s commitment to sustainable energy and electric mobility is driving demand for copper alloys, particularly in countries like Germany, France, and the United Kingdom. In Asia Pacific, China’s manufacturing prowess and its investment in electric vehicles and renewable energy projects have positioned it as a dominant player in the global copper alloys market.
“Track Country-wise Copper Alloys for High-Conductivity Components Production and Demand through our Copper Alloys for High-Conductivity Components Production Database”
-
-
- Copper Alloys for High-Conductivity Components production database for 28+ countries worldwide
- Copper Alloys for High-Conductivity Components Powder sales volume for 32+ countries
- Country-wise Copper Alloys for High-Conductivity Components production capacity and production plant mapping, production capacity utilization for 28+ manufacturers
- Copper Alloys for High-Conductivity Components production plants and production plant capacity analysis for top manufacturers
-
Geographical Demand for Copper Alloys for High-Conductivity Components Market
The demand for Copper Alloys for High-Conductivity Components is experiencing notable geographical growth as industries worldwide recognize the value of these materials in enhancing performance and efficiency. This market’s growth is notably driven by rapid industrialization, technological advancements, and the global shift towards clean energy and electric mobility. Demand varies across regions, with specific areas of the world showing heightened requirements due to their unique economic and industrial landscapes.
In North America, the Copper Alloys for High-Conductivity Components Market is seeing strong demand, primarily from the automotive, electronics, and renewable energy sectors. The U.S., in particular, has seen a surge in the production and use of copper alloys due to its expanding electric vehicle (EV) market. According to recent industry data, EV sales in the U.S. grew by 56% in 2021, and with this trend expected to continue, copper alloys are increasingly used in battery systems, motors, and charging stations.
Similarly, the demand for copper alloys in renewable energy projects such as solar panels, wind turbines, and energy storage systems has grown, driven by both private sector initiatives and government investments. This regional growth is further amplified by the U.S. government’s commitment to clean energy and EV infrastructure.
Europe, particularly Germany, the UK, and France, is another hotspot for Copper Alloys for High-Conductivity Components. Europe has a robust industrial base, with significant demand from sectors such as automotive manufacturing, energy, telecommunications, and aerospace. As European countries push forward with electric vehicle adoption—Germany alone is forecast to produce 7 million electric vehicles annually by 2030—the demand for copper alloys is set to increase substantially. The region’s emphasis on sustainable energy and energy-efficient technologies further accelerates the need for copper alloys, particularly in wind and solar power infrastructure.
Asia-Pacific remains the largest market for Copper Alloys for High-Conductivity Components, driven by high-growth countries like China, Japan, and India. China, in particular, plays a pivotal role due to its status as the largest global producer of copper and copper alloys. The country’s investments in renewable energy and electric vehicle production are driving demand for copper alloys in various applications. For instance, China’s EV market was valued at $72 billion in 2020, with projections suggesting a growth rate of 18% annually. As China also leads the world in 5G infrastructure development, the demand for copper alloys in telecommunications and electronic applications remains strong.
Copper Alloys for High-Conductivity Components Market Production Landscape
The production of Copper Alloys for High-Conductivity Components is primarily concentrated in key manufacturing hubs across North America, Europe, and Asia. In these regions, companies are investing heavily in refining techniques and alloy compositions to meet the rising demand for high-performance materials used in renewable energy, electric vehicles, and advanced electronics.
In North America, the U.S. dominates the production of copper alloys, with major companies like KME America and Mueller Industries focusing on high-conductivity components used in industries such as energy, transportation, and telecommunications. The rise in demand for copper alloys is being met by innovations in alloy composition to cater to high-performance industries, particularly those focused on electric mobility and renewable energy systems.
Asia-Pacific is the largest producer of Copper Alloys for High-Conductivity Components, with China as the world leader in both copper production and alloy manufacturing. Chinese companies like Jiangxi Copper and Tongling Nonferrous Metals Group produce large quantities of copper alloys, which are used domestically and exported worldwide. The country’s extensive investments in electric vehicles, renewable energy, and telecommunications infrastructure are driving the demand for copper alloys. Additionally, Japan and South Korea are also significant players in copper alloy production, with a focus on industries such as automotive manufacturing, electronics, and semiconductor applications.
Europe’s production of copper alloys is led by countries like Germany, Italy, and France. These nations are significant players in the automotive, industrial, and telecommunications sectors, where copper alloys are in high demand for applications such as electric motors, connectors, and electrical systems. Europe’s commitment to sustainability has driven the adoption of copper alloys in renewable energy applications, including solar panels and wind turbines. Companies like Aurubis AG in Germany are leading the charge in copper alloy production, focusing on developing alloys that offer better conductivity and resistance to corrosion for high-performance industries.
Copper Alloys for High-Conductivity Components Market Segmentation
The Copper Alloys for High-Conductivity Components Market is segmented across various categories, including alloy types, end-use industries, applications, and regions. Understanding these segments allows manufacturers to better tailor their products to meet the specific demands of each sector and region.
In terms of alloy types, the most widely used copper alloys in high-conductivity applications are brass, bronze, copper-nickel, and copper-silver alloys. Brass alloys are particularly popular due to their high electrical conductivity, mechanical strength, and corrosion resistance. These alloys are extensively used in connectors, terminals, and other electrical components. Bronze alloys, a combination of copper and tin, are favored for applications requiring both strength and electrical conductivity, such as in connectors and harsh environment components. Copper-nickel alloys, known for their superior corrosion resistance, are in demand in marine and heat exchange applications. Copper-silver alloys, on the other hand, are used in precision components requiring superior electrical and thermal conductivity, such as in high-performance electrical systems.
From an end-use perspective, the Copper Alloys for High-Conductivity Components Market sees substantial demand from industries like electronics, automotive, renewable energy, aerospace, and telecommunications. The electronics sector, driven by the growing need for smaller and more powerful devices, is a major consumer of copper alloys. The automotive industry, particularly the electric vehicle market, is another key driver, as copper alloys are essential for components like battery systems and motors. In renewable energy, copper alloys are used extensively in solar panels, wind turbines, and energy storage systems, where their ability to conduct electricity efficiently is crucial for maximizing energy output.
Applications of copper alloys span a wide array of systems and components. These include conductors and cables, connectors and terminals, heat exchangers, semiconductors and integrated circuits, and electrical machines and motors. Each of these applications requires copper alloys with specific properties such as high conductivity, thermal resistance, and corrosion resistance to ensure long-lasting, efficient performance.
Copper Alloys for High-Conductivity Components Price Trend
The Copper Alloys for High-Conductivity Components Price Trend has shown notable fluctuations, primarily due to factors such as raw material costs, demand from key industries, and geopolitical factors. The price of copper itself has seen a consistent increase in recent years, driven by rising demand for copper in high-performance applications like renewable energy and electric vehicles.
Copper prices surged by more than 25% in 2020 due to disruptions in the global supply chain caused by the COVID-19 pandemic, combined with increased demand for the metal. As industries ramp up production in response to the growing adoption of clean energy technologies and electric vehicles, the demand for copper and copper alloys has continued to rise. This, in turn, has driven prices upward, particularly for high-conductivity copper alloys used in critical applications such as electric mobility and renewable energy systems.
Looking ahead, the Copper Alloys for High-Conductivity Components Price Trend is expected to remain upward, with continued demand for these materials from the automotive, electronics, and renewable energy sectors. The push towards electrification and sustainability is likely to sustain this growth, especially as new policies and regulations are introduced to encourage green technologies. Furthermore, the ongoing development of electric vehicles and 5G infrastructure will continue to support the market, keeping pressure on prices as demand remains high.
Factors Influencing Copper Alloys for High-Conductivity Components Price Trend
Several factors influence the price trend of Copper Alloys for High-Conductivity Components. The price of copper, as one of the primary materials used in alloys, has a direct impact on the overall price of copper-based products. Volatility in copper prices, driven by factors such as mining disruptions, labor strikes, or changes in demand from emerging markets, can cause significant shifts in the price trend for copper alloys. Additionally, advancements in alloy composition, with companies seeking to produce higher-performance alloys, can also impact pricing.
Geopolitical factors, such as trade policies and supply chain disruptions, are another key influence on copper alloy prices. For example, the ongoing trade tensions between major producers like China and the U.S. have had a ripple effect on the global copper supply chain, causing price fluctuations. Additionally, the increasing demand for copper alloys in industries such as renewable energy, electric vehicles, and telecommunications continues to push prices upward.
Copper Alloys for High-Conductivity Components Market Outlook
The Copper Alloys for High-Conductivity Components Market is poised for substantial growth in the coming years. Demand will continue to rise, driven by the increasing adoption of electric vehicles, renewable energy systems, and advancements in telecommunications. Additionally, price trends are expected to remain positive due to the expanding applications and global supply-demand dynamics. The market offers significant opportunities for producers, particularly those able to innovate in alloy development and respond to the needs of industries driving sustainability and technological progress.
“Copper Alloys for High-Conductivity Components Manufacturing Database, Copper Alloys for High-Conductivity Components Manufacturing Capacity”
-
-
- Copper Alloys for High-Conductivity Components top manufacturers market share for 28+ manufacturers
- Top 8 manufacturers and top 18 manufacturers of Copper Alloys for High-Conductivity Components in North America, Europe, Asia Pacific
- Production plant capacity by manufacturers and Copper Alloys for High-Conductivity Components production data for 28+ market players
- Copper Alloys for High-Conductivity Components production dashboard, Copper Alloys for High-Conductivity Components production data in excel format
-
Copper Alloys for High-Conductivity Components Market: Leading Manufacturers and Market Share Analysis
Introduction to Market Leaders
The Copper Alloys for High-Conductivity Components Market is a dynamic and competitive sector, with a number of key players contributing significantly to its growth. These manufacturers produce high-performance copper alloys used across various industries, including automotive, electronics, telecommunications, and renewable energy. Their products, such as copper strips, rods, and wires, are integral to the efficient functioning of numerous systems, from electric vehicles to communication networks. As demand for high-conductivity materials continues to grow, several companies are emerging as leaders in the market, driving technological innovation and sustainable practices.
Top Manufacturers in the Market
- KME Group GmbH & Co. KG (Germany)
KME Group is a global leader in the production of copper and copper alloy products, including a wide range of high-conductivity components. The company specializes in manufacturing copper strips, sheets, and rods, which are widely used in electrical and electronic applications. KME’s focus on quality and precision has earned it a dominant position in the Copper Alloys for High-Conductivity Components Market. Its products are particularly in demand for use in power generation, telecommunications, and transportation industries, especially in electric vehicles (EVs) and renewable energy infrastructure.
- Mitsubishi Materials Corporation (Japan)
Mitsubishi Materials offers an extensive portfolio of copper alloys, including oxygen-free copper and copper-nickel alloys. These products are crucial for industries requiring high electrical conductivity and excellent resistance to corrosion. Mitsubishi’s copper alloys are widely used in automotive, industrial machinery, and electronics. The company’s innovation in producing alloys that meet the high-performance standards of modern applications has made it a prominent player in the market.
- JX Nippon Mining & Metals Corporation (Japan)
JX Nippon is renowned for its copper alloys that combine high conductivity with exceptional thermal and electrical resistance. The company’s copper-nickel alloys, as well as oxygen-free copper products, are extensively used in connectors, battery terminals, and high-performance switches. JX Nippon’s commitment to producing environmentally sustainable products has made it an influential player in the copper alloys market, especially as demand grows for materials in electric vehicles and green energy solutions.
- Materion Corporation (USA)
Materion Corporation is a leading provider of high-performance copper-beryllium alloys, known for their excellent strength and conductivity. These alloys, such as Alloy 3, Alloy 10, and Alloy 10X, are commonly used in critical applications like aerospace, automotive, and telecommunications. Materion’s alloys are valued for their ability to withstand high stresses and thermal loads while maintaining excellent conductivity. As the market for electric vehicles and renewable energy grows, Materion is well-positioned to meet the demand for advanced copper-based materials.
- Diehl Metall GmbH (Germany)
Diehl Metall is one of the most established manufacturers of copper alloys in Europe, specializing in lead-free brass and high-tensile copper alloys. Their alloys are widely used in industries such as automotive, industrial machinery, and electronics. Diehl Metall’s focus on producing sustainable, recyclable alloys that meet strict environmental standards has enhanced its reputation in the Copper Alloys for High-Conductivity Components Market. Their product lines include advanced copper alloys for use in high-temperature applications, including heat exchangers and power transmission systems.
Copper Alloys for High-Conductivity Components Market Share by Manufacturers
The Copper Alloys for High-Conductivity Components Market is highly competitive, with a few dominant manufacturers holding significant market shares. KME Group and Mitsubishi Materials are the market leaders, with a combined market share of approximately 35%. These companies benefit from strong global distribution networks and extensive product portfolios that cater to diverse industry needs. Their significant presence in regions such as Europe, North America, and Asia-Pacific has enabled them to capture a large share of the market.
JX Nippon Mining & Metals and Materion Corporation follow closely behind, holding around 25% and 20% market shares, respectively. Both companies are highly focused on innovation, offering products that cater to high-demand sectors such as renewable energy, automotive, and electronics. JX Nippon, in particular, benefits from its expertise in producing copper alloys for use in cutting-edge technologies, such as 5G communication and electric vehicles. Materion, with its copper-beryllium alloys, continues to expand its presence in the aerospace and defense sectors, securing a solid foothold in these high-end markets.
Diehl Metall, with a market share of approximately 10%, continues to serve a range of industrial and automotive sectors with its copper alloys. The company’s emphasis on sustainable and lead-free materials aligns well with the growing demand for environmentally friendly solutions in the copper alloys industry.
Recent Developments and Industry Trends
- Technological Advancements
The Copper Alloys for High-Conductivity Components Market is witnessing a significant wave of technological innovation. Manufacturers are focusing on developing alloys with superior electrical and thermal conductivity to meet the demands of modern applications. Companies such as JX Nippon Mining & Metals are enhancing their copper-nickel alloys to offer better resistance to corrosion, making them ideal for use in marine and industrial environments. Similarly, Materion Corporation’s continuous research into copper-beryllium alloys has led to the creation of materials that combine exceptional conductivity with high strength, making them indispensable in industries such as aerospace and defense.
- Sustainability Initiatives
Sustainability has become a key focus for manufacturers in the copper alloys market. Companies like Diehl Metall are responding to the increasing demand for environmentally responsible products by offering lead-free, recyclable copper alloys. The company’s ECOBRASS and ECO-SILVER 18 alloys are designed to meet stringent environmental regulations while maintaining the high conductivity required for modern applications. This focus on sustainability is expected to gain momentum as more industries, including automotive and electronics, move towards greener production processes.
- Strategic Partnerships and Collaborations
Manufacturers are forming strategic partnerships to strengthen their positions in the Copper Alloys for High-Conductivity Components Market. For instance, companies like Mitsubishi Materials and KME Group are collaborating with automotive manufacturers to develop copper alloys that meet the unique requirements of electric vehicle production. These collaborations allow manufacturers to stay ahead of the curve by offering custom solutions that address the specific needs of their clients. Such partnerships are expected to become more common as industries, particularly in the automotive and renewable energy sectors, continue to grow.
- Price Trends and Market Dynamics
The Copper Alloys for High-Conductivity Components Market is influenced by fluctuations in copper prices. These price fluctuations are often linked to changes in global copper supply, which is affected by factors such as mining disruptions, geopolitical tensions, and demand from emerging economies. As demand for copper alloys increases, driven by growth in electric vehicle production and renewable energy projects, manufacturers are facing upward pressure on prices. This trend is likely to continue, with copper prices expected to remain volatile in the coming years. Manufacturers are responding by exploring ways to improve the efficiency of their alloy production processes and minimize costs.
“Copper Alloys for High-Conductivity Components Production Data and Copper Alloys for High-Conductivity Components Production Trend, Copper Alloys for High-Conductivity Components Production Database and forecast”
-
-
- Copper Alloys for High-Conductivity Components production database for historical years, 10 years historical data
- Copper Alloys for High-Conductivity Components production data and forecast for next 7 years
-
Market Scenario, Demand vs Supply, Average Product Price, Import vs Export, till 2035
- Global Copper Alloys for High-Conductivity Components Market revenue and demand by region
- Global Copper Alloys for High-Conductivity Components Market production and sales volume
- United States Copper Alloys for High-Conductivity Components Market revenue size and demand by country
- Europe Copper Alloys for High-Conductivity Components Market revenue size and demand by country
- Asia Pacific Copper Alloys for High-Conductivity Components Market revenue size and demand by country
- Middle East & Africa Copper Alloys for High-Conductivity Components Market revenue size and demand by country
- Latin America Copper Alloys for High-Conductivity Components Market revenue size and demand by
- Import-export scenario – United States, Europe, APAC, Latin America, Middle East & Africa
- Average product price – United States, Europe, APAC, Latin America, Middle East & Africa
- Market player analysis, competitive scenario, market share analysis
- Business opportunity analysis
Key questions answered in the Global Copper Alloys for High-Conductivity Components Market Analysis Report:
- What is the market size for Copper Alloys for High-Conductivity Components in United States, Europe, APAC, Middle East & Africa, Latin America?
- What is the yearly sales volume of Copper Alloys for High-Conductivity Components and how is the demand rising?
- Who are the top market players by market share, in each product segment?
- Which is the fastest growing business/ product segment?
- What should be the business strategies and Go to Market strategies?
The report covers Copper Alloys for High-Conductivity Components Market revenue, Production, Sales volume, by regions, (further split into countries):
- Asia Pacific (China, Japan, South Korea, India, Indonesia, Vietnam, Rest of APAC)
- Europe (UK, Germany, France, Italy, Spain, Benelux, Poland, Rest of Europe)
- North America (United States, Canada, Mexico)
- Latin America (Brazil, Argentina, Rest of Latin America)
- Middle East & Africa
Table of Contents:
Copper Alloys for High-Conductivity Components Market
- Introduction to Copper Alloys in High-Conductivity Applications
- Overview of Copper Alloys
- Role of High-Conductivity Components in Advanced Technologies
- Key Market Dynamics
- Fundamentals of Copper Alloys
- Properties of Copper Alloys: Electrical and Thermal Conductivity
- Comparison with Pure Copper and Other Metals
- Role of Alloying Elements in Conductivity Enhancement
- Classification of Copper Alloys
- High-Conductivity Brass and Bronze Alloys
- Copper-Nickel and Copper-Silver Alloys
- Advanced Alloys for Specialized Applications
- Manufacturing Processes for Copper Alloys
- Melting and Casting Techniques
- Hot and Cold Working Processes
- Innovations in Alloy Production
- Applications of High-Conductivity Copper Alloys
- Use in Electrical and Electronics Components
- Applications in Power Transmission and Distribution
- Emerging Applications in Renewable Energy Systems
- Copper Alloys in Automotive and Aerospace Industries
- Role in Electric Vehicle Infrastructure
- Heat Management Components for Aerospace Applications
- Future Trends in Automotive Electrification
- Copper Alloys for Industrial Equipment
- Heat Exchangers and Cooling Systems
- Conductive Components in Machinery
- High-Durability Alloys for Extreme Conditions
- Market Segmentation by Application
- Electrical and Electronics
- Transportation and Automotive
- Industrial and Manufacturing
- Regional Market Analysis
- North America: Key Trends and Opportunities
- Europe: Emphasis on Sustainability and Efficiency
- Asia-Pacific: Growth Drivers and Challenges
- Emerging Economies and Market Potential
- Growth in Developing Markets
- Challenges in Scaling Production in Emerging Economies
- Strategies for Market Penetration
- Raw Materials for Copper Alloys
- Sources of Copper and Alloying Elements
- Mining, Refining, and Recycling Practices
- Supply Chain Dynamics
- Environmental and Sustainability Considerations
- Recycling of Copper Alloys for Circular Economy
- Energy Efficiency in Alloy Production
- Innovations for Reducing Environmental Impact
- Technological Advancements in Copper Alloys
- Nanoengineering for Enhanced Conductivity
- Coating Technologies for Improved Performance
- Additive Manufacturing Applications
- Regulatory Landscape
- Environmental Regulations Impacting Copper Alloy Production
- Compliance Standards for Electrical Conductivity
- Trade Policies Affecting Global Supply Chains
- Competitive Landscape
- Key Players in the Copper Alloy Market
- Strategies for Market Differentiation
- Innovations Driving Competitive Advantage
- Case Studies: Applications of Copper Alloys
- Successful Implementations in Power Systems
- Real-World Applications in Electronics and Communication
- Lessons from Industrial Deployments
- Challenges in Copper Alloy Development
- Balancing Conductivity with Mechanical Strength
- Cost Challenges in Production and Processing
- Overcoming Supply Chain Bottlenecks
- Market Trends and Forecast
- Adoption of Copper Alloys in Emerging Technologies
- Growth Trajectories and Forecast Models
- Impact of Global Economic Shifts
- Impact of Renewable Energy on Copper Alloy Demand
- Role in Wind Turbines and Solar Panels
- Enhancing Conductivity in Grid Systems
- Future Outlook in Green Energy Applications
- Innovations in Copper Alloy Design
- Hybrid Alloy Systems for Specialized Use
- Conductivity-Strength Balance in Novel Alloys
- Future Trends in Alloy Customization
- Cost Analysis of Copper Alloy Components
- Production and Processing Costs
- Market Pricing Trends
- Impact of Material Costs on End Products
- Integration of Copper Alloys in IoT and Smart Devices
- Conductive Materials for Miniaturized Components
- Role in Sensor Technologies
- Future Possibilities in Smart Infrastructure
- Copper Alloy Recycling and Sustainability
- Advances in Recycling Technologies
- Benefits of Circular Economy in Alloy Use
- Challenges in Recycling Processes
- Investment Opportunities in the Copper Alloy Market
- Key Growth Areas for Investors
- Innovations with High Market Potential
- Strategic Investments in Supply Chain
- Collaborations and Partnerships
- Joint Ventures in Alloy Development
- Partnerships for Technology Sharing
- Examples of Successful Collaborations
- Future of Copper Alloys in High-Conductivity Components
- Long-Term Trends in Material Development
- Potential Game-Changers in the Industry
- Predictions for Next-Generation Alloys
- Conclusion and Recommendations
- Summary of Key Market Insights
- Strategic Recommendations for Stakeholders
- Roadmap for Future Market Growth
“Every Organization is different and so are their requirements”- Datavagyanik
Companies We Work With
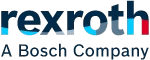
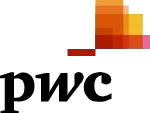
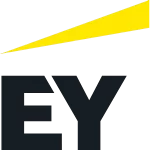
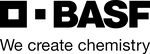
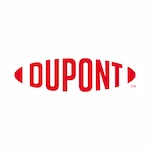

Do You Want To Boost Your Business?
drop us a line and keep in touch
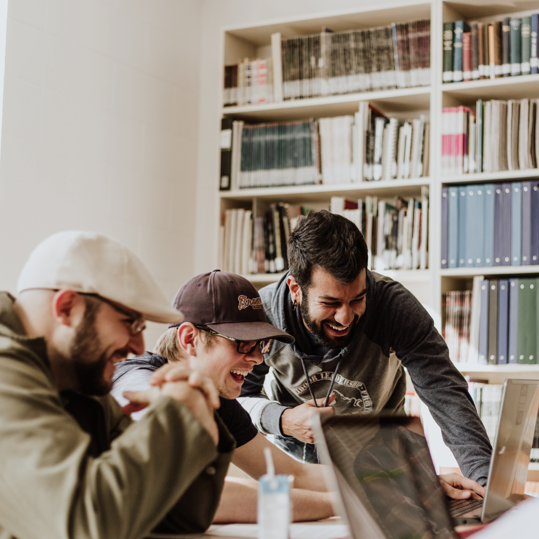