Hybrid Metal-Polymer Materials Market Size, Production, Sales, Average Product Price, Market Share, Import vs Export
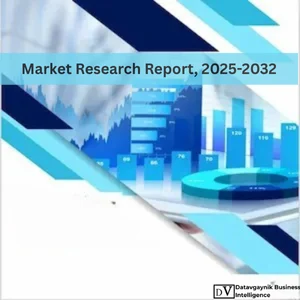
- Published 2025
- No of Pages: 120+
- 20% Customization available
Hybrid Metal-Polymer Materials Market: A Transformational Shift in Material Science
The Hybrid Metal-Polymer Materials Market is rapidly gaining momentum as industries across the globe recognize the unparalleled advantages these materials offer. These hybrid materials, which combine the properties of both metals and polymers, are being increasingly adopted across various sectors due to their remarkable mechanical, thermal, and environmental benefits. As technological advancements continue to evolve, the growth trajectory of the Hybrid Metal-Polymer Materials Market is expected to remain robust, driven by a demand for lightweight, durable, and versatile materials in critical applications. The following analysis delves into the key drivers and trends influencing this market, backed by data and practical examples.
Surge in Demand for Lightweight and Durable Materials in Automotive Industry
The automotive industry is a primary catalyst for the rapid expansion of the Hybrid Metal-Polymer Materials Market. The global push for reducing vehicle weight, improving fuel efficiency, and lowering carbon emissions is driving a substantial increase in the adoption of hybrid materials. According to recent estimates, the global automotive industry is projected to grow at a CAGR of 3.5% through 2027, with hybrid materials playing a pivotal role in meeting environmental regulations and achieving fuel economy goals.
For instance, in the United States alone, the automotive sector accounts for over 60% of the demand for hybrid metal-polymer materials. Manufacturers such as Ford, General Motors, and Volkswagen have already integrated these materials into key components, including bumpers, dashboards, and chassis. The hybrid combination of polymers, which provide lightweight properties, and metals, offering mechanical strength, helps manufacturers meet stringent emission standards without compromising on performance or safety.
Moreover, as electric vehicles (EVs) continue to gain market share, the demand for lightweight, high-strength materials to reduce battery load and increase driving range is expected to grow exponentially. The global EV market size is expected to reach over USD 800 billion by 2027, with a significant reliance on hybrid metal-polymer materials to optimize vehicle performance.
Datavagyanik also covers related markets such as the Hybrid Subsea Pumps Market. These related markets contribute valuable context to the primary topic by highlighting complementary trends and technologies.
Hybrid Metal-Polymer Materials Market’s Role in Aerospace Innovation
The aerospace industry is witnessing a transformative shift towards the use of hybrid metal-polymer materials for lightweight, durable components. With an increasing emphasis on fuel efficiency and sustainability, the aerospace sector has been quick to adopt materials that offer both strength and reduced weight. Hybrid materials, in particular, offer an ideal solution for various parts of an aircraft, including structural components, wings, and interior panels, where both weight reduction and durability are paramount.
In 2023 alone, global spending on aerospace materials grew by approximately 7%, with hybrid materials accounting for a significant portion of the growth. Industry giants like Boeing and Airbus are now extensively using hybrid metal-polymer composites in their new aircraft models. For instance, Boeing’s 787 Dreamliner utilizes carbon fiber composites and polymer-metal combinations to cut down on aircraft weight while maintaining structural integrity. Such innovations are anticipated to increase the adoption of hybrid metal-polymer materials as the aerospace industry strives to meet environmental targets and enhance overall aircraft efficiency.
Growth of Hybrid Metal-Polymer Materials Market in Electronics and Electrical Applications
The growing complexity and miniaturization of electronic devices is a pivotal factor driving the Hybrid Metal-Polymer Materials Market. With the ever-expanding demand for compact, high-performance devices, industries in electronics and electrical components are increasingly relying on hybrid materials. These materials are used in connectors, switches, casings, and other components that demand both high mechanical strength and electrical conductivity.
According to recent market statistics, the global electronics market, which is projected to reach over USD 1.8 trillion by 2027, is set to boost the adoption of hybrid metal-polymer materials significantly. A prime example can be seen in the mobile phone industry, where hybrid materials are utilized to create durable, lightweight casings that also provide excellent shock absorption. Companies like Samsung and Apple have incorporated hybrid materials in the production of smartphones and wearables, enhancing product durability while simultaneously reducing the overall weight.
Moreover, the rise of the Internet of Things (IoT) and wearable electronics is intensifying the demand for miniaturized components. Hybrid metal-polymer materials are ideal for creating robust, lightweight electronic enclosures capable of housing intricate components in a compact space. This trend is expected to continue as electronics manufacturers seek innovative materials to meet both performance and environmental standards.
Hybrid Metal-Polymer Materials Market’s Contribution to Advancements in Additive Manufacturing
Additive manufacturing, also known as 3D printing, is transforming the way industries produce complex parts, and the Hybrid Metal-Polymer Materials Market is at the forefront of this revolution. The unique combination of metal and polymer makes hybrid materials particularly well-suited for additive manufacturing, where intricate geometries and customized parts are often required.
In 2024, the global 3D printing market size reached USD 16.5 billion, and the demand for hybrid materials within this space has surged as manufacturers strive for greater flexibility, efficiency, and cost-effectiveness. For example, aerospace companies are utilizing additive manufacturing to produce customized, lightweight components with hybrid metal-polymer composites. This method not only reduces the lead time for production but also minimizes waste, aligning with the growing trend towards sustainability. The aerospace and automotive industries are expected to see a compound annual growth rate (CAGR) of 15% in 3D printed hybrid materials, indicating significant potential for future growth in this segment.
Sustainable Manufacturing and Environmental Impact in Hybrid Metal-Polymer Materials Market
Sustainability is becoming a critical focus across all industries, and the Hybrid Metal-Polymer Materials Market is no exception. The demand for eco-friendly and energy-efficient materials is escalating, as businesses and governments worldwide prioritize reducing their carbon footprint. Hybrid materials can be tailored to incorporate recycled metals and bio-based or recycled polymers, offering an environmentally conscious alternative to traditional materials.
The global push for sustainability is evident in the European Union’s Green Deal, which aims to achieve carbon neutrality by 2050. As part of these ambitious targets, European manufacturers are increasingly turning to hybrid materials to reduce the carbon footprint of their products. For example, automotive manufacturers like BMW and Volkswagen are using hybrid materials that combine recyclable metals with bio-based polymers, resulting in reduced environmental impact during production and end-of-life disposal.
Additionally, hybrid materials offer improved durability and longer life cycles, which contributes to lower overall energy consumption and less frequent need for replacement. This sustainability advantage is fueling the growth of the Hybrid Metal-Polymer Materials Market, particularly in industries like construction, where energy-efficient and long-lasting materials are critical for reducing environmental impact.
Customization and Versatility Driving Hybrid Metal-Polymer Materials Market Adoption
One of the key factors driving the Hybrid Metal-Polymer Materials Market is the customization and versatility offered by these materials. Hybrid materials can be tailored to meet specific performance requirements by adjusting the ratio of metal to polymer, selecting various types of metals and polymers, and modifying processing techniques. This flexibility allows manufacturers to create materials that cater to the unique needs of different applications, from medical devices to industrial components.
In industries such as medical devices and industrial manufacturing, the ability to modify the composition of hybrid materials ensures that they can provide the necessary mechanical properties for each specific application. For example, hybrid materials used in medical implants must offer a balance of biocompatibility, strength, and flexibility. Similarly, industrial components like gaskets and seals require materials that can withstand extreme conditions while maintaining their integrity. The growing demand for tailored, high-performance materials is expected to continue driving the Hybrid Metal-Polymer Materials Market’s growth across various sectors.
“Track Country-wise Hybrid Metal-Polymer Materials Production and Demand through our Hybrid Metal-Polymer Materials Production Database”
-
-
- Hybrid Metal-Polymer Materials production database for 28+ countries worldwide
- Hybrid Metal-Polymer Materials Powder sales volume for 32+ countries
- Country-wise Hybrid Metal-Polymer Materials production capacity and production plant mapping, production capacity utilization for 28+ manufacturers
- Hybrid Metal-Polymer Materials production plants and production plant capacity analysis for top manufacturers
-
Global Hybrid Metal-Polymer Materials Market: Geographical Demand and Production Overview
The demand for hybrid metal-polymer materials is witnessing a global surge, driven by technological advancements, sustainability needs, and the growing demand for lightweight yet durable materials across a broad range of industries. Different regions are seeing varying levels of demand, largely influenced by local industry requirements, manufacturing capabilities, and environmental regulations. As these materials are increasingly utilized in sectors such as automotive, aerospace, electronics, and healthcare, understanding the geographical demand and production dynamics of the Hybrid Metal-Polymer Materials Market is crucial.
North America’s Robust Demand for Hybrid Metal-Polymer Materials Market
North America, led by the United States and Canada, is one of the largest markets for hybrid metal-polymer materials. This growth is particularly driven by industries such as automotive, aerospace, and electronics, which rely heavily on lightweight and durable materials to meet stringent fuel efficiency and performance standards. In the automotive sector alone, North America’s market share in hybrid metal-polymer materials accounts for over 30% of the global demand.
In the United States, the demand is fueled by the automotive industry’s shift towards electric vehicles (EVs) and the automotive manufacturers’ ongoing push to reduce vehicle weight. For instance, Ford has made significant strides in integrating hybrid materials into its vehicle production to improve fuel economy and reduce emissions. Additionally, the aerospace sector, with players like Boeing and Lockheed Martin, is a prominent adopter of hybrid materials for lightweight components that maintain structural integrity. As North America continues to emphasize sustainability in production, the demand for hybrid metal-polymer materials is expected to grow at a steady pace, reinforcing its status as a leading region in the market.
Europe’s Hybrid Metal-Polymer Materials Market Growth Surge
Europe is a key player in the global Hybrid Metal-Polymer Materials Market, propelled by the continent’s focus on sustainability, energy efficiency, and high-performance manufacturing. The European Union’s commitment to achieving carbon neutrality by 2050 is creating robust demand for materials that can help reduce emissions and improve fuel efficiency across various sectors, especially automotive and aerospace.
Germany, a leader in automotive innovation, is heavily investing in hybrid metal-polymer materials, especially for its premium automotive brands like BMW and Volkswagen. These manufacturers are adopting hybrid materials in lightweight body components to enhance vehicle performance and comply with stringent environmental regulations. Similarly, the aerospace industry in Europe, led by Airbus, is incorporating hybrid materials into aircraft design to achieve fuel efficiency without compromising safety or performance. The rapid adoption of hybrid materials is expected to continue as Europe’s industrial sectors increasingly prioritize sustainable and energy-efficient solutions.
Asia Pacific Hybrid Metal-Polymer Materials Market: Rapid Expansion in Emerging Economies
The Asia Pacific region, comprising countries like China, Japan, South Korea, and India, is witnessing rapid growth in the demand for hybrid metal-polymer materials. This is largely driven by the expansion of manufacturing industries, particularly in the automotive, electronics, and aerospace sectors. China, being the world’s largest automotive market, is a major consumer of hybrid materials, with an increasing focus on electric vehicle production.
In 2024, China accounted for more than 35% of the global automotive market share, and with the nation’s aggressive push toward electric vehicles, the demand for lightweight materials is expected to skyrocket. Companies such as BYD and Geely are leading the charge in integrating hybrid materials into EV components like battery enclosures, body panels, and interior parts to reduce vehicle weight and enhance driving range. This transition is further fueled by China’s government policies that incentivize the use of eco-friendly materials in vehicle manufacturing, contributing to an increase in the demand for hybrid metal-polymer materials.
Japan and South Korea, on the other hand, are leveraging their technological expertise in electronics and aerospace to accelerate the adoption of hybrid materials. Japanese firms such as Toyota and Honda are extensively incorporating hybrid materials in electric vehicle production, while South Korean companies like Samsung and LG are using them in electronics and mobile device manufacturing. As these countries continue to expand their R&D efforts in material science, the market for hybrid metal-polymer materials in Asia Pacific is set to grow significantly in the coming years.
Hybrid Metal-Polymer Materials Market in Latin America and Middle East
In Latin America, hybrid metal-polymer materials are gaining traction, primarily in automotive and construction applications. Countries such as Brazil and Mexico are focusing on developing sustainable, lightweight materials to enhance vehicle performance and reduce emissions. Brazil, with its strong automotive sector, has seen an uptick in the adoption of hybrid materials to optimize vehicle efficiency. The increased push for electric mobility in the region is expected to further propel the demand for hybrid materials in the automotive industry.
In the Middle East, while the production of hybrid metal-polymer materials is still in its nascent stage, the demand for lightweight and durable materials in niche sectors like aerospace and automotive is growing. Countries like the UAE and Saudi Arabia are exploring the potential of these materials in aerospace applications, and hybrid materials are expected to see increased use as the region diversifies its industrial base beyond oil and gas.
Hybrid Metal-Polymer Materials Market Segmentation: Application and Material Type
The Hybrid Metal-Polymer Materials Market can be segmented based on application, material type, and manufacturing process. Each segment plays a pivotal role in the growth of this dynamic market.
Application-Based Segmentation
The automotive industry is by far the largest consumer of hybrid metal-polymer materials, accounting for over 40% of global market demand. These materials are crucial in vehicle manufacturing for reducing weight and enhancing fuel efficiency, especially with the rising focus on electric vehicles (EVs). As electric vehicles become more prevalent, manufacturers are turning to hybrid materials to create lighter, stronger, and more energy-efficient components.
Aerospace follows closely behind, with hybrid materials used to create lightweight yet strong components for aircraft. The aerospace sector is increasingly adopting these materials to improve fuel efficiency and reduce weight without compromising on safety or performance.
Electronics is another rapidly growing application, as hybrid materials are used in connectors, casings, and components for devices like smartphones, wearables, and laptops. The demand for slimmer, more durable electronics continues to drive growth in this sector.
Medical devices, defense, and construction also contribute to the hybrid metal-polymer materials market, with applications ranging from prosthetics and implants to structural components in buildings and infrastructure projects.
Material Type Segmentation
The material type segment includes various metal and polymer combinations used to produce hybrid materials, with aluminum, steel, copper, and titanium being the most commonly used metals. These metals are combined with thermoplastics such as polyethylene and polypropylene, or thermosets like epoxy and polyester, to create materials that offer improved mechanical strength, flexibility, and chemical resistance.
Aluminum-based hybrid materials are widely used in automotive and aerospace applications due to their lightweight and cost-effective properties. Steel and titanium are used in high-performance applications where strength and durability are critical. Polymer-based hybrid materials, including thermoplastics and thermosets, are particularly valuable in industries such as electronics and medical devices, where flexibility and customization are key.
Hybrid Metal-Polymer Materials Price Trend: Market Dynamics and Influencing Factors
The price trend for hybrid metal-polymer materials has shown a consistent upward trajectory, primarily due to increasing raw material costs and growing demand for high-performance composites. However, advancements in manufacturing technologies, such as 3D printing and injection molding, are helping to mitigate some of the cost pressures by making production processes more efficient and cost-effective.
One of the significant factors driving the Hybrid Metal-Polymer Materials Price Trend is the rising cost of raw materials, particularly metals like aluminum, copper, and steel. These metals have seen price increases over the past few years, driven by global supply chain disruptions and higher demand from industries like construction and automotive. Additionally, the increasing demand for high-quality, durable hybrid materials that meet stringent industry standards is contributing to higher prices, especially in the automotive and aerospace sectors.
On the other hand, advances in production technologies such as additive manufacturing are expected to reduce the overall cost of producing hybrid materials. As 3D printing and injection molding techniques become more widespread, the ability to manufacture highly customized parts on-demand, without the need for large-scale traditional manufacturing processes, is reducing the production cost per unit.
Moreover, the growing emphasis on sustainability and eco-friendly materials is influencing the price trend, as companies are investing in the development of recyclable and bio-based hybrid materials. These sustainable alternatives tend to be more expensive to produce due to the higher cost of sourcing bio-based polymers and developing recycling technologies, but they align with the increasing regulatory and consumer pressure for environmentally conscious production methods.
Hybrid Metal-Polymer Materials Price Trend and Future Outlook
Looking ahead, the Hybrid Metal-Polymer Materials Price Trend is expected to stabilize as manufacturing efficiencies improve and economies of scale take effect. The integration of hybrid materials into mass production processes, particularly in industries such as automotive and electronics, will likely drive prices down over time. As new technologies in material science and production processes continue to emerge, the future of the Hybrid Metal-Polymer Materials Market is poised for continued growth and increased affordability, enabling widespread adoption across various industries.
The Hybrid Metal-Polymer Materials Market’s future is one of innovation, sustainability, and efficiency. The combination of performance, versatility, and environmental benefits makes these materials an indispensable part of modern manufacturing. As production methods evolve and global demand continues to rise, the price of hybrid metal-polymer materials will likely remain competitive, further driving their adoption across industries worldwide.
“Hybrid Metal-Polymer Materials Manufacturing Database, Hybrid Metal-Polymer Materials Manufacturing Capacity”
-
-
- Hybrid Metal-Polymer Materials top manufacturers market share for 28+ manufacturers
- Top 8 manufacturers and top 18 manufacturers of Hybrid Metal-Polymer Materials in North America, Europe, Asia Pacific
- Production plant capacity by manufacturers and Hybrid Metal-Polymer Materials production data for 28+ market players
- Hybrid Metal-Polymer Materials production dashboard, Hybrid Metal-Polymer Materials production data in excel format
-
Key Manufacturers in the Hybrid Metal-Polymer Materials Market
The Hybrid Metal-Polymer Materials Market has seen substantial growth in recent years, with a number of key players leading the charge in production and innovation. These manufacturers are not only meeting the rising demand across industries such as automotive, aerospace, electronics, and healthcare but are also driving the development of new hybrid material solutions. Some of the most prominent companies in this space include:
1. BASF SE
BASF SE, a global leader in the chemical industry, is one of the largest producers of hybrid materials. The company offers a range of hybrid metal-polymer solutions designed to meet the needs of industries such as automotive, electronics, and construction. BASF’s hybrid materials are primarily used in applications requiring high durability, lightweight properties, and resistance to extreme conditions. Their Ultramid product line, which combines polyamide with metals, is particularly notable for its use in the automotive sector, offering excellent thermal stability, impact resistance, and strength.
2. Dow Inc.
Dow Inc. is another major player in the Hybrid Metal-Polymer Materials Market, known for its development of advanced materials that combine the advantages of metals and polymers. Dow’s materials are used in a variety of applications, including automotive, electronics, and energy sectors. The company’s Dow Performance Silicones product line, which includes hybrid metal-polymer composites, is widely used in the production of electrical components, connectors, and coatings. Dow’s innovation in silicone-based hybrid materials has driven its adoption in high-performance applications, particularly where temperature resistance and flexibility are key.
3. 3M
3M, a multinational conglomerate known for its innovation in materials science, has been a leading manufacturer of hybrid metal-polymer materials for decades. Their 3M™ Scotch-Weld structural adhesives are a popular choice for automotive and aerospace manufacturers, providing the necessary strength and durability required in critical applications. 3M has also developed hybrid materials for consumer electronics, where their 3M™ VHB™ tape solutions combine polymer adhesives with metals for high-performance bonding. The company’s focus on research and development allows them to create custom hybrid materials tailored to specific industry needs.
4. Toray Industries, Inc.
Toray Industries, Inc. is one of Japan’s leading manufacturers of advanced materials, including hybrid metal-polymer composites. Their Torayca carbon fiber composites are combined with polymer resins to create lightweight and high-strength materials used extensively in the aerospace and automotive industries. Toray is a key supplier of hybrid materials for the production of components like aircraft wings, body panels, and interior parts. The company’s commitment to sustainability and innovation in material science has allowed it to maintain a strong position in the Hybrid Metal-Polymer Materials Market.
5. Saint-Gobain S.A.
Saint-Gobain, a multinational corporation specializing in materials manufacturing, produces high-performance hybrid materials used in a range of industries. Their Hexcel product line focuses on advanced composites that combine metals with polymers for automotive, aerospace, and industrial applications. Saint-Gobain’s composites are known for their superior mechanical properties, including strength, flexibility, and resistance to wear. Their hybrid solutions are increasingly being used in the production of lightweight vehicle parts, structural components, and consumer goods.
6. Huntsman Corporation
Huntsman is another leading player in the Hybrid Metal-Polymer Materials Market, with a strong focus on the automotive, aerospace, and industrial sectors. The company’s Vipel product line, which incorporates hybrid composite materials, is widely used in automotive applications for structural components, including under-the-hood parts. Huntsman’s hybrid materials are designed to offer a balance of mechanical strength, heat resistance, and chemical resistance. Their extensive portfolio of resins and adhesives also enables them to cater to a broad range of applications beyond automotive, including consumer electronics and construction.
7. SABIC
SABIC, a global leader in the production of petrochemical products and hybrid materials, offers a wide range of metal-polymer composites. The company’s Noryl product line, which integrates metal and polymer to deliver exceptional strength and resistance to environmental stress, is highly sought after in the automotive and electronics industries. SABIC’s focus on innovation has led to the development of hybrid materials used in the creation of lightweight components that reduce energy consumption and enhance product performance. The company’s hybrid materials are crucial in applications that require both strength and electrical conductivity, particularly in the automotive and electronics sectors.
8. Covestro AG
Covestro AG is a major player in the development and production of high-performance hybrid materials, particularly for the automotive, electronics, and industrial sectors. Their Desmodur polyurethanes and Baydur hybrid composites are widely used in applications where high mechanical strength and low weight are critical. Covestro’s commitment to sustainability is evident in their development of recyclable hybrid materials, which are being increasingly adopted in the automotive industry for lightweight, eco-friendly vehicle parts.
Hybrid Metal-Polymer Materials Market Share by Manufacturers
The Hybrid Metal-Polymer Materials Market is highly competitive, with the leading players holding a substantial share of the market. As of the latest data, BASF SE, Dow Inc., and 3M are among the top three manufacturers, collectively accounting for over 40% of the global market share. These companies are well-positioned due to their diverse product portfolios, strong R&D capabilities, and long-standing relationships with key industries.
Toray Industries, Inc. and Saint-Gobain S.A. are also significant players, with each holding approximately 10-12% of the market share. Toray’s strong foothold in the aerospace industry and Saint-Gobain’s leadership in the automotive sector ensure their continued dominance in the hybrid materials space.
Huntsman Corporation and SABIC round out the top manufacturers, each contributing approximately 8-10% to the overall market share. Huntsman’s diverse product offerings across several industries, including automotive and consumer electronics, alongside SABIC’s advanced composites for automotive and electronics, allow these companies to maintain their competitive edge in the rapidly evolving hybrid materials market.
Recent Developments and Industry Trends
In recent years, several key developments have shaped the Hybrid Metal-Polymer Materials Market, reflecting an ongoing trend towards sustainability, innovation, and increased adoption of hybrid materials in various industries.
- BASF SE Launches New Hybrid Materials for Automotive and Aerospace Applications (July 2024)
BASF SE has expanded its range of hybrid metal-polymer materials with the launch of a new series designed specifically for the automotive and aerospace industries. These materials, which combine lightweight polymers with metals, offer enhanced fuel efficiency and reduced emissions in electric vehicles (EVs) and aircraft. The launch is seen as a direct response to the growing demand for high-performance, sustainable materials in these sectors.
- 3M Expands Hybrid Adhesives for Electronics Manufacturing (March 2024)
3M has introduced new hybrid adhesive solutions under its 3M™ Scotch-Weld and 3M™ VHB™ product lines, designed specifically for the electronics manufacturing industry. These adhesives combine the durability of metal with the flexibility of polymers, making them ideal for use in mobile devices, wearables, and other consumer electronics. The development is expected to significantly enhance 3M’s presence in the electronics sector, as demand for lightweight and durable materials continues to rise.
- Toray Industries Partners with Major Automotive OEMs to Supply Hybrid Materials (November 2023)
Toray Industries announced a strategic partnership with leading automotive OEMs (original equipment manufacturers) to supply advanced hybrid materials for electric vehicle production. The collaboration focuses on providing lightweight and high-strength components for EVs, including carbon fiber-reinforced composites combined with polymers. This partnership is expected to strengthen Toray’s market position in the rapidly growing EV sector, where lightweight materials are critical for performance and energy efficiency.
- Dow Inc. and General Motors Expand Collaboration for Hybrid Materials in EVs (January 2024)
Dow Inc. and General Motors have expanded their long-standing partnership to include new hybrid materials in the production of electric vehicles. The collaboration focuses on materials that reduce vehicle weight and enhance structural integrity while maintaining cost-effectiveness. The new materials are expected to play a crucial role in GM’s ongoing efforts to achieve greater energy efficiency and performance in their EV lineup.
“Hybrid Metal-Polymer Materials Production Data and Hybrid Metal-Polymer Materials Production Trend, Hybrid Metal-Polymer Materials Production Database and forecast”
-
-
- Hybrid Metal-Polymer Materials production database for historical years, 10 years historical data
- Hybrid Metal-Polymer Materials production data and forecast for next 7 years
-
Market Scenario, Demand vs Supply, Average Product Price, Import vs Export, till 2035
- Global Hybrid Metal-Polymer Materials Market revenue and demand by region
- Global Hybrid Metal-Polymer Materials Market production and sales volume
- United States Hybrid Metal-Polymer Materials Market revenue size and demand by country
- Europe Hybrid Metal-Polymer Materials Market revenue size and demand by country
- Asia Pacific Hybrid Metal-Polymer Materials Market revenue size and demand by country
- Middle East & Africa Hybrid Metal-Polymer Materials Market revenue size and demand by country
- Latin America Hybrid Metal-Polymer Materials Market revenue size and demand by
- Import-export scenario – United States, Europe, APAC, Latin America, Middle East & Africa
- Average product price – United States, Europe, APAC, Latin America, Middle East & Africa
- Market player analysis, competitive scenario, market share analysis
- Business opportunity analysis
Key questions answered in the Global Hybrid Metal-Polymer Materials Market Analysis Report:
- What is the market size for Hybrid Metal-Polymer Materials in United States, Europe, APAC, Middle East & Africa, Latin America?
- What is the yearly sales volume of Hybrid Metal-Polymer Materials and how is the demand rising?
- Who are the top market players by market share, in each product segment?
- Which is the fastest growing business/ product segment?
- What should be the business strategies and Go to Market strategies?
The report covers Hybrid Metal-Polymer Materials Market revenue, Production, Sales volume, by regions, (further split into countries):
- Asia Pacific (China, Japan, South Korea, India, Indonesia, Vietnam, Rest of APAC)
- Europe (UK, Germany, France, Italy, Spain, Benelux, Poland, Rest of Europe)
- North America (United States, Canada, Mexico)
- Latin America (Brazil, Argentina, Rest of Latin America)
- Middle East & Africa
Table of Contents:
Hybrid Metal-Polymer Materials Market
- Introduction to Hybrid Metal-Polymer Materials
- Definition and Key Characteristics
- Importance of Hybrid Materials in Modern Manufacturing
- Overview of Market Trends and Growth Drivers
- Fundamentals of Metal-Polymer Hybrid Materials
- Understanding Metal-Polymer Interaction
- Types of Hybrid Materials: Composition and Properties
- Benefits of Combining Metals and Polymers
- Production Methods for Hybrid Metal-Polymer Materials
- Traditional and Advanced Manufacturing Techniques
- Coating and Bonding Methods for Metal and Polymer Layers
- Role of Additive Manufacturing in Hybrid Material Production
- Applications of Hybrid Metal-Polymer Materials
- Automotive Industry: Lightweight, Durable Solutions
- Aerospace and Defense: High-Performance Materials for Structural Components
- Consumer Electronics: Flexible, Durable Components
- Key Properties of Hybrid Metal-Polymer Materials
- Mechanical Properties: Strength, Durability, and Flexibility
- Electrical Conductivity and Insulation
- Thermal Stability and Resistance
- Metal Selection for Hybrid Materials
- Common Metals Used in Hybrid Materials (e.g., Aluminum, Stainless Steel)
- Influence of Metal Properties on Hybrid Material Performance
- Innovations in Metal Coatings and Surface Treatments
- Polymer Selection for Hybrid Materials
- Role of Polymers in Enhancing Performance
- Common Polymers Used: Thermoplastics, Thermosets, and Elastomers
- Enhancing Compatibility Between Metals and Polymers
- Processing Techniques for Metal-Polymer Composites
- Injection Molding and Extrusion for Hybrid Materials
- Powder Metallurgy and 3D Printing Techniques
- Thermal and Chemical Bonding Methods
- Advantages of Hybrid Metal-Polymer Materials
- Combining the Strength of Metals with the Flexibility of Polymers
- Cost Efficiency in Manufacturing
- Customization for Specific Industrial Applications
- Challenges in Hybrid Metal-Polymer Materials Development
- Issues of Adhesion and Bonding Strength
- Material Compatibility and Processing Challenges
- Long-Term Durability and Degradation Concerns
- Hybrid Metal-Polymer Materials in Automotive Applications
- Lightweight Components for Improved Fuel Efficiency
- Durability and Safety Enhancements in Vehicle Design
- Trends in Hybrid Materials for Electric and Autonomous Vehicles
- Aerospace Applications of Hybrid Metal-Polymer Materials
- Use in Aircraft Components for Weight Reduction and Performance
- Applications in Satellites and Space Exploration
- Regulatory and Safety Standards for Aerospace Materials
- Role of Hybrid Metal-Polymer Materials in Consumer Electronics
- Use in Flexible, Durable Smart Devices
- Advancements in Hybrid Materials for Wearables
- Benefits in Reducing Size and Weight of Devices
- Medical Applications of Hybrid Metal-Polymer Materials
- Biocompatibility and Use in Implants and Prosthetics
- Hybrid Materials for Medical Devices and Diagnostic Equipment
- Enhancing Durability and Performance in Healthcare
- Energy and Renewable Applications
- Hybrid Materials in Solar Panels and Energy Storage Systems
- Applications in Wind Energy and Batteries
- Performance Enhancements for Energy-Efficient Solutions
- Emerging Trends in Hybrid Metal-Polymer Materials
- Innovations in Nano-Composite Hybrid Materials
- The Role of Smart Polymers and Conductive Metals
- Multi-Functional Materials for Advanced Applications
- Market Segmentation by Application
- Automotive
- Aerospace and Defense
- Electronics and Wearables
- Medical Devices
- Energy and Renewable Resources
- Global Market Dynamics and Trends
- Market Overview and Forecasting
- Key Growth Drivers and Restraints in Hybrid Materials
- Regional Insights: North America, Europe, Asia-Pacific, and Rest of the World
- Environmental and Sustainability Considerations
- Reducing Carbon Footprint with Hybrid Materials
- The Role of Recycling and Reuse in Hybrid Material Industries
- Regulatory Pressures and Sustainability Initiatives
- Cost Considerations and Economic Impact
- Production Cost Comparison of Hybrid Materials vs. Traditional Materials
- Factors Influencing Cost: Raw Materials, Technology, and Scale
- Cost-Effective Solutions for High-Volume Manufacturing
- Supply Chain and Logistics for Hybrid Materials
- Raw Material Sourcing and Supply Chain Management
- Distribution Channels and Market Access
- Challenges in Global Supply Chains for Hybrid Materials
- Key Players in the Hybrid Metal-Polymer Materials Market
- Leading Manufacturers and Innovators
- Partnerships, Collaborations, and Acquisitions in the Market
- Competitive Landscape and Market Share Analysis
- Consumer Perception and Demand for Hybrid Materials
- Key Factors Driving Adoption of Hybrid Metal-Polymer Materials
- Consumer Preferences for Lightweight, Durable Materials
- Influences of Cost, Performance, and Environmental Impact
- Technological Innovations and Research in Hybrid Materials
- Recent Advances in Hybrid Metal-Polymer Material Technologies
- Research and Development Focus Areas
- Impact of Emerging Technologies on the Hybrid Materials Market
- Future Prospects of Hybrid Metal-Polymer Materials
- Predictions for Market Growth and Emerging Applications
- Long-Term Trends in Material Science and Hybrid Material Integration
- The Future of Hybrid Materials in Advanced Manufacturing
- Case Studies of Hybrid Metal-Polymer Material Implementation
- Automotive Industry: Lightweight Solutions for Performance
- Aerospace Sector: Enhancing Safety and Efficiency
- Consumer Electronics: Pioneering Designs with Hybrid Materials
- Conclusion and Strategic Recommendations
- Summary of Key Insights and Market Trends
- Strategic Guidance for Industry Stakeholders and Innovators
- Preparing for the Future of Hybrid Metal-Polymer Materials in Manufacturing
“Every Organization is different and so are their requirements”- Datavagyanik
Companies We Work With
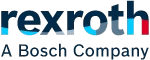
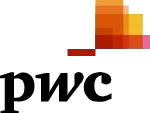
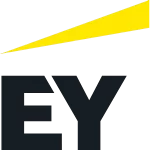
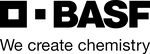
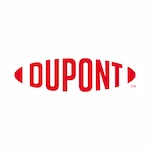

Do You Want To Boost Your Business?
drop us a line and keep in touch
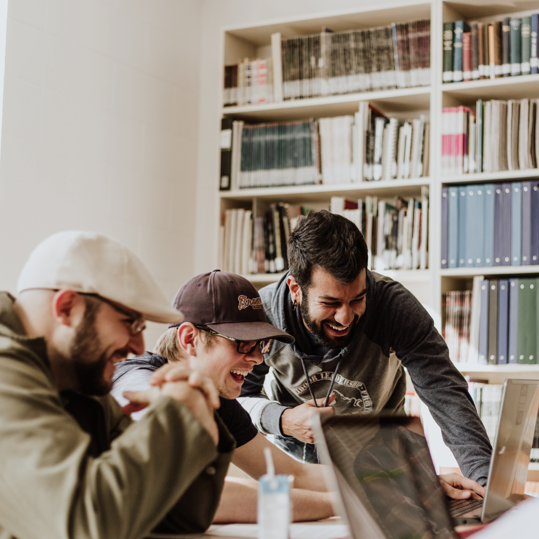