Refractory Metals in Semiconductor Etching Market Size, Production, Sales, Average Product Price, Market Share, Import vs Export
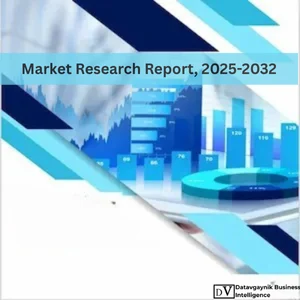
- Published 2025
- No of Pages: 120+
- 20% Customization available
Refractory Metals in Semiconductor Etching Market: An Expanding Landscape
The Refractory Metals in Semiconductor Etching Market is witnessing a profound transformation, driven by rapid technological advancements and the growing need for precision in semiconductor manufacturing. As the demand for ever-smaller and more powerful devices escalates, these refractory metals have become an essential component in semiconductor etching processes. This surge is driven by factors ranging from the miniaturization of devices to the global rise of data processing capabilities.
Miniaturization of Semiconductor Devices and Its Impact on the Refractory Metals in Semiconductor Etching Market
The trend toward miniaturization in semiconductor devices is a major factor fueling the demand for refractory metals in semiconductor etching. As semiconductor devices continue to shrink in size, the precision required in the etching process becomes increasingly critical. In fact, the global semiconductor device market is expected to reach USD 1 trillion by 2030, growing at a compound annual growth rate (CAGR) of 5.6%. Refractory metals such as tungsten, molybdenum, and tantalum play a key role in these precise etching processes, as they offer exceptional high-temperature stability and resistance to wear and corrosion.
These properties are crucial when etching smaller features on silicon wafers used in advanced semiconductor applications. As the size of transistors shrinks, the necessity for these metals to maintain precision in the etching process is more critical than ever before.
Growing Demand for Consumer Electronics and Its Influence on the Refractory Metals in Semiconductor Etching Market
Consumer electronics are one of the largest drivers of the Refractory Metals in Semiconductor Etching Market. With the increasing demand for smartphones, tablets, wearables, and other smart devices, the semiconductor industry faces heightened pressure to produce high-performance components. The global market for consumer electronics is projected to reach USD 1.4 trillion by 2027, growing at a CAGR of 6.1%.
The production of advanced semiconductors to meet these demands involves intricate etching techniques, which rely heavily on the use of refractory metals. These metals ensure that the etching processes used in devices like 3D NAND and FinFETs are precise and durable. Refractory metals provide the required durability, ensuring that semiconductor etching can handle the extreme conditions needed for the production of advanced consumer electronics.
Advancements in Data Processing and Computing Power Driving Refractory Metals in Semiconductor Etching Market
The increasing demand for data processing and computing power has further contributed to the growing need for advanced semiconductor components, which in turn drives the Refractory Metals in Semiconductor Etching Market. Technologies such as cloud computing, artificial intelligence (AI), and big data are spurring the need for more powerful, efficient, and reliable semiconductor chips.
The global data center market, which relies heavily on semiconductors, is forecast to reach USD 500 billion by 2026, expanding at a CAGR of 10%. Refractory metals are crucial in ensuring that semiconductor etching processes are capable of achieving the precision required for these highly complex computing applications. As more powerful chips are developed for AI and machine learning applications, the role of refractory metals in semiconductor etching will continue to grow.
The Rise of 5G and Telecommunications Expands Refractory Metals in Semiconductor Etching Market
The advent of 5G technology has been a significant catalyst for the growth of the semiconductor industry, and by extension, the Refractory Metals in Semiconductor Etching Market. 5G networks demand advanced semiconductor chips that offer higher speeds, lower power consumption, and increased performance. The global 5G semiconductor market is expected to reach USD 9.2 billion by 2025, growing at a CAGR of 79.7%. These chips require precise etching, and refractory metals are indispensable in achieving the accuracy needed for 5G components. As the rollout of 5G infrastructure continues, the need for semiconductor components that require refractory metals in their production processes will grow, thereby expanding the market for these materials.
Emerging Applications in the Automotive Industry Driving Refractory Metals in Semiconductor Etching Market Growth
The automotive industry, particularly with the rise of electric vehicles (EVs) and autonomous vehicles, has introduced new demands for semiconductor components. As automotive electronics evolve to meet the increasing complexity of sensors, control systems, and power management, the need for miniaturized and highly precise semiconductor devices has surged. The global automotive semiconductor market is expected to reach USD 69 billion by 2027, expanding at a CAGR of 8.6%. Refractory metals are integral to the semiconductor etching processes used to manufacture components for the automotive sector. As automotive electronics become more sophisticated, the need for high-precision etching using refractory metals will continue to drive growth in the market.
Advancements in Manufacturing Processes and Their Impact on the Refractory Metals in Semiconductor Etching Market
Manufacturing techniques in the semiconductor industry have also evolved, contributing to the growing demand for refractory metals in semiconductor etching. Technologies such as dry etching and plasma etching, which require the use of refractory metals in their equipment, are increasingly being adopted. These metals are essential for the construction of electrodes, nozzles, and other components exposed to extreme conditions such as high temperatures, pressure, and reactive gases. The global plasma etching market is expected to grow to USD 4.4 billion by 2026, growing at a CAGR of 7.5%. As semiconductor fabrication processes become more complex and advanced, the demand for refractory metals in these etching technologies will continue to rise.
Sustainability and Recycling Trends Contributing to the Growth of Refractory Metals in Semiconductor Etching Market
As environmental concerns continue to rise, there is an increasing emphasis on sustainability in the semiconductor industry. Refractory metals, due to their durability and recyclability, align with these sustainability goals. The ability to recycle and reuse refractory metals has led to a reduction in waste and a more efficient manufacturing process. The global market for recycled metals is growing rapidly, and it is estimated that the recycling rate for tungsten, a key refractory metal, could reach over 60% by 2030.
As the electronics industry embraces more sustainable practices, the recycling and reuse of refractory metals in semiconductor manufacturing will become a key strategy for meeting production needs while minimizing environmental impact. This trend will undoubtedly drive the growth of the Refractory Metals in Semiconductor Etching Market in the coming years.
The Role of Refractory Metals in Precision and Durability of Semiconductor Etching Processes
The primary reason for the increasing demand for refractory metals in semiconductor etching is their exceptional properties, which ensure the precision and durability of the etching process. Refractory metals such as tungsten, molybdenum, and tantalum have high melting points, making them ideal for use in semiconductor etching processes that involve high temperatures and reactive chemicals.
These metals also offer superior corrosion resistance, enabling them to maintain their structural integrity under harsh processing conditions. As semiconductor etching processes become more advanced, these properties are crucial in ensuring that the materials used in production can withstand the extreme conditions required for high-performance semiconductor devices. As a result, the demand for these metals will continue to increase as semiconductor etching processes become more sophisticated and precise.
“Track Country-wise Refractory Metals in Semiconductor Etching Production and Demand through our Refractory Metals in Semiconductor Etching Production Database”
-
-
- Refractory Metals in Semiconductor Etching production database for 28+ countries worldwide
- Refractory Metals in Semiconductor Etching Powder sales volume for 32+ countries
- Country-wise Refractory Metals in Semiconductor Etching production capacity and production plant mapping, production capacity utilization for 28+ manufacturers
- Refractory Metals in Semiconductor Etching production plants and production plant capacity analysis for top manufacturers
-
Geographical Demand for Refractory Metals in Semiconductor Etching Market
The demand for refractory metals in the semiconductor etching market is geographically diverse, driven by the concentration of semiconductor production and technological advancements in various regions. Each region exhibits unique trends, reflective of its industrial strengths, technological developments, and market needs. Notably, Asia-Pacific, North America, and Europe are the primary regions contributing to the market’s growth.
Asia-Pacific is the largest and fastest-growing market for refractory metals in semiconductor etching, owing to its dominance in semiconductor manufacturing. Countries like China, South Korea, Japan, and Taiwan are key players in this space. The semiconductor market in China alone is expected to reach USD 100 billion by 2026, growing at a CAGR of 5.9%. This growth is driven by China’s heavy investments in semiconductor manufacturing infrastructure and R&D to reduce its reliance on foreign technology. The robust demand for high-performance semiconductor devices in industries such as consumer electronics, automotive, and telecommunications is creating a surge in the use of refractory metals like tungsten, molybdenum, and tantalum in semiconductor etching processes.
In North America, the United States holds a dominant position in the global semiconductor market. The demand for high-performance semiconductors, particularly in industries such as cloud computing, AI, and telecommunications, continues to grow. The U.S. semiconductor market size is projected to reach USD 250 billion by 2025, with a 4.5% CAGR. This demand is further fueled by technological innovations such as the rollout of 5G infrastructure and the proliferation of smart devices. As a result, the requirement for precision etching in semiconductor manufacturing, relying on refractory metals, is expected to escalate in the coming years.
Europe’s semiconductor industry, while smaller than that of the Asia-Pacific and North American regions, has shown a consistent upward trajectory. Countries like Germany, France, and the United Kingdom are driving the market growth, especially in advanced semiconductor devices for automotive, aerospace, and telecommunications industries. The European semiconductor market is expected to grow at a CAGR of 5.2%, reaching a value of USD 100 billion by 2027. The automotive sector’s adoption of electric vehicles (EVs) and autonomous driving technology is particularly contributing to the increased demand for semiconductor devices, further driving the use of refractory metals in semiconductor etching.
Production Landscape of Refractory Metals in Semiconductor Etching Market
The production of refractory metals required for semiconductor etching is highly concentrated in specific global regions, leveraging the availability of raw materials, advanced processing technologies, and manufacturing infrastructure. The Asia-Pacific region, particularly China, South Korea, and Japan, dominates the production of refractory metals such as tungsten, molybdenum, and tantalum. China, as the world’s largest producer of tungsten, holds approximately 80% of the global market share. Tungsten is one of the primary refractory metals used in semiconductor etching due to its high melting point, resistance to wear, and thermal stability.
Japan and South Korea, both technological powerhouses, have established themselves as key producers of molybdenum and tantalum. These metals are crucial in the production of advanced semiconductors that require precision etching. In addition to the production of raw refractory metals, these countries have well-developed semiconductor manufacturing ecosystems that produce advanced etching equipment, electrodes, and sputtering targets, which are essential for semiconductor etching processes.
In North America, the U.S. plays a critical role in the production of refined and processed refractory metals. While the U.S. produces tungsten, molybdenum, and tantalum, it is also a major importer of these metals due to the high demand from its semiconductor industry. The U.S. is also heavily involved in the development of advanced etching equipment and technologies, which require high-purity refractory metals for use in various etching applications.
Europe also contributes to the production of refractory metals, particularly in high-value-added products used in aerospace, automotive, and electronics industries. However, Europe relies heavily on imports of raw materials, especially tungsten and molybdenum, from Asia-Pacific countries to meet its semiconductor etching requirements.
Refractory Metals in Semiconductor Etching Market Segmentation
The Refractory Metals in Semiconductor Etching Market can be segmented based on material type, application, and end-use industry. The material type segmentation includes metals like tungsten (W), molybdenum (Mo), tantalum (Ta), and niobium (Nb). These metals each have specific properties that make them suitable for semiconductor etching, such as high melting points, resistance to corrosion, and durability under high-temperature conditions.
Tungsten, as the most widely used refractory metal in semiconductor etching, dominates the material type segment. Tungsten’s high thermal conductivity, durability, and resistance to corrosion make it ideal for use in semiconductor fabrication processes such as ion implantation, plasma etching, and sputtering. Molybdenum, another significant refractory metal, is used in the production of interconnects, electrodes, and sputtering targets due to its superior conductivity at high temperatures.
Tantalum, while less commonly used than tungsten and molybdenum, has seen growing demand in high-performance applications such as capacitors and interconnects for advanced semiconductor devices. Niobium, a lesser-known refractory metal, is used in specialized applications, where its high melting point and corrosion resistance are required in niche semiconductor etching processes.
In terms of application, semiconductor etching equipment remains the largest segment, with refractory metals being used in various components like electrodes, nozzles, and chamber linings. As the need for miniaturization and precision etching increases, the demand for these components has escalated. Another important application is semiconductor wafer manufacturing, where refractory metals are used in the fabrication of interconnects, wires, and contact pads on wafers, ensuring high-performance etching.
The end-use industry segmentation reveals that the consumer electronics sector remains the largest driver for refractory metals in semiconductor etching, as the demand for smaller, faster, and more powerful devices continues to rise. Automotive electronics, driven by the growing adoption of electric vehicles and autonomous driving technologies, is another significant end-use sector. The telecommunications sector, particularly with the advent of 5G networks, is also contributing to the demand for semiconductor devices and, consequently, for refractory metals in etching processes.
Refractory Metals in Semiconductor Etching Price Trends
The price trend of refractory metals in the semiconductor etching market is influenced by factors such as raw material availability, production costs, and global demand. Tungsten, as the most widely used refractory metal in semiconductor etching, has experienced price fluctuations in recent years due to shifts in global supply and demand. The price of tungsten has risen by approximately 25% in the past two years, driven by increased demand from the semiconductor industry and a reduction in global production capacity.
Molybdenum and tantalum have also seen price increases, though at a slightly slower rate compared to tungsten. The price of molybdenum has increased by 15% over the past three years, while tantalum has seen a price rise of 10% during the same period. These price increases are largely attributed to higher demand for advanced semiconductor devices and the need for precision etching processes that rely on these metals.
The ongoing global semiconductor shortage, coupled with the increasing demand for high-performance chips, has created upward pressure on the prices of refractory metals used in semiconductor etching. The need for materials that can withstand extreme temperatures and reactive gases has driven semiconductor manufacturers to secure a stable supply of these metals, which, in turn, has led to higher prices.
In addition, geopolitical factors, such as trade restrictions and tariffs, have also contributed to price volatility in the refractory metals market. For example, the U.S.-China trade war and its impact on the supply of tungsten and other critical metals have created uncertainty in the market, causing price fluctuations.
Impact of Price Trends on Refractory Metals in Semiconductor Etching Market
The price trends of refractory metals have a significant impact on the semiconductor etching market. Higher prices for materials such as tungsten, molybdenum, and tantalum can increase production costs for semiconductor manufacturers. This, in turn, could potentially raise the cost of semiconductor devices, making them less affordable for end-users. However, as the demand for high-performance semiconductors continues to grow, manufacturers are willing to invest in these materials to ensure the precision and durability required for advanced etching processes.
Moreover, the price trends for refractory metals also have an impact on the development of new etching technologies. As the cost of these metals rises, semiconductor manufacturers and equipment providers are exploring alternative materials and innovative etching techniques that can reduce their reliance on high-cost refractory metals. This has led to increased investment in research and development, as companies look to optimize their use of refractory metals while maintaining high performance in their etching processes.
Conclusion: The Future of Refractory Metals in Semiconductor Etching Market
The future of the Refractory Metals in Semiconductor Etching Market looks promising, with continued demand driven by the ongoing advancements in semiconductor manufacturing. As semiconductor devices continue to shrink and evolve, the need for high-performance etching processes will increase, driving the demand for refractory metals. Geographically, Asia-Pacific, North America, and Europe are expected to remain key contributors to the growth of the market.
“Refractory Metals in Semiconductor Etching Manufacturing Database, Refractory Metals in Semiconductor Etching Manufacturing Capacity”
-
-
- Refractory Metals in Semiconductor Etching top manufacturers market share for 28+ manufacturers
- Top 8 manufacturers and top 18 manufacturers of Refractory Metals in Semiconductor Etching in North America, Europe, Asia Pacific
- Production plant capacity by manufacturers and Refractory Metals in Semiconductor Etching production data for 28+ market players
- Refractory Metals in Semiconductor Etching production dashboard, Refractory Metals in Semiconductor Etching production data in excel format
-
Top Manufacturers and Market Share in Refractory Metals in Semiconductor Etching Market
The Refractory Metals in Semiconductor Etching Market is highly competitive, with several manufacturers playing a critical role in meeting the growing demand for these materials. Key players in the market include Global Tungsten & Powders Corp., Molymet, H.C. Starck, and Plansee.
Global Tungsten & Powders Corp., a leading player in the tungsten industry, manufactures high-purity tungsten products that are widely used in semiconductor etching processes. Their product line includes tungsten powders, sputtering targets, and sintered tungsten products, all of which are crucial for semiconductor etching applications.
Molymet, a significant player in the molybdenum market, offers a range of molybdenum-based products, including molybdenum powders and molybdenum wire, which are used extensively in semiconductor etching. Their high-quality molybdenum products are integral to the semiconductor industry’s need for precision and durability in etching processes.
H.C. Starck is another key manufacturer of refractory metals, particularly tantalum and niobium. Their tantalum products are widely used in the semiconductor industry for high-performance applications like capacitors and interconnects.
Plansee, known for its advanced manufacturing capabilities in refractory metals, produces high-performance tungsten and molybdenum products for use in semiconductor etching. Their product line includes tungsten and molybdenum sputtering targets, electrodes, and other components essential for the semiconductor industry.
Recent Developments in Refractory Metals in Semiconductor Etching Market
The Refractory Metals in Semiconductor Etching Market has seen significant developments in recent years. In February 2023, Molymet announced the expansion of its molybdenum production facility in Chile, aimed at increasing the supply of high-purity molybdenum products used in semiconductor etching. This expansion is expected to address the rising demand for advanced semiconductor devices and further solidify Molymet’s position as a leading supplier of molybdenum-based products.
In March 2024, Plansee unveiled a new line of high-performance tungsten sputtering targets designed to meet the growing needs of the semiconductor etching process for advanced semiconductor nodes. This new product line is aimed at semiconductor manufacturers focused on next-generation technologies like 7nm and 5nm process nodes.
These advancements, combined with increasing global demand for semiconductor devices, are expected to drive growth in the Refractory Metals in Semiconductor Etching Market and contribute to the ongoing development of more efficient and precise etching technologies.
“Refractory Metals in Semiconductor Etching Production Data and Refractory Metals in Semiconductor Etching Production Trend, Refractory Metals in Semiconductor Etching Production Database and forecast”
-
-
- Refractory Metals in Semiconductor Etching production database for historical years, 10 years historical data
- Refractory Metals in Semiconductor Etching production data and forecast for next 7 years
-
Market Scenario, Demand vs Supply, Average Product Price, Import vs Export, till 2035
- Global Refractory Metals in Semiconductor Etching Market revenue and demand by region
- Global Refractory Metals in Semiconductor Etching Market production and sales volume
- United States Refractory Metals in Semiconductor Etching Market revenue size and demand by country
- Europe Refractory Metals in Semiconductor Etching Market revenue size and demand by country
- Asia Pacific Refractory Metals in Semiconductor Etching Market revenue size and demand by country
- Middle East & Africa Refractory Metals in Semiconductor Etching Market revenue size and demand by country
- Latin America Refractory Metals in Semiconductor Etching Market revenue size and demand by
- Import-export scenario – United States, Europe, APAC, Latin America, Middle East & Africa
- Average product price – United States, Europe, APAC, Latin America, Middle East & Africa
- Market player analysis, competitive scenario, market share analysis
- Business opportunity analysis
Key questions answered in the Global Refractory Metals in Semiconductor Etching Market Analysis Report:
- What is the market size for Refractory Metals in Semiconductor Etching in United States, Europe, APAC, Middle East & Africa, Latin America?
- What is the yearly sales volume of Refractory Metals in Semiconductor Etching and how is the demand rising?
- Who are the top market players by market share, in each product segment?
- Which is the fastest growing business/ product segment?
- What should be the business strategies and Go to Market strategies?
The report covers Refractory Metals in Semiconductor Etching Market revenue, Production, Sales volume, by regions, (further split into countries):
- Asia Pacific (China, Japan, South Korea, India, Indonesia, Vietnam, Rest of APAC)
- Europe (UK, Germany, France, Italy, Spain, Benelux, Poland, Rest of Europe)
- North America (United States, Canada, Mexico)
- Latin America (Brazil, Argentina, Rest of Latin America)
- Middle East & Africa
Table of Contents:
Refractory Metals in Semiconductor Etching Market
- Introduction to Refractory Metals in Semiconductor Etching
- Definition and Characteristics of Refractory Metals
- Importance of Semiconductor Etching in Electronics Manufacturing
- Role of Refractory Metals in Etching Processes
- Overview of Semiconductor Etching Process
- Etching Techniques and Their Importance in Semiconductor Fabrication
- Types of Etching: Wet vs. Dry Etching
- Key Materials and Equipment Used in Semiconductor Etching
- Properties of Refractory Metals
- Thermal Stability and High Melting Points
- Resistance to Chemical Reactions
- Conductivity and Durability in Harsh Environments
- Refractory Metals and Their Applications in Semiconductor Etching
- Role of Tungsten (W), Molybdenum (Mo), and Tantalum (Ta)
- Contribution to Etching Uniformity and Precision
- Use of Refractory Metals in Etching Masks and Electrodes
- Market Drivers for Refractory Metals in Semiconductor Etching
- Increasing Demand for Smaller, Faster, and More Efficient Semiconductors
- Growth of the Semiconductor Industry
- Technological Advancements in Semiconductor Fabrication
- Types of Refractory Metals Used in Etching Processes
- Tungsten (W): Applications in High-Performance Etching
- Molybdenum (Mo): Role in Etching and Sputtering
- Tantalum (Ta): Contribution to Chemical and Thermal Resistance
- Refractory Metal Coatings in Etching Applications
- Deposition Techniques for Coating Refractory Metals
- Protective Coatings for Etching Tools and Equipment
- Enhancing Etching Precision and Lifespan of Equipment
- Technological Innovations in Refractory Metals for Etching
- Development of New Alloys and Composites
- Nano-Structured Refractory Metals for Enhanced Etching Performance
- Impact of Atomic Layer Etching (ALE) and Molecular Layer Etching (MLE)
- Environmental Impact of Refractory Metals in Semiconductor Etching
- Sustainability and Recycling of Refractory Metals
- Eco-Friendly Alternatives and Processes
- Addressing Waste Management and Toxicity Issues
- Economic Impact of Refractory Metals in Etching
- Cost Analysis of Using Refractory Metals vs. Alternatives
- Price Trends for Refractory Metals in Semiconductor Applications
- Economic Benefits for Semiconductor Manufacturers
- Supply Chain for Refractory Metals in Semiconductor Etching
- Global Supply of Refractory Metals: Key Players and Regions
- Challenges in Sourcing and Distribution of Refractory Metals
- Impact of Supply Chain Disruptions on the Semiconductor Industry
- Challenges in the Use of Refractory Metals in Semiconductor Etching
- High Cost and Scarcity of Certain Refractory Metals
- Handling and Processing Difficulties
- Balancing Performance with Cost Efficiency
- Future Trends in Refractory Metals for Semiconductor Etching
- Emerging Markets and Technologies for Refractory Metals
- Increasing Miniaturization and Demand for Advanced Etching Materials
- Prospects for Refractory Metals in Quantum Computing and Advanced Electronics
- Impact of Semiconductor Industry Growth on Refractory Metals Demand
- Growing Semiconductor Production and Its Demand for Refractory Metals
- Key Regions Leading the Growth in Semiconductor Manufacturing
- How Technological Shifts Influence Metal Demand
- Refractory Metals in Advanced Lithography and Etching Systems
- Evolution of Lithography and Etching Techniques
- Use of Refractory Metals in Photomask Manufacturing
- Role in Extreme Ultraviolet (EUV) Lithography
- Refractory Metals in High-Aspect-Ratio Etching Processes
- Challenges in High-Aspect-Ratio Structures and Etching Techniques
- Role of Refractory Metals in Achieving Precision and Consistency
- Applications in DRAM and 3D NAND Flash Memory
- Refractory Metals for Deep Submicron Etching
- Importance of Deep Submicron Etching in Modern Semiconductor Devices
- Applications in MEMS (Micro-Electro-Mechanical Systems)
- Role of Refractory Metals in Ultra-Fine Patterning
- Materials Science Behind Refractory Metals in Etching
- Advanced Properties of Refractory Metals for Etching Processes
- Structural and Thermal Characteristics of Refractory Materials
- Improving the Efficiency of Refractory Metal Materials
- Role of Refractory Metals in Etching Gas Delivery Systems
- Importance of Gas Delivery in Semiconductor Etching
- How Refractory Metals Enhance Gas Delivery Efficiency
- Selection of Refractory Metals for Specialized Etching Applications
- Refractory Metal Recycling in Semiconductor Etching
- The Role of Recycling Refractory Metals from Etching Equipment
- Sustainable Practices in the Recycling of Tungsten, Molybdenum, and Tantalum
- Recycling Challenges and Opportunities for Semiconductor Manufacturers
- Competitive Landscape in Refractory Metals for Semiconductor Etching
- Leading Companies in Refractory Metal Production for Etching Applications
- Market Share, Strategic Partnerships, and Mergers
- Competitive Analysis of Key Players and Their Strategies
- Impact of Industry Regulations on Refractory Metals in Etching
- Safety and Environmental Regulations for Refractory Metal Use
- Impact of Industry Standards on Metal Selection and Etching Process
- Regulatory Compliance and Certification for Semiconductor Manufacturers
- Market Segmentation by Application: Refractory Metals in Etching
- Segmenting the Market by Semiconductor Device Type
- Usage in Logic Chips, Memory Devices, and Power Electronics
- Segment-Specific Demands for Refractory Metal Properties
- Global Trends in Semiconductor Fabrication and Their Impact on Refractory Metals
- Shifts in Global Semiconductor Fabrication Practices
- How Global Semiconductor Markets Influence Metal Requirements
- Impact of Industry 4.0 and Automation on Refractory Metal Use
- Refractory Metals in Semiconductor Etching for 5G and IoT Technologies
- Role of Refractory Metals in the Development of 5G Infrastructure
- Refractory Metals in Advanced IoT Devices and Systems
- How High-Performance Etching Supports Next-Gen Communication Technologies
- Regional Insights into Refractory Metals for Semiconductor Etching
- Market Dynamics in Key Regions: North America, Europe, Asia-Pacific
- Regional Demand for Refractory Metals in Semiconductor Manufacturing
- Country-Specific Developments and Growth Drivers
- Conclusion and Future Outlook for Refractory Metals in Semiconductor Etching
- Summary of Key Insights and Market Trends
- Future Projections for the Refractory Metals Market in Semiconductor Etching
- Strategies for Market Growth and Development in the Coming Decade
“Every Organization is different and so are their requirements”- Datavagyanik
Companies We Work With
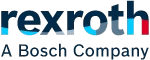
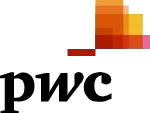
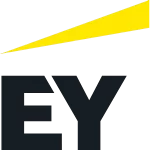
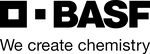
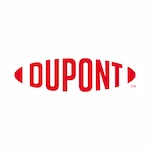

Do You Want To Boost Your Business?
drop us a line and keep in touch
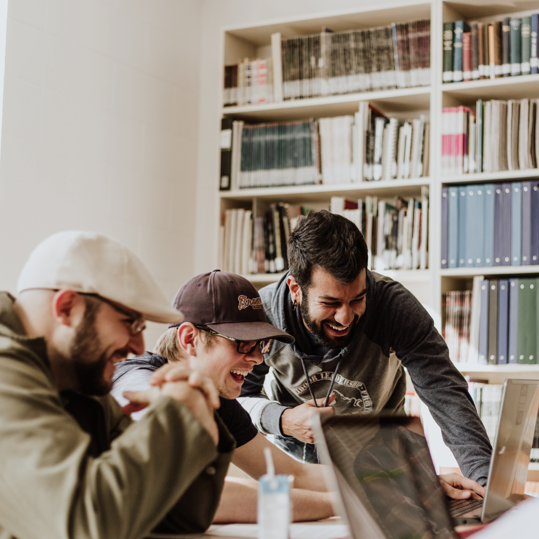