Automated coating systems Market Size, Production, Sales, Average Product Price, Market Share, Import vs Export
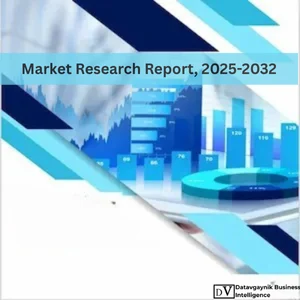
- Published 2025
- No of Pages: 120+
- 20% Customization available
Growing Precision Needs Drive Automated Coating Systems Market
The automated coating systems market is rapidly expanding due to an increasing demand for precision in coating applications. Industries such as medical devices require coatings that must be uniform, consistent, and functional to ensure safety and effectiveness. For example, implantable devices like stents and orthopedic implants depend heavily on precise coatings to maintain biocompatibility and performance. Automated coating systems eliminate the variability caused by manual processes, enabling manufacturers to meet these stringent demands. This rising need for accuracy is a core factor fueling the automated coating systems market growth.
Technological Innovations Propel Automated Coating Systems Market
Innovations in coating technologies are key drivers in the automated coating systems market. Antimicrobial coatings, hydrophilic coatings, and drug-eluting coatings are seeing rapid adoption, especially in medical device manufacturing. For example, antimicrobial coatings help reduce infection risks, which is critical in healthcare settings where infections remain a major concern. Drug-eluting coatings provide controlled release of medication, significantly improving patient outcomes in cardiovascular treatments. These advanced coatings require highly controlled application methods, making automated systems essential and accelerating the automated coating systems market expansion.
Rising Medical Device Production Boosts Automated Coating Systems Market Size
The surge in medical device manufacturing globally has directly increased the automated coating systems market size. With the world’s aging population and increasing chronic diseases, the demand for devices like catheters, implants, and surgical instruments has grown substantially. For example, the implant market has been growing at double-digit rates annually, which directly correlates to increased demand for precise coating processes. Automated coating systems enable manufacturers to scale production efficiently while maintaining high quality, driving market size upward.
Efficiency and Cost Savings Expand Automated Coating Systems Market
The automated coating systems market benefits from the operational efficiencies brought by automation. Automated systems reduce labor costs, material waste, and production time. For instance, switching from manual to automated coating can reduce material waste by up to 30%. This cost-effectiveness allows manufacturers to improve margins while meeting growing production needs. Higher throughput and less downtime also contribute to faster time-to-market, making automated coating systems highly attractive investments, thus expanding the market further.
Regulatory Compliance Strengthens Automated Coating Systems Market Demand
Regulatory pressures in sectors like medical devices are increasing demand for automated coating systems. Compliance with standards requires consistent process control, documentation, and traceability — areas where automated systems excel. For example, FDA and ISO regulations mandate strict control of coating parameters to ensure product safety. Automated systems help manufacturers meet these requirements reliably, pushing adoption across the industry. As regulations tighten globally, the automated coating systems market is expected to continue its strong growth trajectory.
Customization Needs Foster Automated Coating Systems Market Growth
The rise of personalized medicine and customized medical devices has created new growth avenues for the automated coating systems market. Customized devices often require unique coatings tailored to individual patient needs. Automated systems offer flexibility to switch between coating formulations quickly and accurately, supporting diverse production runs. For example, minimally invasive devices require specific coatings that can be precisely applied through automation. This adaptability is a significant factor driving the market’s ongoing expansion.
Infection Control Focus Elevates Automated Coating Systems Market
Post-pandemic healthcare priorities have intensified the focus on infection control, benefiting the automated coating systems market. Uniform application of antimicrobial coatings reduces infection risks associated with medical devices. Automated systems ensure that coatings meet exact standards for thickness and coverage, improving device safety. This growing emphasis on infection prevention is prompting manufacturers to adopt automated coating technologies more aggressively, contributing to the market’s rapid growth.
Asia Pacific Emerges as a Key Market for Automated Coating Systems
The Asia Pacific region is emerging as a dominant player in the automated coating systems market, driven by expanding medical device manufacturing and government healthcare initiatives. Countries like China, India, and Japan are rapidly adopting automation to improve production quality and efficiency. For example, China’s robust manufacturing infrastructure and export growth have increased demand for automated coating solutions. The region’s evolving regulatory environment and rising investments in healthcare infrastructure continue to fuel automated coating systems market growth.
AI and Robotics Integration Enhances Automated Coating Systems Market
The integration of artificial intelligence and robotics is revolutionizing the automated coating systems market. AI-driven systems provide real-time monitoring and adaptive control to optimize coating processes, reducing defects and improving consistency. Robotics enable precision application, especially for complex medical devices. For example, AI-powered quality control can detect coating flaws instantly, minimizing waste. These technological advances are driving innovation and expanding the market by enabling manufacturers to meet increasingly demanding quality standards.
Sustainability Trends Influence Automated Coating Systems Market Evolution
Sustainability concerns are increasingly shaping the automated coating systems market. Manufacturers are adopting eco-friendly coating materials and processes that reduce waste and emissions. Automated systems contribute by precisely controlling material usage and enabling solvent-free or water-based coatings. For example, the shift to water-based coatings in medical device manufacturing is gaining traction due to environmental benefits and regulatory pressure. As sustainability becomes a priority, investments in green automated coating technologies will further propel market growth.
“Track Country-wise Automated coating systems Production and Demand through our Automated coating systems Production Database”
-
-
- Automated coating systems production database for 30+ countries worldwide
- Automated coating systems Powder sales volume for 31+ countries
- Country-wise Automated coating systems production capacity and production plant mapping, production capacity utilization for 30+ manufacturers
- Automated coating systems production plants and production plant capacity analysis for top manufacturers
-
Geographic Demand Patterns Shaping the Automated Coating Systems Market
The automated coating systems market displays marked regional differences driven by varying industrial growth rates, technological maturity, and regulatory environments. Asia Pacific leads demand growth, capturing nearly half of the global market share. Countries such as China, India, and Japan have rapidly expanded their manufacturing base, particularly in sectors like automotive, electronics, and medical devices, which are key consumers of automated coating technologies. For example, China’s manufacturing output has been growing at over 6% annually, fueling increased investments in automation and coating solutions.
North America commands a significant portion of the market, primarily driven by the United States. High standards for product quality and safety in aerospace, automotive, and medical industries prompt companies to adopt automated coating systems to meet stringent regulations and improve efficiency. The region’s robust R&D infrastructure fosters continuous innovation, further increasing demand.
Europe also maintains strong demand, with countries like Germany, France, and Italy leading due to their advanced manufacturing sectors and commitment to Industry 4.0 integration. The focus on sustainable manufacturing and energy-efficient processes is encouraging manufacturers to invest in automated coating systems that reduce waste and improve precision.
Production Capacities and Trends in the Automated Coating Systems Market
Production of automated coating systems is concentrated in regions with mature manufacturing capabilities. The United States and Germany are key producers, leveraging advanced engineering and automation expertise. These countries focus on high-precision coating technologies such as physical vapor deposition and plasma spray coatings, catering to aerospace, automotive, and medical device manufacturers worldwide.
In Asia Pacific, China and Japan have rapidly scaled production facilities, capitalizing on lower production costs and increasing domestic demand. Chinese manufacturers have expanded their capacity to supply both local and export markets, often at competitive price points, driving market expansion. India is also emerging as a growing production hub, supported by government initiatives promoting local manufacturing and technology adoption.
Market Segmentation Driving Diverse Automated Coating Systems Applications
The automated coating systems market segments primarily by coating type, application, and technology, each segment exhibiting unique growth trajectories.
By coating type, antimicrobial and drug-eluting coatings are witnessing rapid adoption in the medical device sector due to increasing infection control needs and enhanced therapeutic outcomes. Hydrophilic coatings are growing quickly in catheter and guidewire manufacturing, driven by the rise in minimally invasive procedures.
Application-wise, medical devices remain the largest segment, propelled by aging populations and increasing surgical procedures worldwide. Automotive components represent another significant segment, as manufacturers seek coatings that improve corrosion resistance and aesthetic appeal while meeting environmental regulations.
Technological segmentation shows physical vapor deposition and chemical vapor deposition leading the market due to their ability to apply durable, high-performance coatings with precision. Electrostatic spray and dip coating techniques continue to grow in applications where cost-efficiency and large-scale production are priorities.
Price Trends Influencing the Automated Coating Systems Market
Automated coating systems price trends reflect the balance between technological complexity, production scale, and material costs. Prices for advanced systems incorporating robotics and AI-driven quality control tend to be higher initially but offer significant long-term savings through efficiency gains and reduced waste.
For instance, the price of automated coating systems with integrated real-time monitoring has increased by around 5-7% annually due to rising demand for high precision and regulatory compliance. However, the cost reduction in coatings material waste and labor typically offsets these upfront expenses within months of deployment.
In emerging markets, competitive pricing strategies by local manufacturers have made automated coating systems more accessible, driving adoption even among small and medium enterprises. This trend is contributing to price normalization globally and expanding market penetration.
Impact of Raw Material Costs on Automated Coating Systems Price Trend
Raw material availability and prices, such as those for specialty coating powders and gases, directly influence the automated coating systems price trend. Fluctuations in metal and chemical prices can lead to adjustments in system pricing, particularly for coatings that rely on rare or high-purity materials.
For example, recent increases in rare earth metal prices have caused slight upticks in coating system costs designed for high-performance aerospace and electronics applications. Manufacturers are responding by investing in more efficient coating techniques that minimize raw material usage, thereby stabilizing pricing pressures.
Future Outlook for Price Trends in the Automated Coating Systems Market
Looking ahead, the automated coating systems price trend is expected to moderate as technological innovations improve system efficiency and manufacturing scale increases. The adoption of Industry 4.0 and smart manufacturing will enable better process control, reducing operational costs.
Moreover, increasing competition from emerging market producers is likely to drive down prices for standard automated coating systems, while premium systems incorporating AI and robotics may command higher prices due to enhanced capabilities.
Regional Production Capacities Driving Market Expansion
Production hubs in North America, Europe, and Asia Pacific will continue to expand capacity to meet growing demand for automated coating systems. For example, Germany’s investment in Industry 4.0 technologies supports highly automated factories producing next-generation coating equipment. Similarly, China’s rapid expansion in manufacturing infrastructure enables large-scale production at competitive prices, strengthening its position as a global supplier.
Emerging regions such as Southeast Asia and Latin America are developing localized production to reduce reliance on imports, further stimulating regional market growth and providing new opportunities for manufacturers.
Market Segmentation by End-Use Industries in Automated Coating Systems Market
Within the automated coating systems market, end-use industries such as medical devices, automotive, aerospace, electronics, and consumer goods show distinct demand patterns.
Medical devices remain the largest segment, propelled by growth in implantable devices and minimally invasive surgical tools. For instance, orthopedic implants coated with antimicrobial and drug-eluting layers are increasingly produced using automated systems to ensure consistent quality.
The automotive industry demands coatings that provide durability and corrosion resistance, especially for electric vehicles where thermal management coatings are becoming important. Aerospace applications prioritize lightweight, high-performance coatings applied through automated physical vapor deposition and plasma spray methods.
Electronics coatings focus on thin, protective layers that enhance device longevity and performance. Consumer goods manufacturers utilize automated coating systems to achieve uniform finishes and improve product aesthetics at scale.
Pricing Strategies in the Automated Coating Systems Market
Pricing in the automated coating systems market reflects a mix of technology level, customization, and service offerings. High-end systems incorporating AI, robotics, and integrated data analytics command premium pricing due to their enhanced precision and reduced operational risks.
Mid-range systems balance cost and capability, targeting small to medium enterprises seeking to improve quality without excessive investment. Entry-level automated coating solutions focus on basic automation to replace manual methods, often priced competitively to encourage adoption.
The evolving price trend is characterized by gradual decreases in baseline system prices due to increased manufacturing efficiency, alongside rising prices for advanced, feature-rich systems.
Conclusion: Geographic and Market Forces Driving Automated Coating Systems Market
The automated coating systems market is shaped by strong geographic demand disparities, production concentration in mature regions, and diverse segmentation by application and technology. Price trends reflect a dynamic interplay of innovation, raw material costs, and competitive pressures.
Asia Pacific’s rapid industrialization, North America’s technological leadership, and Europe’s sustainability focus collectively drive market expansion. Production capacities grow in tandem, supported by government initiatives and private investments.
Market segmentation by coating type and end-use industry highlights targeted growth opportunities, while pricing strategies adapt to evolving technology and market needs. The automated coating systems market is poised for sustained growth, powered by these geographic and market forces.
“Automated coating systems Manufacturing Database, Automated coating systems Manufacturing Capacity”
-
-
- Automated coating systems top manufacturers market share for 30+ manufacturers
- Top 9 manufacturers and top 19 manufacturers of Automated coating systems in North America, Europe, Asia Pacific
- Production plant capacity by manufacturers and Automated coating systems production data for 30+ market players
- Automated coating systems production dashboard, Automated coating systems production data in excel format
-
Top Manufacturers in the Automated Coating Systems Market
The automated coating systems market is dominated by several key manufacturers who lead the industry through innovation, global reach, and extensive product portfolios. Among these, Nordson Corporation, Gema Switzerland GmbH, Sprimag, Arnold Machine, Dubois Equipment Company, EMS Powder Coating, and Anda Technologies are recognized as top players.
Nordson Corporation holds a substantial share of the automated coating systems market due to its comprehensive range of coating equipment, including precision liquid spray systems and powder coating lines. Their product lines, such as the Encore series for powder coatings and Prodigy series for liquid coatings, have established a strong reputation for quality and reliability. Nordson’s focus on technological advancement and global service network enables it to cater to diverse industries like automotive, medical devices, and electronics, maintaining its leading position.
Gema Switzerland GmbH is another major player renowned for electrostatic powder coating equipment. Their OptiFlex Pro series is widely used for delivering consistent, uniform coatings with high transfer efficiency, crucial for industries where finish quality is non-negotiable. Gema’s technological innovation and commitment to energy-efficient coating solutions contribute to its strong market presence and growing share.
Sprimag specializes in spray coating machinery for surface and internal coatings, particularly in metal packaging. Their SprayMaster and CanMaster product lines have been adopted across multiple sectors due to their flexibility and precision. Sprimag’s strength lies in tailored solutions that meet unique application needs, which helps them capture significant niche market share.
Arnold Machine focuses on customized robotic spray systems designed for precise application of adhesives and coatings. The IntelliSpray series is recognized for its ability to enhance process safety and control, making it a preferred choice in highly regulated industries like pharmaceuticals and medical devices. Arnold Machine’s expertise in robotic integration ensures it holds a vital share in segments demanding high precision.
Dubois Equipment Company offers automated finishing systems widely used in wood, metal, and specialty coatings. Their SprayMaster and SprayTech lines are designed to improve efficiency and profitability for manufacturers. Dubois’s specialization in finishing processes supports its strong presence in markets focused on decorative and protective coatings.
EMS Powder Coating delivers complete powder coating systems including ovens and spray machines. Their turnkey solutions cater to varied industry needs, making EMS a significant player in the automated coating systems market. The company’s ability to provide integrated production lines boosts its market share in manufacturing sectors requiring high throughput and quality control.
Anda Technologies is notable for high-speed selective conformal coating machines, critical in electronics manufacturing. Their PrecisionCoat series supports automation in applying protective coatings to printed circuit boards with exceptional accuracy, securing a strong hold in the electronics segment of the automated coating systems market.
Market Share Distribution in the Automated Coating Systems Market
Market share in the automated coating systems market is concentrated among these key players but also shows diversity due to specialized product offerings. Nordson Corporation and Gema Switzerland GmbH collectively hold the largest global market shares, supported by their broad product ranges and extensive geographic reach. Together, they account for approximately 40-45% of the market by revenue.
Sprimag and Arnold Machine maintain significant shares within their specialized niches—spray coating for metal packaging and robotic spray applications respectively—each capturing around 8-12% of the global market. Their focused approach allows them to dominate specific segments while benefiting from industry growth.
Dubois Equipment and EMS Powder Coating control approximately 10-15% of the market, largely through turnkey solutions and finishing system expertise, which appeal to manufacturers seeking integrated production capabilities.
Anda Technologies, while smaller in overall revenue share compared to others, holds a commanding position in the conformal coating niche, accounting for nearly 5-7% of the market. Their high-precision machines are critical for the electronics sector, which is experiencing rapid automation growth.
Smaller regional players and emerging companies collectively account for the remaining market share but are increasingly gaining traction by offering cost-effective and specialized automated coating solutions tailored to local industries.
Product Lines Defining the Market Leaders
Each leading manufacturer differentiates itself through specific product lines designed to meet varying industry demands:
Nordson’s Encore series powder coating systems and Prodigy liquid spray systems emphasize accuracy, reduced waste, and high throughput. These systems integrate smart process controls and are widely used in automotive and medical device coating applications where regulatory compliance and quality consistency are essential.
Gema’s OptiFlex Pro electrostatic powder coating systems focus on energy efficiency and coating uniformity. These systems are popular in high-volume production environments such as appliances and automotive parts manufacturing.
Sprimag’s SprayMaster and CanMaster product lines serve surface and internal coating needs with adjustable configurations, targeting metal packaging and food & beverage sectors requiring high durability and corrosion resistance.
Arnold Machine’s IntelliSpray robotic coating systems are tailored for industries demanding exact adhesive and coating application, including medical device assembly and pharmaceutical packaging, where contamination prevention and precision are critical.
Dubois Equipment’s SprayMaster and SprayTech product lines provide versatile finishing solutions that improve cycle times and reduce material consumption. Their systems are favored in wood finishing and specialty coatings markets.
EMS Powder Coating offers integrated coating lines combining spray booths, curing ovens, and material handling systems. Their modular approach suits manufacturers seeking scalable production capabilities.
Anda Technologies’ PrecisionCoat series is designed for selective conformal coating in electronics manufacturing, offering fast cycle times and consistent coverage critical to PCB reliability.
Recent Industry Developments and Market Player Activities
The automated coating systems market has seen significant activity in recent months:
- In early 2024, several manufacturers announced expansions of their product portfolios to include AI-enabled process monitoring and adaptive coating controls, enhancing precision and reducing defects.
- Collaborations between robotics integrators and coating system manufacturers have accelerated the deployment of fully automated lines in medical device and electronics production, responding to rising demand for contamination control and process consistency.
- There has been an increased focus on sustainability, with manufacturers developing eco-friendly coating materials compatible with automated systems to meet tightening environmental regulations worldwide.
- Companies like Nordson and Gema have expanded their service networks globally, improving aftermarket support and training programs to strengthen customer retention and market presence.
- Emerging market investments, especially in Asia Pacific and Latin America, have led to the establishment of new manufacturing and assembly facilities by major players to reduce lead times and logistics costs.
- In late 2023, several pilot projects demonstrated the effectiveness of combining AI with automated coating systems for predictive maintenance and real-time quality assurance, signaling a trend likely to shape the market’s future.
“Automated coating systems Production Data and Automated coating systems Production Trend, Automated coating systems Production Database and forecast”
-
-
- Automated coating systems production database for historical years, 10 years historical data
- Automated coating systems production data and forecast for next 9 years
-
Market Scenario, Demand vs Supply, Average Product Price, Import vs Export, till 2035
- Global Automated coating systems Market revenue and demand by region
- Global Automated coating systems Market production and sales volume
- United States Automated coating systems Market revenue size and demand by country
- Europe Automated coating systems Market revenue size and demand by country
- Asia Pacific Automated coating systems Market revenue size and demand by country
- Middle East & Africa Automated coating systems Market revenue size and demand by country
- Latin America Automated coating systems Market revenue size and demand by
- Import-export scenario – United States, Europe, APAC, Latin America, Middle East & Africa
- Average product price – United States, Europe, APAC, Latin America, Middle East & Africa
- Market player analysis, competitive scenario, market share analysis
- Business opportunity analysis
Key questions answered in the Global Automated coating systems Market Analysis Report:
- What is the market size for Automated coating systems in United States, Europe, APAC, Middle East & Africa, Latin America?
- What is the yearly sales volume of Automated coating systems and how is the demand rising?
- Who are the top market players by market share, in each product segment?
- Which is the fastest growing business/ product segment?
- What should be the business strategies and Go to Market strategies?
The report covers Automated coating systems Market revenue, Production, Sales volume, by regions, (further split into countries):
- Asia Pacific (China, Japan, South Korea, India, Indonesia, Vietnam, Rest of APAC)
- Europe (UK, Germany, France, Italy, Spain, Benelux, Poland, Rest of Europe)
- North America (United States, Canada, Mexico)
- Latin America (Brazil, Argentina, Rest of Latin America)
- Middle East & Africa
Table of Contents:
Automated Coating Systems Market report:
- Executive Summary
- Overview of Automated Coating Systems
- Evolution and Technological Advancements in Coating Automation
- Types of Automated Coating Systems
- 4.1 Spray Coating Systems
- 4.2 Powder Coating Systems
- 4.3 Dip Coating Systems
- 4.4 Electrostatic Coating Systems
- Key Components and Functional Architecture of Automated Coating Systems
- Global Market Landscape and Industry Outlook
- Key Factors Driving Market Growth
- Market Restraints and Challenges Affecting Adoption
- Opportunities in Emerging Economies and Niche Applications
- Market Segmentation Analysis
- 10.1 By Technology
- 10.2 By Application Industry
- 10.3 By Coating Type
- 10.4 By Automation Level
- Regional Market Analysis
- 11.1 North America: Market Trends and Forecast
- 11.2 Europe: Market Dynamics and Growth Potential
- 11.3 Asia Pacific: Market Development and Investment Opportunities
- 11.4 Latin America: Emerging Market Insights
- 11.5 Middle East & Africa: Growth Drivers and Challenges
- Global Market Size and Forecast (2020–2035)
- Competitive Landscape and Market Positioning of Key Players
- Innovations and R&D Activities in Automated Coating Technologies
- Impact of Industry 4.0 and Smart Manufacturing on Coating Systems
- Environmental Regulations and Their Influence on Market Dynamics
- Energy Efficiency Trends in Automated Coating Systems
- Demand Analysis by End-User Industries
- 18.1 Automotive
- 18.2 Aerospace
- 18.3 Electronics
- 18.4 Healthcare
- 18.5 Industrial Equipment
- Supply Chain Analysis and Logistics Optimization
- Raw Material Trends and Supply Constraints
- Pricing Analysis and Cost Drivers in the Automated Coating Industry
- Vendor Landscape and Strategic Initiatives
- Technological Disruptions Shaping the Future of Coating Automation
- Mergers, Acquisitions, and Partnerships Impacting Market Dynamics
- Risk Assessment and Mitigation Strategies for Market Participants
- Consumer Preferences and Changing Demand Patterns
- Investment Opportunities and Strategic Recommendations
- Case Studies of Successful Automated Coating System Implementations
- Future Outlook and Market Projections (2020–2035)
- Key Takeaways and Strategic Insights for Stakeholders
Other recently published reports:
“Every Organization is different and so are their requirements”- Datavagyanik
Companies We Work With
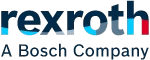
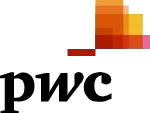
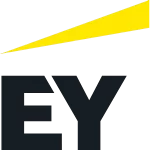
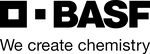
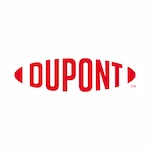

Do You Want To Boost Your Business?
drop us a line and keep in touch
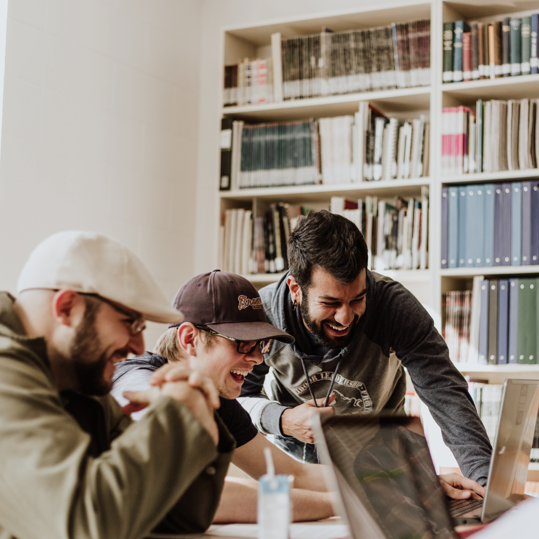