Automated coating systems for mdeical devices Market Size, Production, Sales, Average Product Price, Market Share, Import vs Export
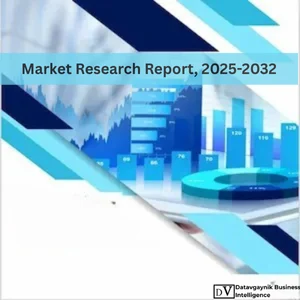
- Published 2025
- No of Pages: 120+
- 20% Customization available
Precision and Compliance Driving the Automated Coating Systems for Medical Devices Market
The automated coating systems for medical devices market is rapidly evolving as manufacturers prioritize consistency, cleanliness, and regulatory compliance. Medical devices such as catheters, guidewires, stents, and orthopedic implants require precise coatings that improve performance, reduce infection risks, and enhance biocompatibility. Automated systems eliminate variability, deliver uniform layer thickness, and ensure sterile processing, all of which are vital in meeting global regulatory standards. The shift from manual to automated coating is no longer optional—it’s a necessity to remain competitive and compliant in today’s healthcare manufacturing environment.
Rising Demand for Coated Medical Devices Accelerating Market Growth
A key driver behind the surge in the automated coating systems for medical devices market is the growing demand for coated medical devices themselves. For instance, hydrophilic coatings, which reduce friction during device insertion, are becoming standard in urology, cardiology, and vascular procedures. Similarly, antimicrobial and drug-eluting coatings are essential in preventing infections and delivering localized therapy. As the number of minimally invasive procedures continues to rise globally—growing at double-digit rates annually in some regions—the volume of coated devices being manufactured is increasing in parallel. This directly drives the demand for automated coating systems capable of high-volume, precision-driven production.
Automated Coating Systems for Medical Devices Market Size Reflects Expanding Adoption
The automated coating systems for medical devices market size is reflecting the acceleration of adoption among OEMs and contract manufacturers. The market is expected to grow steadily over the next decade, driven by a combination of factors including aging populations, increased healthcare spending, and the proliferation of chronic diseases requiring implantable and disposable medical devices. Automated systems not only reduce per-unit coating cost through efficiency and material optimization, but they also support scale-up for mass production—especially important as demand grows in emerging markets and regulatory scrutiny intensifies worldwide.
Innovation in Coating Technologies Reinforces Market Momentum
Emerging technologies are redefining the boundaries of what coatings can do for medical devices. For example, nanocoatings are enabling targeted drug delivery and enhanced adhesion, while plasma-based surface treatments improve bonding without altering device geometry. These cutting-edge solutions require highly controlled application environments—something only automated systems can reliably provide. With manufacturers exploring next-generation coating materials and complex multi-layered coatings, the market is seeing a sharp pivot toward advanced automated platforms capable of supporting these intricate processes.
Regulatory Pressures Mandate Automation and Traceability
Manufacturers in the medical device space are under increasing pressure to comply with stringent international standards, such as ISO 13485 and FDA’s Quality System Regulation. Automation in coating processes ensures repeatability, minimizes contamination risk, and facilitates digital traceability—critical for audits and quality control. Manual coating methods are not only slower but also introduce variability, which is unacceptable when patient safety is on the line. Automated coating systems offer closed-loop process control, reducing rework rates and ensuring that every device meets strict performance criteria before it leaves the production floor.
Material Waste Reduction and Cost Efficiency Attracting Investment
Another compelling factor driving the automated coating systems for medical devices market is cost efficiency. Automated systems drastically reduce coating material waste through precision spray or dip control, real-time feedback mechanisms, and minimal overspray. In high-value coatings such as drug-eluting compounds or silver-ion antimicrobial solutions, even slight reductions in waste translate to significant cost savings. Manufacturers are increasingly opting for automated solutions not only to improve performance but also to boost margins in a competitive landscape where speed, quality, and cost are all under pressure.
Smart Manufacturing and Industry 4.0 Integration Boosting Market Adoption
The integration of automated coating systems with smart factory technologies is further advancing market growth. These systems are now equipped with sensors, IoT connectivity, and data analytics platforms that provide real-time visibility into production metrics. Manufacturers can monitor coating uniformity, machine performance, and material usage remotely, improving responsiveness and operational uptime. Predictive maintenance capabilities also ensure that equipment is serviced before failure, minimizing unplanned downtime. Such capabilities align with broader trends in Industry 4.0, where automation and data converge to create highly agile and scalable production environments.
Application Expansion into New Medical Segments
As the functionality and performance of medical devices continue to evolve, so do their coating requirements. Devices used in neurological procedures, wearable sensors, implantable drug delivery systems, and robotic surgical instruments all require advanced coatings that enhance biocompatibility, conductivity, or antimicrobial resistance. These expanding applications are significantly broadening the scope of the automated coating systems for medical devices market. Manufacturers must invest in highly flexible coating systems that can handle small-batch, high-mix production without compromising quality—capabilities that automated systems increasingly offer through modular designs and intelligent controls.
Global Healthcare Trends Fueling Long-Term Market Demand
The broader growth in global healthcare infrastructure and medical technology investment directly benefits the automated coating systems for medical devices market. With the global elderly population expected to double over the next three decades, the incidence of cardiovascular disease, diabetes, and orthopedic conditions is set to rise sharply. Each of these conditions often requires long-term use of coated medical devices—from drug-eluting stents to joint implants. Additionally, healthcare access is expanding in emerging economies, where governments are investing in localized manufacturing capacity. Automated systems allow producers in these regions to scale production quickly and meet global quality standards.
Future-Ready Systems Support Customization and Rapid Development
Customization is becoming a key differentiator in the medical device industry, especially for devices tailored to patient-specific needs or niche therapeutic areas. Automated coating systems now offer flexible changeover capabilities, recipe-based programming, and customizable nozzle or immersion modules that support rapid development cycles. Manufacturers are increasingly leveraging this flexibility to prototype, test, and commercialize new products faster. As the demand for speed-to-market intensifies, especially in post-pandemic global health systems, automated coating solutions that support agile manufacturing will continue to gain market share.
“Track Country-wise Automated coating systems for mdeical devices Production and Demand through our Automated coating systems for mdeical devices Production Database”
-
-
- Automated coating systems for mdeical devices production database for 30+ countries worldwide
- Automated coating systems for mdeical devices Powder sales volume for 31+ countries
- Country-wise Automated coating systems for mdeical devices production capacity and production plant mapping, production capacity utilization for 30+ manufacturers
- Automated coating systems for mdeical devices production plants and production plant capacity analysis for top manufacturers
-
North America: Dominant Force in the Automated Coating Systems for Medical Devices Market
The automated coating systems for medical devices market in North America continues to assert global leadership, driven by the region’s advanced healthcare infrastructure and early adoption of medical manufacturing technologies. The United States, in particular, houses a high concentration of OEMs and contract manufacturers specializing in Class II and III medical devices. This cluster effect has spurred investment in sophisticated automated coating systems that offer high-throughput capabilities and stringent process control.
For example, the rising prevalence of cardiovascular diseases in the U.S. has led to a spike in demand for drug-eluting stents and coated catheters—devices that require precision coating for efficacy and safety. Additionally, as U.S. medical device exports increase year over year, the need for scalable, regulatory-compliant production has further fueled adoption of automated systems across states like California, Minnesota, and Massachusetts.
Europe’s Regulatory Stringency Fuels Market Adoption
Europe represents a mature yet rapidly evolving segment of the automated coating systems for medical devices market. The continent’s stringent regulatory landscape, exemplified by the Medical Device Regulation (MDR), has compelled manufacturers to adopt automated processes that offer traceability, repeatability, and minimal human error.
Countries like Germany and Ireland are notable for their highly specialized medtech hubs. For instance, Germany’s emphasis on precision engineering has led to increased demand for coating systems capable of handling nanometer-scale uniformity for implantable devices. Ireland, a significant exporter of coated cardiovascular and orthopedic devices, has seen a surge in investments into robotic and AI-driven coating technologies. These automated systems allow local manufacturers to meet European safety benchmarks while competing on the global stage.
Asia Pacific: Epicenter of Production and Emerging Demand
Asia Pacific has emerged as both a manufacturing powerhouse and an expanding consumer base in the automated coating systems for medical devices market. China leads regional production due to its strong supply chain, government-backed manufacturing zones, and growing domestic demand for coated devices. In India, policy initiatives like “Make in India” have sparked industrial expansion in medical technology, prompting domestic manufacturers to adopt automation in coating to remain globally competitive.
Japan and South Korea are recognized for their innovation-led approach. In these markets, automated coating systems are utilized for high-precision applications, such as microelectronic medical sensors and coated endoscopy tools. Southeast Asian countries like Malaysia and Vietnam, meanwhile, are gaining traction as secondary manufacturing hubs due to low production costs and increasing exports to Western countries.
Latin America and the Middle East: Gradual Uptake Driven by Imports
While not as dominant in production, regions such as Latin America and the Middle East are witnessing gradual growth in demand for coated medical devices, particularly in urban healthcare centers. Brazil and Mexico, for instance, have begun importing automated coating systems to support local assembly and partial manufacturing of surgical instruments and disposable devices. The Middle East, driven by hospital expansions in the Gulf Cooperation Council (GCC) countries, is importing pre-coated medical products and exploring regional assembly using semi-automated systems.
Global Production Trends Reshaping the Automated Coating Systems for Medical Devices Market
Production in the automated coating systems for medical devices market is increasingly becoming localized, with manufacturers setting up regional facilities to shorten lead times and minimize supply chain disruptions. For instance, global firms are establishing coating operations in Poland and Czechia to serve the European market, while in Asia, dual-facility strategies across China and India are being adopted to hedge geopolitical risks.
Automated systems are being integrated with cleanroom manufacturing lines to meet the stringent sterility requirements of coatings such as hydrophobic and antimicrobial layers. New-generation systems now offer in-line curing and quality assurance protocols that drastically reduce post-processing time, enabling higher batch throughput. These innovations are reshaping production economics and accelerating time-to-market for coated medical devices.
Market Segmentation: Diverse Needs Across Device Categories
The automated coating systems for medical devices market is segmented based on coating type, application method, automation level, and end-use category. Each segment presents unique technical challenges and opportunities:
- Coating Type: Hydrophilic and antimicrobial coatings dominate current demand. Hydrophilic coatings are favored in urology and vascular applications due to their ability to reduce friction. Antimicrobial coatings, on the other hand, are vital for implants and surgical tools, reducing the risk of hospital-acquired infections.
- Application Method: Spray coating systems are most widely used due to their adaptability and speed, especially for high-volume disposable devices. Dip coating systems, while slower, are ideal for complex geometries such as implantable pacemaker leads and orthopedic pins.
- Automation Level: Fully automated coating systems are rapidly gaining preference in high-volume production environments. These systems offer integrated robotics, AI-driven process controls, and real-time defect detection. Semi-automated systems still find favor in niche manufacturing, especially in small-batch production or R&D settings.
- End-Use Category: Cardiovascular, orthopedic, and diagnostic devices are the largest consumers of advanced coatings. Cardiovascular coatings must deliver not only lubricity but also drug-delivery capabilities. Orthopedic coatings often require bioresorbable materials, while diagnostic device coatings emphasize anti-fog, anti-glare, and anti-microbial properties.
Automated Coating Systems for Medical Devices Price Trend Influenced by Tech Complexity
The automated coating systems for medical devices price trend is primarily influenced by system complexity, throughput capacity, and integration requirements. Entry-level systems with basic programmable controls and low throughput typically range between USD 75,000 and USD 150,000. However, fully automated, high-volume systems equipped with real-time analytics, AI integration, and cleanroom compatibility can exceed USD 500,000.
For instance, systems designed for drug-eluting stent production command premium pricing due to the stringent precision and contamination control requirements. Similarly, multi-axis robotic coating systems for implantable orthopedic devices carry higher upfront costs but deliver long-term value through reduced waste and labor savings.
Regional Price Differences Reflect Supply Chain and Tariff Dynamics
Automated coating systems for medical devices price variation is also visible across geographies due to differences in supply chain efficiency, import tariffs, and localization of assembly. In North America and Western Europe, higher labor and compliance costs lead to higher system prices, but value-added features such as remote monitoring and automated documentation are standard.
In contrast, prices in Asia Pacific—particularly China and India—are more competitive due to the presence of local system integrators and government incentives for automation. However, these systems may offer fewer customization options and lower after-sales support compared to Western counterparts.
Automated Coating Systems for Medical Devices Price Sensitivity Among Small Manufacturers
Small and mid-sized medical device firms exhibit heightened sensitivity to the automated coating systems for medical devices price trend. These firms are often caught between the need for precision and the pressure to contain capital expenditures. To bridge this gap, equipment providers are now offering leasing models and modular systems that allow incremental upgrades. This flexibility allows smaller firms to enter the market with semi-automated solutions and scale up as demand grows.
Additionally, regional governments are increasingly supporting automation adoption through grants and tax incentives, helping smaller players offset initial investments in automated coating infrastructure.
Price Trend Outlook: Stabilizing with Innovation and Competition
As more players enter the automated coating systems for medical devices market, competition is expected to exert downward pressure on pricing in standardized segments. However, for highly specialized applications—such as coating neurosurgical implants or microfluidic diagnostic cartridges—prices are likely to remain high due to the technical sophistication required.
System manufacturers are also integrating more AI and cloud-based features, which could create a two-tier pricing structure: one for high-end, data-rich platforms and another for simplified, standalone systems. Over the next five years, while the average automated coating systems for medical devices price may stabilize, the market will likely segment further based on capability tiers.
“Automated coating systems for mdeical devices Manufacturing Database, Automated coating systems for mdeical devices Manufacturing Capacity”
-
-
- Automated coating systems for mdeical devices top manufacturers market share for 30+ manufacturers
- Top 9 manufacturers and top 19 manufacturers of Automated coating systems for mdeical devices in North America, Europe, Asia Pacific
- Production plant capacity by manufacturers and Automated coating systems for mdeical devices production data for 30+ market players
- Automated coating systems for mdeical devices production dashboard, Automated coating systems for mdeical devices production data in excel format
-
Global Leaders in the Automated Coating Systems for Medical Devices Market
The automated coating systems for medical devices market is highly consolidated, with a few dominant global manufacturers accounting for a significant share of the revenue. These companies lead the industry through technological innovation, strategic acquisitions, and strong distribution networks. Each major player brings unique capabilities to the table, from high-precision nano-coating systems to turnkey modular coating lines integrated with cleanroom technologies.
Sono-Tek Corporation: Precision Ultrasonic Coating for Medical Devices
Sono-Tek Corporation is one of the most prominent players in the automated coating systems for medical devices market. Known for its patented ultrasonic spray technology, Sono-Tek has established a strong foothold in precision medical applications. Its product line includes the ExactaCoat and FlexiCoat systems, which are widely adopted for coating stents, balloon catheters, and diagnostic components.
These systems offer advantages such as minimal overspray, ultra-thin coating layers, and high repeatability—crucial for drug-eluting applications. The company’s systems are scalable and customizable, which has allowed it to maintain a leading market share in North America and Europe, particularly among contract manufacturers and OEMs seeking precision and regulatory compliance.
SAMES KREMLIN: Robust Solutions for Mass Production
SAMES KREMLIN, part of the EXEL Industries group, is another dominant player with a strong portfolio in spray and electrostatic coating solutions for the medical sector. The company’s Inobell and Nanobell atomizers are integrated into automated coating systems for devices requiring ultra-fine finishes, such as implantable electronic sensors and coated metal surgical instruments.
SAMES KREMLIN holds a competitive market share in Europe and Asia, where its high-throughput systems are favored for large-scale production environments. The firm’s expertise in surface treatment and fluid dynamics has enabled it to develop tailored coating solutions that meet the growing demand for specialty medical devices.
Nordson Corporation: Expanding Market Share Through Innovation
Nordson Corporation is a global heavyweight in dispensing and coating systems and holds a substantial share of the automated coating systems for medical devices market. The company’s ASYMTEK product line includes micro-dispensing and conformal coating systems widely used in the electronics and life sciences sectors.
In medical devices, Nordson’s Spectrum II systems are applied to coat complex geometries with hydrophobic or biocompatible materials. These systems integrate advanced motion control and process monitoring, making them ideal for high-precision coatings required in catheters, microfluidic devices, and lab-on-chip platforms. Nordson continues to expand its market share by investing in AI-driven process optimization and in-line inspection technologies.
PlasmaTreat: Leadership in Surface Activation and Pre-Treatment
While not a coating system provider in the traditional sense, PlasmaTreat plays a vital role in the automated coating systems for medical devices market by offering surface pre-treatment technologies that enhance coating adhesion and durability. Its Openair-Plasma systems are widely used as a pre-coating step in catheter and tubing production lines.
The company’s solutions are particularly important for substrates like silicone, polyethylene, and other low-surface-energy materials common in medical devices. PlasmaTreat’s integration with automated lines has become a standard for manufacturers looking to boost coating reliability and reduce failure rates, thereby earning the company a niche but essential market share.
Specialty Coating Systems (SCS): Pioneering in Conformal and Parylene Coatings
Specialty Coating Systems (SCS) is a leader in parylene and conformal coating equipment used in medical applications. Its PrecisionCoat series has become the go-to solution for devices requiring ultra-thin, uniform coatings that provide moisture, chemical, and dielectric barriers.
SCS maintains a strong global presence with installations in North America, Europe, and Asia, particularly among manufacturers of pacemakers, hearing aids, and diagnostic equipment. The company’s focus on biocompatible, ISO-compliant coating technologies allows it to maintain a significant share in specialized medical applications where performance and reliability are non-negotiable.
Automated Coating Systems for Medical Devices Market Share by Manufacturer
The automated coating systems for medical devices market is segmented with top players such as Sono-Tek, Nordson, and SCS collectively accounting for an estimated 45–50% of global market revenue. Mid-tier players such as SAMES KREMLIN and PlasmaTreat contribute another 25–30%, while smaller regional manufacturers and custom system integrators make up the rest.
Market share is strongly influenced by the application segment each company specializes in. For instance, Sono-Tek leads in cardiovascular applications, SCS dominates in electronics-integrated medical devices, and Nordson is a preferred choice for high-mix production lines. The remaining market is fragmented, with smaller players often competing on customization, price, and local service capabilities.
Product Line Differentiation as a Key to Market Penetration
Manufacturers are increasingly differentiating their offerings through modularity, software integration, and environmental compliance. For example, Nordson’s proprietary software platforms allow users to fine-tune coating parameters with AI feedback loops, significantly reducing material waste. SAMES KREMLIN has also developed low-VOC and solvent recovery systems, aligning with sustainability initiatives.
Furthermore, SCS has pioneered the use of environmentally stable parylene dimer compounds in its coating materials, which has given it an edge in environmentally regulated markets such as Europe and California. This product-level innovation is becoming a key lever in capturing larger portions of the market.
Recent Developments and Industry News
- In October 2023, Nordson announced a strategic upgrade to its Spectrum II line, adding machine-learning-based defect detection, aimed at reducing coating inconsistencies in high-speed production environments.
- In March 2024, Sono-Tek expanded its manufacturing facility in New York to meet growing global demand for its ExactaCoat series, reflecting a 20% year-over-year increase in orders from the medical device sector.
- In July 2023, PlasmaTreat partnered with a leading catheter manufacturer in Germany to co-develop a pre-treatment line integrated with AI-powered monitoring for catheter coatings, aimed at improving adhesion by over 30%.
- In February 2025, Specialty Coating Systems launched the PrecisionCoat VI, a next-generation system offering dual-coating capabilities for simultaneous application of parylene and acrylic coatings. This system is already being adopted in production lines for implantable neuromodulation devices.
Strategic Outlook for Market Players
Looking ahead, the automated coating systems for medical devices market will see increased competition driven by digital transformation, sustainability regulations, and demand for ultra-precision coatings. Market leaders are expected to expand their portfolios through R&D investments and acquisitions of niche technology providers. Smaller players will likely focus on regional customization, service flexibility, and competitive pricing.
As device complexity increases and coating functionality becomes more central to device performance, manufacturers of automated coating systems will play an even more critical role in shaping the future of medical device innovation and global healthcare delivery.
“Automated coating systems for mdeical devices Production Data and Automated coating systems for mdeical devices Production Trend, Automated coating systems for mdeical devices Production Database and forecast”
-
-
- Automated coating systems for mdeical devices production database for historical years, 10 years historical data
- Automated coating systems for mdeical devices production data and forecast for next 9 years
-
Market Scenario, Demand vs Supply, Average Product Price, Import vs Export, till 2035
- Global Automated coating systems for mdeical devices Market revenue and demand by region
- Global Automated coating systems for mdeical devices Market production and sales volume
- United States Automated coating systems for mdeical devices Market revenue size and demand by country
- Europe Automated coating systems for mdeical devices Market revenue size and demand by country
- Asia Pacific Automated coating systems for mdeical devices Market revenue size and demand by country
- Middle East & Africa Automated coating systems for mdeical devices Market revenue size and demand by country
- Latin America Automated coating systems for mdeical devices Market revenue size and demand by
- Import-export scenario – United States, Europe, APAC, Latin America, Middle East & Africa
- Average product price – United States, Europe, APAC, Latin America, Middle East & Africa
- Market player analysis, competitive scenario, market share analysis
- Business opportunity analysis
Key questions answered in the Global Automated coating systems for mdeical devices Market Analysis Report:
- What is the market size for Automated coating systems for mdeical devices in United States, Europe, APAC, Middle East & Africa, Latin America?
- What is the yearly sales volume of Automated coating systems for mdeical devices and how is the demand rising?
- Who are the top market players by market share, in each product segment?
- Which is the fastest growing business/ product segment?
- What should be the business strategies and Go to Market strategies?
The report covers Automated coating systems for mdeical devices Market revenue, Production, Sales volume, by regions, (further split into countries):
- Asia Pacific (China, Japan, South Korea, India, Indonesia, Vietnam, Rest of APAC)
- Europe (UK, Germany, France, Italy, Spain, Benelux, Poland, Rest of Europe)
- North America (United States, Canada, Mexico)
- Latin America (Brazil, Argentina, Rest of Latin America)
- Middle East & Africa
Table of Contents:
Automated Coating Systems for Medical Devices Market report:
- Introduction to Automated Coating Systems for Medical Devices
- Scope and Importance in the Medical Device Industry
- Evolution of Coating Technologies in Medical Applications
- Key Functionalities and Technical Specifications of Automated Coating Systems
- Classification of Medical Device Coatings
- 5.1 Antimicrobial Coatings
- 5.2 Hydrophilic Coatings
- 5.3 Drug-Eluting Coatings
- 5.4 Biocompatible Coatings
- Regulatory Framework Governing Medical Device Coatings
- Market Dynamics and Industry Trends
- 7.1 Drivers Influencing Market Growth
- 7.2 Restraints and Challenges in Adoption
- 7.3 Opportunities in Emerging Healthcare Markets
- Impact of COVID-19 and Post-Pandemic Market Recovery
- Technological Advancements in Automated Coating Processes
- 9.1 Plasma Coating Technologies
- 9.2 Nano-Coating Techniques
- 9.3 Robotic Precision Coating Systems
- Global Market Overview and Growth Forecast (2020–2035)
- Analysis of Key End-Use Medical Devices
- 11.1 Catheters
- 11.2 Stents
- 11.3 Implants
- 11.4 Surgical Instruments
- 11.5 Diagnostic Equipment
- Market Segmentation by Coating Type, Device, and Application
- Regional Market Insights and Forecasts
- 13.1 North America Market Trends and Outlook
- 13.2 Europe Market Dynamics and Forecast
- 13.3 Asia Pacific Growth Opportunities and Challenges
- 13.4 Latin America Emerging Markets
- 13.5 Middle East & Africa Market Landscape
- Competitive Landscape of Automated Coating System Providers
- Profiles of Key Players in the Medical Device Coating Industry
- Strategic Developments: Partnerships, Mergers, and Acquisitions
- Cost Analysis and Pricing Trends in Coating Processes
- Supply Chain Analysis for Medical Device Coating Systems
- Manufacturing Process Optimization and Efficiency Trends
- Analysis of Key Raw Materials and Sourcing Strategies
- Innovations in Biocompatible and Drug-Eluting Coatings
- Risk Analysis and Market Entry Barriers
- Sustainability Trends and Eco-Friendly Coating Solutions
- Patent Landscape and Intellectual Property Considerations
- Quality Control and Compliance in Coating Systems
- Market Opportunities in Minimally Invasive and Wearable Medical Devices
- Integration of AI and Automation in Coating Technologies
- Case Studies of Successful Automated Coating Applications in Medical Devices
- Market Forecast and Future Growth Prospects (2020–2035)
- Key Takeaways and Strategic Recommendations for Stakeholders
Other recently published reports:
“Every Organization is different and so are their requirements”- Datavagyanik
Companies We Work With
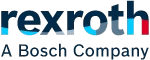
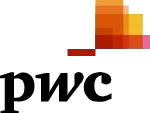
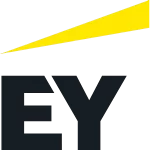
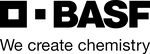
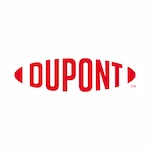

Do You Want To Boost Your Business?
drop us a line and keep in touch
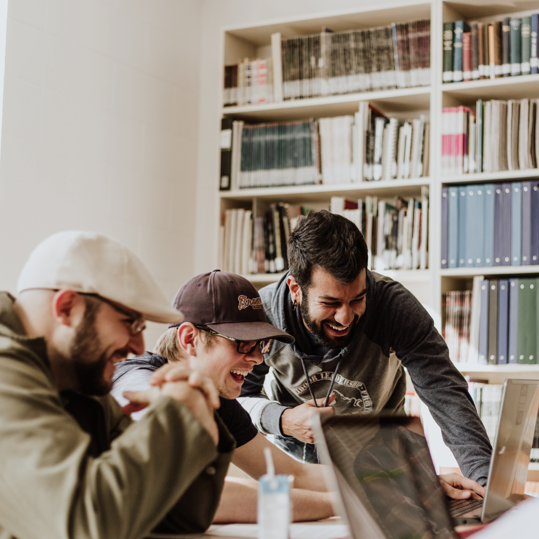