Carbon Fiber Reinforced Polymers in 3D Printing Market Size, Production, Sales, Average Product Price, Market Share, Import vs Export
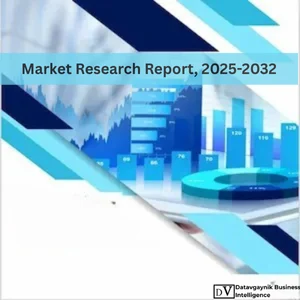
- Published 2025
- No of Pages: 120+
- 20% Customization available
Carbon Fiber Reinforced Polymers in 3D Printing Market Growth Drivers
The Carbon Fiber Reinforced Polymers in 3D Printing Market is experiencing substantial growth, driven by an increased demand for high-performance, lightweight materials across various industries. These materials, which combine the strength of carbon fibers with the flexibility of polymers, are increasingly sought after for their exceptional mechanical properties, including high tensile strength, impact resistance, and dimensional stability. As industries look to push the boundaries of product design and functionality, Carbon Fiber Reinforced Polymers in 3D Printing Market are rapidly gaining traction.
High Demand in Aerospace and Automotive Industries
The Carbon Fiber Reinforced Polymers in 3D Printing Market is witnessing robust demand from sectors like aerospace and automotive, where lightweight, high-strength materials are crucial. The aerospace industry, for instance, continues to seek materials that reduce weight without compromising structural integrity. CFRPs, due to their superior strength-to-weight ratio, have become essential in the manufacturing of components like brackets, wings, and fuselage parts. The Global Aerospace Manufacturing Market is projected to grow at a CAGR of 5.4%, further boosting the need for CFRPs in 3D printing applications. For example, companies like Boeing and Lockheed Martin are increasingly utilizing CFRPs in additive manufacturing to improve fuel efficiency and reduce overall aircraft weight.
The automotive industry has also emerged as a significant adopter of Carbon Fiber Reinforced Polymers in 3D Printing Market. The push towards electric vehicles (EVs) and fuel-efficient designs has placed a spotlight on lightweight materials. CFRPs help achieve these objectives by significantly reducing the weight of vehicles while maintaining high strength, improving performance, and energy efficiency. Major automotive manufacturers, including Ford and General Motors, are leveraging CFRPs to create custom, high-performance parts for both prototype and production models.
The shift toward electric vehicles is expected to accelerate the adoption of CFRPs, particularly in vehicle body panels, engine components, and structural supports. With global EV sales projected to grow by 27% by 2027, the demand for CFRPs in 3D printing is expected to follow suit.
Datavagyanik also covers related markets such as the Carbon-Fiber Reinforced Polyamide Market, the High-Performance Polymers for Industrial 3D Printing Market, and the Recycled Plastics in 3D Printing Filaments Market. These related markets contribute valuable context to the primary topic by highlighting complementary trends and technologies.
Customization and Complex Geometries in Industrial Applications
A key factor contributing to the growth of the Carbon Fiber Reinforced Polymers in 3D Printing Market is the ability of 3D printing to create customized, complex geometries. Traditional manufacturing processes often face limitations when it comes to producing intricate designs or parts that require specific geometrical features. However, 3D printing allows for the creation of parts with shapes and structures that would be impossible or prohibitively expensive to produce using conventional methods. CFRPs excel in this area, enabling the production of high-performance, lightweight parts with optimized material usage, a feature particularly beneficial in aerospace, automotive, and industrial manufacturing.
For instance, in aerospace, CFRPs are used to print complex internal structures of engine components that not only reduce weight but also improve performance and efficiency. In automotive manufacturing, the ability to print intricate car parts—such as suspension components or interior features—has led to significant reductions in production costs and time. The versatility of CFRPs in 3D printing allows for rapid prototyping of these components, speeding up design iterations and reducing lead times. This flexibility is becoming indispensable as industries push for increasingly tailored products and faster production cycles.
Rapid Prototyping and Shortened Lead Times
The ability to rapidly prototype and test designs is one of the most significant advantages of using Carbon Fiber Reinforced Polymers in 3D Printing Market applications. Traditional manufacturing methods often require long lead times to develop molds, tools, and prototypes, which can slow down the product development process. In contrast, 3D printing allows manufacturers to quickly create functional prototypes of high-performance parts using CFRPs. This capability results in faster product iterations, reduced development costs, and more efficient testing processes.
For example, in the automotive sector, companies like Ford have adopted CFRP-based 3D printing to rapidly test and validate new car components, significantly shortening the design-to-production timeline. In aerospace, the ability to print prototype parts, test their performance, and adjust designs in real-time is crucial to meeting strict safety and regulatory standards. This accelerated prototyping process has led to increased adoption of CFRPs, as companies strive to meet market demands more efficiently. The ability to test and iterate with minimal lead time is a game-changer for industries where innovation and quick turnarounds are essential.
Cost-Effective Low-Volume Production
Another compelling driver of the Carbon Fiber Reinforced Polymers in 3D Printing Market is the ability to produce high-performance parts in low to medium volumes without incurring the high costs typically associated with traditional manufacturing methods. Conventional manufacturing processes, such as injection molding or die-casting, are often not cost-effective for producing small batches of parts. CFRP-based 3D printing, however, eliminates the need for expensive molds, tooling, and setup costs, making it an ideal solution for low-volume production runs.
This is particularly advantageous in industries that require bespoke or highly specialized components, such as medical devices, aerospace, and defense. In the medical field, for example, CFRPs are used to create customized implants and prosthetics tailored to individual patients. By using 3D printing, manufacturers can quickly produce high-quality, patient-specific parts without the need for expensive tooling, which can make traditional manufacturing methods prohibitively expensive for small production runs. The flexibility and cost-effectiveness of CFRPs in 3D printing are opening up new possibilities for industries that rely on low-volume production.
Sustainability and Waste Reduction
The growing emphasis on sustainability in manufacturing is another key factor driving the adoption of Carbon Fiber Reinforced Polymers in 3D Printing Market. 3D printing is inherently more sustainable than traditional subtractive manufacturing methods, as it is an additive process that builds parts layer by layer, minimizing material waste. This efficiency in material usage is particularly important in industries where raw material costs are high, such as aerospace and automotive.
Additionally, the use of recycled carbon fibers in the production of CFRPs further enhances the sustainability of the material. Companies in the Carbon Fiber Reinforced Polymers in 3D Printing Market are increasingly focusing on incorporating recycled carbon fibers into their 3D printing materials, aligning with global efforts to reduce carbon footprints and promote circular economies. For example, the aerospace industry is exploring the use of recycled CFRPs in manufacturing lightweight, high-strength parts, reducing both waste and the environmental impact of production processes.
As industries strive to meet sustainability goals, the use of CFRPs in 3D printing is expected to grow, driven by the material’s ability to reduce waste, increase material efficiency, and support the use of recycled content. This trend is especially significant as companies seek to align with global initiatives to reduce carbon emissions and adopt more environmentally friendly production practices.
Increasing Integration of CFRPs in Diverse Industries
The Carbon Fiber Reinforced Polymers in 3D Printing Market is expanding rapidly across a wide range of industries, from aerospace to healthcare to sports equipment. In healthcare, CFRPs are being used to create custom prosthetics, implants, and medical devices, thanks to their lightweight, durable, and biocompatible properties. The medical sector is seeing increasing demand for personalized healthcare solutions, and CFRP-based 3D printing offers the ideal combination of strength, flexibility, and customization for this purpose.
In sports and leisure, CFRPs are used to create high-performance equipment like bicycles, tennis rackets, and skis. The material’s ability to reduce weight while maintaining strength and durability has made it a popular choice for elite athletes seeking an edge in performance. As sports equipment manufacturers continue to push for innovations that improve performance, the demand for CFRPs in 3D printing is set to increase.
As more industries recognize the benefits of CFRPs in 3D printing, the market will continue to expand, driven by the material’s versatility and high-performance capabilities. From reducing weight and improving fuel efficiency in aerospace and automotive to providing personalized healthcare solutions in medicine, CFRPs are poised to play an increasingly important role in the future of additive manufacturing.
“Track Country-wise Carbon Fiber Reinforced Polymers in 3D Printing Production and Demand through our Carbon Fiber Reinforced Polymers in 3D Printing Production Database”
-
-
- Carbon Fiber Reinforced Polymers in 3D Printing production database for 28+ countries worldwide
- Carbon Fiber Reinforced Polymers in 3D Printing Powder sales volume for 32+ countries
- Country-wise Carbon Fiber Reinforced Polymers in 3D Printing production capacity and production plant mapping, production capacity utilization for 28+ manufacturers
- Carbon Fiber Reinforced Polymers in 3D Printing production plants and production plant capacity analysis for top manufacturers
-
Geographical Demand for Carbon Fiber Reinforced Polymers in 3D Printing Market
The demand for Carbon Fiber Reinforced Polymers in 3D Printing Market is witnessing a significant shift across various geographical regions, driven by the increasing need for lightweight, high-performance materials in key industries. North America, Europe, and the Asia Pacific region are leading the charge, with each region experiencing unique growth drivers, challenges, and opportunities.
North America’s Stronghold in Carbon Fiber Reinforced Polymers in 3D Printing Market
North America, particularly the United States, has established itself as a dominant player in the Carbon Fiber Reinforced Polymers in 3D Printing Market, thanks to the region’s advanced manufacturing capabilities, a robust aerospace and defense sector, and strong automotive demand. The United States, with major manufacturers such as Boeing, Lockheed Martin, and Ford, is at the forefront of leveraging CFRPs for 3D printing applications. Aerospace and automotive industries are increasingly turning to CFRPs to reduce weight, enhance fuel efficiency, and improve performance. For instance, the use of CFRPs in automotive applications has been projected to grow by 20% annually as demand for lightweight vehicle parts surges due to the rise of electric vehicles.
In addition to aerospace and automotive, the U.S. medical industry is also embracing CFRP 3D printing technologies. Personalized healthcare solutions such as custom implants, prosthetics, and orthopedic devices are gaining significant traction due to the strength and biocompatibility of CFRPs. The rapid prototyping capability offered by 3D printing is accelerating the development of these highly customized medical solutions.
Europe: A Hub for Aerospace and Automotive Applications of CFRPs in 3D Printing
Europe stands as another prominent region for the Carbon Fiber Reinforced Polymers in 3D Printing Market. Countries such as Germany, the UK, France, and Italy are spearheading the development and adoption of CFRP-based 3D printing in industries like aerospace, automotive, and industrial manufacturing. Europe’s leading automotive players, including BMW, Mercedes-Benz, and Ferrari, are heavily investing in CFRPs to develop lightweight, durable components for high-performance vehicles. The European automotive market is projected to grow at a CAGR of 5.8% by 2026, with CFRP adoption playing a pivotal role in achieving emission and performance targets for electric vehicles.
The aerospace sector in Europe is also witnessing strong growth in CFRP usage, driven by companies like Airbus and Rolls-Royce. CFRPs are integral to the design and production of lightweight, high-strength components for aircraft, which are essential for improving fuel efficiency and reducing environmental impact. Europe’s aerospace sector is expected to grow at a rate of 4.5% annually, fueled by the increased adoption of additive manufacturing techniques and CFRPs in the production of parts like engine components and structural elements.
Asia Pacific: A Rising Power in Carbon Fiber Reinforced Polymers in 3D Printing Market
The Asia Pacific region is quickly becoming a hotbed for the growth of the Carbon Fiber Reinforced Polymers in 3D Printing Market. China, Japan, South Korea, and India are embracing CFRP-based 3D printing technologies across multiple industries. China, being the largest producer of carbon fibers, is also witnessing an exponential rise in the demand for CFRPs in 3D printing, particularly in aerospace, automotive, and manufacturing. The country’s aerospace industry, led by COMAC, is increasingly integrating CFRPs in the development of aircraft components, driven by the need for lighter, fuel-efficient designs.
In Japan, automotive giants such as Toyota and Honda are incorporating CFRPs into their 3D printing processes to create lightweight, high-performance parts, particularly for electric vehicles. The country’s automotive sector is set to grow by 6% annually, with CFRP adoption playing a crucial role in vehicle weight reduction and performance optimization. South Korea is also witnessing growing demand for CFRPs in aerospace and automotive manufacturing, with companies like Hyundai and Kia actively researching and implementing CFRP 3D printing technologies.
India, while slower to adopt CFRP 3D printing compared to its counterparts, is beginning to make significant strides in sectors like aerospace and defense. The Indian Space Research Organisation (ISRO) and defense contractors are increasingly turning to CFRPs for 3D printing lightweight components for satellites and military equipment.
Carbon Fiber Reinforced Polymers in 3D Printing Market Segmentation: By Type
The Carbon Fiber Reinforced Polymers in 3D Printing Market is segmented based on the type of resin matrix used in combination with carbon fibers. The two primary types of CFRPs used in 3D printing are thermoplastic and thermoset CFRPs, each catering to different industry needs and applications.
Thermoplastic CFRPs: Durability Meets Flexibility
Thermoplastic CFRPs have gained significant attention in the 3D printing industry due to their ability to be reshaped and reprocessed. These materials, often based on resins like nylon, PEEK, and PEKK, are highly suitable for applications that require repeated heating and cooling cycles. The thermoplastic matrix provides the advantage of recyclability, allowing manufacturers to reuse materials, which makes them highly cost-effective for applications in automotive, aerospace, and industrial manufacturing. As a result, the thermoplastic CFRP market is expected to see robust growth, with a CAGR of 6% over the next five years.
Thermoset CFRPs: Strength and Stability
On the other hand, thermoset CFRPs are gaining traction in industries requiring exceptional rigidity, heat resistance, and overall strength. Once cured, thermoset CFRPs cannot be reshaped, making them ideal for high-performance applications in aerospace, defense, and sports equipment. These CFRPs provide unmatched structural integrity and are used extensively for the production of components such as aircraft wings, fuselage parts, and high-performance sports gear. The thermoset CFRP market is anticipated to grow at a CAGR of 5% as demand for high-performance parts continues to increase in these sectors.
Carbon Fiber Reinforced Polymers in 3D Printing Market Segmentation: By Application
The Carbon Fiber Reinforced Polymers in 3D Printing Market is also segmented based on the applications of CFRPs in various industries. Some of the key applications include prototyping, end-use parts manufacturing, and tooling and fixtures.
Prototyping: The Key to Faster Product Development
Prototyping is one of the most critical applications of CFRPs in 3D printing. The ability to quickly create functional prototypes allows manufacturers to test, validate, and refine their designs in less time than traditional manufacturing methods would permit. For industries like automotive and aerospace, the speed and flexibility of CFRP-based prototyping have been a game-changer. For example, automotive companies like Ford use CFRP 3D printing to rapidly prototype engine components, significantly reducing design iteration cycles. As the demand for faster product development intensifies, the prototyping segment is expected to grow at a robust pace of 7.2% annually.
End-Use Parts Manufacturing: From Concept to Functionality
End-use parts manufacturing is another critical application of CFRPs in 3D printing, where the focus is on creating final components for products. The ability to produce lightweight, durable parts with complex geometries is crucial in industries such as aerospace, automotive, and healthcare. CFRPs enable the production of custom-made components that meet stringent performance and durability standards. In aerospace, for example, companies are using CFRPs to manufacture structural components for aircraft that not only reduce weight but also improve overall efficiency and safety. The end-use parts manufacturing segment of the CFRP 3D printing market is forecasted to grow at a CAGR of 8% over the next five years.
Tooling and Fixtures: Enhanced Precision in Manufacturing
The tooling and fixtures segment is another area where CFRPs are making a significant impact. Using 3D printing to create customized molds, jigs, and assembly tools offers manufacturers the ability to improve precision while reducing lead times and production costs. The ability to print complex, custom geometries with CFRPs has revolutionized the production of tooling and fixtures, particularly in industries that require high precision and low-volume production. This segment is projected to grow by 6.5% annually as industries demand more efficient and customizable production processes.
Carbon Fiber Reinforced Polymers in 3D Printing Price Trends and Market Dynamics
The price trend for Carbon Fiber Reinforced Polymers in 3D Printing Market has been impacted by several factors, including raw material costs, technological advancements, and market demand. Over the last few years, the price of CFRPs has decreased due to advances in manufacturing technologies and economies of scale. For instance, the introduction of continuous fiber 3D printing methods has significantly reduced the production costs of CFRPs, making them more accessible to industries that were previously hesitant to adopt this material due to its high cost.
However, the price of CFRPs is still relatively high compared to other materials, such as traditional polymers and metals. The price trend is expected to remain volatile in the short term due to fluctuations in the cost of carbon fibers and resin systems. Despite this, the long-term outlook for CFRP prices is optimistic, with a projected steady decrease as 3D printing technologies continue to advance and competition in the CFRP production space intensifies.
As demand for CFRPs in 3D printing grows across various sectors, price trends are expected to stabilize, creating a more predictable and cost-effective market for manufacturers. The continued development of recycled carbon fibers and sustainable production methods will also play a critical role in shaping the price dynamics of the market in the coming years.
Conclusion: A Diverse and Growing Market for CFRPs in 3D Printing
The Carbon Fiber Reinforced Polymers in 3D Printing Market is poised for significant growth, fueled by a variety of factors such as increasing demand for high-performance materials, the rise of electric vehicles, and the continued advancement of 3D printing technologies. Geographically, North America, Europe, and the Asia Pacific region are leading the market, each driven by sector-specific growth opportunities and demand for CFRPs in additive manufacturing applications. As the market continues to evolve, industries across the board are increasingly turning to CFRPs to achieve lighter, stronger, and more durable components, positioning this material as a cornerstone of future manufacturing innovations.
“Carbon Fiber Reinforced Polymers in 3D Printing Manufacturing Database, Carbon Fiber Reinforced Polymers in 3D Printing Manufacturing Capacity”
-
-
- Carbon Fiber Reinforced Polymers in 3D Printing top manufacturers market share for 28+ manufacturers
- Top 8 manufacturers and top 18 manufacturers of Carbon Fiber Reinforced Polymers in 3D Printing in North America, Europe, Asia Pacific
- Production plant capacity by manufacturers and Carbon Fiber Reinforced Polymers in 3D Printing production data for 28+ market players
- Carbon Fiber Reinforced Polymers in 3D Printing production dashboard, Carbon Fiber Reinforced Polymers in 3D Printing production data in excel format
-
Top Manufacturers in the Carbon Fiber Reinforced Polymers in 3D Printing Market
The Carbon Fiber Reinforced Polymers in 3D Printing Market is witnessing an influx of key players across the global manufacturing landscape. These players have cemented their positions by delivering high-quality materials and innovative 3D printing solutions that meet the diverse needs of various industries. Among the most notable companies, several have emerged as leaders in the CFRP-based 3D printing market, with robust product portfolios and a deep commitment to advancing technology.
- Markforged
Markforged is a trailblazer in the world of 3D printing, specializing in carbon fiber reinforced materials for additive manufacturing. The company’s flagship product, the Markforged X7, uses continuous carbon fiber filaments to print parts with exceptional strength-to-weight ratios. The machine is known for its precision and ability to print high-performance CFRP parts that can withstand demanding industrial applications.
Markforged has played a significant role in driving the adoption of CFRPs for functional end-use parts across industries like aerospace, automotive, and manufacturing. Their proprietary Onyx filament, combined with carbon fiber reinforcement, has made it possible to print both lightweight and durable components, significantly reducing production time and costs.
- 3D Systems
3D Systems is one of the largest and most diversified manufacturers in the 3D printing space, offering a wide range of products that cater to different sectors. In the Carbon Fiber Reinforced Polymers in 3D Printing Market, 3D Systems provides robust materials like the DuraForm® FR1200, a CFRP-based material that offers enhanced mechanical properties and is suitable for high-temperature environments.
Their 3D printing technology supports industries such as aerospace, automotive, and healthcare, where there is a growing demand for CFRP components. 3D Systems has leveraged its global presence to become a significant player in the CFRP additive manufacturing sector, making its mark by offering high-strength, lightweight materials for a variety of applications.
- Stratasys
Stratasys is another key manufacturer in the CFRP 3D printing market, offering cutting-edge technologies and materials that have reshaped the way industries approach additive manufacturing. Their FDM-based (Fused Deposition Modeling) 3D printers, combined with carbon fiber reinforcement, enable the creation of parts with high strength-to-weight ratios. Stratasys’ continuous carbon fiber technology, used in machines like the Fortus 900mc, is a game-changer for industries requiring strong, durable parts.
Stratasys is particularly popular in the aerospace and automotive industries, where high-performance CFRP parts are required for structural components. Their composite filament, including carbon fiber-infused materials, is widely used for applications like prototyping and low-volume production runs.
- EOS GmbH
EOS is a leading provider of industrial 3D printing solutions and materials, including high-performance Carbon Fiber Reinforced Polymers in 3D Printing Market. EOS provides specialized 3D printing materials like EOS® Carbon PA12, a material that blends carbon fiber with polyamide for excellent stiffness, strength, and durability. EOS’ solution is widely adopted in automotive and aerospace industries for producing high-performance components with superior mechanical properties.
The company’s reputation for producing quality materials and machines has helped them secure a strong foothold in the CFRP 3D printing market. EOS also offers a comprehensive range of printers capable of printing parts with carbon fiber reinforcement, catering to both rapid prototyping and end-use production needs.
- HP Inc.
HP Inc. has made significant strides in the 3D printing market with its innovative Multi Jet Fusion technology, which allows for the production of highly detailed and durable parts. HP’s collaboration with major players like BASF has led to the development of high-performance composite filaments that incorporate carbon fiber to strengthen 3D printed parts.
HP’s expertise in high-quality 3D printing is evident in industries like automotive, healthcare, and consumer goods, where demand for CFRP parts with tailored mechanical properties is on the rise. HP’s 3D printing solutions focus on delivering cost-effective production and high-quality results with CFRPs, enabling manufacturers to create high-strength components with reduced weight.
- Toray Industries
Toray Industries is a leading manufacturer of advanced composite materials, including carbon fiber-reinforced filaments used in 3D printing applications. Toray’s carbon fiber materials are used in a variety of sectors, including automotive, aerospace, and sports equipment. They supply high-performance composite fibers and resins to manufacturers in the 3D printing industry, making them an essential player in the Carbon Fiber Reinforced Polymers in 3D Printing Market.
Toray’s commitment to developing new CFRP materials and their expertise in carbon fiber production enables them to maintain a competitive edge. Their technology is increasingly being utilized for high-performance parts such as aircraft components, automotive parts, and structural applications.
Carbon Fiber Reinforced Polymers in 3D Printing Market Share by Manufacturers
The Carbon Fiber Reinforced Polymers in 3D Printing Market is highly competitive, with several manufacturers vying for market share across different geographical regions and sectors. Markforged, 3D Systems, Stratasys, and EOS GmbH represent some of the most influential players, holding a significant portion of the global market. The competitive dynamics of the market are driven by the growing demand for high-strength, lightweight components in industries such as aerospace, automotive, and healthcare.
Markforged holds a prominent position in the CFRP 3D printing market due to its strong product portfolio, including its continuous carbon fiber technology, which enables manufacturers to produce parts with exceptional mechanical properties. Their user-friendly systems and reliable performance have positioned them as a top player, particularly in rapid prototyping and low-volume production applications.
3D Systems and Stratasys have also established strong positions with their comprehensive product lines and industry-specific solutions. While 3D Systems is well-regarded for its diverse materials and versatility in various sectors, Stratasys remains a leader in the aerospace and automotive industries, where their composite materials and machines offer unmatched durability and performance.
EOS GmbH and HP Inc. are important players in the market, with EOS holding a significant share due to its specialization in industrial-grade 3D printing systems for carbon fiber-based materials. HP’s advanced Multi Jet Fusion technology, coupled with its partnership with leading material suppliers, positions it as a growing contender in the CFRP 3D printing sector.
Recent News and Industry Developments
Recent advancements and partnerships have further fueled the growth of the Carbon Fiber Reinforced Polymers in 3D Printing Market. On March 15, 2025, Stratasys announced the release of its latest composite filament, designed to deliver enhanced strength and durability in demanding environments. This move is expected to bolster Stratasys’ market share, especially in the automotive and aerospace sectors, where high-performance parts are in high demand.
In another significant development, Markforged unveiled an updated version of its X7 3D printer on April 1, 2025. The new machine incorporates a more advanced continuous carbon fiber printing system that offers even higher precision and durability. This update allows Markforged to expand its offerings in sectors such as industrial manufacturing and defense, where high-performance, lightweight parts are critical.
Meanwhile, HP Inc. has focused on enhancing its Multi Jet Fusion technology, signing a partnership with BASF on April 10, 2025, to develop new CFRP materials for 3D printing. This partnership aims to expand the use of CFRPs in industries such as healthcare, automotive, and consumer goods, where there is an increasing demand for high-strength, lightweight components.
“Carbon Fiber Reinforced Polymers in 3D Printing Production Data and Carbon Fiber Reinforced Polymers in 3D Printing Production Trend, Carbon Fiber Reinforced Polymers in 3D Printing Production Database and forecast”
-
-
- Carbon Fiber Reinforced Polymers in 3D Printing production database for historical years, 10 years historical data
- Carbon Fiber Reinforced Polymers in 3D Printing production data and forecast for next 7 years
-
Market Scenario, Demand vs Supply, Average Product Price, Import vs Export, till 2035
- Global Carbon Fiber Reinforced Polymers in 3D Printing Market revenue and demand by region
- Global Carbon Fiber Reinforced Polymers in 3D Printing Market production and sales volume
- United States Carbon Fiber Reinforced Polymers in 3D Printing Market revenue size and demand by country
- Europe Carbon Fiber Reinforced Polymers in 3D Printing Market revenue size and demand by country
- Asia Pacific Carbon Fiber Reinforced Polymers in 3D Printing Market revenue size and demand by country
- Middle East & Africa Carbon Fiber Reinforced Polymers in 3D Printing Market revenue size and demand by country
- Latin America Carbon Fiber Reinforced Polymers in 3D Printing Market revenue size and demand by
- Import-export scenario – United States, Europe, APAC, Latin America, Middle East & Africa
- Average product price – United States, Europe, APAC, Latin America, Middle East & Africa
- Market player analysis, competitive scenario, market share analysis
- Business opportunity analysis
Key questions answered in the Global Carbon Fiber Reinforced Polymers in 3D Printing Market Analysis Report:
- What is the market size for Carbon Fiber Reinforced Polymers in 3D Printing in United States, Europe, APAC, Middle East & Africa, Latin America?
- What is the yearly sales volume of Carbon Fiber Reinforced Polymers in 3D Printing and how is the demand rising?
- Who are the top market players by market share, in each product segment?
- Which is the fastest growing business/ product segment?
- What should be the business strategies and Go to Market strategies?
The report covers Carbon Fiber Reinforced Polymers in 3D Printing Market revenue, Production, Sales volume, by regions, (further split into countries):
- Asia Pacific (China, Japan, South Korea, India, Indonesia, Vietnam, Rest of APAC)
- Europe (UK, Germany, France, Italy, Spain, Benelux, Poland, Rest of Europe)
- North America (United States, Canada, Mexico)
- Latin America (Brazil, Argentina, Rest of Latin America)
- Middle East & Africa
Table of Contents:
Carbon Fiber Reinforced Polymers in 3D Printing Market
- Introduction to Carbon Fiber Reinforced Polymers (CFRPs) in 3D Printing
- Overview of CFRPs and Their Significance in 3D Printing
- Evolution of Carbon Fiber Technology in Additive Manufacturing
- Composition and Properties of Carbon Fiber Reinforced Polymers
- Key Materials Used in CFRPs
- Mechanical Properties: Strength, Stiffness, and Durability
- Thermal and Electrical Conductivity Benefits
- Types of Carbon Fiber Reinforced Polymers for 3D Printing
- Unidirectional vs. Bidirectional Reinforcement
- Hybrid Composites: CFRP with Other Polymers
- Specialty CFRPs for Specific 3D Printing Applications
- Manufacturing Processes of CFRP Filaments for 3D Printing
- Extrusion and Filament Production Techniques
- Challenges in Ensuring Material Consistency and Quality
- Innovations in CFRP Filament Production
- Advantages of Carbon Fiber Reinforced Polymers in 3D Printing
- Enhanced Structural Performance and Lightweight Characteristics
- Corrosion Resistance and Impact Strength
- Application Versatility in Multiple Industries
- Applications of CFRP in 3D Printing
- Aerospace, Automotive, and Defense Industries
- Prototyping, Tooling, and End-Use Parts
- Medical, Sports, and Consumer Goods
- CFRP 3D Printing in the Automotive Industry
- Lightweight Solutions for Vehicle Parts
- Cost Efficiency and Performance in Automotive Manufacturing
- Trends in CFRP Applications for Electric Vehicles
- Carbon Fiber Reinforced Polymers for Aerospace and Defense Applications
- High-Performance Parts for Aircraft and Drones
- Structural Integrity and Safety Standards
- The Role of CFRP in Reducing Aircraft Weight
- CFRP 3D Printing in Medical Devices and Prosthetics
- Customization and Precision in Healthcare Solutions
- Biocompatibility Considerations
- Future Innovations in Medical Applications of CFRPs
- Emerging Trends in Carbon Fiber Reinforced Polymers for 3D Printing
- Advancements in Material Formulation and Technology
- Integration of Smart Materials and Sensors in CFRPs
- Trends in Sustainability and Eco-friendly CFRPs
- Challenges in Using CFRP for 3D Printing
- Material Costs and Availability
- Processing and Print Speed Limitations
- Difficulty in Achieving Consistent Print Quality
- Market Size and Growth Projections of CFRP in 3D Printing
- Global Market Trends and Demand Forecasts
- Factors Driving Growth in CFRP 3D Printing Applications
- Key Market Segments and Regional Insights
- Cost Analysis of Carbon Fiber Reinforced Polymers in 3D Printing
- Price Comparisons: CFRP vs. Other 3D Printing Materials
- Cost Implications for Small vs. Large Scale Manufacturers
- Economic Impact on End-Use Industries
- The Role of CFRP in Industrial 3D Printing for High-Performance Parts
- Industrial Applications for Custom Manufacturing and Tooling
- Functional Part Production: Combining Speed with Durability
- Automation and Digital Fabrication with CFRP
- Sustainability and Environmental Impact of CFRPs in 3D Printing
- Environmental Benefits of Using Carbon Fiber in 3D Printing
- Life Cycle Assessment of CFRP Products
- Recycling Challenges and Solutions for CFRPs in 3D Printing
- Comparison of Carbon Fiber Reinforced Polymers with Other Reinforced Materials
- CFRPs vs. Glass Fiber Reinforced Polymers (GFRPs)
- Cost vs. Performance in Material Selection
- Application Suitability Across Different Industries
- Technological Innovations in CFRP 3D Printing
- Advances in High-Speed 3D Printing for Carbon Fiber Filaments
- Multi-material Printing and Hybrid Approaches
- Development of Automated and Robotic 3D Printing Solutions
- Future Outlook for CFRP Materials in 3D Printing
- Predictions for Market Evolution and Technological Breakthroughs
- Potential for Wider Adoption Across New Industries
- Challenges in Scaling Production and Meeting Demand
- Regulatory Landscape for CFRP Materials in 3D Printing
- Standards and Certification for CFRP Materials in Different Sectors
- Safety Regulations in Aerospace, Automotive, and Medical Uses
- Global Compliance and Testing Guidelines for CFRP Products
- Key Players and Manufacturers in the CFRP 3D Printing Market
- Leading Companies in CFRP Filament Production
- Market Share and Competitive Strategies
- Collaboration and Partnership Models in CFRP Development
- Research and Development in Carbon Fiber Reinforced Polymers
- Ongoing Research on Enhancing CFRP Performance
- Novel Materials and Hybrid Approaches for Advanced Applications
- Collaborative R&D Projects with Universities and Institutions
- Education and Training for CFRP 3D Printing Technologies
- Skill Development for Engineers and Designers
- Educational Programs and Certifications in CFRP Technologies
- Workshops, Conferences, and Seminars on CFRP Innovations
- Carbon Fiber Reinforced Polymers in 3D Printing: Consumer vs. Industrial Applications
- Demands and Expectations for Consumer Products
- Industrial Applications: Quality, Precision, and Production Volume
- Case Studies of Leading Applications in Both Sectors
- Impact of CFRP 3D Printing on Supply Chains and Logistics
- Shortening Lead Times and Reducing Waste in Manufacturing
- On-demand Production and Customization in Logistics
- The Future of CFRP-Based On-Demand Manufacturing Systems
- CFRP 3D Printing in Prototyping and Design
- How CFRPs Enhance Rapid Prototyping for Product Development
- Applications in Product Testing, Simulation, and Testing Models
- Accelerating Product Development and Reducing Time-to-Market
- Consumer Preferences and Market Demand for CFRP 3D Printed Products
- Understanding Consumer Needs for Lightweight and High-Strength Products
- The Growing Popularity of CFRP in Customization and Personalized Products
- Marketing Strategies for CFRP-Based Products in the Consumer Market
- Conclusion: The Future of Carbon Fiber Reinforced Polymers in 3D Printing
- Summary of Key Trends, Benefits, and Market Insights
- Long-term Prospects and Future Technological Developments
- Concluding Thoughts on the Impact of CFRPs on 3D Printing Industries
“Every Organization is different and so are their requirements”- Datavagyanik
Companies We Work With
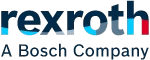
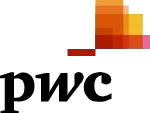
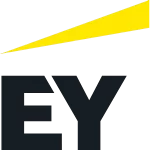
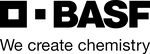
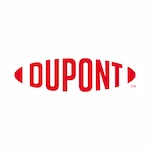

Do You Want To Boost Your Business?
drop us a line and keep in touch
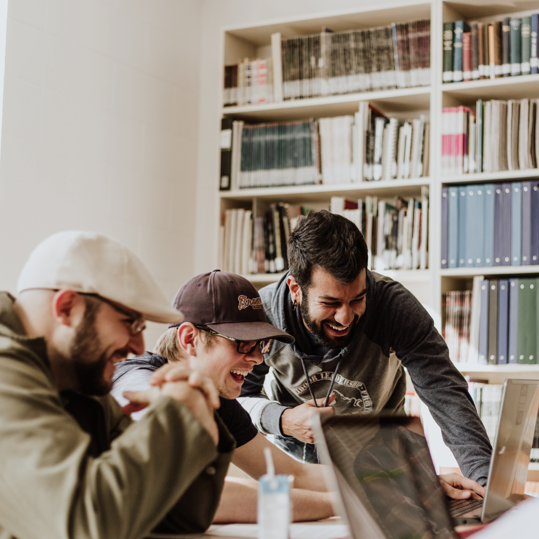