Coating Thickness Testing System market Market Size, Production, Sales, Average Product Price, Market Share, Import vs Export
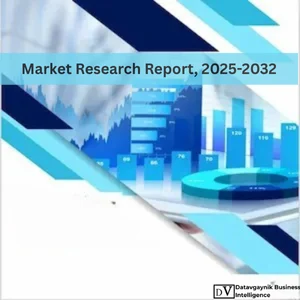
- Published 2025
- No of Pages: 120+
- 20% Customization available
Expanding Quality Demands Powering the Coating Thickness Testing System Market
The Coating Thickness Testing System Market is experiencing a structural transformation, driven by escalating demands for precision, regulatory compliance, and performance validation across core industries. The shift from conventional to high-performance coatings is not merely an industry evolution—it is a response to intensifying global quality mandates. For instance, in automotive manufacturing, over 90 million vehicles were produced globally in 2023, with a significant portion requiring multi-layer coatings for corrosion protection, aesthetics, and thermal insulation. Coating thickness testing systems ensure uniform layer deposition, which directly impacts vehicle longevity and brand reputation.
Similarly, in aerospace, each square meter of aircraft surface demands meticulously applied coatings that can withstand extreme environmental and mechanical stress. The precision coating market for aerospace is projected to grow at over 6.2% CAGR through 2030, directly elevating the demand for high-end coating thickness testing equipment. These trends underscore a critical paradigm: industries no longer view coating control as optional—it is foundational.
Coating Thickness Testing System Market Anchored by Advancing Coating Technologies
As coating materials evolve, so must the technologies that measure them. The Coating Thickness Testing System Market is increasingly shaped by the emergence of advanced coatings—such as nanocoatings, anti-microbial coatings, and eco-friendly formulations. For example, nanocoatings used in electronics, medical devices, and optics require micron-level accuracy in measurement. This level of precision is only possible with next-generation, non-destructive testing systems integrated with digital imaging and AI analytics.
Thermal barrier coatings, which are now widely used in turbine blades and high-temperature machinery, also demand accurate layer thickness control to ensure performance under intense heat. Their usage is growing at over 7% annually in energy and aerospace applications. As a result, testing systems that can non-invasively assess multi-layer and composite coatings are becoming indispensable.
Coating Thickness Testing System Market Driven by Regulatory Compliance and Industry Standards
One of the strongest pillars supporting the Coating Thickness Testing System Market is the proliferation of stringent global regulations across sectors such as infrastructure, marine, defense, and oil & gas. For instance, ISO 2178 and ASTM D7091 standards specify procedures and tolerances for coating thickness measurements, making compliance a non-negotiable factor for procurement and project execution.
Regulatory enforcement in oil & gas alone has led to over 35% year-on-year increase in non-destructive testing equipment adoption, particularly in offshore and pipeline segments. In infrastructure, coatings applied to steel bridges must adhere to mandated thickness levels to pass federal inspections. Failure leads not only to rework but to multi-million-dollar liabilities. This regulatory-driven precision culture is embedding coating thickness testing systems deeper into standard operating procedures across regions.
Rise of Non-Destructive Testing (NDT) Technologies Catalyzing Coating Thickness Testing System Market
The surge in non-destructive testing solutions is transforming how industries validate material integrity and coating effectiveness. The Coating Thickness Testing System Market is witnessing a strong shift toward portable, AI-integrated NDT systems that reduce downtime and increase operational efficiency. Ultrasonic and eddy current-based testers, for instance, are now the backbone of pipeline and aerospace inspections.
Between 2022 and 2024, portable NDT device shipments grew by more than 18%, reflecting a major move away from legacy lab-based systems. Moreover, AI-enabled testers that deliver real-time analytics and automatic report generation have increased adoption in manufacturing units aiming for zero-defect production lines. In automotive plants, integration of real-time thickness monitoring into robotic arms has cut quality control time by up to 30%.
Infrastructure Boom Fueling Coating Thickness Testing System Market
The global infrastructure boom is providing robust momentum to the Coating Thickness Testing System Market. With trillions being poured into urbanization, highways, smart cities, and high-speed rail, the need for protective coatings—and accurate measurement thereof—is more vital than ever. For instance, more than 60% of new infrastructure projects in Asia involve steel components exposed to corrosion risks. Coating thickness testing systems ensure the integrity and compliance of these applications, especially in regions prone to extreme weather.
Large-scale bridge refurbishments in North America and mega port developments in the Middle East have also elevated the demand for rugged, high-performance coating measurement devices. These systems are no longer limited to QA labs—they are now essential field tools used in real-time inspections, often linked to cloud-based project documentation systems.
Coating Thickness Testing System Market Size Surging with Automotive and Aerospace Expansion
The Coating Thickness Testing System Market Size has expanded notably, with the automotive and aerospace sectors representing over 40% of global demand. In electric vehicles alone, the number of critical coating points has increased by 25% compared to internal combustion engine models. This includes battery casing, connectors, and motor housing—all requiring high-precision coating thickness validation.
In aerospace, new aircraft production is projected to exceed 40,000 units over the next two decades. Each aircraft requires hundreds of coating applications—from anti-corrosion layers on fuselage components to thermal coatings on engine nozzles. Precision in these areas not only extends lifecycle performance but directly influences airworthiness certification. Consequently, the aerospace coating testing segment within the overall market is expected to see a CAGR above 6.8% through 2030.
Industrial Digitization and Smart Manufacturing Enhancing Coating Thickness Testing System Market Potential
The global shift toward Industry 4.0 is unlocking new growth pathways for the Coating Thickness Testing System Market. Manufacturing units are integrating smart coating thickness testers into their automated assembly lines. These devices communicate with production management systems, enabling real-time decisions, process corrections, and traceability.
For example, a leading electronics manufacturer implemented cloud-connected ultrasonic testing systems across its PCB production lines, resulting in a 20% improvement in yield and a 12% drop in coating-related rework. Such implementations are now becoming standard, especially in regions like South Korea, Germany, and the U.S., where digital twin technologies and predictive maintenance are increasingly mainstream.
Corrosion Prevention Awareness Bolstering Coating Thickness Testing System Market
Corrosion-related damage costs industries over $2.5 trillion globally each year, according to industry estimates. As a result, coating applications have become more aggressive, and so has the necessity for precise validation. The Coating Thickness Testing System Market has grown in direct proportion to the heightened awareness around corrosion control, particularly in oil & gas, maritime, and energy sectors.
For example, in offshore drilling, components are often exposed to saltwater environments, necessitating coatings that not only protect but also meet international durability standards. Here, testing systems that can operate underwater or in harsh environments are in high demand. In pipeline maintenance, thickness testing systems help predict coating degradation patterns, enabling preventive interventions that save millions in unplanned repairs.
Global Supply Chains Requiring Uniform Coating Standards Across Regions
With supply chains increasingly global, maintaining consistent coating quality across geographies has become non-negotiable. The Coating Thickness Testing System Market is vital in enabling this standardization. Whether a component is produced in Vietnam or Germany, it must meet identical coating quality requirements before integration into a final product.
Multinational OEMs now mandate that suppliers use approved thickness testing systems calibrated to specific tolerances. For instance, electronics producers require anodized aluminum coatings to meet exact micron-level specifications to ensure fitment and insulation integrity. The push for uniformity is driving demand not only for testing systems but also for standardized training and certification programs globally.
“Track Country-wise Coating Thickness Testing System Production and Demand through our Coating Thickness Testing System Production Database”
-
-
- Coating Thickness Testing System production database for 30+ countries worldwide
- Coating Thickness Testing System Powder sales volume for 31+ countries
- Country-wise Coating Thickness Testing System production capacity and production plant mapping, production capacity utilization for 30+ manufacturers
- Coating Thickness Testing System production plants and production plant capacity analysis for top manufacturers
-
North America Leads Global Precision Adoption in the Coating Thickness Testing System Market
The Coating Thickness Testing System Market in North America is growing at a consistent pace, led by strong end-user industries such as automotive, aerospace, and oil & gas. The United States, with its large-scale vehicle manufacturing hubs and aerospace assembly lines, accounts for the majority share of the regional market. For instance, over 10 million vehicles produced annually in the U.S. require anti-corrosion and aesthetic coatings, where layer uniformity is critical. This demand directly translates into a strong uptake of advanced testing systems.
In aerospace, high-performance coatings are not optional—they are mission-critical. Each aircraft has multiple coatings applied for thermal resistance, radar absorption, and corrosion protection. As new aircraft programs expand, the need for ultra-precise thickness validation is surging. Moreover, the oil & gas industry, particularly in Texas and the Gulf Coast, requires rugged testing systems capable of withstanding extreme field conditions. These applications are strengthening market penetration and driving innovation in portable, non-destructive testing equipment.
Europe’s Industrial Sophistication Driving Coating Thickness Testing System Market Maturity
Europe’s highly developed industrial infrastructure has positioned it as one of the most advanced adopters in the Coating Thickness Testing System Market. Germany, France, and the United Kingdom lead in deployment, with heavy usage across automotive manufacturing, aircraft assembly, marine infrastructure, and industrial automation.
Germany, for example, houses several global automotive brands that produce high-end vehicles where visual finish, coating durability, and corrosion resistance are non-negotiable. Every production line in these factories is equipped with digital coating thickness testers that verify each layer in real time, often with AI-enabled feedback loops that auto-adjust application systems. In France, aerospace and marine sectors dominate demand. Aircraft wings, fuselage components, and naval equipment must meet strict EU performance guidelines, pushing adoption of multi-technology testing systems including ultrasonic and eddy current models.
Sustainability mandates in the region are also influencing procurement behavior. Manufacturers are shifting to low-VOC and bio-based coatings, which behave differently under application. This shift has led to increased investment in new testing technologies that can accurately assess unconventional coating formulations, further expanding the Coating Thickness Testing System Market in the region.
Asia Pacific Emerges as the Growth Engine for the Coating Thickness Testing System Market
In Asia Pacific, rapid industrialization and production scale-ups are accelerating the Coating Thickness Testing System Market. China, Japan, India, and South Korea are the dominant players, supported by expanding automotive, electronics, shipbuilding, and construction sectors. China, for instance, produces more vehicles and ships annually than any other country. These industries require coating systems for corrosion resistance and structural longevity, and the demand for testing equipment has risen proportionally.
Japan and South Korea, with their precision-oriented electronics and semiconductor sectors, emphasize micron-level coating thickness measurement. A semiconductor wafer, for example, may require multiple nanocoatings, each with a tight thickness tolerance. In these contexts, high-frequency eddy current testers and beta backscatter devices are the preferred technologies. Meanwhile, India’s infrastructure boom, driven by public and private investments in smart cities and railways, is creating sustained demand for field-deployable coating thickness testing systems.
As environmental regulations tighten and manufacturing sophistication rises across Asia, investment in accurate, fast, and portable thickness testing devices is surging—placing the region at the center of future growth in the Coating Thickness Testing System Market.
Middle East and Africa Strengthen Demand for Protective Testing in Harsh Environments
The Coating Thickness Testing System Market in the Middle East and Africa is defined by its dependence on the oil & gas and infrastructure sectors. Offshore platforms, refineries, and pipelines are exposed to some of the world’s harshest environments. Here, protective coatings are more than just preventive—they are critical for operational safety. As infrastructure ages and corrosion risks increase, demand for robust and portable testing systems has risen sharply.
For instance, countries like Saudi Arabia and the UAE are investing in large-scale construction and industrial diversification projects. High-value coatings are applied to steel structures, bridges, tanks, and marine equipment. In these applications, non-destructive testing systems are deployed regularly for both quality control and maintenance cycles. Africa’s mining and transport infrastructure, meanwhile, is driving growth in portable ultrasonic testers used for verifying coating thickness on equipment and rail assets.
Latin America Experiencing Steady Uptake in the Coating Thickness Testing System Market
Latin America’s Coating Thickness Testing System Market is gaining ground, driven by growing automotive production in Mexico, oil & gas developments in Brazil, and expanding construction activities across the continent. Automotive OEMs in Mexico are installing advanced coating lines to serve export-focused manufacturing. These lines increasingly require in-line coating thickness validation to ensure compliance with international standards.
Brazil’s offshore oil fields, including pre-salt layers, are highly sensitive to corrosion and environmental stress, resulting in increased deployment of thickness testing systems for safety assurance. The market here is also influenced by import dependence—advanced testing systems are largely sourced from North America and Europe, which affects both availability and pricing.
As industrial automation begins to take hold in the region, and with governments focusing on durability standards for public infrastructure, demand for advanced yet cost-effective coating thickness testing systems is expected to accelerate.
Coating Thickness Testing System Market Segmentation Reflects Evolving Industry Needs
The Coating Thickness Testing System Market is segmented based on technology, application, and end-use industry. Each segment reflects the unique needs and priorities of the industries they serve.
Magnetic induction systems dominate segments where steel is the primary substrate, such as automotive and construction. These are preferred for their accuracy and speed in measuring non-magnetic coatings on ferrous metals. Eddy current systems are growing in importance due to the rise in aluminum and other non-ferrous substrates, especially in aerospace and consumer electronics.
Ultrasonic systems, capable of measuring thick and multi-layer coatings, are increasingly adopted in oil & gas, heavy equipment, and marine applications. Beta backscatter systems, which excel at measuring very thin coatings, are becoming the standard in semiconductor and electronics manufacturing.
From an end-use perspective, automotive and aerospace collectively contribute to nearly 45% of global demand. Electronics, marine, construction, and oil & gas make up the remainder, with each showing double-digit growth in specific regions. As the range and complexity of coatings expand, the segmentation of testing systems continues to evolve accordingly.
Coating Thickness Testing System Price Trend Shaped by Innovation and Regional Dynamics
The Coating Thickness Testing System Price Trend is influenced by multiple factors, including technology complexity, region, application, and supply chain dynamics. Portable magnetic and eddy current testers typically start around the mid-range price bracket, while high-end ultrasonic and beta backscatter systems can command premium pricing due to their precision and real-time capabilities.
In North America and Europe, prices remain higher due to labor costs, software integration, and regulatory certifications. For instance, digital systems integrated with cloud monitoring and AI diagnostics can cost 30–40% more than traditional models. However, the ROI is justified in high-throughput environments where rework reduction and predictive maintenance offset upfront investment.
In Asia Pacific, pricing is more competitive due to localized production, lower manufacturing costs, and growing domestic brands. This has put pressure on global manufacturers to localize or adapt models to meet both price and performance expectations.
The Coating Thickness Testing System Price Trend is also impacted by material shortages and semiconductor availability, especially for digital models that depend on advanced sensors. While raw material inflation has slightly pushed prices up in recent years, economies of scale and modular design are helping stabilize pricing in volume-based markets like China and India.
Coating Thickness Testing System Price Reflects Value Across Use Cases
The Coating Thickness Testing System Price varies not just by technology but also by user expectations. Entry-level models for basic paint thickness measurement in automotive body shops are available at affordable rates, while advanced models designed for multi-layer, sub-micron precision in electronics fabrication are significantly more expensive.
This price stratification allows for broad market participation—from SMEs in emerging markets to multinational OEMs with strict QA protocols. Additionally, leasing models, SaaS-based diagnostics, and equipment-as-a-service offerings are reshaping how buyers approach capital investment, especially in regions where upfront costs are a barrier.
As innovation continues and production technology advances, the Coating Thickness Testing System Price Trend is expected to balance between premium performance tiers and mass-market accessibility.
“Coating Thickness Testing System Manufacturing Database, Coating Thickness Testing System Manufacturing Capacity”
-
-
- Coating Thickness Testing System top manufacturers market share for 30+ manufacturers
- Top 9 manufacturers and top 19 manufacturers of Coating Thickness Testing System in North America, Europe, Asia Pacific
- Production plant capacity by manufacturers and Coating Thickness Testing System production data for 30+ market players
- Coating Thickness Testing System production dashboard, Coating Thickness Testing System production data in excel format
-
Leading Manufacturers in the Coating Thickness Testing System Market
The Coating Thickness Testing System Market is characterized by a diverse array of manufacturers, each contributing unique technologies and product lines to meet the evolving demands of various industries.
Helmut Fischer GmbH stands out as a pioneer in the field, offering a comprehensive range of instruments such as the DUALSCOPE FMP100, which combines eddy current and magnetic induction methods for versatile applications. Their focus on precision and innovation has solidified their position in the market.
Elcometer Limited is renowned for its Elcometer 456 series, which provides accurate and reliable measurements for both ferrous and non-ferrous substrates. Their commitment to user-friendly interfaces and robust design caters to sectors like automotive and marine industries.
DeFelsko Corporation offers the PosiTector 6000 series, known for its durability and adaptability in various environments. Their emphasis on digital integration and data management aligns with the industry’s shift towards smart manufacturing.
Mitutoyo Corporation, a global leader in precision measuring instruments, provides coating thickness gauges that are integral in quality control processes across manufacturing sectors. Their products are synonymous with accuracy and reliability.
ElektroPhysik Dr. Steingroever GmbH & Co. KG specializes in high-precision instruments, including the MiniTest series, which are widely used in industrial applications requiring meticulous coating measurements.
Keyence Corporation integrates advanced technologies into their measurement systems, offering solutions that enhance production efficiency and quality assurance in electronics and automotive industries.
Olympus Corporation brings its expertise in optical and digital technologies to the market, providing instruments that offer high-resolution measurements essential in aerospace and medical device manufacturing.
PCE Instruments delivers a broad spectrum of testing equipment, including coating thickness gauges that serve various industries, from construction to electronics, emphasizing versatility and ease of use.
Anton Paar GmbH offers specialized instruments for measuring coating thickness, particularly in research and development settings, where precision and repeatability are paramount.
Cygnus Instruments Ltd. focuses on ultrasonic measurement technologies, providing solutions that are crucial in industries like shipbuilding and oil & gas, where non-destructive testing is essential.
Market Share Distribution Among Manufacturers
The Coating Thickness Testing System Market exhibits a competitive landscape with several key players holding significant shares. Helmut Fischer GmbH and Elcometer Limited collectively account for a substantial portion of the market, driven by their extensive product portfolios and global reach.
DeFelsko Corporation maintains a strong presence, particularly in North America, attributed to their innovative solutions and customer-centric approach. Mitutoyo Corporation’s global footprint and reputation for precision contribute to its notable market share.
Emerging players like ElektroPhysik and Keyence are gaining traction by introducing cutting-edge technologies that cater to the evolving needs of industries emphasizing automation and data integration.
Recent Developments and Industry Trends
The Coating Thickness Testing System Market is witnessing several notable developments:
- Integration of AI and IoT: Manufacturers are incorporating artificial intelligence and Internet of Things capabilities into their instruments, enabling predictive maintenance and real-time data analysis, which enhances operational efficiency.
- Focus on Sustainability: There’s a growing emphasis on developing eco-friendly coatings and corresponding testing systems that align with environmental regulations and sustainability goals.
- Expansion in Emerging Markets: Companies are increasingly targeting emerging economies, recognizing the growth potential in regions undergoing rapid industrialization and infrastructure development.
- Advancements in Non-Destructive Testing (NDT): Innovations in NDT technologies are allowing for more accurate and efficient coating thickness measurements, reducing downtime and improving safety in critical applications.
- Customization and Modular Designs: Manufacturers are offering customizable solutions and modular designs to cater to specific industry requirements, providing flexibility and scalability.
These developments indicate a dynamic market landscape where technological innovation and strategic expansion are key drivers of growth and competitiveness.
“Coating Thickness Testing System Production Data and Coating Thickness Testing System Production Trend, Coating Thickness Testing System Production Database and forecast”
-
-
- Coating Thickness Testing System production database for historical years, 10 years historical data
- Coating Thickness Testing System production data and forecast for next 9 years
-
Market Scenario, Demand vs Supply, Average Product Price, Import vs Export, till 2035
- Global Coating Thickness Testing System market Market revenue and demand by region
- Global Coating Thickness Testing System market Market production and sales volume
- United States Coating Thickness Testing System market Market revenue size and demand by country
- Europe Coating Thickness Testing System market Market revenue size and demand by country
- Asia Pacific Coating Thickness Testing System market Market revenue size and demand by country
- Middle East & Africa Coating Thickness Testing System market Market revenue size and demand by country
- Latin America Coating Thickness Testing System market Market revenue size and demand by
- Import-export scenario – United States, Europe, APAC, Latin America, Middle East & Africa
- Average product price – United States, Europe, APAC, Latin America, Middle East & Africa
- Market player analysis, competitive scenario, market share analysis
- Business opportunity analysis
Key questions answered in the Global Coating Thickness Testing System market Market Analysis Report:
- What is the market size for Coating Thickness Testing System market in United States, Europe, APAC, Middle East & Africa, Latin America?
- What is the yearly sales volume of Coating Thickness Testing System market and how is the demand rising?
- Who are the top market players by market share, in each product segment?
- Which is the fastest growing business/ product segment?
- What should be the business strategies and Go to Market strategies?
The report covers Coating Thickness Testing System market Market revenue, Production, Sales volume, by regions, (further split into countries):
- Asia Pacific (China, Japan, South Korea, India, Indonesia, Vietnam, Rest of APAC)
- Europe (UK, Germany, France, Italy, Spain, Benelux, Poland, Rest of Europe)
- North America (United States, Canada, Mexico)
- Latin America (Brazil, Argentina, Rest of Latin America)
- Middle East & Africa
Table of Contents:
Coating Thickness Testing System Market report:
- Executive Summary
- Introduction to Coating Thickness Testing Systems
- 2.1 Definition and Overview
- 2.2 Importance in Industrial Applications
- 2.3 Evolution of Coating Thickness Measurement Technologies
- Principles of Coating Thickness Measurement
- 3.1 Magnetic Induction Method
- 3.2 Eddy Current Testing
- 3.3 Ultrasonic Thickness Measurement
- 3.4 X-ray Fluorescence (XRF) Techniques
- 3.5 Emerging Non-Destructive Testing Methods
- Global Coating Thickness Testing System Market Overview
- 4.1 Market Definition and Scope
- 4.2 Key Market Trends and Developments
- 4.3 Market Lifecycle Analysis
- Market Dynamics
- 5.1 Growth Drivers
- 5.2 Challenges and Market Restraints
- 5.3 Opportunities in Advanced Manufacturing Sectors
- 5.4 Impact of Technological Advancements on Market Growth
- Technological Innovations in Coating Thickness Testing Systems
- 6.1 Integration with IoT and Smart Sensors
- 6.2 Automation and AI in Coating Measurement
- 6.3 Portable and Handheld Device Innovations
- Regulatory Landscape and Industry Standards
- 7.1 Compliance Requirements in Key Industries
- 7.2 Impact of Quality Assurance Standards
- Global Market Size and Forecast (2020–2035)
- 8.1 Historical Market Performance
- 8.2 Forecast Assumptions and Methodology
- 8.3 Revenue and Volume Projections
- Market Segmentation Analysis
- 9.1 By Technology (Magnetic, Eddy Current, Ultrasonic, XRF, Others)
- 9.2 By Product Type (Portable Devices, Desktop Systems, Integrated Systems)
- 9.3 By Application (Automotive, Aerospace, Marine, Electronics, Construction, Oil & Gas, Others)
- 9.4 By End-Use Industry
- Regional Market Analysis
- 10.1 North America: Market Trends and Growth Prospects
- 10.2 Europe: Regulatory Dynamics and Industry Developments
- 10.3 Asia Pacific: Growing Industrial Demand and Market Opportunities
- 10.4 Latin America: Market Landscape and Investment Trends
- 10.5 Middle East & Africa: Demand Drivers and Market Insights
- Competitive Landscape
- 11.1 Overview of Leading Market Players
- 11.2 Market Share Analysis
- 11.3 Competitive Strategies and Key Developments
- Profiles of Key Companies in the Coating Thickness Testing System Market
- 12.1 Company Overview
- 12.2 Product Portfolio and Innovations
- 12.3 Strategic Initiatives and Partnerships
- Strategic Developments: Mergers, Acquisitions, and Collaborations
- Supply Chain Analysis and Value Chain Assessment
- Raw Material Sourcing and Procurement Trends
- Manufacturing Process Overview and Efficiency Analysis
- Cost Structure and Pricing Trends
- Import-Export Analysis and Global Trade Dynamics
- Demand and Consumption Analysis by Industry
- Application Insights: Key Industry Use Cases
- 20.1 Automotive Industry
- 20.2 Aerospace and Defense Sector
- 20.3 Oil & Gas and Marine Applications
- 20.4 Electronics and Semiconductor Industry
- 20.5 Construction and Infrastructure
- Impact of Industry 4.0 on Coating Thickness Testing Systems
- Risk Analysis and Market Entry Barriers
- Investment Opportunities in Emerging Markets
- Case Studies of Innovative Coating Thickness Measurement Applications
- Impact of Global Events (e.g., COVID-19) on Market Dynamics
- Future Market Trends and Strategic Growth Outlook (2020–2035)
- Key Takeaways and Strategic Recommendations for Stakeholders
- Appendix
- 28.1 Glossary of Terms
- 28.2 Research Methodology
- 28.3 List of Figures and Tables
Other recently published reports:
“Every Organization is different and so are their requirements”- Datavagyanik
Companies We Work With
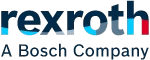
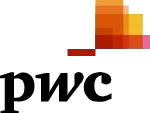
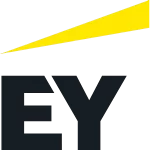
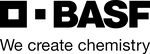
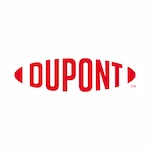

Do You Want To Boost Your Business?
drop us a line and keep in touch
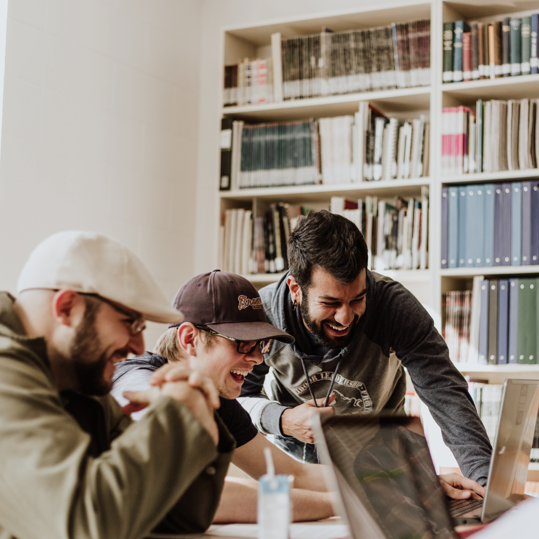