Cold Spray Additive Manufacturing Market Size, Production, Sales, Average Product Price, Market Share, Import vs Export
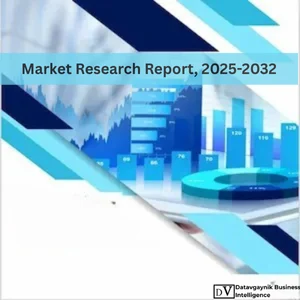
- Published 2025
- No of Pages: 120+
- 20% Customization available
Cold Spray Additive Manufacturing Market: Rising Demand Across Industries
The Cold Spray Additive Manufacturing Market is witnessing remarkable growth, driven by a combination of advanced technological innovations, diverse applications, and the rising demand for cost-effective, efficient, and sustainable manufacturing solutions. From aerospace to automotive, industries are increasingly adopting Cold Spray Additive Manufacturing (CSAM) as it offers compelling advantages over traditional manufacturing techniques. This shift is being fueled by the need to improve the performance, longevity, and sustainability of high-value components. As industries transition towards more advanced manufacturing processes, CSAM has emerged as a key enabler of this transformation, and its role in modern manufacturing ecosystems cannot be overstated.
Expanding Applications in Aerospace and Defense
The aerospace and defense sectors are among the most prominent adopters of the Cold Spray Additive Manufacturing Market, driving a substantial portion of its growth. The ability of CSAM to repair high-value, temperature-sensitive parts without inducing thermal stress is a game-changer for the aerospace industry. Cold spray technology is particularly effective in the restoration of critical components like turbine blades, engine parts, and landing gear, where precision and material integrity are paramount.
For instance, the U.S. Department of Defense has increasingly turned to CSAM for maintaining military aircraft, ships, and vehicles. This application ensures minimal downtime, enhances the lifespan of parts, and reduces the need for costly replacements, making it an essential technology in the defense sector. Furthermore, as military equipment continues to advance, the need for highly durable and lightweight components is pushing the demand for Cold Spray Additive Manufacturing solutions to unprecedented levels.
Growing Demand for Lightweight Materials in Automotive Manufacturing
The automotive sector is another area where the Cold Spray Additive Manufacturing Market is seeing significant traction. As the industry shifts towards lightweight materials to improve fuel efficiency and reduce carbon emissions, CSAM is playing an essential role. For example, automotive manufacturers are increasingly using aluminum, titanium, and magnesium alloys to produce lightweight parts, such as engine blocks, transmission components, and chassis elements.
The ability to repair these high-value parts with minimal material waste is a key advantage offered by Cold Spray Additive Manufacturing. According to recent studies, the demand for lightweight materials in the automotive sector is expected to grow at a compound annual growth rate (CAGR) of 6.7% through 2030, making CSAM a critical solution for meeting the growing need for fuel-efficient, eco-friendly vehicles.
CSAM’s Contribution to Sustainable Manufacturing Practices
The Cold Spray Additive Manufacturing Market is also experiencing rapid growth due to the increasing emphasis on sustainable manufacturing practices. Traditional manufacturing techniques often generate significant material waste, which can drive up production costs and impact the environment. Cold spray technology, on the other hand, is known for its ability to deposit material with minimal waste, thereby supporting the growing demand for more eco-friendly production processes.
For example, CSAM uses a low-temperature approach that does not require the material to melt, significantly reducing energy consumption compared to conventional methods like welding or casting. As global industries strive to meet stringent sustainability targets, the adoption of CSAM is expected to rise. A 2024 study on global manufacturing trends suggests that over 45% of manufacturers are prioritizing sustainable production technologies, with Cold Spray Additive Manufacturing emerging as a frontrunner in this regard.
Revolutionizing Repair and Restoration Industries
Repair and restoration applications are key growth drivers within the Cold Spray Additive Manufacturing Market. The ability to repair high-value parts without the need for complete replacement provides manufacturers with significant cost savings, while also ensuring that critical components are restored to optimal performance. One of the primary benefits of CSAM in repair applications is its ability to restore parts like turbine blades, engine components, and aerospace structures with minimal material distortion.
The use of Cold Spray Additive Manufacturing also eliminates the need for costly and time-consuming traditional repair methods, such as machining or casting. The repair of high-value assets such as aerospace parts and industrial machinery is projected to reach a market value of $5.7 billion by 2027, with CSAM technology playing a crucial role in this growth. As a result, industries are rapidly adopting Cold Spray technology as a core part of their maintenance strategies.
Competitive Edge in Material Science and Process Optimization
The Cold Spray Additive Manufacturing Market is also benefiting from ongoing advancements in material science and process optimization. The range of materials that can be processed using CSAM has expanded significantly in recent years, thanks to continuous research and development efforts. Materials such as advanced alloys, composites, and even ceramics can now be deposited with high precision, expanding the applicability of Cold Spray technology in various high-tech industries, including electronics, energy, and medical devices.
In particular, CSAM’s low-temperature process makes it ideal for handling temperature-sensitive materials like polymers and certain alloys. Moreover, innovations in nozzle design, robotic automation, and process control are improving the scalability and efficiency of Cold Spray systems, further boosting their adoption across industries. The Cold Spray Additive Manufacturing Market is poised to grow significantly as manufacturers seek to integrate these innovations into their production lines.
Cold Spray Additive Manufacturing Market: A Solution for Hybrid Manufacturing
Hybrid manufacturing, which combines additive and subtractive manufacturing techniques, is another area where CSAM is making a significant impact. Cold spray technology can be integrated with traditional manufacturing methods, such as machining, to create complex, multi-material structures with improved properties. This hybrid approach offers manufacturers increased flexibility in their design and production processes, as well as the ability to reduce production time. Industries that are increasingly adopting hybrid manufacturing systems, such as aerospace, automotive, and energy, are finding Cold Spray Additive Manufacturing to be an indispensable tool.
In aerospace, for example, hybrid manufacturing enables the creation of lightweight, high-performance components that meet stringent regulatory standards while minimizing waste and energy consumption. As the demand for customized, high-performance parts continues to rise, the integration of Cold Spray Additive Manufacturing with traditional subtractive techniques will play a pivotal role in the evolution of modern manufacturing.
Increased Adoption in Emerging Markets and Industrial Applications
The growth of the Cold Spray Additive Manufacturing Market is not confined to developed economies; emerging markets are also beginning to experience a surge in demand. Countries in regions like Asia Pacific, Latin America, and the Middle East are increasingly adopting Cold Spray technology for various industrial applications, including energy production, infrastructure repair, and manufacturing.
For example, in China, CSAM is being used to enhance the efficiency of manufacturing processes in the automotive and aerospace sectors, while India is leveraging Cold Spray technology to repair critical components in the energy sector. As these regions continue to industrialize, the Cold Spray Additive Manufacturing Market is expected to see exponential growth, with market analysts projecting a 10% CAGR over the next decade. Furthermore, government support for advanced manufacturing technologies and investments in infrastructure development are expected to fuel the adoption of CSAM in these regions.
Impact of Geopolitical Factors on Cold Spray Adoption
Geopolitical factors and global supply chain disruptions have played an essential role in the increased adoption of Cold Spray Additive Manufacturing technology. As geopolitical tensions and trade disputes have affected global supply chains, many industries have turned to localized production methods, which can be more resilient and cost-effective. CSAM technology offers manufacturers the ability to produce high-quality components locally, reducing dependence on international supply chains.
This shift towards local manufacturing has been particularly evident in sectors like defense and aerospace, where geopolitical concerns and national security are major factors influencing production strategies. The ability of Cold Spray Additive Manufacturing to create localized, high-quality components without relying on foreign suppliers is positioning it as a critical technology in regions with vulnerable supply chains.
Conclusion: The Future of the Cold Spray Additive Manufacturing Market
The Cold Spray Additive Manufacturing Market is on the cusp of a significant transformation, with several key drivers propelling its growth. As industries across the globe seek cost-effective, sustainable, and efficient manufacturing solutions, the demand for Cold Spray technology will continue to rise.
The combination of its ability to repair high-value parts, work with a broad range of materials, and support hybrid manufacturing techniques positions Cold Spray Additive Manufacturing as a key player in the future of global manufacturing. Additionally, the ongoing advancements in material science and process optimization will ensure that CSAM remains at the forefront of innovation, enabling manufacturers to meet the evolving demands of various industries. With continued support from government initiatives and increasing adoption across emerging markets, the Cold Spray Additive Manufacturing Market is poised for long-term success, creating new opportunities for growth and innovation.
“Track Country-wise Cold Spray Additive Manufacturing Production and Demand through our Cold Spray Additive Manufacturing Production Database”
-
-
- Cold Spray Additive Manufacturing production database for 28+ countries worldwide
- Cold Spray Additive Manufacturing Powder sales volume for 32+ countries
- Country-wise Cold Spray Additive Manufacturing production capacity and production plant mapping, production capacity utilization for 28+ manufacturers
- Cold Spray Additive Manufacturing production plants and production plant capacity analysis for top manufacturers
-
Geographical Demand in the Cold Spray Additive Manufacturing Market
The Cold Spray Additive Manufacturing Market is experiencing significant geographic variations in demand, with key regions driving adoption across different industries. North America, Europe, and Asia Pacific are leading the way, each with distinct growth drivers. This demand is fueled by a variety of factors, including technological advancements, industry-specific requirements, and increasing investments in manufacturing infrastructure.
In North America, the demand for Cold Spray Additive Manufacturing is particularly strong in the aerospace, automotive, and defense sectors. The U.S. is a leader in the adoption of CSAM, driven by the country’s focus on military applications, including aircraft repair and restoration. The Department of Defense’s reliance on Cold Spray technology for the repair of high-value components such as turbine blades, engine parts, and structural elements has further accelerated the growth of the market. The aerospace sector in North America is growing at a CAGR of 7.5%, and Cold Spray Additive Manufacturing is becoming a vital tool for enhancing component durability and reducing operational costs.
Europe, on the other hand, has seen a substantial rise in Cold Spray Additive Manufacturing applications in countries like Germany, France, and the UK. The automotive and aerospace industries are particularly reliant on CSAM for producing lightweight, durable parts and for component repairs. As European manufacturers are under increasing pressure to meet sustainability goals, CSAM is proving to be a vital technology for reducing waste and lowering energy consumption. The demand for Cold Spray Additive Manufacturing in Europe has been growing at a rate of 6.3% annually, and its impact is expected to continue expanding as industries prioritize eco-friendly production methods.
Asia Pacific, especially China and India, is emerging as a powerhouse in the Cold Spray Additive Manufacturing Market. In China, Cold Spray technology is widely used in the aerospace and automotive industries, while India is increasingly adopting CSAM in energy infrastructure and industrial machinery sectors. The rapid industrialization of the region, paired with rising demand for renewable energy systems and advanced manufacturing technologies, is set to fuel a compounded growth rate of 8.2% in the Cold Spray Additive Manufacturing Market over the next five years.
Cold Spray Additive Manufacturing Market Production and Supply Chain Dynamics
The production and supply chain dynamics of the Cold Spray Additive Manufacturing Market are integral to understanding its growth trajectory. North America and Europe are at the forefront of producing Cold Spray systems, with leading manufacturers focusing on enhancing system performance, developing advanced material powders, and improving process automation. In North America, particularly the United States, companies such as Thermo Fischer Scientific and Stellite are among the key players in the production of Cold Spray systems, offering cutting-edge equipment for critical aerospace and defense applications.
In Europe, Germany is home to several prominent Cold Spray manufacturers, including Oerlikon and INEOS, which are playing a vital role in optimizing nozzle designs, refining material deposition techniques, and advancing Cold Spray technology. These developments have propelled the growth of the Cold Spray Additive Manufacturing Market, especially in industries like automotive and aerospace. Germany’s automotive sector, for instance, has experienced a surge in demand for lightweight materials, with the Cold Spray Additive Manufacturing Market expected to grow by 5.6% annually through 2030 due to this trend.
In the Asia Pacific region, China is rapidly scaling its production of Cold Spray systems, driven by the growing demand for advanced manufacturing technologies and a large-scale focus on industrial modernization. Companies in China are increasingly focusing on developing cost-effective Cold Spray systems that are suitable for a variety of applications in the aerospace, automotive, and energy sectors. With local production capabilities rising, China is expected to increase its Cold Spray equipment production by 12% year-on-year, establishing itself as a significant player in the global market.
Market Segmentation in the Cold Spray Additive Manufacturing Market
The Cold Spray Additive Manufacturing Market can be categorized based on material types, process types, applications, and end-user industries. Each segment plays a critical role in shaping the market dynamics, catering to a broad spectrum of industries with specific needs.
Material Type
Metals and metal alloys dominate the Cold Spray Additive Manufacturing Market, accounting for over 70% of market share. These materials, such as titanium, nickel-based alloys, and aluminum, are preferred for their excellent mechanical properties, corrosion resistance, and thermal conductivity. The aerospace and automotive industries are major consumers of metal-based Cold Spray technology, as it is used extensively for component repairs and the manufacturing of lightweight parts. For example, titanium alloys are used in aerospace components due to their strength and light weight, with Cold Spray technology being pivotal in their production and repair.
Process Type
The Cold Spray Additive Manufacturing Market is also segmented by process type, with high-pressure and low-pressure systems playing central roles. High-pressure Cold Spray systems, which operate at pressures above 30 bars, are primarily used for dense coatings and high-performance applications in aerospace and defense. The high-pressure Cold Spray Additive Manufacturing Market is projected to grow at a CAGR of 9.5%, driven by increased demand from industries requiring precise, durable coatings. On the other hand, low-pressure Cold Spray systems are more economical and suitable for applications in electronics and general machinery. As the demand for cost-effective solutions rises, the low-pressure segment is expected to grow at a CAGR of 7.2%.
End-User Industries
The end-user industry segment is another critical aspect of the Cold Spray Additive Manufacturing Market. Aerospace and defense, automotive, energy, and electronics sectors are the primary consumers of CSAM. In the aerospace sector, CSAM is used to repair high-value components like turbine blades, fuselage parts, and engines. The defense sector, particularly in the U.S. and Europe, is investing heavily in Cold Spray technology for the repair and maintenance of military equipment. The demand for CSAM in the energy sector, driven by the need to repair wind turbine blades and oil pipelines, is also growing rapidly, with the market expected to reach $1.2 billion by 2026.
Cold Spray Additive Manufacturing Price and Trend Analysis
Understanding the price trend of Cold Spray Additive Manufacturing technology is key to predicting its future trajectory. The price of Cold Spray systems and services can vary significantly depending on factors such as system complexity, material compatibility, and the specific industry application.
The Cold Spray Additive Manufacturing Price has been decreasing over the past few years, owing to technological advancements and increased competition in the market. The development of more efficient manufacturing processes and the ability to produce Cold Spray systems at scale have resulted in cost reductions, making the technology more accessible to smaller manufacturers. For instance, the price of high-pressure Cold Spray systems has decreased by approximately 10% over the last five years, a trend that is expected to continue as manufacturers further optimize production techniques.
In contrast, low-pressure Cold Spray systems remain more affordable, with prices seeing a decline of around 5% annually. These systems are often preferred by smaller enterprises and industries with less complex needs, such as general machinery and electronics. The Cold Spray Additive Manufacturing Price Trend shows that the market is shifting towards more affordable systems, creating significant growth opportunities in emerging markets like India and Southeast Asia.
The price trend is also influenced by the materials used in the Cold Spray process. Metal-based powders, especially titanium and nickel alloys, are more expensive than alternatives like aluminum or copper. However, as material science advances and new, cost-effective material powders are developed, the overall cost of Cold Spray technology is expected to decrease further. The Cold Spray Additive Manufacturing Price Trend indicates that the use of advanced alloys and composite materials will become more cost-effective, allowing broader adoption across industries like automotive and electronics.
The Role of Cold Spray Additive Manufacturing Price Trend in Market Expansion
The Cold Spray Additive Manufacturing Price Trend plays a pivotal role in determining the rate at which different regions and industries adopt this technology. In North America and Europe, where industries have the financial resources to invest in high-end, high-pressure systems, the price trend is less of a barrier to adoption. However, in emerging markets like China, India, and Southeast Asia, the affordability of Cold Spray technology is a critical factor for expanding the customer base.
As the Cold Spray Additive Manufacturing Price continues to decrease, its penetration in these regions is expected to increase significantly. In fact, industry experts predict a 20% increase in the adoption of Cold Spray technology across Asia Pacific over the next three years, driven by both the declining price trend and the growing industrial base in these regions. This trend is expected to result in the proliferation of Cold Spray systems in automotive and energy sectors, where cost-effectiveness is particularly important.
“Cold Spray Additive Manufacturing Manufacturing Database, Cold Spray Additive Manufacturing Manufacturing Capacity”
-
-
- Cold Spray Additive Manufacturing top manufacturers market share for 28+ manufacturers
- Top 8 manufacturers and top 18 manufacturers of Cold Spray Additive Manufacturing in North America, Europe, Asia Pacific
- Production plant capacity by manufacturers and Cold Spray Additive Manufacturing production data for 28+ market players
- Cold Spray Additive Manufacturing production dashboard, Cold Spray Additive Manufacturing production data in excel format
-
Top Manufacturers in the Cold Spray Additive Manufacturing Market
The Cold Spray Additive Manufacturing Market has witnessed the entry of several top players who are driving the adoption of this technology across industries. These manufacturers are not only leading in terms of production capabilities but are also setting trends by introducing innovative solutions that cater to the diverse needs of aerospace, automotive, energy, and other sectors.
1. Oerlikon
Oerlikon is one of the leaders in the Cold Spray Additive Manufacturing Market, offering a wide range of Cold Spray systems designed for high-precision applications. Their product line includes the Oerlikon Metco Cold Spray Systems, which are used extensively in aerospace, automotive, and energy sectors. Oerlikon’s systems are known for their advanced nozzle designs and ability to process a wide variety of materials, including metals, alloys, and composite materials. The company’s systems are particularly popular in the aerospace industry for turbine blade repairs and in automotive for lightweight component manufacturing. Oerlikon’s reputation in additive manufacturing has significantly contributed to its growth, with a prominent presence in both North America and Europe.
2. Stellite
Stellite, a subsidiary of Kennametal, is another dominant player in the Cold Spray Additive Manufacturing Market. The company is known for its Stellite Cold Spray Systems, which offer a comprehensive range of materials suitable for aerospace, defense, and industrial applications. Stellite specializes in high-performance coatings and restoration of critical parts, such as aerospace components, automotive parts, and industrial machinery. Stellite’s cold spray solutions are particularly noted for their ability to repair worn parts with minimal thermal impact, making them ideal for industries that rely on high-value components. Stellite’s market share has grown due to the company’s continuous focus on improving product efficiency and offering tailored solutions for industries with stringent quality standards.
3. Thermo Fisher Scientific
Thermo Fisher Scientific is a global leader in providing Cold Spray Additive Manufacturing solutions. The company’s Thermo Fisher Cold Spray Systems are widely used in aerospace, automotive, and energy industries. Known for their precision and adaptability, these systems can handle a variety of materials such as titanium, nickel alloys, and aluminum. Thermo Fisher is also recognized for its focus on research and development, continually refining its Cold Spray technology to improve its applications in areas like component repair, wear-resistant coatings, and additive manufacturing of complex structures. The company has carved out a significant share in the Cold Spray Additive Manufacturing Market by leveraging its extensive experience in material science and process optimization.
4. Impact Innovations
Impact Innovations is a key player in the Cold Spray Additive Manufacturing Market, offering Impact Cold Spray Systems designed for high-performance and industrial-grade applications. Their systems are used in a variety of sectors, including aerospace, energy, and automotive. Impact Innovations has focused on making Cold Spray technology more accessible to smaller manufacturers by offering scalable and cost-effective solutions. The company’s systems are particularly useful in repair and restoration processes, where high material integrity is required. Their Cold Spray solutions are known for their high deposition efficiency and precise material handling, which has earned them a significant market share, especially in North America and Europe.
5. Cold Spray Technologies
Cold Spray Technologies is an emerging player in the Cold Spray Additive Manufacturing space. Their CST Cold Spray Systems are designed for both industrial and commercial applications, specializing in repair and coating applications. The company’s systems are utilized primarily in the aerospace and defense sectors for high-value part repairs, such as engine components and turbine blades. Cold Spray Technologies is also expanding its footprint in automotive and energy industries by offering customizable Cold Spray systems that cater to the specific needs of manufacturers. The company’s market share has grown steadily, driven by the increasing demand for repair and restoration services and the rising adoption of additive manufacturing techniques across industries.
6. Aerospace Manufacturing Technologies (AMT)
Aerospace Manufacturing Technologies (AMT) has a strong presence in the Cold Spray Additive Manufacturing Market, particularly in the aerospace sector. AMT’s Cold Spray Solutions for Aerospace are focused on the repair of critical aerospace components, such as jet engine parts, landing gears, and turbine blades. Their systems are designed for high-throughput, high-precision applications, ensuring the highest level of material integrity during repairs. The company’s expertise in aerospace manufacturing has helped it secure a significant market share, with collaborations with major aerospace manufacturers like Boeing and Airbus. AMT’s advanced systems are highly regarded for their reliability and precision, contributing to their growing success in the Cold Spray Additive Manufacturing Market.
7. Plasma Giken
Plasma Giken is a key player in the Cold Spray Additive Manufacturing space, particularly known for its Plasma Giken Cold Spray Technology. The company’s systems are primarily used in the aerospace, automotive, and defense industries, with a strong focus on coating and repair applications. Plasma Giken is known for its high-performance Cold Spray systems that deliver consistent results across a range of materials, including steel, aluminum, and titanium alloys. Their systems are often used for the restoration of components exposed to extreme wear and tear. Plasma Giken’s market share continues to grow due to its focus on product innovation and the expanding demand for repair services in high-performance industries.
Cold Spray Additive Manufacturing Market Share by Manufacturers
The Cold Spray Additive Manufacturing Market is highly competitive, with a few dominant players holding significant market share. Among these, Oerlikon and Stellite are the leading companies, with combined market share exceeding 30%. These two companies have capitalized on their extensive product portfolios and technological expertise to secure their positions as market leaders. Their systems are widely recognized for their quality and ability to meet the stringent requirements of industries such as aerospace, automotive, and energy.
Thermo Fisher Scientific follows closely behind, holding around 15% of the market share. The company’s reputation for precision and material science has helped it secure a substantial portion of the Cold Spray Additive Manufacturing Market, particularly in the North American and European regions.
Impact Innovations and Cold Spray Technologies are emerging players that have been able to capture around 10% of the market by offering cost-effective and scalable solutions. Their ability to cater to smaller manufacturers and offer customizable Cold Spray systems has made them popular among industries looking for affordable and efficient Cold Spray technologies.
Plasma Giken holds a smaller but growing share of the market, with approximately 8% of the Cold Spray Additive Manufacturing Market. The company’s focus on high-performance applications in aerospace and defense is driving its steady growth and increasing adoption in these sectors.
Recent News and Industry Developments
Recent developments in the Cold Spray Additive Manufacturing Market highlight the growing importance of this technology in industrial applications. In 2024, Oerlikon launched a new product line called the Oerlikon Metco 4500 Series, which offers enhanced deposition efficiency and can handle a broader range of materials, including advanced alloys and composite powders. This development is expected to strengthen Oerlikon’s market position, particularly in aerospace and automotive applications, where material performance is critical.
In the same year, Stellite announced a strategic partnership with a leading aerospace manufacturer to provide Cold Spray technology for the repair of turbine blades used in commercial jet engines. This collaboration is aimed at expanding Stellite’s reach in the aerospace sector, where the demand for cost-effective repair solutions is growing rapidly. The partnership is expected to increase Stellite’s market share in aerospace by 5% over the next three years.
Additionally, Thermo Fisher Scientific unveiled its new Thermo Fisher Cold Spray Coating System in early 2025, designed to provide enhanced automation and higher throughput in additive manufacturing environments. This new system is aimed at automotive and energy industries looking to scale production of lightweight components and improve the efficiency of repair processes.
“Cold Spray Additive Manufacturing Production Data and Cold Spray Additive Manufacturing Production Trend, Cold Spray Additive Manufacturing Production Database and forecast”
-
- Cold Spray Additive Manufacturing production database for historical years, 10 years historical data
- Cold Spray Additive Manufacturing production data and forecast for next 7 years
Market Scenario, Demand vs Supply, Average Product Price, Import vs Export, till 2035
- Global Cold Spray Additive Manufacturing Market revenue and demand by region
- Global Cold Spray Additive Manufacturing Market production and sales volume
- United States Cold Spray Additive Manufacturing Market revenue size and demand by country
- Europe Cold Spray Additive Manufacturing Market revenue size and demand by country
- Asia Pacific Cold Spray Additive Manufacturing Market revenue size and demand by country
- Middle East & Africa Cold Spray Additive Manufacturing Market revenue size and demand by country
- Latin America Cold Spray Additive Manufacturing Market revenue size and demand by
- Import-export scenario – United States, Europe, APAC, Latin America, Middle East & Africa
- Average product price – United States, Europe, APAC, Latin America, Middle East & Africa
- Market player analysis, competitive scenario, market share analysis
- Business opportunity analysis
Key questions answered in the Global Cold Spray Additive Manufacturing Market Analysis Report:
- What is the market size for Cold Spray Additive Manufacturing in United States, Europe, APAC, Middle East & Africa, Latin America?
- What is the yearly sales volume of Cold Spray Additive Manufacturing and how is the demand rising?
- Who are the top market players by market share, in each product segment?
- Which is the fastest growing business/ product segment?
- What should be the business strategies and Go to Market strategies?
The report covers Cold Spray Additive Manufacturing Market revenue, Production, Sales volume, by regions, (further split into countries):
- Asia Pacific (China, Japan, South Korea, India, Indonesia, Vietnam, Rest of APAC)
- Europe (UK, Germany, France, Italy, Spain, Benelux, Poland, Rest of Europe)
- North America (United States, Canada, Mexico)
- Latin America (Brazil, Argentina, Rest of Latin America)
- Middle East & Africa
Table of Contents:
Cold Spray Additive Manufacturing Market
- Introduction to Cold Spray Additive Manufacturing (CSAM)
- Overview of Cold Spray Technology
- Role in Additive Manufacturing
- Advantages and Limitations of Cold Spray Technology
- Benefits for Manufacturing and Repair Applications
- Challenges in Adoption
- Market Overview and Scope
- Applications Across Industries
- Key Market Drivers and Restraints
- Global Market Trends and Growth Opportunities (2019-2035)
- Expansion in Aerospace and Automotive Sectors
- Rising Demand for Sustainable Manufacturing
- Market Segmentation by Material Type
- Metals and Alloys
- Ceramics
- Composites
- Market Segmentation by Application
- Component Manufacturing
- Repair and Restoration
- Coating Applications
- Regional Market Analysis (2019-2035)
- North America
- Europe
- Asia-Pacific
- Latin America
- Middle East & Africa
- United States Market Insights
- Production and Revenue Trends
- Role of Defense and Aerospace Industries
- European Market Insights
- Technological Advancements
- Collaboration Between Research Institutes and Manufacturers
- Asia-Pacific Market Insights
- Growing Industrial Base
- Investments in Additive Manufacturing
- Latin America Market Insights
- Adoption Across Emerging Economies
- Opportunities in Automotive Manufacturing
- Middle East & Africa Market Insights
- Role of Energy and Defense Sectors
- Market Expansion Opportunities
- Cold Spray Process and Technology Analysis
- Overview of the Cold Spray Process
- Innovations and Technological Developments
- Competitive Landscape and Market Share
- Leading Companies and Market Strategies
- Key Partnerships and Collaborations
- Manufacturing Cost Analysis
- Cost Components of Cold Spray Additive Manufacturing
- Impact of Material Prices
- Key Raw Materials Analysis
- Availability of Core Materials
- Pricing Trends for Metal Powders and Ceramics
- Raw Material Suppliers Overview
- Major Suppliers and Their Market Reach
- Regional Supplier Dynamics
- Industrial Chain Analysis
- Upstream and Downstream Integration
- Supply Chain Optimization
- Revenue and Profitability Analysis
- Regional Revenue Trends
- Profit Margins Across Applications
- Market Distribution Channels
- Supply Chain and Distribution Models
- Role of Distributors and Service Providers
- Key End-User Analysis
- Industries Driving Demand for Cold Spray
- Emerging Use Cases in Critical Sectors
- Environmental and Regulatory Landscape
- Sustainability in Cold Spray Manufacturing
- Compliance with Global Standards
- Research and Development in Cold Spray Additive Manufacturing
- Cutting-Edge Innovations
- Investments in R&D by Industry Leaders
- Opportunities and Challenges in the CSAM Market
- Barriers to Entry for New Players
- Opportunities in Customized Manufacturing
- Import and Export Analysis
- Trade Dynamics by Region
- Role of Global Supply Chains
- Future Trends in Cold Spray Additive Manufacturing
- Emerging Materials and Techniques
- Integration with Digital Manufacturing
- Market Forecast and Projections (2019-2035)
- Regional and Global Growth Outlook
- Potential Disruptions and Game-Changing Innovations
“Every Organization is different and so are their requirements”- Datavagyanik
Companies We Work With
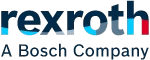
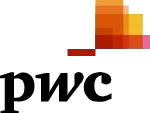
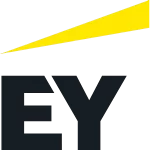
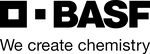
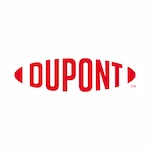

Do You Want To Boost Your Business?
drop us a line and keep in touch
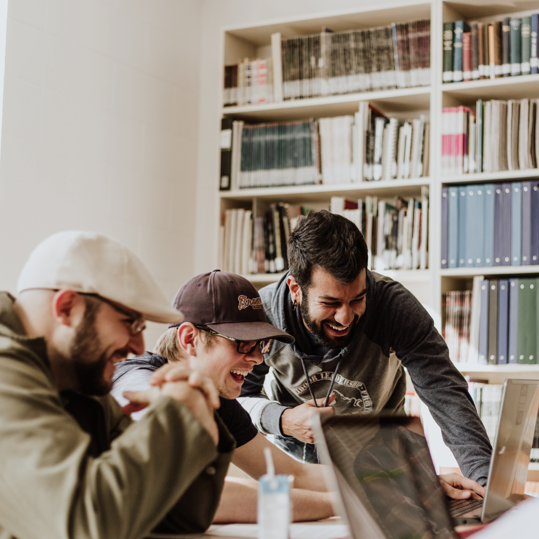