Internal Engine Coatings Market Size, Production, Sales, Average Product Price, Market Share, Import vs Export
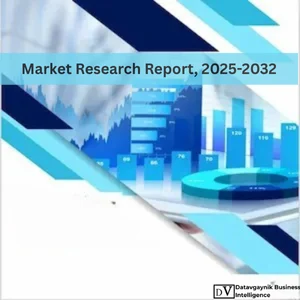
- Published 2025
- No of Pages: 120+
- 20% Customization available
Internal Engine Coatings Market Gaining Momentum Amid Shifting Industry Priorities
The Internal Engine Coatings Market is experiencing an accelerated shift driven by structural changes in the automotive, aerospace, and industrial machinery sectors. For instance, the rising demand for fuel efficiency, longevity, and reduced maintenance is directly increasing the adoption of high-performance engine coatings. Coatings that were once considered niche—such as thermal barrier and low-friction solutions—have now become essential components in the design of modern internal combustion engines. The shift is evident in the fact that OEMs are integrating coatings during production stages, rather than relying solely on aftermarket applications. This fundamental transition has pushed the Internal Engine Coatings Market into a high-growth trajectory globally.
Fuel Efficiency as a Primary Growth Lever in the Internal Engine Coatings Market
Fuel economy remains one of the most influential drivers in the Internal Engine Coatings Market. For example, dry film lubricants used in piston skirts and valve trains have proven to reduce friction losses by up to 30%, thereby improving fuel consumption metrics by 3–5% in passenger vehicles. With global fuel efficiency regulations tightening across the U.S., EU, India, and China, automakers are compelled to implement technologies that offer quantifiable gains. This includes applying DLC (diamond-like carbon) and ceramic-based coatings on critical engine parts to reduce wear and friction, significantly improving miles per gallon (MPG) ratings. As a result, the Internal Engine Coatings Market is not only benefitting from compliance-related urgency but also from the financial and operational savings that these coatings offer.
Datavagyanik also covers related markets such as the Internal combustion engine oil additive Market and the Biodegradable Engine Oil Market. Understanding these markets sheds light on emerging innovations and industry crossovers that impact the main topic.
Stricter Emission Norms Fuel Demand Across the Internal Engine Coatings Market
Another compelling factor driving the Internal Engine Coatings Market is the global implementation of stricter emission norms. For instance, the transition from Euro 6 to Euro 7 regulations in the European Union has created a sense of urgency among automakers to improve combustion efficiency and reduce particulate emissions. Coatings such as thermal barriers, when applied to cylinder heads and pistons, help maintain optimal combustion temperatures and reduce unburned hydrocarbons. This, in turn, directly lowers NOx and CO2 emissions. Countries like China and India, implementing equivalent BS-VI and China 6 norms, are accelerating local demand. Consequently, the Internal Engine Coatings Market is witnessing parallel growth in both developed and emerging economies.
Hybrid Powertrain Growth Catalyzing the Internal Engine Coatings Market
The widespread adoption of hybrid electric vehicles (HEVs) is creating new growth pockets within the Internal Engine Coatings Market. Unlike fully electric vehicles, HEVs retain internal combustion engines, albeit operating under more dynamic and varied load cycles. These load cycles increase stress on engine components, demanding enhanced coatings for longevity and efficiency. For instance, Toyota and Honda, both leaders in hybrid vehicles, have been investing in nanostructured coatings that can withstand rapid start-stop cycles and temperature fluctuations. As HEV production is expected to rise by over 20% CAGR globally through 2030, the Internal Engine Coatings Market is likely to see proportional growth in applications tailored to hybrid configurations.
Advanced Materials Boosting Innovation in the Internal Engine Coatings Market
Innovations in materials science are redefining the scope of the Internal Engine Coatings Market. Nano-coatings, self-healing coatings, and ceramic matrix composites are enabling engines to operate at higher pressures and temperatures without degrading component lifespan. For example, the use of zirconia-based ceramic coatings can maintain thermal insulation properties even at 1200°C, making them ideal for turbocharged engines and high-performance aerospace turbines. Moreover, self-lubricating coatings embedded with molybdenum disulfide are gaining adoption in high-revving engines across motorsports. These material advancements are not only performance-driven but are also reducing the environmental impact by minimizing the need for lubricant top-ups and engine part replacements.
Aerospace Sector Opening High-Value Channels in the Internal Engine Coatings Market
The aerospace industry’s growing demand for efficient, lightweight, and thermally resilient engines has opened up premium application segments for the Internal Engine Coatings Market. Jet engines, for example, require thermal barrier coatings for turbine blades and combustion chambers to operate efficiently at extreme altitudes and temperatures. With global commercial aircraft production expected to exceed 40,000 units by 2040, and defense aircraft demand on the rise, aerospace alone is set to become one of the most lucrative sectors within the Internal Engine Coatings Market. Additionally, the integration of hypersonic technology and reusable space vehicles is accelerating the need for next-generation coatings capable of withstanding extreme re-entry temperatures.
High-Performance Automotive Segment Accelerating Demand in the Internal Engine Coatings Market
Luxury and performance vehicle manufacturers are investing heavily in the Internal Engine Coatings Market to support engines that exceed conventional operating thresholds. For instance, brands like Ferrari, Porsche, and BMW are leveraging plasma-sprayed coatings on cylinder walls and DLC coatings on camshafts to enhance wear resistance and heat dissipation. These coatings enable engine downsizing without compromising output, supporting the trend toward smaller, turbocharged engines delivering higher torque. Furthermore, with the performance car segment expected to grow at over 8% CAGR through 2030, largely driven by the Asia Pacific and Middle East markets, the Internal Engine Coatings Market is aligned to benefit significantly from this upward trend.
Emerging Economies Reshaping Regional Dynamics in the Internal Engine Coatings Market
Countries like India, Brazil, Mexico, and Indonesia are becoming vital to the growth dynamics of the Internal Engine Coatings Market. For instance, India produced over 25 million vehicles in 2023 alone, with rising demand for efficient two-wheelers and commercial vehicles driving coating consumption. Domestic manufacturers are now implementing cost-effective thermal and anti-friction coatings to meet BS-VI emission norms and improve component durability in tropical climates. Similarly, Mexico’s rising role as a manufacturing hub for North American vehicle exports is creating a robust market for internal engine coatings tailored to both OEM and aftermarket applications. These countries are not only contributing to consumption but also scaling up their own production capacities, transforming the Internal Engine Coatings Market into a more decentralized and competitive landscape.
Electric Powertrain Integration Broadening Scope of the Internal Engine Coatings Market
Contrary to initial assumptions, the electrification of mobility is not limiting the growth of the Internal Engine Coatings Market. Instead, it is reshaping its trajectory. In electric and hybrid vehicles, coatings are increasingly used in auxiliary systems such as electric drive units, reducers, and thermally sensitive components within range extenders. For instance, Tesla and Rivian are adopting coatings in battery cooling systems and electric motor assemblies to manage heat dissipation and corrosion. Moreover, fuel cell vehicles, which operate at elevated temperatures, require advanced coatings for hydrogen combustion chambers and turbine components. As electrified powertrains evolve, so will the demand for engineered coatings—further embedding the Internal Engine Coatings Market into the future of mobility.
Aftermarket and Remanufacturing Bolstering Volume in the Internal Engine Coatings Market
The global trend toward vehicle remanufacturing and extended engine life is supporting the aftermarket side of the Internal Engine Coatings Market. As vehicle replacement cycles get longer and consumers demand cost-effective maintenance solutions, coating applications during engine rebuilds are gaining traction. For instance, aftermarket service providers across Europe and North America are offering cylinder wall coating services using plasma and thermal spray techniques to restore engines without requiring new components. The aftermarket segment, expected to grow by 6% CAGR through 2030, represents a consistent and volume-driven contributor to the Internal Engine Coatings Market, particularly in regions with aging vehicle populations.
“Track Country-wise Internal Engine Coatings Production and Demand through our Internal Engine Coatings Production Database”
-
-
- Internal Engine Coatings production database for 20+ countries worldwide
- Country-wise Internal Engine Coatings production capacity and production plant mapping
- Internal Engine Coatings production plants and production plant capacity analysis for key manufacturers
-
United States Leading Innovation in the Internal Engine Coatings Market
The United States remains a global powerhouse in the Internal Engine Coatings Market, driven by its dominant automotive, aerospace, and industrial machinery sectors. For instance, U.S.-based OEMs such as General Motors and Ford are investing in advanced coating technologies to meet stringent EPA emission norms and CAFE standards. These companies are applying DLC coatings and thermal spray systems to internal combustion components to boost durability and minimize fuel losses. Moreover, the rise in hybrid electric vehicles across the U.S. has not diminished the role of internal engines; instead, it has redefined the requirements, pushing demand for coatings that endure variable load cycles and thermal fluctuations. Aerospace manufacturers like GE Aviation are also scaling up their use of high-temperature ceramic coatings, making the country a key contributor to volume and innovation in the Internal Engine Coatings Market.
Germany Driving High-Performance Growth in the Internal Engine Coatings Market
Germany’s engineering precision and stronghold in automotive manufacturing have positioned it as a critical hub for the Internal Engine Coatings Market in Europe. With leading OEMs such as BMW, Mercedes-Benz, and Volkswagen continuously advancing engine efficiency, the demand for high-performance coatings is expanding. For example, Germany’s widespread use of plasma-sprayed ceramic coatings on engine cylinder heads and turbo components is enabling longer engine life under high thermal loads. The country’s implementation of Euro 7 norms is further compelling the adoption of coatings that can reduce emissions by enhancing combustion efficiency. In addition, Germany’s participation in performance vehicle and motorsport segments fuels the need for friction-reducing and high-temperature-resistant solutions. The presence of high-value R&D institutions and coating manufacturers also enhances local production capacity, solidifying Germany’s strategic role in the Internal Engine Coatings Market.
France and Italy Strengthening Regional Demand in the Internal Engine Coatings Market
France and Italy collectively contribute to expanding the Internal Engine Coatings Market through specialized applications in automotive and aerospace sectors. In France, aerospace manufacturers like Safran are demanding thermal barrier coatings capable of withstanding extreme pressures and heat in jet engines. For example, the growing production of narrow-body commercial aircraft has directly increased consumption of thermal insulation coatings. On the automotive front, French brands such as Renault and Peugeot are implementing corrosion-resistant coatings to comply with EU environmental regulations and improve lifecycle cost metrics. Italy, meanwhile, leverages its heritage in high-performance vehicles—such as Ferrari, Maserati, and Lamborghini—to push for coatings that can tolerate rapid acceleration and elevated operating temperatures. This unique requirement for high-friction and anti-wear coatings in racing and luxury engines contributes distinctly to the Internal Engine Coatings Market in Southern Europe.
United Kingdom and Sweden Expanding Technological Capabilities in the Internal Engine Coatings Market
The United Kingdom is building a robust niche within the Internal Engine Coatings Market by integrating academic research with industrial coating applications. For instance, UK-based manufacturers are increasingly developing nano-structured coatings that provide dual benefits—reducing wear and enabling thermal regulation in performance engines. The country’s investment in green mobility and compliance with post-Brexit emissions standards has boosted demand for low-friction coatings in both commercial and passenger vehicle segments. In Sweden, companies like Volvo are enhancing hybrid vehicle designs using lightweight coatings that optimize thermal management without adding mass. Sweden’s harsh climate also increases the need for coatings that perform in cold-start conditions, pushing adoption of advanced lubrication coatings. Together, the UK and Sweden are shaping the future of lightweight, multi-functional coatings in the Internal Engine Coatings Market.
China Scaling Production Leadership in the Internal Engine Coatings Market
China is emerging as the largest production hub within the Internal Engine Coatings Market, backed by its dominant automotive output and increasing technological capabilities. Producing over 25 million vehicles annually, China’s demand for wear-resistant, thermal barrier, and oil-shedding coatings is rising exponentially. Domestic automakers such as BYD and Geely are incorporating ceramic coatings in hybrid and fuel-efficient engines to comply with China 6 emission norms. Moreover, the rapid industrialization of heavy machinery and diesel engines for infrastructure and logistics is accelerating demand for corrosion-resistant coatings. China’s investment in local manufacturing of advanced coatings is reducing dependency on imports, while its growing aerospace sector is creating high-value applications for nano-engineered coatings. These developments are positioning China as both a consumption and production leader in the Internal Engine Coatings Market.
Japan and South Korea Innovating for Precision in the Internal Engine Coatings Market
Japan and South Korea are setting benchmarks in precision-engineered coatings within the Internal Engine Coatings Market. In Japan, companies like Toyota and Honda are pioneering low-emission hybrid engines that rely on DLC and thermal-resistant coatings for prolonged performance. For example, Japanese manufacturers apply multi-layered coatings to cylinder bores to balance wear resistance with reduced friction, extending engine life in urban and stop-start conditions. South Korea, home to Hyundai and Kia, is combining thermal barrier and corrosion-resistant technologies to improve marine, industrial, and automotive engine output. South Korea’s shipbuilding sector, one of the largest in the world, uses these coatings extensively for large diesel engines, creating spillover demand beyond automotive. Collectively, both nations are contributing to high-precision applications and raising the performance standards of the global Internal Engine Coatings Market.
India and Southeast Asia Driving Cost-Effective Expansion in the Internal Engine Coatings Market
India and Southeast Asian countries like Thailand, Indonesia, and Vietnam are becoming significant contributors to the Internal Engine Coatings Market, particularly in cost-sensitive segments. India’s automotive production, including over 21 million two-wheelers and 4 million passenger vehicles annually, demands low-friction and corrosion-resistant coatings for fuel efficiency and durability. For example, Indian manufacturers are increasingly using oil-shedding coatings in budget motorcycles to reduce sludge formation and enhance cooling efficiency. Meanwhile, Thailand’s automotive export industry and Indonesia’s infrastructure-heavy diesel engine demand are fostering production of internal engine coatings tailored for regional needs. These economies are not only absorbing imports from global suppliers but are also investing in domestic production units to cater to OEM and aftermarket demand. The scalability and affordability of coating technologies are reshaping the Internal Engine Coatings Market across Asia.
“Internal Engine Coatings Manufacturing Database, Internal Engine Coatings Manufacturing Capacity”
-
-
- Internal Engine Coatings top manufacturers market share
- Top five manufacturers and top 10 manufacturers of Internal Engine Coatings in North America, Europe, Asia Pacific
- Production plant capacity by manufacturers and Internal Engine Coatings production data for market players
- Internal Engine Coatings production dashboard, Internal Engine Coatings production data in excel format
-
Market Segmentation by Coating Type Reflects Application-Driven Demand in the Internal Engine Coatings Market
The Internal Engine Coatings Market is segmented by coating type into thermal barrier coatings, dry film lubricants, corrosion-resistant coatings, oil-shedding coatings, and heat-resistant coatings. Each serves distinct application niches. For instance, thermal barrier coatings (TBCs), commonly zirconia-based, are used extensively in turbochargers and combustion chambers to maintain high efficiency at extreme temperatures. Dry film lubricants, often containing graphite or MoS₂, reduce metal-to-metal contact in piston assemblies and valve trains, improving fuel economy and reducing engine noise. Corrosion-resistant coatings are vital in marine and industrial diesel engines, preventing failure due to prolonged exposure to saline or chemical environments. Oil-shedding coatings help maintain cleanliness and oil flow in connecting rods and valve covers, while heat-resistant coatings are essential in engines operating under cyclical thermal stress. This functional diversification reflects the multidimensional nature of demand within the Internal Engine Coatings Market.
Material-Based Segmentation Strengthens Technical Adaptability in the Internal Engine Coatings Market
The Internal Engine Coatings Market is also segmented by substrate material—aluminum, steel, cast iron, and magnesium alloys—each with specific coating compatibility needs. For example, aluminum, widely used for its lightweight advantages in automotive and aerospace applications, requires coatings that address thermal degradation and galling issues. Coatings like anodized ceramics and dry films are tailored for aluminum substrates. Steel and cast iron, used in heavy-duty engines, demand corrosion-resistant and low-friction coatings that prevent pitting and oxidation. Magnesium alloys, gaining ground in high-performance and electric vehicle designs, require ultra-light coatings that do not compromise surface hardness. The ability to customize coatings based on substrate compatibility is increasing the adaptability of the Internal Engine Coatings Market, enhancing its relevance across traditional and next-generation engines.
Application-Based Segmentation Unlocking Multi-Sectoral Growth in the Internal Engine Coatings Market
By application, the Internal Engine Coatings Market spans passenger vehicles, commercial vehicles, industrial engines, marine engines, and aerospace systems. Passenger vehicles dominate volume consumption due to their global footprint, with over 70 million units sold annually. These engines require coatings for pistons, cylinders, and camshafts to meet fuel economy targets and extend service life. Commercial vehicles, including trucks and buses, demand high-durability coatings capable of withstanding prolonged operational hours and higher thermal loads. Industrial engines used in mining, agriculture, and power generation require corrosion and heat-resistant coatings to operate in rugged environments. Marine engines face additional challenges due to saltwater corrosion, making anti-corrosion coatings indispensable. Finally, aerospace engines depend on high-performance thermal coatings to withstand extreme atmospheric pressures and heat. This wide array of applications is continuously expanding the scope and depth of the Internal Engine Coatings Market.
Leading Manufacturers Shaping the Internal Engine Coatings Market Globally
The Internal Engine Coatings Market is supported by a strong network of global manufacturers that offer specialized coatings for a variety of engine types, performance requirements, and environmental conditions. These companies are driving the market forward with proprietary technologies, advanced material science, and high-capacity production systems tailored to automotive, aerospace, marine, and industrial applications.
Henkel AG & Co. KGaA – Performance Coatings for Powertrain Components
Henkel is a dominant player in the Internal Engine Coatings Market, particularly through its LOCTITE and BONDERITE product lines. LOCTITE dry film lubricants are extensively used on piston skirts, valve trains, and camshafts to reduce friction and wear. BONDERITE coatings, on the other hand, are engineered for corrosion protection and thermal stability in extreme engine conditions. Henkel has focused heavily on water-based and environmentally friendly formulations, making it a preferred supplier among OEMs looking to meet sustainability goals. The company’s global manufacturing footprint and R&D capabilities position it at the forefront of innovation within the Internal Engine Coatings Market.
Praxair Surface Technologies (now part of Oerlikon Group) – Thermal Spray Coating Specialists
Praxair Surface Technologies, now integrated under the Oerlikon Group, specializes in thermal barrier coatings (TBCs) and wear-resistant coatings applied using advanced HVOF (High-Velocity Oxy-Fuel) and plasma spray processes. Their Metco and Amdry series are widely used in high-performance internal combustion engines and aerospace turbine components. These coatings are particularly valuable for engines operating under high thermal stress and pressure, such as in motorsport and jet propulsion systems. Oerlikon’s focus on lightweight, high-temperature-resistant coatings ensures continued leadership in the Internal Engine Coatings Market, especially across Europe and North America.
Zircotec Ltd – Ceramic Thermal Coating Innovator
UK-based Zircotec has carved a niche in the Internal Engine Coatings Market with its proprietary plasma-applied ceramic coatings. The Thermohold range is known for reducing under-hood temperatures by up to 33%, directly benefiting turbocharged and high-compression engines. Zircotec serves automotive OEMs and aftermarket tuning industries, offering solutions that improve engine efficiency while enhancing thermal management. Its expertise in motorsport-grade coatings has attracted clients in Formula One, WRC, and endurance racing, expanding its role in performance-critical applications.
A&A Coatings – Custom Engineered Internal Engine Coatings for Industrial Engines
A&A Coatings, based in the United States, specializes in custom-engineered coatings for industrial and heavy-duty engines. Their offerings include thermal spray coatings, wear-resistant coatings, and corrosion-resistant applications tailored for generators, marine engines, and diesel systems. Products like Ceramic-Metal Matrix Coatings are developed to improve surface hardness and prevent thermal degradation. The company serves sectors such as oil & gas, power generation, and large-scale manufacturing, providing essential coating solutions that extend operational lifespans and improve energy efficiency in industrial applications of the Internal Engine Coatings Market.
Bodycote plc – Heat Treatment and Engine Coatings Synergy
Bodycote, a global leader in thermal processing, integrates heat treatment with surface coating technologies. Their S³P (Specialty Stainless Steel Processing) and Thermal Spray Coating services are applied on engine parts to enhance wear and corrosion resistance. Operating over 180 facilities worldwide, Bodycote collaborates with engine manufacturers across automotive and aerospace sectors to provide coatings that meet exact performance specifications. Their capability to combine metallurgical expertise with surface protection makes them a vital player in the Internal Engine Coatings Market.
Poeton Industries – High-Precision Coatings for Aerospace and Motorsport
Poeton Industries, headquartered in the UK, offers a range of advanced coatings such as Apticote 2000, a series of dry film lubricants and thermal barriers tailored for internal engine applications. These coatings are extensively used in aircraft engines and racing vehicles where minimal friction and extreme temperature resistance are critical. Poeton’s ability to deliver high-precision applications, often customized for specific projects, positions it as a premium supplier in the Internal Engine Coatings Market, especially in sectors that demand consistent performance under high stress.
Morgan Advanced Materials – Ceramic Coatings for Harsh Environments
Morgan Advanced Materials supplies ceramic-based coatings and components for engines exposed to extreme environments. Their products, such as Haldenwanger ceramics, are utilized in high-temperature areas of engines and turbines. The company is deeply embedded in the aerospace and power generation industries, providing materials that maintain structural integrity even under continuous high thermal loads. Their advanced ceramics play an increasingly strategic role in the evolution of the Internal Engine Coatings Market, especially in reducing component degradation and increasing engine reliability.
CemeCon AG – PVD Coating Technology Pioneer
CemeCon AG, based in Germany, brings advanced PVD (Physical Vapor Deposition) technologies into the Internal Engine Coatings Market. Their HiPIMS (High Power Impulse Magnetron Sputtering) coatings are used on engine valves, camshafts, and fuel system components to reduce wear and friction. These coatings are particularly effective in engines with high cycle frequency and demanding operating environments. CemeCon’s focus on precision deposition, along with its environmentally responsible coating systems, supports the market’s transition toward high-performance, sustainable technologies.
Curtiss-Wright Surface Technologies – Defense and Aerospace Coatings Leader
Curtiss-Wright serves both defense and commercial aerospace clients with specialized internal engine coatings. Their E/M Coating Services division delivers solutions such as solid film lubricants, anti-galling coatings, and thermal barriers designed for jet engines and turbine systems. These coatings ensure performance continuity under rapid pressure changes and temperature spikes, often seen in defense aviation platforms. With a global service network, Curtiss-Wright is a strategic contributor to the high-end segment of the Internal Engine Coatings Market.
Other Emerging Players and Regional Specialists in the Internal Engine Coatings Market
Beyond the major players, several emerging and regional manufacturers are scaling their presence in the Internal Engine Coatings Market. For example, India-based Pidilite Industries is expanding its automotive coatings segment with cost-effective formulations for two-wheeler engines. In China, Beijing Asahi Coatings is growing rapidly, supplying coatings tailored for domestic ICE and hybrid vehicle manufacturers. Companies like Magellan Aerospace and Hauzer Techno Coating are also contributing to niche applications, including aviation and industrial diesel engines, through innovations in vacuum coating and ion beam technologies.
“Internal Engine Coatings Production Data and Internal Engine Coatings Production Trend, Internal Engine Coatings Production Database and forecast”
-
-
- Internal Engine Coatings production database for historical years, 10 years historical data
- Internal Engine Coatings production data and forecast for next 7 years
-
Recent Developments and Strategic Moves in the Internal Engine Coatings Market
– In January 2024, Henkel announced a new R&D center in North Carolina dedicated to sustainable coatings, including advanced dry film lubricants for next-gen powertrains.
– In October 2023, Zircotec introduced Thermohold Ultra, a new generation of ceramic coatings targeting turbocharged hybrid engines in performance vehicles.
– Oerlikon launched a next-gen Amdry 9954 thermal barrier coating in September 2023, designed for aerospace engines operating at over 1300°C.
– In July 2023, CemeCon AG expanded its facility in Würselen, Germany, to meet growing demand for PVD coatings in EV and hybrid ICE components.
– Bodycote acquired two regional coating service providers in Mexico and the Czech Republic in Q2 2023 to increase reach in the Americas and Central Europe.
These strategic investments and product innovations signal that the Internal Engine Coatings Market is transitioning into a phase of maturity where performance, sustainability, and cost-efficiency will define competitive advantage. Manufacturers are no longer limited to addressing thermal or frictional issues—they are increasingly expected to deliver multi-functional coatings that support long-term engine health and regulatory compliance across a wide range of geographies and industries.
Market Scenario, Demand vs Supply, Average Product Price, Import vs Export, till 2035
- Global Internal Engine Coatings Market revenue and demand by region
- Global Internal Engine Coatings Market production and sales volume
- United States Internal Engine Coatings Market revenue size and demand by country
- Europe Internal Engine Coatings Market revenue size and demand by country
- Asia Pacific Internal Engine Coatings Market revenue size and demand by country
- Middle East & Africa Internal Engine Coatings Market revenue size and demand by country
- Latin America Internal Engine Coatings Market revenue size and demand by
- Import-export scenario – United States, Europe, APAC, Latin America, Middle East & Africa
- Average product price – United States, Europe, APAC, Latin America, Middle East & Africa
- Market player analysis, competitive scenario, market share analysis
- Business opportunity analysis
Key questions answered in the Global Internal Engine Coatings Market Analysis Report:
- What is the market size for Internal Engine Coatings in United States, Europe, APAC, Middle East & Africa, Latin America?
- What is the yearly sales volume of Internal Engine Coatings and how is the demand rising?
- Who are the top market players by market share, in each product segment?
- Which is the fastest growing business/ product segment?
- What should be the business strategies and Go to Market strategies?
The report covers Internal Engine Coatings Market revenue, Production, Sales volume, by regions, (further split into countries):
- Asia Pacific (China, Japan, South Korea, India, Indonesia, Vietnam, Rest of APAC)
- Europe (UK, Germany, France, Italy, Spain, Benelux, Poland, Rest of Europe)
- North America (United States, Canada, Mexico)
- Latin America (Brazil, Argentina, Rest of Latin America)
- Middle East & Africa
Table of Contents:
- Introduction to the Internal Engine Coatings Market
- Definition and Scope of Internal Engine Coatings
- Importance in Automotive and Industrial Engines
- Market Evolution and Emerging Trends
- Market Segmentation of Internal Engine Coatings
- By Coating Type (Thermal Barrier, Anti-Friction, Corrosion-Resistant, etc.)
- By Engine Type (Gasoline, Diesel, Hybrid, Electric Vehicle Components)
- By End-Use Industry (Automotive, Aerospace, Marine, Industrial Machinery)
- Global Internal Engine Coatings Market Overview and Forecast (2020-2040)
- Historical Market Performance
- Key Growth Drivers and Challenges
- Market Expansion Opportunities
- Regional Analysis of the Internal Engine Coatings Market
- Regional Market Trends and Demand Fluctuations
- Expansion of Internal Engine Coatings Production Facilities
- Country-Specific Market Growth Potential
- North America Internal Engine Coatings Market
- Market Size and Production Capacity
- Competitive Landscape and Key Players
- Industry Regulations and Compliance Factors
- Europe Internal Engine Coatings Market
- Technological Advancements and Innovations
- Regional Demand Trends in Automotive and Aerospace Sectors
- Market Forecast and Growth Potential
- Asia Pacific Internal Engine Coatings Market
- Rapid Industrialization and Rising Automotive Production
- Expansion of Internal Engine Coatings Production Facilities
- Future Market Growth and Demand Drivers
- Latin America Internal Engine Coatings Market
- Emerging Opportunities in Local Manufacturing
- Competitive Landscape and Market Share Distribution
- Challenges in Supply Chain and Distribution
- Middle East & Africa Internal Engine Coatings Market
- Role in High-Performance and Heavy-Duty Engines
- Market Potential in Energy and Marine Sectors
- Long-Term Growth Strategies
- Internal Engine Coatings Production Estimates and Future Outlook (2020-2040)
- Global and Regional Production Trends
- Investments in Advanced Manufacturing Technologies
- Sustainability and Efficiency Improvements in Coating Production
- Competitive Landscape of Internal Engine Coatings Manufacturers
- Market Positioning of Key Industry Players
- Strategies for Competitive Growth
- Research and Development in Internal Engine Coatings
- Global Internal Engine Coatings Production Overview
- Trends in Engine Coating Materials and Application Processes
- Advances in High-Performance Coating Technologies
- Future Production Capacity Expansions
- Revenue Market Share of Internal Engine Coatings Manufacturers (2020-2035)
- Financial Performance of Leading Companies
- Investment Trends and Market Profitability
- Revenue Growth Strategies
- Manufacturing Technologies for Internal Engine Coatings
- Evolution of Coating Application Techniques
- High-Temperature Resistant and Low-Friction Coatings
- Future Innovations in Internal Engine Coatings
- Pricing Trends and Profit Margins in the Internal Engine Coatings Market
- Factors Influencing Price Fluctuations
- Cost-Benefit Analysis of Different Coating Types
- Market-Specific Pricing Strategies
- Internal Engine Coatings Market Export Analysis
- Key Exporting Countries and Global Trade Routes
- Impact of Regulatory Standards on International Trade
- Export Growth Projections
- Internal Engine Coatings Market Import Analysis
- Demand for Imported Coatings by Region
- Comparative Analysis of Domestic vs. Imported Products
- Trade Barriers and Regulatory Challenges
- Consumption Patterns in the Internal Engine Coatings Market
- Industry Sectors Driving Market Demand
- Adoption of Next-Generation Coating Technologies
- Future Consumption Trends
- Regional Consumption Analysis of Internal Engine Coatings
- Variations in Demand Across Key Markets
- Economic and Industrial Factors Affecting Consumption
- Strategic Growth Opportunities
- Product-Based Consumption Analysis in the Internal Engine Coatings Market
- Market Demand by Coating Type and Application
- Performance Comparison of Different Internal Engine Coatings
- New Product Development Trends
- Global Internal Engine Coatings Production Forecast by Product Type (2020-2040)
- Manufacturing Trends for Different Coating Materials
- Future Demand Projections by Engine Type
- Growth Potential in Innovative Coating Solutions
- Revenue Market Share by Internal Engine Coatings Product Type (2020-2040)
- Financial Insights by Coating Category
- Market Share Trends of Various Coating Technologies
- Future Revenue Growth Potential
- Internal Engine Coatings Manufacturing Cost Analysis
- Breakdown of Production Costs and Cost Optimization Strategies
- Economic Factors Influencing Manufacturing Costs
- Future Cost Trends and Efficiency Improvements
- Key Raw Materials for Internal Engine Coatings Production
- Essential Materials and Their Market Availability
- Supply Chain Risks and Alternative Sourcing Strategies
- Pricing Trends of Raw Materials
- Leading Suppliers of Raw Materials for Internal Engine Coatings
- Global and Regional Raw Material Providers
- Strategies for Securing Raw Material Supply Chains
- Challenges in Sourcing High-Quality Materials
- Industrial Chain Analysis of the Internal Engine Coatings Market
- Supply Chain Overview from Raw Materials to End-Use Applications
- Role of Distributors and Logistics in Market Growth
- Strategies for Optimizing the Industrial Chain
- Marketing Strategies and Sales Channels for Internal Engine Coatings
- Effective Market Penetration Strategies
- Digital and Traditional Marketing Approaches
- Distribution Networks and Customer Engagement
- Comprehensive List of Internal Engine Coatings Distributors
- Leading Market Distributors and Their Roles
- Geographic Reach and Distribution Capabilities
- Market Expansion Strategies
- Key Partnerships and Collaborations in the Internal Engine Coatings Industry
- Strategic Alliances and Joint Ventures
- Impact of Collaborations on Market Growth
- Future Prospects of Industry Partnerships
- Major End-Users of Internal Engine Coatings
- Key Industries Utilizing Internal Engine Coatings
- Market Strategies for Targeting End-Users
- Future Demand Trends in Different Sectors
- Internal Engine Coatings Production and Supply Forecast (2025-2040)
- Long-Term Production and Demand Trends
- Market Growth Predictions and Industry Advancements
- Future Evolution of the Supply Chain
“Every Organization is different and so are their requirements”- Datavagyanik
Companies We Work With
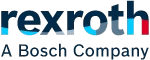
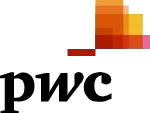
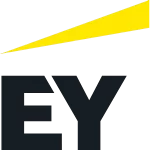
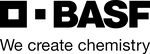
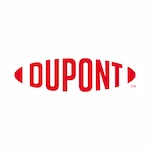

Do You Want To Boost Your Business?
drop us a line and keep in touch
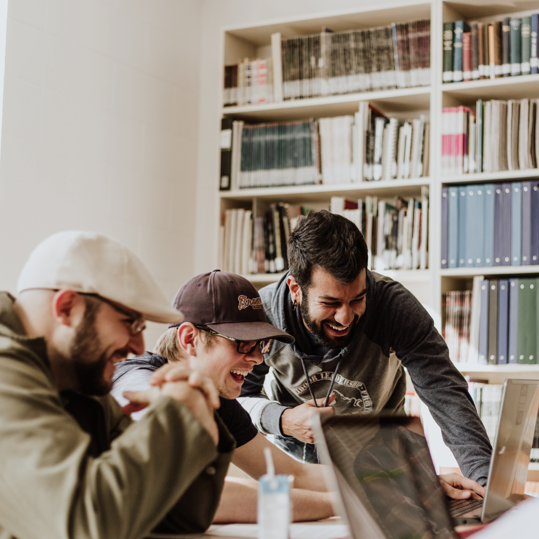