Hydrophobic Coating for Oil & Gas Industry Market Size, Production, Sales, Average Product Price, Market Share, Import vs Export
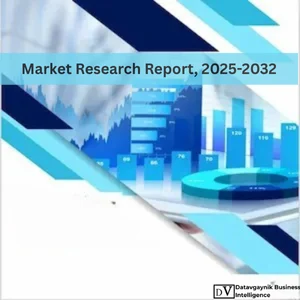
- Published 2025
- No of Pages: 120+
- 20% Customization available
Accelerating Growth in Hydrophobic Coating for Oil & Gas Industry Market
The Hydrophobic Coating for Oil & Gas Industry Market is experiencing significant momentum, fueled by escalating demand for protective solutions that safeguard critical infrastructure in extremely harsh environments. Oil and gas assets, including pipelines, offshore platforms, and storage tanks, face constant exposure to water, salt, and chemicals — factors that accelerate corrosion and degrade materials. As the industry expands its offshore drilling and deepwater exploration activities, the need for advanced water-repellent coatings has become more urgent. The market size is poised for steady growth, driven by increasing investments in infrastructure and stringent safety regulations.
In regions like the North Sea and Gulf of Mexico, where equipment is exposed to saline seawater and extreme weather conditions, hydrophobic coatings are indispensable. Their ability to prevent moisture accumulation and resist corrosion not only extends equipment life but also reduces costly maintenance and downtime. This market trend is underscored by the growing shift towards adopting high-performance coatings, including silicone- and fluoropolymer-based solutions, which offer superior protection and longer service life compared to traditional coatings.
Corrosion Protection: The Backbone of Hydrophobic Coating for Oil & Gas Industry Market Demand
The foremost driver behind the Hydrophobic Coating for Oil & Gas Industry Market is corrosion protection. Corrosion poses one of the greatest risks to oil and gas infrastructure, leading to equipment failure, safety hazards, and financial losses. In offshore environments, metal surfaces are continuously exposed to moisture, salt spray, and temperature fluctuations, creating ideal conditions for rust and deterioration.
Hydrophobic coatings create an invisible shield that repels water and prevents it from adhering to surfaces, effectively halting the corrosion cycle. For example, pipelines coated with advanced hydrophobic layers demonstrate extended lifespan by significantly reducing rust formation. The market is also witnessing the integration of nanotechnology into coatings, enhancing water repellency and durability, thereby providing an even more robust defense against corrosion.
The widespread adoption of these coatings in oil refineries, subsea equipment, and storage tanks illustrates their critical role. Operators report a substantial decrease in maintenance frequency and costs, highlighting the economic and operational benefits fueling market growth.
Operational Efficiency Boost Through Hydrophobic Coating for Oil & Gas Industry Market Expansion
The Hydrophobic Coating for Oil & Gas Industry Market also benefits from its contribution to improving operational efficiency. Water-induced issues such as ice and hydrate formation inside pipelines are major challenges, especially in cold climates or deepwater conditions. These issues lead to blockages, reducing flow efficiency and risking shutdowns.
By applying hydrophobic coatings, the industry minimizes ice adhesion and hydrate build-up, maintaining optimal flow and preventing energy losses. This technological advantage leads to smoother operations, less downtime, and improved safety. For instance, offshore platforms equipped with hydrophobic coatings see better flow assurance, enabling uninterrupted oil and gas transportation.
In addition, hydrophobic coatings reduce friction and drag within pipelines, which enhances energy efficiency by lowering the pumping power required. This efficiency translates into reduced operational costs and supports the industry’s sustainability goals by cutting energy consumption.
Maintenance Cost Reduction Driving Hydrophobic Coating for Oil & Gas Industry Market Growth
Maintenance expenses form a significant portion of operational budgets in the oil and gas sector. The Hydrophobic Coating for Oil & Gas Industry Market gains traction as these coatings help reduce wear and tear, thus lowering maintenance requirements.
By preventing water accumulation and corrosion, hydrophobic coatings extend the service intervals of critical assets such as pipelines, tanks, and offshore rigs. This results in fewer unplanned shutdowns, less frequent recoating, and reduced labor costs. For example, operators using hydrophobic coatings report up to a 30% reduction in maintenance-related downtime.
Moreover, the coatings’ self-cleaning properties prevent the buildup of contaminants, reducing the need for harsh cleaning chemicals and minimizing environmental impact. This cost-efficiency and sustainability aspect further encourage industry players to adopt hydrophobic solutions widely.
Performance in Extreme Conditions Bolstering Hydrophobic Coating for Oil & Gas Industry Market Demand
The oil and gas industry operates in some of the planet’s most challenging environments—offshore rigs face corrosive saltwater, Arctic operations encounter freezing temperatures, and desert facilities endure intense heat and sand abrasion. The Hydrophobic Coating for Oil & Gas Industry Market is thriving because these coatings reliably perform in such extremes.
Hydrophobic coatings resist exposure to chemicals, saltwater, and thermal fluctuations, protecting assets in harsh conditions. For example, Arctic offshore installations benefit from coatings that reduce ice adhesion, improving safety and reducing operational interruptions. In high-temperature desert environments, these coatings prevent moisture ingress, protecting steel structures from thermal stress and corrosion.
This capability to withstand diverse, challenging environments makes hydrophobic coatings a crucial investment for oil and gas operators looking to maximize asset longevity and operational continuity.
Technological Advancements Driving Innovation in Hydrophobic Coating for Oil & Gas Industry Market
Innovation plays a central role in shaping the Hydrophobic Coating for Oil & Gas Industry Market. The advent of nanotechnology has revolutionized coating performance by enabling ultra-thin, highly durable layers that deliver exceptional water repellency and chemical resistance.
For example, next-generation nano-coatings create microscopic surface textures that prevent water adhesion at a molecular level, vastly improving longevity and protective qualities. Furthermore, smart coatings that respond to environmental stimuli such as temperature and humidity changes are emerging, offering tailored protection and real-time self-healing capabilities.
These technological breakthroughs enhance the market by addressing evolving challenges and performance expectations, opening new application areas and increasing adoption rates across the oil and gas sector.
Environmental Compliance as a Catalyst in Hydrophobic Coating for Oil & Gas Industry Market Expansion
Increasing environmental regulations and sustainability mandates are driving demand within the Hydrophobic Coating for Oil & Gas Industry Market. Governments and industry bodies require oil and gas operators to minimize environmental risks, including emissions and contamination from infrastructure degradation.
Hydrophobic coatings contribute by reducing corrosion-related leaks and failures, thereby preventing environmental contamination. Additionally, the shift towards eco-friendly formulations—such as waterborne and low-VOC coatings—aligns with global efforts to reduce chemical pollutants.
For instance, operators are now selecting hydrophobic coatings that not only meet rigorous performance standards but also comply with evolving environmental guidelines. This dual focus on protection and sustainability accelerates market growth by aligning industry needs with regulatory frameworks.
Market Expansion Opportunities in Emerging Oil & Gas Regions Elevate Hydrophobic Coating for Oil & Gas Industry Market
Emerging oil and gas markets in Asia Pacific, Latin America, and parts of Africa present significant growth opportunities for the Hydrophobic Coating for Oil & Gas Industry Market. These regions are investing heavily in infrastructure development, including new offshore drilling projects, pipeline expansions, and refinery upgrades.
For example, Asia Pacific’s offshore oil exploration in regions like the South China Sea and India’s growing offshore reserves require durable hydrophobic coatings capable of withstanding tropical marine environments. Similarly, Latin America’s deepwater drilling activities off the coast of Brazil demand advanced protective coatings to combat intense saline corrosion.
These markets’ expansion, combined with rising industrialization and energy demand, positions the Hydrophobic Coating for Oil & Gas Industry Market for substantial growth as operators prioritize asset protection and lifecycle cost reduction.
Sectoral Adoption Driving Diverse Applications in Hydrophobic Coating for Oil & Gas Industry Market
The Hydrophobic Coating for Oil & Gas Industry Market sees widespread adoption across various subsectors including upstream exploration, midstream transportation, and downstream refining. Each sector faces unique environmental challenges that hydrophobic coatings address effectively.
In upstream operations, coatings protect offshore platforms and subsea equipment from saltwater corrosion and biofouling. Midstream pipelines benefit from coatings that prevent moisture ingress and ice formation, critical for maintaining flow and preventing leaks. Downstream refineries use hydrophobic coatings to safeguard processing units and storage tanks against chemical exposure and moisture-induced degradation.
This broad application spectrum ensures steady demand and encourages continuous innovation within the market to meet specific sectoral needs.
“Track Country-wise Hydrophobic Coating for Oil & Gas Industry Production and Demand through our Hydrophobic Coating for Oil & Gas Industry Production Database”
-
-
- Hydrophobic Coating for Oil & Gas Industry production database for 30+ countries worldwide
- Hydrophobic Coating for Oil & Gas Industry Powder sales volume for 31+ countries
- Country-wise Hydrophobic Coating for Oil & Gas Industry production capacity and production plant mapping, production capacity utilization for 30+ manufacturers
- Hydrophobic Coating for Oil & Gas Industry production plants and production plant capacity analysis for top manufacturers
-
Geographic Demand Dynamics Shaping the Hydrophobic Coating for Oil & Gas Industry Market
The Hydrophobic Coating for Oil & Gas Industry Market reveals significant regional disparities shaped by industrial growth, infrastructure development, and environmental conditions. North America stands as a dominant consumer driven by extensive offshore drilling, shale gas production, and aging infrastructure requiring refurbishment. For example, the U.S. Gulf Coast and Canadian oil sands fields heavily invest in hydrophobic coatings to mitigate corrosion from saltwater and chemical exposure. This region’s emphasis on technological innovation and stringent safety regulations propels the demand for high-performance hydrophobic coatings.
In contrast, Europe’s Hydrophobic Coating for Oil & Gas Industry Market is characterized by robust offshore exploration in the North Sea and a rising push toward sustainable, eco-friendly coating technologies. Countries like Norway and the UK prioritize waterborne and low-VOC hydrophobic coatings that combine performance with environmental compliance. The expansion of offshore wind energy infrastructure also stimulates demand for hydrophobic solutions adaptable to marine conditions.
Asia Pacific is emerging as the fastest-growing regional market for hydrophobic coatings in oil and gas, propelled by countries such as China, India, and Australia. For instance, China’s offshore oil exploration in the Bohai Bay and South China Sea requires advanced coatings resistant to saline corrosion and tropical humidity. India’s accelerating refinery expansions and pipeline networks demand durable hydrophobic coatings capable of withstanding monsoon moisture and high temperatures. Australia’s offshore natural gas platforms face harsh marine environments where hydrophobic coatings are vital for maintenance cost reduction and operational efficiency.
Production Landscape Influencing the Hydrophobic Coating for Oil & Gas Industry Market Growth
The Hydrophobic Coating for Oil & Gas Industry Market production is concentrated in regions with strong industrial bases and advanced chemical manufacturing capabilities. North America leads with established producers specializing in silicone, fluoropolymer, and epoxy-based hydrophobic coatings tailored for oil and gas infrastructure. Companies leverage cutting-edge R&D to produce coatings with enhanced corrosion resistance and temperature stability, meeting the exacting standards of offshore and onshore operations.
Europe’s production hubs, notably in Scandinavia and Germany, focus on sustainability-driven innovation. The Hydrophobic Coating for Oil & Gas Industry Market in this region is marked by the rise of eco-friendly formulations such as waterborne hydrophobic coatings, which reduce volatile organic compound emissions without compromising protective performance. Manufacturers here often supply both local operators and international markets, capitalizing on strong environmental regulations and high demand for green technologies.
Asia Pacific’s production capacity is rapidly expanding to meet growing regional demand. China dominates with significant investments in coating technology and manufacturing infrastructure, aiming to reduce dependence on imports of high-performance hydrophobic coatings. India and Australia are developing their production ecosystems, focusing on customized solutions that cater to local environmental challenges and regulatory frameworks. This regional production surge supports the broader Hydrophobic Coating for Oil & Gas Industry Market growth, enabling quicker delivery and cost efficiencies.
Market Segmentation Driving the Hydrophobic Coating for Oil & Gas Industry Market Expansion
The Hydrophobic Coating for Oil & Gas Industry Market segmentation is diverse, shaped by coating types, application areas, and end-use sectors. Silicone-based hydrophobic coatings lead the market segment due to their excellent water repellency, UV stability, and temperature resistance, making them ideal for offshore platforms and subsea equipment. For example, offshore rigs in the Gulf of Mexico utilize silicone coatings extensively to combat saltwater-induced corrosion and maintain structural integrity.
Fluoropolymer-based coatings follow closely, prized for their chemical inertness and low friction properties. These coatings find applications in pipelines and processing units where exposure to aggressive chemicals and hydrocarbons is routine. Their long-lasting nature reduces the frequency of recoating, contributing to lower lifecycle costs.
Epoxy-based hydrophobic coatings also play a crucial role, especially in protecting storage tanks and refinery equipment. Their strong adhesion and abrasion resistance suit environments with mechanical wear and chemical exposure. Emerging nano-coatings and waterborne hydrophobic coatings represent a fast-growing segment due to increasing environmental regulations and demand for sustainable solutions. These advanced coatings offer superior protection with minimal ecological impact.
Application-Based Market Segmentation in Hydrophobic Coating for Oil & Gas Industry Market
Application-wise, offshore oil and gas infrastructure accounts for a significant portion of the Hydrophobic Coating for Oil & Gas Industry Market demand. Offshore platforms, drilling rigs, pipelines, and subsea equipment operate in highly corrosive saltwater environments and require coatings that deliver long-term protection. For example, the North Sea’s offshore facilities use hydrophobic coatings to withstand cold, turbulent waters and reduce ice formation on surfaces.
Onshore applications, including pipelines, storage tanks, and refinery units, constitute another major segment. Pipelines, often exposed to moisture from soil and atmospheric conditions, benefit from hydrophobic coatings that prevent water ingress and corrosion. Storage tanks containing crude oil or chemicals demand robust coatings to avoid leaks and contamination, enhancing operational safety.
Subsea equipment, including valves, pumps, and control units in deepwater operations, face extreme pressure and corrosive conditions. Hydrophobic coatings with nano-engineered properties are increasingly applied here to provide durable, low-maintenance protection, critical for expensive and hard-to-access equipment.
Price Trends and Hydrophobic Coating for Oil & Gas Industry Price Analysis
The Hydrophobic Coating for Oil & Gas Industry Price and price trends have evolved with technological advancements and raw material cost fluctuations. Over recent years, the price trajectory has generally been upward, reflecting increased demand for high-performance coatings with superior durability and environmental compliance. For example, silicone and fluoropolymer-based coatings command premium prices due to their enhanced protective qualities and longer service life compared to traditional epoxy or acrylic coatings.
Raw material costs, including specialty polymers and nanomaterials, influence pricing significantly. Fluctuations in petrochemical feedstock prices impact production costs, which in turn affect the Hydrophobic Coating for Oil & Gas Industry Price. Despite these variations, the overall value proposition remains strong as operators prioritize total cost of ownership over upfront expenditure, given the extended asset life and reduced maintenance expenses that hydrophobic coatings deliver.
Emerging eco-friendly hydrophobic coatings tend to have a higher initial price point due to complex formulations and compliance testing. However, their growing adoption in regions with strict environmental regulations, such as Europe and North America, supports stable pricing and encourages further innovation.
Impact of Regional Raw Material Availability on Hydrophobic Coating for Oil & Gas Industry Price
Raw material sourcing plays a critical role in shaping the Hydrophobic Coating for Oil & Gas Industry Price and price trends globally. Regions with established petrochemical industries, such as the Middle East and North America, benefit from localized raw material supply chains, which help stabilize prices and ensure timely production.
Conversely, countries heavily reliant on imports of specialty chemicals, like some Asia Pacific nations, may experience price volatility due to logistical challenges and global trade disruptions. For example, fluctuations in fluoropolymer availability can impact the production cost of premium hydrophobic coatings, leading to temporary price increases in affected markets.
Manufacturers increasingly focus on optimizing formulations to reduce reliance on costly raw materials without compromising performance, aiming to balance competitive pricing with technological advancement.
Market Pricing Strategies in Hydrophobic Coating for Oil & Gas Industry Market
Pricing strategies in the Hydrophobic Coating for Oil & Gas Industry Market are increasingly value-driven, with manufacturers and suppliers emphasizing the long-term benefits of advanced coatings over initial cost considerations. For instance, premium hydrophobic coatings marketed for offshore applications highlight extended asset protection, reduced maintenance downtime, and compliance with environmental standards as key selling points justifying higher prices.
Bulk purchasing agreements and long-term supply contracts between coating producers and oil and gas operators help stabilize Hydrophobic Coating for Oil & Gas Industry Price, ensuring predictable cost structures in large-scale projects. Additionally, tiered pricing models based on application complexity and coating specifications allow for tailored solutions, expanding market accessibility while maintaining profitability.
Price Sensitivity and Demand Correlation in Hydrophobic Coating for Oil & Gas Industry Market
Demand elasticity in the Hydrophobic Coating for Oil & Gas Industry Market varies with sectoral requirements and economic cycles. In high-value applications such as offshore platforms and subsea equipment, price sensitivity is relatively low because the cost of failure far outweighs coating expenses. Operators prioritize reliability and durability, driving demand for premium coatings despite higher prices.
Conversely, onshore pipeline projects, especially in emerging markets with tighter budget constraints, exhibit higher price sensitivity. Here, cost-effective hydrophobic coatings with acceptable performance trade-offs gain traction, spurring the development of mid-range products.
This balance between price and performance shapes the market’s product portfolio and influences innovation pathways aimed at optimizing both cost and effectiveness.
Hydrophobic Coating for Oil & Gas Industry Market Outlook: Balancing Demand, Production, and Pricing
As the oil and gas industry advances into more challenging terrains and tighter regulatory environments, the Hydrophobic Coating for Oil & Gas Industry Market must navigate complex demand patterns, evolving production capacities, and dynamic pricing. Sustained investments in offshore exploration, particularly in Asia Pacific and Latin America, will continue to fuel demand growth. Simultaneously, production expansion in emerging economies aims to reduce supply chain vulnerabilities and support local market needs.
Price trends will likely reflect ongoing raw material costs, technological advancements, and environmental compliance pressures. The market’s ability to offer customized, durable, and sustainable hydrophobic coatings at competitive prices will be critical in capturing new opportunities and meeting the sector’s stringent operational demands.
“Hydrophobic Coating for Oil & Gas Industry Manufacturing Database, Hydrophobic Coating for Oil & Gas Industry Manufacturing Capacity”
-
-
- Hydrophobic Coating for Oil & Gas Industry top manufacturers market share for 30+ manufacturers
- Top 9 manufacturers and top 19 manufacturers of Hydrophobic Coating for Oil & Gas Industry in North America, Europe, Asia Pacific
- Production plant capacity by manufacturers and Hydrophobic Coating for Oil & Gas Industry production data for 30+ market players
- Hydrophobic Coating for Oil & Gas Industry production dashboard, Hydrophobic Coating for Oil & Gas Industry production data in excel format
-
Leading Manufacturers Shaping the Hydrophobic Coating for Oil & Gas Industry Market
The Hydrophobic Coating for Oil & Gas Industry Market is dominated by a mix of global chemical giants and specialized coating manufacturers who are continuously innovating to meet the demanding needs of oil and gas infrastructure. These companies hold substantial market shares through diversified product portfolios, advanced technologies, and extensive global distribution networks.
Among the foremost leaders is BASF SE, recognized for its high-performance hydrophobic coating solutions tailored specifically for the oil and gas sector. BASF’s product lines focus on silicone- and fluoropolymer-based coatings that excel in corrosion resistance and durability in offshore and onshore environments. Their coatings are engineered to withstand harsh marine conditions, extreme temperatures, and chemical exposure. BASF’s commitment to sustainability is evident in their development of low-VOC, waterborne hydrophobic coatings, which are gaining rapid traction in environmentally sensitive projects.
Another dominant player is PPG Industries, whose portfolio includes a range of epoxy and fluoropolymer hydrophobic coatings widely used in pipeline protection, storage tanks, and offshore platforms. PPG’s flagship products deliver exceptional adhesion and chemical resistance, ensuring long service life and reduced maintenance intervals. The company also emphasizes customizable solutions, allowing operators to specify coatings optimized for particular environmental challenges, such as high salinity or abrasive particulate exposure.
Sherwin-Williams is notable for its advanced hydrophobic coatings designed for subsea and deepwater oil and gas infrastructure. Their product offerings include nano-engineered coatings that provide enhanced water repellency and self-cleaning properties, minimizing biofouling and corrosion. Sherwin-Williams’ innovative coatings have been deployed in major offshore projects globally, reinforcing their market leadership in protecting subsea assets.
Jotun is a leading Scandinavian manufacturer that has carved a significant niche in the Hydrophobic Coating for Oil & Gas Industry Market through its marine and protective coatings expertise. Jotun’s product range includes silicone- and epoxy-based hydrophobic coatings engineered to resist saltwater corrosion and ice formation, particularly suitable for cold climates like the North Sea and Arctic regions. Their emphasis on environmentally friendly coatings with reduced volatile organic compounds aligns with Europe’s strict regulatory environment.
Hempel is another major European player focused on sustainable hydrophobic coating solutions that address the oil and gas sector’s environmental and operational needs. Their coatings are widely used in offshore drilling rigs, refineries, and pipeline networks. Hempel’s specialty lies in combining long-lasting protection with ease of application, helping reduce downtime and improve safety in oil and gas operations.
In the Asia Pacific region, Asian Paints and Chugoku Marine Paints are significant contributors to the Hydrophobic Coating for Oil & Gas Industry Market. Asian Paints has rapidly expanded its portfolio to include waterborne and nano-based hydrophobic coatings, responding to the region’s growing demand for corrosion protection in offshore and onshore oil fields. Chugoku Marine Paints, with decades of expertise in marine coatings, offers a range of hydrophobic products optimized for tropical and saline environments common to Asia Pacific offshore operations.
Manufacturer Market Share in the Hydrophobic Coating for Oil & Gas Industry Market
Market share distribution in the Hydrophobic Coating for Oil & Gas Industry Market is concentrated among these key players, each holding strategic positions due to their product innovation, regional presence, and customer base.
North American manufacturers, primarily BASF, PPG Industries, and Sherwin-Williams, collectively control a significant portion of the global market, estimated at nearly 40%. Their strength lies in advanced coating technologies that meet the rigorous demands of offshore and shale gas infrastructure in the United States and Canada.
European players such as Jotun and Hempel command approximately 25% of the market share, with their dominance rooted in the North Sea offshore oil activities and Europe’s regulatory push toward eco-friendly coatings. Their focus on sustainability and compliance with environmental standards gives them a competitive edge in the region.
Asia Pacific manufacturers, including Asian Paints and Chugoku Marine Paints, hold an increasing share approaching 20%, fueled by expanding oil and gas exploration and production activities in countries like China, India, and Australia. These companies benefit from local manufacturing capabilities and tailored solutions for the region’s diverse and challenging environments.
The remaining market share is distributed among regional and niche players in the Middle East, Latin America, and Africa, where emerging oil fields and infrastructural developments are creating new opportunities for hydrophobic coatings.
Product Lines and Innovations Among Hydrophobic Coating for Oil & Gas Industry Market Leaders
BASF’s flagship product lines, such as their Siloxane-based hydrophobic coatings, are designed to deliver superior resistance to saltwater corrosion and thermal degradation. Their “ProtectCoat” series offers long-term durability and ease of application on offshore platforms and subsea pipelines. BASF also integrates nanotechnology to enhance water repellency, ensuring minimal surface wetting and contamination.
PPG Industries’ “CorroShield” line is renowned for its epoxy and fluoropolymer coatings that provide excellent chemical and abrasion resistance. These coatings are tailored for harsh oil and gas environments, including refinery equipment and long-distance pipeline networks. PPG’s ongoing R&D efforts focus on enhancing self-healing capabilities and reducing coating thickness without compromising protection.
Sherwin-Williams’ “HydroGuard Nano” series represents a breakthrough in hydrophobic coatings, combining nano-engineered surfaces that repel water and prevent microbial growth. These coatings significantly reduce maintenance costs by minimizing biofouling on subsea equipment. Their products have been pivotal in deepwater projects in the Gulf of Mexico and offshore Brazil.
Jotun’s “SeaShield” line of silicone-based coatings is engineered for extreme cold and marine exposure, ideal for Arctic offshore platforms and North Sea rigs. Their coatings reduce ice adhesion and improve structural longevity under fluctuating temperatures. Jotun’s commitment to green chemistry is reflected in their eco-friendly waterborne “EcoProtect” hydrophobic coatings, popular in European offshore applications.
Hempel’s hydrophobic coatings such as “MarineX” and “AquaGuard” are designed to offer fast curing, high chemical resistance, and ease of maintenance for oil and gas assets. Their coatings are frequently used in refineries and storage tanks where chemical exposure and moisture intrusion pose constant threats.
Asian Paints’ “ShieldPro” range focuses on waterborne and nano-coatings suited for tropical offshore environments. Their coatings combine durability with environmental compliance, addressing challenges like monsoonal humidity and saline corrosion. Chugoku Marine Paints offers their “MarineShield” hydrophobic coatings tailored for the Asia Pacific marine oil sector, emphasizing high adhesion and abrasion resistance.
Recent Industry Developments and Market Player Updates
In 2024, several noteworthy developments have shaped the Hydrophobic Coating for Oil & Gas Industry Market landscape. BASF announced the launch of an advanced nanotechnology-based hydrophobic coating, promising extended asset life for offshore platforms while reducing environmental impact. This new product line, unveiled in early Q1 2024, aims to capture growing demand in North America and Asia Pacific.
PPG Industries recently expanded its manufacturing capacity in the U.S., focusing on fluoropolymer coatings designed for deepwater oil extraction. This strategic investment, completed in mid-2023, aligns with increasing offshore drilling activity in the Gulf of Mexico and supports faster delivery to key customers.
Sherwin-Williams secured a multi-year contract with a major subsea equipment operator to supply their HydroGuard Nano coatings, marking one of the largest deals in the subsea hydrophobic coating segment. This agreement, announced in late 2023, underscores the rising importance of biofouling prevention and corrosion protection in subsea infrastructure.
In Europe, Jotun’s partnership with offshore wind farm developers to supply environmentally friendly hydrophobic coatings signals a diversification of their application areas. The collaboration, initiated in early 2024, reflects the growing crossover between oil and gas and renewable energy sectors, particularly in harsh marine environments.
Hempel’s recent launch of a waterborne hydrophobic coating line compliant with the latest EU VOC regulations demonstrates the company’s commitment to sustainability. Released in late 2023, these coatings have quickly gained acceptance among European oil and gas operators seeking greener alternatives without sacrificing performance.
Asian Paints’ investment in a new research center dedicated to hydrophobic coatings innovation, opened in mid-2023, supports their regional expansion strategy. This facility focuses on developing cost-effective, durable coatings for the rapidly growing Indian and Southeast Asian oil and gas markets.
“Hydrophobic Coating for Oil & Gas Industry Production Data and Hydrophobic Coating for Oil & Gas Industry Production Trend, Hydrophobic Coating for Oil & Gas Industry Production Database and forecast”
-
-
- Hydrophobic Coating for Oil & Gas Industry production database for historical years, 10 years historical data
- Hydrophobic Coating for Oil & Gas Industry production data and forecast for next 9 years
-
Market Scenario, Demand vs Supply, Average Product Price, Import vs Export, till 2035
- Global Hydrophobic Coating for Oil & Gas Industry Market revenue and demand by region
- Global Hydrophobic Coating for Oil & Gas Industry Market production and sales volume
- United States Hydrophobic Coating for Oil & Gas Industry Market revenue size and demand by country
- Europe Hydrophobic Coating for Oil & Gas Industry Market revenue size and demand by country
- Asia Pacific Hydrophobic Coating for Oil & Gas Industry Market revenue size and demand by country
- Middle East & Africa Hydrophobic Coating for Oil & Gas Industry Market revenue size and demand by country
- Latin America Hydrophobic Coating for Oil & Gas Industry Market revenue size and demand by
- Import-export scenario – United States, Europe, APAC, Latin America, Middle East & Africa
- Average product price – United States, Europe, APAC, Latin America, Middle East & Africa
- Market player analysis, competitive scenario, market share analysis
- Business opportunity analysis
Key questions answered in the Global Hydrophobic Coating for Oil & Gas Industry Market Analysis Report:
- What is the market size for Hydrophobic Coating for Oil & Gas Industry in United States, Europe, APAC, Middle East & Africa, Latin America?
- What is the yearly sales volume of Hydrophobic Coating for Oil & Gas Industry and how is the demand rising?
- Who are the top market players by market share, in each product segment?
- Which is the fastest growing business/ product segment?
- What should be the business strategies and Go to Market strategies?
The report covers Hydrophobic Coating for Oil & Gas Industry Market revenue, Production, Sales volume, by regions, (further split into countries):
- Asia Pacific (China, Japan, South Korea, India, Indonesia, Vietnam, Rest of APAC)
- Europe (UK, Germany, France, Italy, Spain, Benelux, Poland, Rest of Europe)
- North America (United States, Canada, Mexico)
- Latin America (Brazil, Argentina, Rest of Latin America)
- Middle East & Africa
Table of Contents:
Hydrophobic Coating for Oil & Gas Industry Market Report
- Introduction to Hydrophobic Coatings for Oil & Gas Industry
- Definition and Characteristics of Hydrophobic Coatings
- Role and Importance of Hydrophobic Coatings in the Oil & Gas Industry
- Benefits of Hydrophobic Coatings for Oil & Gas Applications
- Market Overview
- Current Market Trends and Dynamics in the Oil & Gas Sector
- Key Drivers of Hydrophobic Coating Adoption in the Industry
- Challenges and Restraints in Market Growth
- Environmental Impact and Sustainability Considerations
- Hydrophobic Coating Applications in Oil & Gas
- Offshore and Onshore Drilling Equipment
- Corrosion Protection for Rig Components
- Anti-Fouling Applications for Subsea Equipment
- Pipelines and Storage Tanks
- Coatings for Preventing Water and Moisture Infiltration
- Anti-Corrosive Protection for Underground and Offshore Pipelines
- Surface and Subsurface Exploration Tools
- Coatings for Enhanced Durability and Performance in Harsh Environments
- Oilfield Pumps, Valves, and Fittings
- Preventing Scale and Corrosion in Critical Components
- Safety Equipment and Infrastructure
- Hydrophobic Coatings for Protective Gear and Critical Structures
- Types of Hydrophobic Coatings Used in the Oil & Gas Industry
- Fluoropolymer-Based Coatings
- Silicone and Silane-Based Hydrophobic Coatings
- Nanocoatings and Nanotechnology-Enhanced Coatings
- Polyurethane and Epoxy Coatings
- Ceramic and Hybrid Coatings
- Others: Graphene and Custom Coating Solutions
- Technological Developments and Innovations
- Nanotechnology in Hydrophobic Coating
- Advancements in Self-Cleaning Surfaces
- Enhanced Hydrophobicity and Longevity
- Smart Coatings for Predictive Maintenance
- Improved Durability and Resistance to High Temperatures and Pressures
- Innovations in Coating Application Methods
- Regional Market Analysis
6.1 North America
- Market Size and Trends in the U.S. and Canada
- Demand for Hydrophobic Coatings in Oil & Gas Exploration and Production
6.2 Europe
- Adoption and Growth of Hydrophobic Coatings in European Oil & Gas Operations
- Regulatory Considerations in the European Market
6.3 Asia-Pacific
- Growth Opportunities for Hydrophobic Coatings in APAC’s Oil & Gas Sector
- Key Challenges and Regional Market Potential
6.4 Middle East & Africa
- Emerging Markets for Hydrophobic Coatings in the Middle East and Africa
- Key Drivers and Regional Trends in Oil & Gas Production
6.5 Latin America
- Demand for Hydrophobic Coatings in Oil & Gas Activities in LATAM
- Economic Impact and Market Challenges in the Region
- Competitive Landscape and Key Market Players
- Market Share of Leading Hydrophobic Coating Providers for the Oil & Gas Industry
- Strategic Movements: Mergers, Acquisitions, and Partnerships
- Leading Manufacturers and Suppliers of Coatings for Oil & Gas
- Analysis of Industry Leaders’ Strengths and Market Position
- Cost and Manufacturing Insights
- Breakdown of Manufacturing Costs for Hydrophobic Coatings
- Key Raw Materials for Coating Production
- Pricing Trends in the Oil & Gas Coatings Market
- Supply Chain Analysis and Challenges in the Coatings Industry
- Regulatory and Compliance Overview
- Industry Regulations Governing Hydrophobic Coatings in Oil & Gas Operations
- Environmental Impact Assessments and Compliance Standards
- Safety Standards for Coatings in Harsh and Hazardous Environments
- Market Forecast and Projections
- Market Size and Growth Forecast (2025-2035)
- Projected Demand for Hydrophobic Coatings in Various Oil & Gas Applications
- Regional Market Growth and Expansion Projections
- Impact of Market Drivers and Barriers on Future Growth
- Hydrophobic Coating Performance Metrics
- Testing and Evaluation of Coating Efficacy in Oil & Gas Operations
- Key Performance Indicators (KPIs) for Coating Durability and Longevity
- Comparative Performance Analysis of Different Coating Technologies
- Environmental and Sustainability Considerations
- Eco-Friendly Coatings and Green Technologies in Oil & Gas
- Impact of Hydrophobic Coatings on Reducing Operational Costs and Carbon Footprint
- Sustainable Alternatives to Traditional Coatings in the Industry
- Challenges and Risks in Hydrophobic Coating Adoption
- Performance Degradation Under Extreme Environmental Conditions
- Cost and Availability of High-Quality Coatings
- Integration Issues in Existing Oil & Gas Infrastructure
- Addressing Industry-Specific Technical and Operational Challenges
- Future Outlook and Opportunities
- Market Opportunities for Hydrophobic Coatings in New Oil & Gas Exploration Frontiers
- Emerging Applications and Markets for Hydrophobic Coatings
- Investment Opportunities and Technological Advancements on the Horizon
- Conclusion
- Summary of Key Findings from the Market Report
- Strategic Recommendations for Industry Stakeholders
- Final Thoughts on the Future of Hydrophobic Coatings in the Oil & Gas Sector
Other recently published reports:
“Every Organization is different and so are their requirements”- Datavagyanik
Companies We Work With
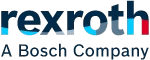
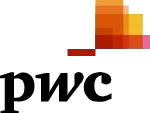
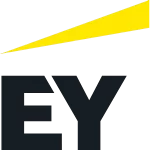
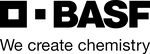
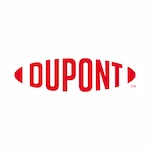

Do You Want To Boost Your Business?
drop us a line and keep in touch
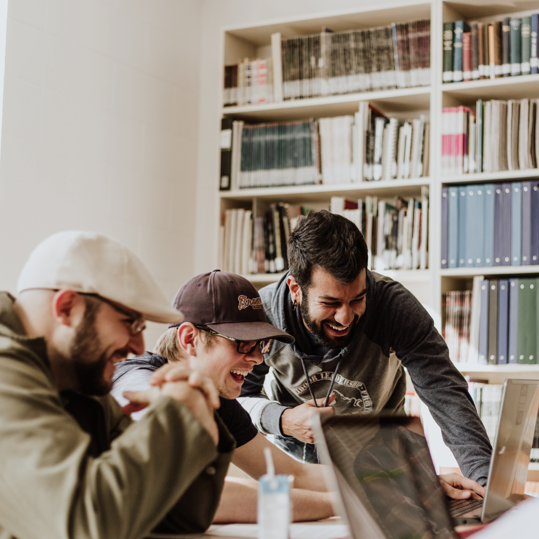