Lead-Free Solder Alloys for Electronics Market Size, Production, Sales, Average Product Price, Market Share, Import vs Export
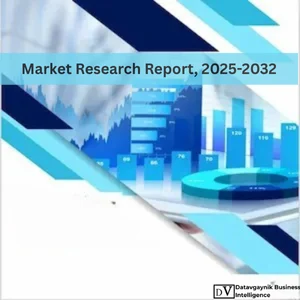
- Published 2025
- No of Pages: 120+
- 20% Customization available
Environmental Regulations Driving the Lead-Free Solder Alloys for Electronics Market
The Lead-Free Solder Alloys for Electronics Market is being significantly propelled by the global shift toward stricter environmental regulations. Governments across major industrial economies have imposed legally binding mandates to limit the use of hazardous substances, particularly lead, in electrical and electronic equipment. For instance, the European Union’s RoHS directive has played a crucial role in forcing manufacturers to eliminate lead content in electronics sold within its jurisdiction. Similarly, countries such as Japan, China, and the United States have introduced parallel regulatory standards, accelerating the transition to lead-free materials.
This regulatory landscape is not just influencing domestic policy but is shaping international trade. Exporters from Asia, including Vietnam, India, and Taiwan, are increasingly aligning their production processes to meet the standards set by the EU and US markets. As compliance becomes essential for market access, the Lead-Free Solder Alloys for Electronics Market is seeing increased investment in compliant materials and technologies, particularly in regions with high manufacturing intensity.
Rise of Green Electronics Accelerates Adoption in Global Manufacturing
Global manufacturing is undergoing a major transition toward green and sustainable production. The Lead-Free Solder Alloys for Electronics Market is a key beneficiary of this shift. For instance, the global production of smartphones, which crossed 1.2 billion units in 2023, is largely dependent on materials that meet stringent environmental and safety standards. Major electronics manufacturers including Apple, Samsung, and Dell have adopted comprehensive green sourcing policies that mandate the use of lead-free solder in circuit boards and electronic assemblies.
This move is not only regulatory-driven but also closely tied to brand reputation and consumer perception. As sustainability becomes a decisive factor in purchasing behavior, electronics companies are forced to meet expectations by adopting safer, recyclable materials. In this context, lead-free solder alloys—primarily composed of tin, silver, and copper—are emerging as the industry norm. The Lead-Free Solder Alloys for Electronics Market is thus deeply intertwined with the broader evolution of sustainable electronics manufacturing.
Datavagyanik also covers related markets such as the Lead-free PVC stabilizers Market. These related markets contribute valuable context to the primary topic by highlighting complementary trends and technologies.
Technological Advancements Improve Performance of Lead-Free Alloys
Historically, lead-based solders were preferred for their low melting points and reliable wetting characteristics. However, recent advancements in metallurgy and materials science have significantly improved the reliability and thermal performance of lead-free alternatives. Alloys such as SAC305, comprising 96.5% tin, 3% silver, and 0.5% copper, have become the de facto standard in many applications due to their mechanical strength and fatigue resistance.
For example, SAC-based alloys are now widely used in automotive electronic control units, where resistance to vibration and high temperatures is critical. In aerospace, where reliability under thermal cycling is a must, lead-free solder compositions with minor additions of antimony and bismuth are proving effective. These innovations are not only enhancing the performance of electronic systems but also contributing to a growing preference for lead-free options. As a result, the Lead-Free Solder Alloys for Electronics Market is increasingly viewed not just as a compliance necessity but as a high-performance solution.
Consumer Electronics Segment Leads Market Demand
The consumer electronics sector accounts for a dominant share in the Lead-Free Solder Alloys for Electronics Market. In 2024, consumer electronics represented nearly 42% of total global demand for lead-free solder alloys. This is driven by mass production of smartphones, laptops, smart TVs, and wearables—all of which require high-density circuit boards with reliable soldering.
As consumer expectations around sustainability and safety evolve, companies like HP, Lenovo, and Xiaomi are expanding their lead-free product lines. The transition is particularly pronounced in high-growth markets such as Southeast Asia, Latin America, and Eastern Europe, where manufacturing activity is expanding and local regulations are aligning with international standards. In these regions, demand for affordable but compliant solder materials is pushing suppliers to scale operations rapidly.
Automotive Electronics Fuel Market Expansion with High-Reliability Needs
Another key growth driver for the Lead-Free Solder Alloys for Electronics Market is the automotive sector. With the global electric vehicle market expected to reach over 40 million units annually by 2030, the need for durable, heat-resistant electronic components is surging. Applications such as battery management systems, infotainment modules, and advanced driver-assistance systems (ADAS) require solder alloys capable of withstanding extended thermal cycles and mechanical stress.
Lead-free solder alloys are increasingly being chosen for their robust thermal fatigue performance and environmental compliance. Automakers including Tesla, Toyota, Volkswagen, and BYD are partnering with component suppliers to ensure all in-vehicle electronics are RoHS-compliant. The growing sophistication of in-vehicle electronics, combined with rising pressure to meet environmental targets, is making lead-free alloys a standard in automotive design.
Lead-Free Solder Alloys for Electronics Market Size Reflects Global Shift
The Lead-Free Solder Alloys for Electronics Market Size has shown consistent growth over the past decade and is expected to continue this trajectory. Based on estimates from Datavagyanik, the global market size surpassed USD 2.8 billion in 2023 and is projected to grow at a compound annual growth rate (CAGR) exceeding 6.5% through 2030. This growth reflects a multi-sectoral adoption pattern that includes not only consumer and automotive electronics but also medical devices, telecommunications, and industrial control systems.
This momentum is further supported by regional policy shifts. In the United States, the Environmental Protection Agency (EPA) has increased oversight of lead usage in manufacturing, indirectly boosting demand for lead-free solutions. In China, the Ministry of Industry and Information Technology has introduced targets to reduce toxic substances in electronics, reinforcing the long-term outlook for lead-free materials.
Medical and Industrial Electronics Open High-Growth Avenues
The Lead-Free Solder Alloys for Electronics Market is also finding new opportunities in sectors with stringent safety and reliability standards, such as medical and industrial electronics. Medical device manufacturers are increasingly shifting to biocompatible, lead-free solder materials for use in implants, imaging equipment, and diagnostic systems. The FDA and other global regulatory bodies now require compliance with lead-free standards for a broad range of medical electronic products.
In industrial electronics, applications such as factory automation, renewable energy systems, and heavy-duty power modules demand durable solder joints. Lead-free alloys are proving their worth in this space by offering excellent thermal stability and resistance to electrochemical migration. With the rise of Industry 4.0 and smart manufacturing, the integration of lead-free solder into high-reliability electronics is becoming a norm, not an exception.
Supply Chain Expansion and Localized Manufacturing Strategies
To meet growing global demand, manufacturers in the Lead-Free Solder Alloys for Electronics Market are expanding capacity and establishing new production bases. Companies such as Kester, Senju Metal Industry, and Alpha Assembly Solutions are investing in localized manufacturing facilities in Mexico, Poland, and Southeast Asia to reduce supply chain risks and meet regional demand efficiently.
This trend toward localization is also driven by geopolitical shifts and trade barriers, which are encouraging companies to diversify sourcing and reduce dependence on a single region. For example, the US-China trade tensions have led many North American electronics firms to source solder materials from Vietnam or Malaysia, where manufacturers have upgraded capabilities to produce high-purity lead-free alloys.
Innovation in Alloy Composition and Process Optimization
Research and development are central to the evolution of the Lead-Free Solder Alloys for Electronics Market. Advanced formulations incorporating microalloying elements such as nickel, germanium, and indium are being tested to further enhance wettability, reduce oxidation, and increase mechanical performance. These innovations are especially valuable in miniaturized electronics and high-density interconnect (HDI) boards, where solder performance directly affects product lifespan.
Simultaneously, improvements in reflow soldering techniques and the development of fluxes compatible with lead-free alloys are streamlining manufacturing processes. This has helped mitigate earlier challenges such as void formation and lower joint strength, enabling broader application of lead-free solder in precision electronics.
“Track Country-wise Lead-Free Solder Alloys for Electronics Production and Demand through our Lead-Free Solder Alloys for Electronics Production Database”
-
- Lead-Free Solder Alloys for Electronics production database for 28+ countries worldwide
- Lead-Free Solder Alloys for Electronics Powder sales volume for 32+ countries
- Country-wise Lead-Free Solder Alloys for Electronics production capacity and production plant mapping, production capacity utilization for 28+ manufacturers
- Lead-Free Solder Alloys for Electronics production plants and production plant capacity analysis for top manufacturers
Asia Pacific Leads Global Demand in the Lead-Free Solder Alloys for Electronics Market
Asia Pacific has firmly established itself as the epicenter of growth in the Lead-Free Solder Alloys for Electronics Market. As per Datavagyanik’s analysis, over 55% of the global demand is concentrated in this region, primarily due to the dominance of electronics manufacturing hubs in China, Japan, South Korea, and Taiwan. For example, China alone accounts for more than 30% of global electronics output, driving continuous demand for high-performance soldering materials.
The transition toward lead-free soldering in China has been accelerated by government policy under the “Made in China 2025” initiative, which promotes greener manufacturing practices. Similarly, in Japan, the presence of advanced semiconductor manufacturers and automotive electronics producers, such as Toyota and Sony, supports a mature and innovation-driven market for lead-free alloys. In South Korea, companies like Samsung and LG are leading adopters of tin-silver-copper-based alloys for mobile devices and smart appliances. These countries not only consume large volumes but are also heavily involved in R&D aimed at alloy performance optimization.
North America Embraces High-Reliability Applications in Lead-Free Solder Alloys for Electronics Market
The North American Lead-Free Solder Alloys for Electronics Market is characterized by demand from high-reliability sectors such as aerospace, defense, automotive, and medical electronics. The United States, in particular, has seen a substantial increase in the use of lead-free materials, driven by both federal regulation and industry-led sustainability initiatives.
For instance, Boeing and Lockheed Martin have shifted toward lead-free solutions in non-critical and even some high-reliability applications. Additionally, the rise of electric vehicles in the US market—with EV sales growing over 40% year-on-year in 2023—has increased the consumption of solder alloys that offer superior thermal and mechanical stability. Automotive manufacturers including General Motors and Tesla have adopted advanced soldering materials to meet internal environmental targets and compliance standards such as IPC-J-STD-006 for solder alloy quality. This specialized demand positions North America as a strategic market for premium-grade alloys.
Europe Drives Sustainable Production in the Lead-Free Solder Alloys for Electronics Market
Europe has long been at the forefront of sustainable electronics manufacturing, and its leadership continues in the Lead-Free Solder Alloys for Electronics Market. Germany, France, the UK, and the Nordics are collectively responsible for over 20% of global demand, with a focus on low-toxicity, high-durability materials. German automotive giants like Volkswagen and BMW mandate lead-free compliance for suppliers across their EV value chains.
In France, the defense and medical electronics industries are growing contributors to demand. Companies like Safran and Thales have increasingly relied on SAC and Sn-Bi alloys in mission-critical assemblies. Meanwhile, the UK’s focus on green electronics has resulted in public funding for innovation in recyclable and biodegradable soldering materials. As electronics production returns to Europe under the EU’s strategic autonomy goals, regional consumption of lead-free alloys is expected to rise by over 6% CAGR through 2030, based on projections by Datavagyanik.
Emerging Economies Fuel Next Wave of Demand in the Lead-Free Solder Alloys for Electronics Market
While developed markets lead in volume and innovation, emerging economies are showing strong momentum in the Lead-Free Solder Alloys for Electronics Market. India, Brazil, Vietnam, and Mexico are experiencing rapid growth in electronics assembly, especially in consumer electronics and automotive components.
India, for instance, has witnessed a 25% annual increase in smartphone manufacturing output between 2021 and 2023. Government programs such as “Make in India” and the Production-Linked Incentive (PLI) scheme have brought global players into local manufacturing, accelerating the need for RoHS-compliant materials. In Vietnam, major contract manufacturers such as Foxconn and Pegatron have expanded capacity for lead-free PCB assembly to support brands seeking China+1 alternatives.
As these markets industrialize and comply with global export norms, their consumption of advanced solder alloys is expected to increase substantially, creating new demand pockets across the Lead-Free Solder Alloys for Electronics Market.
Market Segmentation by Alloy Type Reveals Preference for SAC Alloys
In terms of material composition, the Lead-Free Solder Alloys for Electronics Market is segmented primarily into Tin-Silver-Copper (SAC), Tin-Copper (Sn-Cu), Tin-Silver (Sn-Ag), and niche variants such as Tin-Bismuth (Sn-Bi) and Tin-Zinc (Sn-Zn). Among these, SAC alloys—particularly SAC305—account for over 60% of global consumption due to their ideal balance of melting point, thermal fatigue resistance, and mechanical strength.
For example, SAC305, with its melting range around 217–221°C, has become the standard alloy in surface-mount technology (SMT) processes. It is widely used in smartphone PCB assembly, automotive ECUs, and LED lighting systems. On the other hand, Sn-Cu alloys are preferred for wave soldering and lower-cost applications due to their simplicity and cost-efficiency.
The adoption of Sn-Bi alloys is increasing in applications where low-temperature soldering is essential, such as in flexible electronics and wearable devices. These alloys are valued for their reduced thermal stress on sensitive substrates. This diversification of materials is helping manufacturers tailor solutions to specific reliability, cost, and processing requirements across the Lead-Free Solder Alloys for Electronics Market.
Application-Based Segmentation Highlights Broad Industry Integration
From consumer electronics to aerospace, the Lead-Free Solder Alloys for Electronics Market serves a wide array of industries. Consumer electronics remains the largest segment, contributing nearly 40% of total volume. Applications include mobile phones, laptops, gaming consoles, and smart appliances—each requiring dense interconnects and high-throughput soldering processes.
The automotive segment is the second-largest, driven by the global shift toward electric mobility and connected vehicles. With EV production expected to exceed 15 million units annually by 2027, the demand for high-reliability lead-free solders in battery systems, inverters, and thermal management units is increasing.
Medical electronics also present a growing niche. Implantable devices and diagnostic systems require biocompatible, corrosion-resistant solder materials. As global healthcare electronics spending rises, demand in this segment is growing at a projected CAGR of 7.2% through 2030, according to Datavagyanik.
Global Production and Supply Chain Developments in the Lead-Free Solder Alloys for Electronics Market
The production landscape for the Lead-Free Solder Alloys for Electronics Market is highly consolidated among a few global players but increasingly supported by regional manufacturing expansions. Key producers include Senju Metal Industry (Japan), Kester (USA), Alpha Assembly Solutions (Global), and Indium Corporation. These firms control a significant share of alloy formulation and innovation pipelines.
Regional manufacturing is expanding in strategic zones. For instance, Malaysia, Mexico, and Poland have become attractive production bases due to trade accessibility, skilled labor, and favorable regulatory frameworks. With rising logistics costs and geopolitical uncertainties, OEMs are encouraging suppliers to build closer to final assembly plants, promoting a shift toward decentralized alloy production hubs.
Lead-Free Solder Alloys for Electronics Price Driven by Raw Material Costs and Alloy Composition
Lead-Free Solder Alloys for Electronics Price is largely influenced by fluctuations in the global prices of tin, silver, and copper—the primary constituents. For example, in early 2024, tin prices hovered around USD 25,000 per metric ton, up by nearly 18% compared to the previous year. This has directly impacted the Lead-Free Solder Alloys for Electronics Price Trend, particularly for high-silver content alloys like SAC305.
Additionally, the use of precious metals such as silver, which contributes to better wetting and mechanical properties, significantly raises material costs. As a result, manufacturers often tailor compositions to reduce silver content where performance allows, creating alloy variants like SAC105 or low-silver SACX series. These modifications help manage the Lead-Free Solder Alloys for Electronics Price while maintaining product quality.
Moreover, regional pricing differs based on transportation costs, local taxes, and supplier presence. In Europe and North America, prices are typically higher due to stricter quality standards and regulatory compliance costs. In contrast, bulk production in China and Southeast Asia allows for more competitive pricing, especially in consumer-grade applications.
Lead-Free Solder Alloys for Electronics Price Trend Reflects Balance of Demand and Innovation
The Lead-Free Solder Alloys for Electronics Price Trend reflects not only raw material inputs but also technological innovations and supply chain dynamics. For example, the introduction of micro-alloyed formulations with trace elements like nickel or germanium, while slightly more expensive, enhances long-term reliability and reduces total cost of ownership for industrial buyers.
Furthermore, economies of scale in large contract manufacturing environments have helped moderate price increases. Companies like Foxconn and Flex are negotiating long-term supply agreements, which allow for greater stability in Lead-Free Solder Alloys for Electronics Price over extended production cycles.
Datavagyanik anticipates that while raw material price volatility will persist, technological improvements and regional supply chain integration will help stabilize the Lead-Free Solder Alloys for Electronics Price Trend over the next five years, especially in mid- to high-volume application areas.
“Lead-Free Solder Alloys for Electronics Manufacturing Database, Lead-Free Solder Alloys for Electronics Manufacturing Capacity”
-
-
- Lead-Free Solder Alloys for Electronics top manufacturers market share for 28+ manufacturers
- Top 8 manufacturers and top 18 manufacturers of Lead-Free Solder Alloys for Electronics in North America, Europe, Asia Pacific
- Production plant capacity by manufacturers and Lead-Free Solder Alloys for Electronics production data for 28+ market players
- Lead-Free Solder Alloys for Electronics production dashboard, Lead-Free Solder Alloys for Electronics production data in excel format
-
Key Manufacturers Shaping the Lead-Free Solder Alloys for Electronics Market
The Lead-Free Solder Alloys for Electronics Market is consolidated among a handful of global players who dominate both production capacity and innovation pipelines. These manufacturers have built extensive portfolios of solder alloys catering to diverse end-use industries, ranging from consumer electronics and automotive to aerospace and medical devices. Their strong technical expertise, global supply chains, and R&D capabilities give them a competitive advantage, enabling them to lead market trends and meet complex client requirements.
Senju Metal Industry Co., Ltd. – A Global Pioneer in Lead-Free Innovation
Senju Metal Industry, headquartered in Japan, is widely recognized as one of the most influential players in the Lead-Free Solder Alloys for Electronics Market. The company holds a significant global market share, with manufacturing bases in Japan, China, Malaysia, and the United States. Senju’s lead-free solder product line, including the Senju M705 series, is extensively used in applications requiring high thermal and mechanical reliability. The M705 alloy, based on SAC formulations, is preferred in high-performance automotive and industrial electronics.
Senju has also developed specialized alloys such as SMIC705-G for low-void performance and SMIC701 for high-speed soldering. These product lines have gained traction in automotive ECUs, powertrain control modules, and high-frequency consumer electronics. With continuous investments in process automation and alloy innovation, Senju continues to hold a strong position in Asia Pacific and has been expanding its footprint in North America and Europe.
Kester – Leading North American Supplier in High-Reliability Segments
Kester, a leading American manufacturer, commands a strong position in the Lead-Free Solder Alloys for Electronics Market, particularly within North America. The company’s Ultrapure K100LD and Kester NXG1 are widely adopted by OEMs and EMS providers for both consumer and industrial electronics. These lead-free alloys offer enhanced wettability and reduced dross formation, making them highly efficient for both wave and selective soldering applications.
Kester also serves the aerospace and defense sectors, offering solder products that comply with high-reliability military standards. Its Lead-Free No-Clean Solder Wire series has been deployed in medical imaging equipment and avionics, where joint reliability and low ionic contamination are critical. With strategic distribution partnerships in Mexico and Canada, Kester continues to gain share in automotive and telecommunications electronics.
Indium Corporation – High-Performance Lead-Free Solutions for Advanced Applications
Indium Corporation has built a strong reputation for providing high-performance solder materials tailored to demanding electronics applications. Known for its Indalloy range, the company offers a wide variety of lead-free alloys including Indalloy 241 (Sn42/Bi58) and Indalloy 217 (SAC305). These are extensively used in servers, data centers, medical electronics, and RF systems.
One of Indium’s standout developments is its Durafuse LT alloy technology, which delivers low-temperature processing combined with high-melting durability—an ideal match for wearable and IoT devices. The company also specializes in engineered solders for semiconductor packaging, where voiding, electromigration, and thermal cycling are major concerns. Indium has established a substantial market share in both North America and Asia, supported by facilities in the US, China, Malaysia, and South Korea.
Alpha Assembly Solutions – A Dominant Force in Volume Manufacturing
Alpha Assembly Solutions, part of MacDermid Alpha Electronics Solutions, operates one of the largest global networks for solder materials. The company’s Alpha SACX Plus series, available in multiple silver-content variants (SACX0307, SACX0807), is widely used in high-volume consumer electronics manufacturing due to its cost-effectiveness and stable performance.
Alpha’s CVP-390 and CVP-520 solder pastes have also become benchmarks in applications involving high-speed surface mount technology (SMT) and reflow soldering. These products are optimized for void reduction, printability, and thermal stability. Alpha continues to grow its presence in India, Southeast Asia, and Eastern Europe, supplying to contract manufacturers such as Foxconn, Jabil, and Flex. With production facilities in over 20 countries, Alpha holds a leading position in the global Lead-Free Solder Alloys for Electronics Market.
Tamura Corporation – Reliable Supplier for Automotive and Power Electronics
Tamura Corporation, based in Japan, is another major player in the Lead-Free Solder Alloys for Electronics Market with a strong focus on automotive and industrial applications. Tamura’s LSC and LSM series lead-free solders are used in hybrid vehicle control units and battery monitoring systems. The company also offers proprietary flux technologies that ensure high joint reliability under thermal cycling.
Tamura’s extensive research in halogen-free fluxes and corrosion-resistant alloys has positioned it as a preferred supplier for green electronics and clean-room assembly environments. With new investments in Southeast Asia and a growing presence in the European market, Tamura is gaining momentum in power electronics and renewable energy systems.
Market Share Distribution Among Key Players
Datavagyanik estimates the current global market share in the Lead-Free Solder Alloys for Electronics Market as follows:
- Senju Metal Industry – 19%
- Alpha Assembly Solutions – 17%
- Kester – 12%
- Indium Corporation – 10%
- Tamura Corporation – 8%
- Others (regional and niche players) – 34%
The remaining share is fragmented among regional suppliers, including Nihon Superior (Japan), Vital New Material (China), Balver Zinn (Germany), and small-scale local producers who serve country-specific demands in Brazil, Turkey, and Eastern Europe.
These regional companies often compete on price and customization, offering proprietary alloys for niche applications like LED packaging, photovoltaics, and low-temperature electronics. However, the global leaders dominate in terms of volume, quality assurance, and compliance with international standards.
Recent Developments in the Lead-Free Solder Alloys for Electronics Market
In recent months, the Lead-Free Solder Alloys for Electronics Market has seen several key developments that reflect shifting dynamics in both demand and innovation:
- January 2024: Alpha Assembly Solutions launched a new version of SACX Plus 0807HF, designed to reduce voiding in high-density PCBs used in AI server modules.
- March 2024: Senju Metal Industry announced the expansion of its Malaysian production facility to meet rising demand for automotive-grade lead-free solders in Southeast Asia.
- April 2024: Indium Corporation introduced the Durafuse HT series for high-temperature applications, targeting aerospace and automotive powertrain electronics.
- February 2024: Kester entered a joint venture with a Brazilian electronics manufacturer to localize production of its K100LD alloy, aiming to reduce import costs and lead times in Latin America.
These strategic initiatives underline a common direction: aligning manufacturing closer to consumption centers, reducing lead times, and innovating around energy efficiency, miniaturization, and thermal management.
“Lead-Free Solder Alloys for Electronics Production Data and Lead-Free Solder Alloys for Electronics Production Trend, Lead-Free Solder Alloys for Electronics Production Database and forecast”
-
-
- Lead-Free Solder Alloys for Electronics production database for historical years, 10 years historical data
- Lead-Free Solder Alloys for Electronics production data and forecast for next 7 years
-
Market Scenario, Demand vs Supply, Average Product Price, Import vs Export, till 2035
- Global Lead-Free Solder Alloys for Electronics Market revenue and demand by region
- Global Lead-Free Solder Alloys for Electronics Market production and sales volume
- United States Lead-Free Solder Alloys for Electronics Market revenue size and demand by country
- Europe Lead-Free Solder Alloys for Electronics Market revenue size and demand by country
- Asia Pacific Lead-Free Solder Alloys for Electronics Market revenue size and demand by country
- Middle East & Africa Lead-Free Solder Alloys for Electronics Market revenue size and demand by country
- Latin America Lead-Free Solder Alloys for Electronics Market revenue size and demand by
- Import-export scenario – United States, Europe, APAC, Latin America, Middle East & Africa
- Average product price – United States, Europe, APAC, Latin America, Middle East & Africa
- Market player analysis, competitive scenario, market share analysis
- Business opportunity analysis
Key questions answered in the Global Lead-Free Solder Alloys for Electronics Market Analysis Report:
- What is the market size for Lead-Free Solder Alloys for Electronics in United States, Europe, APAC, Middle East & Africa, Latin America?
- What is the yearly sales volume of Lead-Free Solder Alloys for Electronics and how is the demand rising?
- Who are the top market players by market share, in each product segment?
- Which is the fastest growing business/ product segment?
- What should be the business strategies and Go to Market strategies?
The report covers Lead-Free Solder Alloys for Electronics Market revenue, Production, Sales volume, by regions, (further split into countries):
- Asia Pacific (China, Japan, South Korea, India, Indonesia, Vietnam, Rest of APAC)
- Europe (UK, Germany, France, Italy, Spain, Benelux, Poland, Rest of Europe)
- North America (United States, Canada, Mexico)
- Latin America (Brazil, Argentina, Rest of Latin America)
- Middle East & Africa
Table of Contents:
Lead-Free Solder Alloys for Electronics Market
- Introduction to Lead-Free Solder Alloys
-
- Overview and Importance of Lead-Free Solder Alloys
- Transition from Lead-Based to Lead-Free Alternatives
- Market Drivers and Challenges
-
- Environmental and Regulatory Drivers
- Technical Challenges in Adoption
- Types of Lead-Free Solder Alloys
-
- Tin-Silver-Copper (SAC) Alloys
- Tin-Copper Alloys
- Tin-Silver Alloys
- Novel Alloy Compositions
- Global Market Size and Forecast (2020–2035)
-
- Historical Analysis (2020–2024)
- Market Growth Projections and Influencing Factors
- Regional Market Analysis: North America
-
- Production and Revenue Insights
- Key End-User Industries
- Regional Market Analysis: Europe
-
- Adoption of Lead-Free Solders in Automotive and Electronics
- Regulatory Impact on the Market
- Regional Market Analysis: Asia-Pacific
-
- Manufacturing Hubs and Supply Chains
- Role of Emerging Economies in Market Expansion
- Regional Market Analysis: Latin America
-
- Opportunities in the Consumer Electronics Sector
- Market Barriers and Growth Potential
- Regional Market Analysis: Middle East & Africa
-
- Demand from Emerging Electronics Markets
- Challenges in Local Manufacturing
- Applications of Lead-Free Solder Alloys
- Consumer Electronics
- Automotive Electronics
- Aerospace and Defense Electronics
- Medical Devices
- Competitive Landscape and Key Players
- Profiles of Major Companies in the Market
- Strategic Initiatives: Partnerships, Mergers, and R&D
- Manufacturing Processes of Lead-Free Solder Alloys
- Key Techniques and Advancements
- Efficiency Improvements in Production
- Raw Material Supply Chain
- Sourcing of Key Materials (Tin, Silver, Copper, etc.)
- Supply Chain Challenges and Solutions
- Cost Structure Analysis
- Material, Labor, and Manufacturing Costs
- Trends in Cost Reduction
- Technological Innovations in Lead-Free Solders
- New Alloy Compositions for Improved Performance
- Role of Nanotechnology in Solder Development
- Environmental Impact of Lead-Free Solder Alloys
- Reduction of E-Waste Toxicity
- Sustainability in Production and Recycling
- Regulatory Landscape
- RoHS and WEEE Compliance
- Regional Regulations and Their Impacts
- Adoption Trends by Industry
- Electronics Manufacturing Services (EMS)
- Original Equipment Manufacturers (OEMs)
- Global Import-Export Trends
- Trade Flow Analysis by Region
- Major Exporting and Importing Countries
- Price Analysis and Trends (2020–2035)
- Price Fluctuations of Key Alloy Materials
- Regional Variations in Pricing
- Lead-Free Solder Alloys for Advanced Electronics
- Use in High-Reliability Electronics
- Applications in 5G and IoT Devices
- Consumer Trends and Insights
- Preferences for Sustainable Electronics
- Challenges in Transition to Lead-Free Solders
- Impact of Technological Advancements on Market Growth
- Integration with Advanced Manufacturing Techniques
- Development of Flexible and Miniaturized Electronics
- Investment Landscape
- Key Funding and R&D Investments
- Public and Private Sector Support
- Opportunities in Emerging Markets
- Demand for Solder Alloys in Developing Economies
- Growth of Local Electronics Manufacturing
- Supply Chain and Logistics
- Distribution Channels and Regional Availability
- Innovations in Solder Delivery Methods
- Marketing Strategies for Lead-Free Solder Alloys
- Approaches for Promoting Sustainable Products
- Market Education Initiatives
- Case Studies of Successful Transitions to Lead-Free Solder
- Lessons from Key Industry Leaders
- Overcoming Adoption Barriers
- Challenges and Risk Mitigation Strategies
- Technical Limitations in Solder Performance
- Supply Chain Risks and Contingencies
- Future Market Trends and Innovations
- Emerging Applications in AI and Quantum Electronics
- Long-Term Projections for Market Expansion
- Regional Production and Demand Forecast (2025–2035)
- North America
- Europe
- Asia-Pacific
- Latin America
- Middle East & Africa
- Impact of Recycling on the Lead-Free Solder Market
- Opportunities in Alloy Recovery and Reuse
- Challenges in Recycling Processes
- Partnerships and Collaborations
- Alliances Between Manufacturers and Electronics Companies
- Role of Research Institutions in Market Development
- Conclusion and Strategic Recommendations
- Key Insights from the Analysis
- Strategic Roadmap for Market Participants
“Every Organization is different and so are their requirements”- Datavagyanik
Companies We Work With
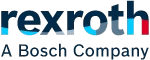
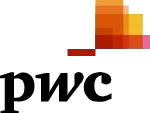
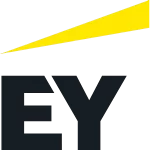
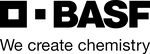
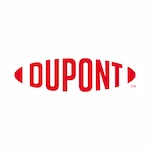

Do You Want To Boost Your Business?
drop us a line and keep in touch
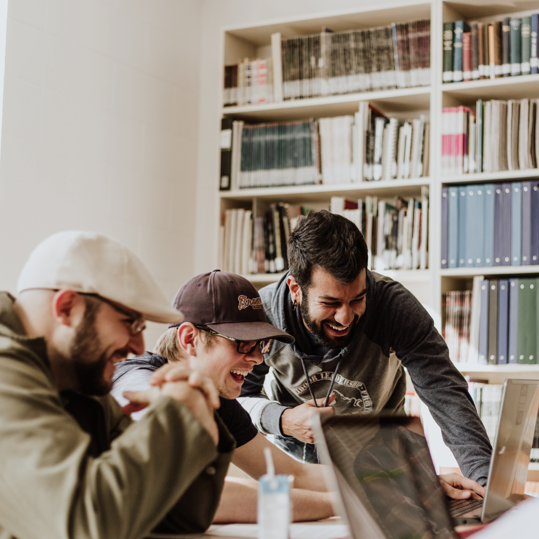