Metal Wires & Strips for Medical Device Manufacturing Market Size, Production, Sales, Average Product Price, Market Share, Import vs Export
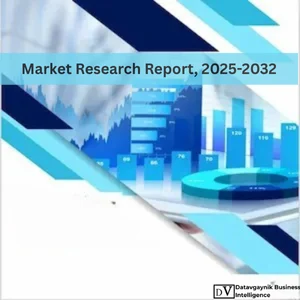
- Published 2025
- No of Pages: 120+
- 20% Customization available
Rising Demand for Minimally Invasive Surgeries Boosting the Metal Wires & Strips for Medical Device Manufacturing Market
The Metal Wires & Strips for Medical Device Manufacturing Market is experiencing a significant surge, driven by the exponential growth of minimally invasive procedures. As global healthcare systems prioritize patient outcomes, quicker recovery, and reduced hospital stays, the adoption of technologies that support such procedures has become critical. Devices like catheters, endoscopes, and stents—core to these interventions—rely heavily on precision-engineered metal wires and strips. The number of minimally invasive surgeries performed globally has risen by over 15% annually over the last five years, directly influencing the increased consumption of fine medical-grade wires and strips across various applications.
In procedures such as balloon angioplasty, neurovascular stenting, and laparoscopy, the demand for ultra-fine yet mechanically strong components is non-negotiable. This has positioned the Metal Wires & Strips for Medical Device Manufacturing Market as a foundational element of surgical innovation.
Accelerated Innovation in Medical Devices Powering the Metal Wires & Strips for Medical Device Manufacturing Market
The relentless pace of innovation in medical devices is another strong driver behind the growth of the Metal Wires & Strips for Medical Device Manufacturing Market. From implantable defibrillators to robotic-assisted surgical tools, the need for highly conductive, flexible, and corrosion-resistant metals is on the rise. For instance, the global market for implantable cardiac devices alone is projected to surpass USD 20 billion by 2027, creating unprecedented demand for precision wires made of titanium, stainless steel, and nickel alloys.
Metal strips and wires are no longer limited to structural purposes—they also serve as signal conductors, structural supports, and sensor interfaces in cutting-edge devices. The increasing integration of AI and digital monitoring in diagnostics further escalates the requirement for thin, reliable metal wires, especially in wearables and next-generation diagnostic equipment.
Aging Population and Chronic Illness Trends Expanding the Metal Wires & Strips for Medical Device Manufacturing Market
The demographic shift toward an aging global population has direct implications for the Metal Wires & Strips for Medical Device Manufacturing Market. Populations over the age of 60 are expected to double by 2050, crossing the 2 billion mark. This aging cohort is more susceptible to chronic diseases such as cardiovascular disorders, osteoporosis, and diabetes—all of which often require implantable or supportive medical devices.
Devices such as vascular stents, spinal implants, and orthopedic fixtures depend on biocompatible and corrosion-resistant metal wires and strips for long-term performance. For example, over 3 million stents are implanted globally each year, with demand rising at over 6% CAGR. The correlation between this demographic trend and the escalating need for device materials positions the market for metal wires and strips as essential in age-related healthcare.
High-Precision Manufacturing Techniques Reinforcing Metal Wires & Strips for Medical Device Manufacturing Market Growth
Advanced manufacturing technologies such as laser cutting, precision drawing, and cold rolling are transforming the capabilities of metal wires and strips, enabling high tolerance, micro-scale precision, and structural consistency. These innovations are critical for producing components that fit the complex geometries of minimally invasive devices and robotic surgical tools.
The Metal Wires & Strips for Medical Device Manufacturing Market is seeing increased investment in automation and digital quality control systems, which improve efficiency and reduce defect rates. For instance, the demand for laser-cut hypotubes—used in catheter assemblies—has grown by more than 12% annually. This reflects how precision-focused production is not only enabling innovation but also scaling up supply capacity to meet growing medical needs.
Biocompatibility and Safety Standards Elevating Demand in the Metal Wires & Strips for Medical Device Manufacturing Market
The need for biocompatible and safe materials is a key factor shaping the Metal Wires & Strips for Medical Device Manufacturing Market. Implantable devices must endure physiological stress and remain inert within the human body over extended periods. Alloys such as nitinol, cobalt-chromium, and titanium are now preferred materials due to their proven safety, flexibility, and corrosion resistance.
With regulatory scrutiny intensifying globally, manufacturers are compelled to use metals that comply with FDA and ISO standards. These regulations mandate strict biocompatibility testing and long-term performance validation, which has increased reliance on premium-grade metal wires and strips. This shift toward quality-first material sourcing is leading to higher adoption of specialized alloys and advanced surface finishing processes.
Customization and Patient-Specific Solutions Reshaping the Metal Wires & Strips for Medical Device Manufacturing Market
Another defining trend in the Metal Wires & Strips for Medical Device Manufacturing Market is the growing emphasis on customization. As healthcare evolves toward personalized treatment, the demand for patient-specific medical devices—ranging from implants to diagnostic sensors—is rising. Customization requires adaptable, formable, and precisely manufactured metal components.
The use of 3D printing and computer-aided wire bending allows for tailoring metal wire geometries to match patient anatomy. For instance, orthopedic implants often require custom-contoured fixation wires and strips, and these are now manufactured with micron-level tolerances. The need for such patient-centric manufacturing is rapidly expanding the market opportunity for metal wire producers who can deliver agile production capabilities and complex geometries.
Metal Wires & Strips for Medical Device Manufacturing Market Size Expansion Fueled by Diagnostic Advancements
Advancements in diagnostic imaging and monitoring technologies are creating significant tailwinds for the Metal Wires & Strips for Medical Device Manufacturing Market. Devices like MRI machines, CT scanners, and wearable biosensors rely heavily on micro-wires for signal transmission, electromagnetic shielding, and sensor integration.
In particular, the global biosensor market—valued at over USD 27 billion—is growing at a rate of nearly 8% annually. These devices frequently incorporate micro-wires made from silver, platinum, and stainless steel. This direct link between diagnostic innovation and material demand highlights the growing size and complexity of the market for medical-grade metal components.
Regulatory Focus and Regional Medical Device Investments Accelerating the Metal Wires & Strips for Medical Device Manufacturing Market
Regulatory bodies across the United States, Europe, and Asia-Pacific are enforcing stricter compliance on medical device materials, pushing manufacturers toward higher standards in raw materials and finished components. Simultaneously, governments are increasing investments in healthcare infrastructure, which indirectly boosts demand for medical devices and their underlying materials.
For example, the U.S. medical device industry has received over USD 15 billion in public-private investments over the last three years. Europe’s MDR regulations have redefined safety benchmarks, leading to rising demand for certified, biocompatible metal wires. In Asia, countries like Japan and South Korea are channeling R&D funds into advanced implants and diagnostic tools, directly benefiting the Metal Wires & Strips for Medical Device Manufacturing Market.
Metal Wires & Strips for Medical Device Manufacturing Market Size Outlook Reflects Resilience and Growth
Based on current market dynamics, the Metal Wires & Strips for Medical Device Manufacturing Market Size is projected to reach a multi-billion-dollar valuation within the next five years. This robust growth is driven by multiple converging forces—aging demographics, chronic illness prevalence, minimally invasive surgical trends, and sustained innovation in diagnostics and implants.
Across all regions, suppliers who focus on material excellence, regulatory compliance, and technological adaptability are well-positioned to capture a growing share of this essential medical manufacturing segment.
“Track Country-wise Metal Wires & Strips for Medical Device Manufacturing Production and Demand through our Metal Wires & Strips for Medical Device Manufacturing Production Database”
-
-
- Metal Wires & Strips for Medical Device Manufacturing production database for 28+ countries worldwide
- Metal Wires & Strips for Medical Device Manufacturing Powder sales volume for 32+ countries
- Country-wise Metal Wires & Strips for Medical Device Manufacturing production capacity and production plant mapping, production capacity utilization for 28+ manufacturers
- Metal Wires & Strips for Medical Device Manufacturing production plants and production plant capacity analysis for top manufacturers
-
North America Leading Innovation in the Metal Wires & Strips for Medical Device Manufacturing Market
The Metal Wires & Strips for Medical Device Manufacturing Market in North America, particularly in the United States, continues to lead global innovation and consumption. Datavagyanik highlights that over 40% of the global production of implantable cardiovascular and neurostimulation devices originates in the U.S. These products, which include stents, pacemakers, and neuromodulators, depend extensively on medical-grade metal wires such as nickel-titanium alloys and stainless steel variants.
For example, the U.S. performs over 600,000 angioplasty procedures each year, most requiring guidewires and stents produced from precision-drawn metal wires. As healthcare systems prioritize minimally invasive interventions, demand for these wires continues to grow at over 9% annually. Furthermore, the country’s robust R&D ecosystem and stringent FDA standards drive the adoption of high-performance alloys and advanced wire fabrication technologies, thereby expanding the Metal Wires & Strips for Medical Device Manufacturing Market significantly.
Europe Prioritizing Biocompatibility and Precision in the Metal Wires & Strips for Medical Device Manufacturing Market
Europe’s contribution to the Metal Wires & Strips for Medical Device Manufacturing Market is shaped by its regulatory rigor and strong emphasis on medical engineering. Countries like Germany, France, and Switzerland are known for manufacturing high-precision surgical tools, vascular implants, and spinal fixation devices. Datavagyanik identifies Germany as a key hub, with over 2,000 companies focused on medical device manufacturing—many of which rely on custom-shaped metal wires and micro-strips for structural support and signal conductivity.
For instance, Germany’s orthopedic implant market has been growing steadily at 7% CAGR, driving increased demand for titanium and cobalt-chromium wires used in bone screws and plates. The region also leads in robotic surgery integration, where fine electrical wires are embedded into smart instruments for real-time feedback. These applications reinforce Europe’s growing share in the Metal Wires & Strips for Medical Device Manufacturing Market and its shift toward biocompatible, corrosion-resistant materials.
Asia Pacific Emerging as a High-Growth Zone in the Metal Wires & Strips for Medical Device Manufacturing Market
Asia Pacific is rapidly emerging as the most dynamic region in the Metal Wires & Strips for Medical Device Manufacturing Market. Countries like China, Japan, South Korea, and India are not only increasing domestic production but are also becoming major exporters of medical-grade wires and strips. Datavagyanik notes that China alone accounts for nearly 30% of global stainless steel wire output, much of which is channeled into stents, catheters, and surgical instruments.
Japan’s leadership in precision manufacturing is evident in its neurovascular device segment, where high-tensile nickel-titanium wires are used for minimally invasive aneurysm treatments. Meanwhile, India’s healthcare expansion and the government’s “Make in India” initiative have triggered double-digit growth in medical device output, which includes localized production of orthopedic wires and cardiac device strips.
For instance, India’s vascular stent market is expanding at 14% annually, and more than 70% of those stents are now being manufactured domestically. This not only accelerates the Metal Wires & Strips for Medical Device Manufacturing Market growth in Asia but also increases the region’s influence in the global supply chain.
Regional Production Shaping the Global Metal Wires & Strips for Medical Device Manufacturing Market
Global production of metal wires and strips for medical devices is concentrated in regions with strong metallurgy and cleanroom manufacturing capabilities. North America and Europe focus on high-end, regulatory-compliant production using titanium, nitinol, and specialized nickel alloys, while Asia Pacific emphasizes volume and cost efficiency.
Datavagyanik estimates that 60% of the world’s stainless steel wire used in catheter assemblies is produced in China and Taiwan. However, when it comes to titanium wires for orthopedic implants, the U.S. and Germany together control over 70% of production. Japan remains dominant in the production of fine-diameter wires under 0.01 mm, essential for applications in cochlear implants and biosensors.
As the demand for patient-specific and miniaturized devices grows, regions with precision manufacturing capabilities and cleanroom integration will command a larger share of the Metal Wires & Strips for Medical Device Manufacturing Market.
Segmentation by Material Type in the Metal Wires & Strips for Medical Device Manufacturing Market
The Metal Wires & Strips for Medical Device Manufacturing Market is segmented based on materials that address different device requirements. Stainless steel remains the most commonly used metal due to its cost-effectiveness, strength, and corrosion resistance. It dominates the production of surgical instruments, catheter wires, and dental implants.
Titanium, while more expensive, is favored in orthopedic and spinal applications because of its high strength-to-weight ratio and bio-inert properties. The titanium wire segment is growing at over 10% CAGR, particularly in spinal fixation devices and joint replacements.
Nickel-titanium (Nitinol) wires are increasingly used in self-expanding stents, guidewires, and filters. These wires offer shape memory and superelastic properties, which are essential in dynamic bodily environments. For instance, more than 90% of neurovascular stents now use Nitinol due to its reliability and resilience.
Other metals such as platinum, gold, and cobalt-chromium are used in highly specialized applications like cochlear implants, neurostimulation leads, and cardiovascular pacing systems. The diversity in metal types ensures that the Metal Wires & Strips for Medical Device Manufacturing Market addresses the full spectrum of clinical applications.
Application-Based Demand Segmentation in the Metal Wires & Strips for Medical Device Manufacturing Market
From cardiovascular devices to diagnostic instruments, the Metal Wires & Strips for Medical Device Manufacturing Market is segmented across multiple end-use applications. Cardiovascular stents represent one of the largest application areas, growing at 7–8% annually. These devices require biocompatible and highly ductile wires that can expand without fracturing.
Catheters and guidewires follow closely, especially with the growth of minimally invasive vascular procedures. Neurostimulation and orthopedic implants are among the fastest-growing segments, with annual growth rates exceeding 11%, creating strong demand for fine wires that offer both strength and flexibility.
In diagnostics, wires are used in electrodes, imaging sensors, and EMI shielding for equipment like MRI and ECG machines. The expansion of the global diagnostic imaging market, which is expected to surpass USD 50 billion by 2026, is a key contributor to the Metal Wires & Strips for Medical Device Manufacturing Market.
Metal Wires & Strips for Medical Device Manufacturing Price Trend Driven by Alloy Composition and Precision Requirements
The Metal Wires & Strips for Medical Device Manufacturing Price is significantly influenced by raw material costs, alloy composition, and manufacturing precision. For example, stainless steel wire prices have remained relatively stable, ranging between USD 3,000 and USD 4,500 per metric ton. However, titanium and nickel-titanium wires command premium pricing—up to USD 45,000 per metric ton—due to their specialized processing needs and limited availability.
Datavagyanik highlights that the Metal Wires & Strips for Medical Device Manufacturing Price Trend is upward for high-performance alloys, primarily due to the growing complexity of implantable devices. With increasing demand for customization and tighter tolerances, labor and equipment costs also play a larger role in final product pricing.
For instance, laser-cut hypotubes used in robotic catheters may cost up to 5 times more than conventional wire forms due to their intricate geometries and high-quality surface finishes. As miniaturization advances, the Metal Wires & Strips for Medical Device Manufacturing Price Trend reflects a clear premium for ultra-fine, specialty wire grades.
Future Outlook on Metal Wires & Strips for Medical Device Manufacturing Price Trend
Moving forward, Datavagyanik anticipates a bifurcated Metal Wires & Strips for Medical Device Manufacturing Price Trend. Commodity-grade materials like stainless steel will remain competitively priced due to scale and availability. However, prices for advanced materials such as platinum-iridium wires, cobalt-chromium strips, and Nitinol will continue to climb due to supply chain limitations and stricter performance expectations.
Additionally, geopolitical factors and environmental regulations surrounding mining and alloy processing may influence the Metal Wires & Strips for Medical Device Manufacturing Price in the near future. The introduction of ESG requirements and clean manufacturing standards will likely push up production costs, especially in Europe and North America.
Manufacturers who invest in recycling capabilities, energy-efficient processing, and sustainable sourcing are expected to gain pricing leverage while appealing to increasingly eco-conscious device OEMs.
“Metal Wires & Strips for Medical Device Manufacturing Manufacturing Database, Metal Wires & Strips for Medical Device Manufacturing Manufacturing Capacity”
-
-
- Metal Wires & Strips for Medical Device Manufacturing top manufacturers market share for 28+ manufacturers
- Top 8 manufacturers and top 17 manufacturers of Metal Wires & Strips for Medical Device Manufacturing in North America, Europe, Asia Pacific
- Production plant capacity by manufacturers and Metal Wires & Strips for Medical Device Manufacturing production data for 28+ market players
- Metal Wires & Strips for Medical Device Manufacturing production dashboard, Metal Wires & Strips for Medical Device Manufacturing production data in excel format
-
Leading Manufacturers Shaping the Metal Wires & Strips for Medical Device Manufacturing Market
The Metal Wires & Strips for Medical Device Manufacturing Market is driven by a set of highly specialized global manufacturers who command strong technical capabilities and product portfolios. These companies are instrumental in producing the advanced metal components required in a wide array of medical applications, from vascular stents and guidewires to implantable neuromodulators and surgical tools.
Fort Wayne Metals is one of the leading players in this market, widely recognized for its leadership in nitinol and other advanced alloy wire production. The company offers custom wire forms, shaped wire, and multifilar coil wire products that serve cardiovascular, neurovascular, and orthopedic device manufacturers. With capabilities in both melting and drawing of specialty metals, Fort Wayne Metals plays a critical role in supplying biocompatible materials for demanding implant applications.
Ulbrich Stainless Steels & Special Metals is another key manufacturer with a dominant presence in medical strip and fine wire production. Its precision flat wire and edge-conditioned strip products are widely used in catheter reinforcements, surgical blades, and dental tools. Ulbrich’s medical-grade offerings include stainless steel, titanium, and cobalt-chromium alloys, engineered to meet tight tolerances and critical mechanical properties required in implantable and diagnostic devices.
Combined Metals Company contributes significantly to the Metal Wires & Strips for Medical Device Manufacturing Market through its advanced processing of stainless steel and nickel-based strips. These materials are used extensively in devices such as neurostimulators, defibrillators, and implantable pumps. The company specializes in high-precision rolling and slitting technologies that cater to custom geometries demanded by modern medical device designs.
Johnson Matthey’s medical materials division, although more niche in scope, serves high-end segments of the market with platinum, iridium, and precious metal wires for applications like electrode leads and sensor assemblies. These components are essential in cardiac rhythm management and advanced diagnostic devices.
Elgiloy Specialty Metals provides precision drawn wire and strip products made from Elgiloy alloy, cobalt-chromium-nickel alloys, and stainless steel. Their materials are particularly sought after for use in balloon catheters, orthodontic appliances, and orthopedic fasteners due to their fatigue strength and corrosion resistance.
Metal Wires & Strips for Medical Device Manufacturing Market Share by Leading Manufacturers
The Metal Wires & Strips for Medical Device Manufacturing Market is moderately consolidated, with the top 8 to 10 manufacturers accounting for roughly 45 to 50 percent of global revenue. Fort Wayne Metals maintains a leading share within the nitinol and stainless-steel wire segment, contributing to over 12 percent of the market alone. This leadership is driven by its integrated supply chain, which includes alloy melting, wire drawing, and shape-setting capabilities, allowing for greater control over product consistency and performance.
Ulbrich holds close to 8 to 10 percent of the Metal Wires & Strips for Medical Device Manufacturing Market share, with a focus on edge-rolled and slit strip products used in flexible shafts and endoscopic instruments. Its competitive strength lies in its customization capabilities and ability to produce complex cross-sectional geometries at scale.
Combined Metals Company and Elgiloy Specialty Metals each contribute approximately 5 to 7 percent of market share, primarily in the orthopedic, dental, and catheter markets. Their value proposition lies in their high-speed precision slitting and alloy expertise, which enables them to meet the growing demand for corrosion-resistant, fatigue-tolerant strip materials.
Smaller players and regional manufacturers supply the remaining 50 percent of the market, often focusing on specific alloys, regional distribution, or high-volume commodity-grade materials. However, larger players continue to expand vertically into advanced processing to capture greater market share.
Product Line Innovations Driving Competitive Differentiation
Within the Metal Wires & Strips for Medical Device Manufacturing Market, manufacturers are increasingly diversifying their product lines to serve more complex applications. For instance, Fort Wayne Metals has developed wire-based solutions specifically designed for torque-transmitting catheter shafts and superelastic coils for thrombectomy devices.
Ulbrich’s UltraLite and EdgePlus product series are designed to meet the requirements of low-profile implantable devices that demand extreme thinness, high tensile strength, and seamless edges. These product lines support innovations in miniaturized pacemakers and intravascular diagnostic sensors.
Combined Metals has introduced ultra-flat strip technologies with enhanced dimensional control, which are being adopted in drug-eluting stent platforms and microelectromechanical systems (MEMS) used in smart diagnostics.
Meanwhile, Elgiloy’s orthopedic wire series includes cobalt-chromium and titanium-based options tailored for bone screws, spinal rods, and trauma fixation devices. Their products are certified to meet the ASTM F1058 and ISO 5832 standards for implantable materials.
Recent Industry Developments and Timeline of Key Activities
The Metal Wires & Strips for Medical Device Manufacturing Market has seen a number of important developments in the last 24 months that reflect evolving strategies and shifting priorities among major players.
In December 2024, Fort Wayne Metals completed the expansion of its nitinol melting and shape-setting facility, effectively doubling its annual production capacity. This move was in response to soaring demand from cardiovascular device makers seeking to secure long-term material supply chains for stent and guidewire components.
In early 2024, Ulbrich launched a new precision strip processing line at its Connecticut facility, capable of producing ultra-thin medical strips below 0.01 mm thickness. This investment was made to support growing demand from neurostimulation and biosensor manufacturers looking for next-generation conductive materials.
In July 2023, Combined Metals entered a partnership with a European device OEM to co-develop a proprietary cobalt-alloy strip for a novel orthopedic implant system. The partnership involved joint R&D and preclinical material testing aimed at reducing implant fatigue failure rates.
Elgiloy Specialty Metals, in late 2023, announced its expansion into Asia Pacific with a distribution hub in Singapore, targeting the growing base of OEMs in India, China, and Southeast Asia. The move is part of a broader strategy to increase its footprint in rapidly growing medical markets.
The overall trend in recent developments reflects increased vertical integration, a push toward material science innovation, and regional supply chain diversification. As demand for advanced implants, neurovascular devices, and wearable diagnostic tools accelerates, top manufacturers are positioning themselves as not just suppliers, but strategic partners in product development.
“Metal Wires & Strips for Medical Device Manufacturing Production Data and Metal Wires & Strips for Medical Device Manufacturing Production Trend, Metal Wires & Strips for Medical Device Manufacturing Production Database and forecast”
-
-
- Metal Wires & Strips for Medical Device Manufacturing production database for historical years, 10 years historical data
- Metal Wires & Strips for Medical Device Manufacturing production data and forecast for next 8 years
-
Market Scenario, Demand vs Supply, Average Product Price, Import vs Export, till 2035
- Global Metal Wires & Strips for Medical Device Manufacturing Market revenue and demand by region
- Global Metal Wires & Strips for Medical Device Manufacturing Market production and sales volume
- United States Metal Wires & Strips for Medical Device Manufacturing Market revenue size and demand by country
- Europe Metal Wires & Strips for Medical Device Manufacturing Market revenue size and demand by country
- Asia Pacific Metal Wires & Strips for Medical Device Manufacturing Market revenue size and demand by country
- Middle East & Africa Metal Wires & Strips for Medical Device Manufacturing Market revenue size and demand by country
- Latin America Metal Wires & Strips for Medical Device Manufacturing Market revenue size and demand by
- Import-export scenario – United States, Europe, APAC, Latin America, Middle East & Africa
- Average product price – United States, Europe, APAC, Latin America, Middle East & Africa
- Market player analysis, competitive scenario, market share analysis
- Business opportunity analysis
Key questions answered in the Global Metal Wires & Strips for Medical Device Manufacturing Market Analysis Report:
- What is the market size for Metal Wires & Strips for Medical Device Manufacturing in United States, Europe, APAC, Middle East & Africa, Latin America?
- What is the yearly sales volume of Metal Wires & Strips for Medical Device Manufacturing and how is the demand rising?
- Who are the top market players by market share, in each product segment?
- Which is the fastest growing business/ product segment?
- What should be the business strategies and Go to Market strategies?
The report covers Metal Wires & Strips for Medical Device Manufacturing Market revenue, Production, Sales volume, by regions, (further split into countries):
- Asia Pacific (China, Japan, South Korea, India, Indonesia, Vietnam, Rest of APAC)
- Europe (UK, Germany, France, Italy, Spain, Benelux, Poland, Rest of Europe)
- North America (United States, Canada, Mexico)
- Latin America (Brazil, Argentina, Rest of Latin America)
- Middle East & Africa
Table of Contents:
Metal Wires & Strips for Medical Device Manufacturing Market
- Introduction to Metal Wires & Strips in Medical Device Manufacturing
- Definition and Functional Importance in Medical Equipment
- Key Characteristics: Strength, Flexibility, and Biocompatibility
- Industry Adoption and Growing Demand for Precision Metal Components
- Classification of Metal Wires & Strips Used in Medical Devices
- Stainless Steel, Titanium, and Cobalt-Based Alloys
- Nitinol and Other Shape Memory Alloys (SMA) in Medical Applications
- Coated vs. Non-Coated Wires and Their Performance Advantages
- Market Growth Drivers and Key Challenges
- Rising Demand for Minimally Invasive Surgical Instruments
- Advancements in Metal Processing for Enhanced Biocompatibility
- Supply Chain Constraints and Cost Challenges in High-Precision Manufacturing
- North America Market Analysis for Medical-Grade Metal Wires & Strips
- Market Size, Trends, and Growth Forecast
- Key Applications in Orthopedic, Cardiovascular, and Neurological Devices
- Competitive Landscape and Major Suppliers in the Region
- Europe Metal Wires & Strips for Medical Devices Market
- Impact of EU Regulations on Material Safety and Biocompatibility
- Market Growth in Dental, Implantable, and Surgical Applications
- Strategic Developments by Leading Medical Wire and Strip Manufacturers
- Asia Pacific Market Trends and Expansion Opportunities
- Growing Medical Device Manufacturing Hubs in China, India, and Japan
- Increasing Investment in Advanced Medical Equipment Production
- Export and Import Trends Influencing Regional Market Growth
- Latin America Market Scope and Development Trends
- Adoption of Medical Wires and Strips in Prosthetics and Rehabilitation Devices
- Economic and Regulatory Factors Shaping the Market
- Business Challenges and Potential for Local Manufacturing Expansion
- Middle East & Africa Market Overview
- Demand for High-Quality Medical Components in Emerging Healthcare Sectors
- Investment in Advanced Surgical and Diagnostic Equipment
- Regional Trade Policies and Barriers to Market Entry
- Production Processes and Manufacturing Techniques
- Precision Wire Drawing, Extrusion, and Rolling Methods
- Advances in Coating Technologies for Enhanced Corrosion Resistance
- Cost Optimization Strategies for High-Volume Production
- Competitive Landscape and Key Industry Players
- Leading Suppliers of Medical-Grade Metal Wires & Strips
- Business Growth Strategies and R&D Investments
- Mergers, Acquisitions, and Industry Collaborations
- Revenue and Market Share Analysis by Manufacturer
- Financial Performance of Major Market Players
- Revenue Trends and Profitability in the Medical Wire Industry
- Forecasted Market Share and Strategic Positioning
- Pricing Strategies and Market Cost Dynamics
- Raw Material Cost Impact on Final Product Pricing
- Competitive Pricing Models in Global Markets
- Future Cost Trends and Economic Impact on Medical Device Manufacturing
- Trade and International Market Expansion
- Export-Import Statistics for Medical-Grade Metal Wires & Strips
- Trade Regulations, Tariffs, and Compliance Standards
- Market Entry Strategies and Regional Business Expansion Plans
- Industry-Specific Applications of Medical Wires & Strips
- Usage in Catheters, Stents, and Guidewires
- Role in Orthopedic Implants, Pacemakers, and Surgical Robotics
- Expansion in Wearable and Smart Medical Device Technologies
- Market Demand and Consumption Forecast (2025-2040)
- Projected Consumption Growth Across Key Medical Segments
- Future Demand in Emerging Healthcare Markets
- Innovations Driving Adoption in Next-Generation Medical Devices
- Raw Material Sourcing and Supply Chain Optimization
- Global Availability of High-Purity Metal Alloys
- Challenges in Sourcing Medical-Grade Titanium and Nitinol
- Sustainable and Ethical Procurement Strategies for Medical Manufacturers
- Distribution Networks and Supply Chain Logistics
- Role of Medical Device OEMs and Component Suppliers
- Impact of Digital Marketplaces and E-Procurement on Metal Wire Distribution
- Logistics and Warehousing Challenges in Global Markets
- Regulatory Compliance and Medical Device Safety Standards
- FDA, CE, and ISO Guidelines for Medical Wire and Strip Materials
- Biocompatibility Testing and Material Validation Processes
- Government Policies on Medical Device Component Approvals
- Investment Trends and Business Growth Opportunities
- High-Growth Sectors and Regions for Market Expansion
- Venture Capital and Private Equity Investments in Medical Manufacturing
- Risks and Rewards for New Market Entrants in Medical Wire Production
- Technological Innovations and Future Market Developments
- Advances in Nanotechnology and Smart Metal Coatings
- Role of AI and Automation in Precision Wire Processing
- Research in Self-Healing and Bio-Absorbable Metal Wires
- Long-Term Market Forecast and Industry Roadmap (2025-2040)
- Future Growth Strategies and Market Expansion Projections
- Challenges and Opportunities for New and Existing Players
- Key Trends Shaping the Future of Medical Wire and Strip Manufacturing
- Conclusion and Strategic Business Recommendations
- Summary of Key Market Insights and Competitive Landscape
- Best Practices for Manufacturers and Supply Chain Partners
- Actionable Strategies for Investors and Industry Stakeholders
Other recently published reports:
“Every Organization is different and so are their requirements”- Datavagyanik
Companies We Work With
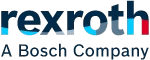
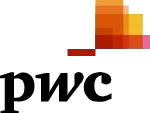
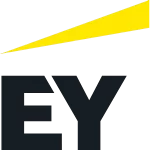
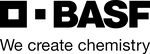
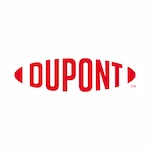

Do You Want To Boost Your Business?
drop us a line and keep in touch
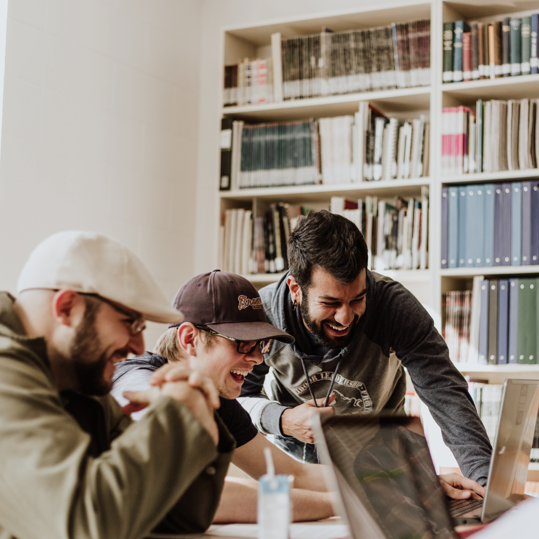