Pipeline Emergency Repair Clamps Market Size, Production, Sales, Average Product Price, Market Share, Import vs Export
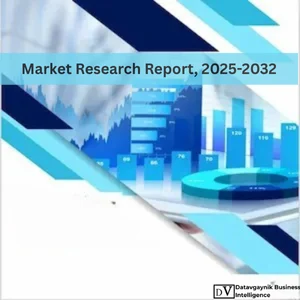
- Published 2025
- No of Pages: 120+
- 20% Customization available
Accelerating Infrastructure Aging Fuels the Pipeline Emergency Repair Clamps Market
The Pipeline Emergency Repair Clamps Market is experiencing accelerated growth, largely driven by the rapid deterioration of global pipeline infrastructure. For instance, in North America alone, over 70% of oil and gas pipelines are more than 30 years old, many of which are well past their original design life. This aging infrastructure leads to a rising incidence of leaks, cracks, and corrosion, creating urgent demand for swift, cost-effective solutions.
Pipeline emergency repair clamps are emerging as a frontline response to this challenge. These clamps allow operators to contain leaks without the need for full pipeline shutdowns, which can cost millions in lost production. For example, a single-day shutdown of a mid-sized crude oil pipeline can result in losses ranging from $500,000 to over $2 million. In such scenarios, emergency clamps deliver an immediate return on investment, justifying their growing integration into routine pipeline maintenance strategies.
According to Datavagyanik, the Pipeline Emergency Repair Clamps Market Size has increased significantly in regions with older pipeline systems, particularly across the U.S., Canada, and parts of Europe, where maintenance costs now account for over 60% of pipeline operating budgets.
Expansion of Energy Infrastructure Strengthens Pipeline Emergency Repair Clamps Market Growth
As energy consumption scales globally, the expansion of oil, gas, water, and renewable energy pipeline networks is intensifying. For instance, over 120,000 kilometers of new oil and gas pipelines are under planning or construction worldwide as of 2025. These infrastructure projects span regions such as Asia Pacific, the Middle East, and Africa—markets where pipeline reliability is becoming mission-critical.
This network expansion directly boosts the Pipeline Emergency Repair Clamps Market by necessitating robust emergency systems for newly laid and legacy pipelines alike. In fast-growing economies such as India and Indonesia, where pipeline mileage is projected to grow by over 40% by 2030, the installation of safety-first infrastructure components, including emergency clamps, is now standard practice in both public and private sector projects.
The increasing complexity and length of pipeline routes, particularly those crossing geologically unstable areas or spanning offshore segments, further underlines the need for rapid-repair solutions. This trend is especially visible in offshore subsea pipeline projects, where emergency access is limited and high-pressure containment solutions are critical.
Regulatory Pressures and Environmental Concerns Push the Pipeline Emergency Repair Clamps Market Forward
Environmental compliance and stringent safety mandates are becoming decisive market drivers. Across the U.S. and the European Union, pipeline operators are now required to report even minor leaks under environmental impact laws such as the EPA’s Leak Detection and Repair (LDAR) program or the EU’s Methane Strategy.
Such regulatory scrutiny is catalyzing growth in the Pipeline Emergency Repair Clamps Market, as operators seek proactive measures to mitigate legal risks and environmental penalties. For instance, fines related to non-compliance with pipeline integrity regulations in the U.S. exceeded $90 million in 2023 alone. Emergency repair clamps, being fast to deploy and cost-effective, are increasingly being included in operators’ emergency preparedness kits.
Moreover, high-profile pipeline failures, such as the 2021 Colonial Pipeline ransomware-triggered shutdown or the 2022 Nord Stream gas leak, have heightened public and political focus on infrastructure resilience. This has led to a surge in risk mitigation investments, of which the emergency clamp segment forms a critical part.
High Costs of Downtime Drive Demand in Pipeline Emergency Repair Clamps Market
The Pipeline Emergency Repair Clamps Market is also benefitting from the industry’s increasing intolerance to unplanned downtime. In sectors such as oil and gas, water utilities, and petrochemicals, even a few hours of unscheduled downtime can derail logistics, damage equipment, and delay critical supply chains.
To illustrate, a study by Datavagyanik revealed that a midstream oil company operating in the Permian Basin faced daily revenue losses exceeding $1.2 million due to unexpected pipeline leaks. By adopting emergency repair clamps, the same operator reduced leak-related downtime by over 70%, leading to a 15% reduction in annual maintenance expenses.
In addition, modern clamps are now engineered to handle a broader range of pressures and pipeline materials, which enhances their versatility across multiple applications. This adaptability makes them especially valuable in sectors where diverse pipeline types intersect, such as industrial parks, urban utility grids, and portside energy terminals.
Urbanization and Industrial Growth Create New Pipeline Emergency Repair Clamps Market Opportunities
Rapid urbanization and industrial growth, particularly across Asia Pacific and the Middle East, are amplifying the installation of pipeline systems for water, gas, and chemical distribution. Urban population centers in countries like China, the UAE, and Vietnam are expected to grow by over 30% by 2035, requiring extensive utility infrastructure, including reliable emergency repair systems.
The Pipeline Emergency Repair Clamps Market is tapping into this growth through solutions tailored to municipal and industrial needs. For example, water utilities in India have reported a 25% year-on-year increase in demand for emergency clamps due to rising maintenance needs in legacy water supply pipelines. Similarly, chemical processing plants in Southeast Asia are investing in pressure-rated clamp systems that can handle aggressive media and extreme temperatures.
With urban infrastructure budgets increasingly under pressure, municipal bodies are favoring the use of emergency clamps as a way to defer costly pipeline replacements. Datavagyanik forecasts that demand for emergency repair clamps in the municipal sector will grow at a CAGR of 8.7% through 2030, particularly in cities with outdated underground utilities.
Offshore and Subsea Pipeline Projects Fuel Specialized Segment in Pipeline Emergency Repair Clamps Market
A critical growth segment within the Pipeline Emergency Repair Clamps Market is dedicated to offshore and subsea pipeline applications. As offshore energy exploration continues to expand—especially in regions like the Gulf of Mexico, West Africa, and Southeast Asia—so does the need for specialized emergency repair solutions capable of operating in hostile marine environments.
These clamps must handle extreme pressure differentials, salinity-induced corrosion, and limited human intervention. For example, Norway’s North Sea subsea fields have reported a 60% increase in the deployment of remotely installable emergency repair clamps, particularly for pipelines transporting LNG and hydrogen blends.
Technological innovations are rapidly transforming this segment. Companies are now developing smart clamps equipped with sensors to monitor pipeline integrity post-installation, allowing for predictive maintenance. The result is a substantial reduction in the total cost of ownership and improved operational continuity for offshore operators.
Hydrogen Economy and Carbon Capture Pipelines Expand Scope of Pipeline Emergency Repair Clamps Market
The energy transition is introducing new materials and stresses into pipeline infrastructure. As hydrogen and carbon capture projects scale globally, their pipeline requirements are creating a fresh wave of demand in the Pipeline Emergency Repair Clamps Market.
For instance, hydrogen molecules are significantly smaller than methane, making them more prone to leakage and embrittlement of pipeline materials. Emergency repair clamps designed for hydrogen applications must therefore meet stricter sealing and material compatibility standards. Europe, which is expected to install over 23,000 km of hydrogen pipelines by 2040, is leading this innovation wave.
Similarly, carbon capture and storage (CCS) projects are gaining momentum, with more than 260 active pipeline initiatives globally. These pipelines often operate under extreme pressures and fluctuating temperatures, further emphasizing the need for high-performance emergency clamp systems.
Manufacturers are responding by designing multi-purpose clamps using nickel-based alloys and advanced elastomers that maintain integrity under such specialized conditions. Datavagyanik estimates that by 2032, over 20% of the global Pipeline Emergency Repair Clamps Market Size will be attributed to hydrogen and CCS pipeline projects.
“Track Country-wise Pipeline Emergency Repair Clamps Production and Demand through our Pipeline Emergency Repair Clamps Production Database”
-
-
- Pipeline Emergency Repair Clamps production database for 28+ countries worldwide
- Pipeline Emergency Repair Clamps Powder sales volume for 32+ countries
- Country-wise Pipeline Emergency Repair Clamps production capacity and production plant mapping, production capacity utilization for 28+ manufacturers
- Pipeline Emergency Repair Clamps production plants and production plant capacity analysis for top manufacturers
-
North America Maintains Market Leadership in Pipeline Emergency Repair Clamps Market
The Pipeline Emergency Repair Clamps Market in North America continues to dominate the global landscape, driven by a combination of aging pipeline infrastructure, regulatory pressure, and technological innovation. For instance, over 2.6 million kilometers of oil and gas pipelines operate across the United States and Canada—over half of which were installed before the 1980s. This aging infrastructure results in frequent leaks and ruptures, intensifying demand for emergency repair solutions.
Datavagyanik highlights that the U.S. alone accounted for over 28% of global revenue in the Pipeline Emergency Repair Clamps Market in 2024. Factors contributing to this include high awareness of pipeline integrity risks and a robust domestic manufacturing ecosystem. Moreover, leading U.S.-based manufacturers are investing in high-performance clamps made from stainless steel and corrosion-resistant alloys to serve the demands of high-pressure transmission lines, including hydrogen pipelines emerging under the Inflation Reduction Act.
In Canada, midstream operators are adopting repair clamps across LNG and oil sands pipelines to reduce environmental incidents. The environmental impact costs from oil spills in Alberta alone exceeded $400 million in the last decade, compelling operators to integrate clamps into their preventive maintenance regimes.
Europe Drives Sustainable Innovation in Pipeline Emergency Repair Clamps Market
Europe represents the second-largest regional contributor to the Pipeline Emergency Repair Clamps Market, driven by energy transition policies, hydrogen infrastructure expansion, and aggressive decarbonization targets. Countries such as Germany, France, the U.K., and the Netherlands are leading the charge.
Germany, for instance, is building over 1,800 km of hydrogen pipelines by 2030 under its National Hydrogen Strategy. These pipelines require specialized clamps capable of handling embrittlement risks and ultra-high pressure. German manufacturers have responded with cutting-edge products utilizing duplex stainless steel and advanced sealing polymers, strengthening the country’s export capabilities.
In France, utility regulators have enforced rapid leak response guidelines for municipal water systems, especially in cities like Marseille and Lyon, where over 20% of water is lost annually due to pipeline failures. Emergency repair clamps offer a low-disruption alternative to full pipeline replacements, aligning with public-sector cost controls.
The U.K., with over 45,000 km of offshore pipelines and aggressive renewable integration goals, is generating high demand for corrosion-resistant clamps in offshore wind and hydrogen blending projects. Datavagyanik estimates that the U.K. market will grow at a CAGR of 7.5% through 2031, especially in the offshore segment.
Asia Pacific Emerges as High-Growth Hub in Pipeline Emergency Repair Clamps Market
Asia Pacific is the fastest-growing regional market, backed by large-scale infrastructure development, rapid urbanization, and strong governmental investments in energy and water distribution networks. Countries like China, India, Japan, South Korea, and Australia are spearheading growth in this region.
China’s Pipeline Emergency Repair Clamps Market is fueled by a vast oil and gas network exceeding 175,000 kilometers and rising investments in hydrogen and water reuse pipelines. Chinese manufacturers are focusing on scalable, mid-cost clamps for domestic and export markets, particularly targeting Southeast Asia and Africa. For instance, demand from Belt and Road countries for pipeline clamp imports from China grew by 23% between 2020 and 2024.
In India, rapid urban expansion and smart city initiatives are pushing municipalities to adopt pipeline maintenance tools to curb water losses that currently exceed 30% in some urban areas. Datavagyanik projects a 9.2% CAGR in India’s municipal segment of the Pipeline Emergency Repair Clamps Market through 2030.
Japan and South Korea are leaning on advanced materials technology to produce export-grade clamps. These clamps are used in cryogenic LNG, hydrogen, and high-precision chemical pipelines, where temperature tolerance and leak integrity are critical. Their exports to the Middle East, Europe, and North America have grown steadily, accounting for over $80 million in 2024.
Middle East and Africa Leverage Imports to Strengthen Pipeline Emergency Repair Clamps Market
The Middle East and Africa region is rapidly increasing its footprint in the Pipeline Emergency Repair Clamps Market, although domestic production remains limited. The market is heavily driven by oil and gas infrastructure across Saudi Arabia, UAE, and Nigeria, coupled with urban water infrastructure challenges in North and East Africa.
Saudi Arabia alone operates over 120,000 kilometers of hydrocarbon pipelines, many of which traverse harsh desert environments. This has led to a strong demand for high-durability repair clamps, particularly in areas with sand corrosion and temperature extremes. Imported clamps—primarily from Europe and the U.S.—are widely used for pipeline incident response and routine maintenance.
In Africa, countries like Kenya and South Africa are deploying emergency repair clamps across aging water distribution pipelines, some of which lose over 40% of supply due to leakages. Public-private partnerships are promoting the use of cost-effective clamp systems as part of broader water infrastructure upgrade programs.
Latin America’s Growing Pipeline Projects Amplify Pipeline Emergency Repair Clamps Market Demand
Latin America is seeing a surge in demand for emergency repair clamps driven by energy diversification, particularly natural gas and LNG pipeline projects in Brazil, Argentina, and Mexico. For example, Brazil’s pipeline expansion for pre-salt offshore gas fields is projected to add 5,000 km of pipeline capacity by 2030.
These infrastructure additions require robust leak response mechanisms. Emergency repair clamps are favored due to their ease of installation and cost-effectiveness, especially in remote or offshore locations. Mexico’s Pemex and private pipeline operators have reported an 18% rise in clamp usage for incident response between 2020 and 2024, as theft-related damages and operational leaks become increasingly common.
Product Segmentation Deepens Customization in Pipeline Emergency Repair Clamps Market
The Pipeline Emergency Repair Clamps Market is segmented by product type into leak repair clamps, full-circumference clamps, split clamps, and multi-purpose clamps. Each segment addresses distinct pipeline damage scenarios.
Leak repair clamps account for over 40% of market share, driven by high usage in routine maintenance across water and gas distribution systems. Full-circumference clamps are gaining traction in industrial and offshore environments, where larger or circumferential pipeline damage occurs. Datavagyanik forecasts this segment to grow at 6.8% CAGR due to increasing offshore exploration in Latin America and Southeast Asia.
Multi-purpose clamps, designed to fit a range of diameters and pressure ratings, are gaining popularity in developing markets where standardization across pipeline networks is still evolving. These clamps reduce inventory costs and enable faster field repairs.
Pressure and Diameter Requirements Influence Pipeline Emergency Repair Clamps Market Structure
The Pipeline Emergency Repair Clamps Market is also defined by pressure range and pipeline diameter. High-pressure clamps—used in oil, gas, and hydrogen transmission—are growing rapidly, especially with the rise of hydrogen economy projects. These clamps must endure pressures exceeding 150 bar and maintain structural integrity under cyclic stress conditions.
In contrast, low-pressure clamps are widely adopted in municipal water pipelines and some chemical industries. Here, installation speed and corrosion resistance are the key buying criteria. The small-diameter pipeline segment dominates volume demand due to widespread urban utility usage, while large-diameter clamps are essential in transmission pipelines and offshore applications.
Production Landscape Expands Across Key Global Hubs in Pipeline Emergency Repair Clamps Market
The production ecosystem of the Pipeline Emergency Repair Clamps Market is centered in the U.S., Germany, China, and Japan. U.S.-based manufacturers are integrating smart technologies such as embedded pressure sensors and real-time leak detection capabilities into clamp design. German firms are focusing on precision manufacturing using high-grade materials like Hastelloy and Inconel.
Chinese production emphasizes cost-effective mass manufacturing with improved quality control for export. Japanese and South Korean companies are creating niche high-performance clamps for LNG and cryogenic hydrogen pipelines.
India is gradually increasing domestic capacity through Make in India initiatives, supported by government procurement for municipal projects. Datavagyanik estimates that India’s production output in this segment will double between 2025 and 2030.
Global Trade Patterns and Pipeline Emergency Repair Clamps Price Trends
Trade patterns in the Pipeline Emergency Repair Clamps Market reflect a blend of specialization and cost optimization. Europe and North America lead in exporting high-specification clamps, while Asia Pacific—especially China and India—supplies a wide range of price-competitive options to emerging markets.
The Pipeline Emergency Repair Clamps Price Trend varies significantly by material, application, and end-user sector. For example, stainless steel clamps designed for high-pressure subsea pipelines can cost over $2,500 per unit, while plastic or composite clamps for urban water networks may cost as little as $40–$100.
Datavagyanik notes that the average Pipeline Emergency Repair Clamps Price increased by 6.3% in 2023, driven by rising raw material costs and increased demand for specialized clamps for hydrogen and CCS pipelines. However, bulk procurement by utilities and economies of scale in Asia are expected to moderate this trend through 2026.
Custom-engineered clamps now represent over 20% of total market revenue, and their pricing is influenced by both technical complexity and certification requirements. The Pipeline Emergency Repair Clamps Price Trend is expected to remain firm in high-pressure and subsea segments, while competitive pricing will define the municipal and industrial segments.
“Pipeline Emergency Repair Clamps Manufacturing Database, Pipeline Emergency Repair Clamps Manufacturing Capacity”
-
-
- Pipeline Emergency Repair Clamps top manufacturers market share for 28+ manufacturers
- Top 8 manufacturers and top 18 manufacturers of Pipeline Emergency Repair Clamps in North America, Europe, Asia Pacific
- Production plant capacity by manufacturers and Pipeline Emergency Repair Clamps production data for 28+ market players
- Pipeline Emergency Repair Clamps production dashboard, Pipeline Emergency Repair Clamps production data in excel format
-
Top Manufacturers Powering the Pipeline Emergency Repair Clamps Market
The Pipeline Emergency Repair Clamps Market is currently dominated by a select group of global manufacturers that have established strong footholds through advanced engineering capabilities, specialized product lines, and robust distribution networks. These companies are setting benchmarks in quality, material innovation, and customization, serving both legacy infrastructure and modern energy networks.
Key manufacturers include:
- Clock Spring Company
- Team Industrial Services
- TD Williamson
- STATS Group
- PLIDCO
- Romacon
- Hydratight
- Smith Flow Control
- ICR Group
- InduMar Systems
Each of these companies offers distinct value propositions, from high-pressure oil and gas applications to rapid-response municipal water pipeline solutions. Their strategies are aligned with emerging energy trends, pipeline aging cycles, and evolving environmental and safety regulations.
Pipeline Emergency Repair Clamps Market Share by Manufacturers
The Pipeline Emergency Repair Clamps Market is consolidated at the top, with the five largest players accounting for more than half of total global revenue. These companies compete on the basis of innovation, installation speed, material resilience, and application versatility.
Clock Spring Company holds a dominant position with a sizable share of the market, driven by its proprietary composite clamp solutions that are favored for lightweight installation and corrosion resistance. Its product range is widely deployed in transmission pipelines, especially in remote or offshore environments where minimal equipment access is critical.
Team Industrial Services, through brands like Furmanite, commands a significant portion of the global market by offering metallic and high-strength clamps used extensively in refineries, LNG terminals, and power plants. Its sealing technology supports live repairs without the need for depressurization.
TD Williamson leverages its global pipeline services to support clamp deployment in complex environments, such as live oil and gas networks. Its in-service pipeline repair tools and split-sleeve clamps are frequently used in midstream infrastructure.
STATS Group has carved out a niche in subsea and high-pressure repair clamps. Its modular and isolation-compatible clamp systems are frequently adopted in offshore platforms where operational continuity is paramount.
PLIDCO, one of the oldest names in the industry, specializes in heavy-duty clamps for oil and gas networks, including mechanical and weldable variants used for both temporary and permanent solutions. Their clamps are preferred by pipeline operators facing high-risk operations due to their proven field performance over decades.
The remaining market share is distributed among regional players focused on local pipeline infrastructure needs, particularly in Asia and the Middle East. These manufacturers often cater to smaller-diameter or low-pressure pipeline segments and compete primarily on pricing and quick delivery.
Manufacturer Product Lines in the Pipeline Emergency Repair Clamps Market
Distinct product lines across leading manufacturers define the competitive edge in the Pipeline Emergency Repair Clamps Market. These products are engineered with varying levels of sophistication depending on the application—ranging from low-pressure municipal lines to high-pressure, high-temperature industrial pipelines.
- Clock Spring’s composite clamp systems are optimized for environments where metal fatigue and corrosion are common issues. Their installation time is significantly shorter, making them ideal for emergency interventions in geographically isolated or underwater pipelines.
- Team Industrial’s SureSeal and Stopple clamps are designed for live pipeline intervention, enabling operators to perform repairs without shutting down operations. These are critical in petrochemical facilities and power stations where every hour of downtime translates into substantial losses.
- TD Williamson offers SureLock™ series clamps, which are designed with pressure-monitoring integration. These clamps are used in pipelines that transport volatile gases, where precision in sealing and pressure control is mandatory.
- STATS Group’s clamp systems, including custom-engineered subsea clamps, are pressure-rated beyond conventional standards and include isolation features that support multiple maintenance operations simultaneously.
- PLIDCO’s Clamp+Sleeve and Split+Sleeve systems remain the go-to solution for pipeline operators requiring rugged, field-proven clamps for severe mechanical failures, including longitudinal splits and large-diameter holes.
These product lines reflect the shift toward modular, intelligent, and long-lasting solutions that align with the complexity of modern pipeline networks.
Regional Production Strength and Supply Chain Advantage
The production footprint in the Pipeline Emergency Repair Clamps Market is concentrated in North America, Europe, and East Asia. Manufacturers in the U.S. and Germany lead in high-performance clamps made from specialty alloys, while manufacturers in China and India produce standardized clamps in bulk to cater to high-volume markets.
North America serves as a hub for high-pressure and subsea repair clamp production. European companies focus on export-grade clamps with stringent safety certifications, especially for hydrogen and carbon capture pipelines. Asia’s manufacturers are expanding aggressively by developing cost-efficient models that can be customized for local infrastructure requirements.
Production scalability and proximity to pipeline-intensive regions give certain manufacturers a logistical and cost advantage. Manufacturers investing in local assembly units in the Middle East and Southeast Asia are better positioned to win government and municipal contracts in these fast-expanding regions.
Pipeline Emergency Repair Clamps Price and Market Dynamics
The Pipeline Emergency Repair Clamps Price varies substantially based on application, pressure rating, material, and diameter. Standard water distribution clamps for low-pressure lines may range between $50 and $300 per unit. In contrast, custom-engineered clamps for high-pressure oil and gas pipelines or subsea applications may exceed $3,000, with some large-diameter or sensor-integrated clamps priced above $10,000.
Datavagyanik observes that the Pipeline Emergency Repair Clamps Price Trend has seen upward movement over the past 12 months, largely due to rising raw material costs, increased demand for specialty alloys, and more complex customer requirements. The price of stainless steel-based clamps has increased by over 8%, while clamps using duplex or super duplex materials have seen double-digit inflation.
However, regional price stabilization is expected in the low- and mid-pressure segments as local production capacities expand. In Asia and Latin America, bulk procurement by public utilities and contractors is driving down per-unit pricing for standardized clamp solutions.
The Pipeline Emergency Repair Clamps Price Trend is expected to remain firm in the subsea and hydrogen pipeline categories, where certification, durability, and precision engineering drive premium pricing.
Recent Developments in the Pipeline Emergency Repair Clamps Market
The last 18 months have been transformative for the Pipeline Emergency Repair Clamps Market, marked by product launches, facility expansions, and strategic partnerships.
- In early 2023, multiple manufacturers expanded production capacity in response to increased demand from hydrogen infrastructure projects across Europe and North America.
- By mid-2023, several product lines were upgraded with integrated monitoring features, enabling remote condition tracking and predictive maintenance—key for operators managing critical energy infrastructure.
- In late 2023, new clamp variants were introduced for carbon dioxide pipelines, responding to the rising number of CCS (carbon capture and storage) projects entering development or execution phase.
- In Q1 2024, manufacturers entered partnerships with pipeline service providers in Southeast Asia and the Middle East to localize supply chains and reduce lead times for emergency deployments.
These developments reflect how the Pipeline Emergency Repair Clamps Market is evolving beyond traditional repair tools into a space where smart technology, sustainability, and regional customization are becoming central to competitive strategy.
“Pipeline Emergency Repair Clamps Production Data and Pipeline Emergency Repair Clamps Production Trend, Pipeline Emergency Repair Clamps Production Database and forecast”
-
-
- Pipeline Emergency Repair Clamps production database for historical years, 10 years historical data
- Pipeline Emergency Repair Clamps production data and forecast for next 7 years
-
Market Scenario, Demand vs Supply, Average Product Price, Import vs Export, till 2035
- Global Pipeline Emergency Repair Clamps Market revenue and demand by region
- Global Pipeline Emergency Repair Clamps Market production and sales volume
- United States Pipeline Emergency Repair Clamps Market revenue size and demand by country
- Europe Pipeline Emergency Repair Clamps Market revenue size and demand by country
- Asia Pacific Pipeline Emergency Repair Clamps Market revenue size and demand by country
- Middle East & Africa Pipeline Emergency Repair Clamps Market revenue size and demand by country
- Latin America Pipeline Emergency Repair Clamps Market revenue size and demand by
- Import-export scenario – United States, Europe, APAC, Latin America, Middle East & Africa
- Average product price – United States, Europe, APAC, Latin America, Middle East & Africa
- Market player analysis, competitive scenario, market share analysis
- Business opportunity analysis
Key questions answered in the Global Pipeline Emergency Repair Clamps Market Analysis Report:
- What is the market size for Pipeline Emergency Repair Clamps in United States, Europe, APAC, Middle East & Africa, Latin America?
- What is the yearly sales volume of Pipeline Emergency Repair Clamps and how is the demand rising?
- Who are the top market players by market share, in each product segment?
- Which is the fastest growing business/ product segment?
- What should be the business strategies and Go to Market strategies?
The report covers Pipeline Emergency Repair Clamps Market revenue, Production, Sales volume, by regions, (further split into countries):
- Asia Pacific (China, Japan, South Korea, India, Indonesia, Vietnam, Rest of APAC)
- Europe (UK, Germany, France, Italy, Spain, Benelux, Poland, Rest of Europe)
- North America (United States, Canada, Mexico)
- Latin America (Brazil, Argentina, Rest of Latin America)
- Middle East & Africa
Table of Contents:
Pipeline Emergency Repair Clamps Market
- Introduction to Pipeline Emergency Repair Clamps
1 Definition and Functionality of Repair Clamps
1.2 Critical Role in Pipeline Emergency Maintenance
1.3 Overview of Industry Applications - Market Segmentation by Clamp Type
1 Split Repair Clamps
2.2 Bolted Repair Clamps
2.3 High-Pressure Repair Clamps
2.4 Specialized Repair Clamps - Applications of Emergency Repair Clamps
1 Oil & Gas Pipelines
3.2 Water Supply Networks
3.3 Chemical and Industrial Pipelines
3.4 Subsea Pipeline Repair - Global Market Dynamics and Trends
1 Market Drivers and Growth Opportunities
4.2 Key Challenges in Adoption and Deployment
4.3 Emerging Trends in Pipeline Repair Technologies - Regional Market Analysis
1 North America Market Insights
5.2 Europe Market Growth Opportunities
5.3 Asia-Pacific Market Dynamics
5.4 Latin America Market Potential
5.5 Middle East & Africa Market Trends - Global Market Size and Forecast (2020-2035)
1 Historical Market Performance (2015-2019)
6.2 Forecasted Market Growth (2020-2035) - Competitive Landscape of Emergency Repair Clamps Market
1 Profiles of Leading Manufacturers
7.2 Market Share Analysis of Key Players
7.3 Strategic Developments in the Industry - Technological Innovations in Emergency Repair Clamps
1 Advances in Clamp Material Technology
8.2 Design Enhancements for Rapid Deployment
8.3 Integration of Monitoring Systems in Repair Solutions - Manufacturing Process and Cost Analysis
1 Overview of Manufacturing Techniques
9.2 Innovations in Production Efficiency
9.3 Cost Trends and Optimization Strategies - Material Analysis in Repair Clamp Manufacturing
1 Stainless Steel and Alloy Materials
10.2 Elastomers and Sealing Components
10.3 Advanced Composites for Lightweight Solutions - Market Segmentation by Pipeline Diameter Compatibility
1 Small-Diameter Pipeline Repair Clamps
11.2 Medium-Diameter Pipeline Repair Clamps
11.3 Large-Diameter Pipeline Repair Clamps - Environmental and Regulatory Compliance
1 Global Standards for Emergency Pipeline Repairs
12.2 Environmental Impact of Repair Clamp Usage
12.3 Regional Compliance Requirements - Industry-Specific Challenges and Solutions
1 Addressing High-Pressure Leakages
13.2 Enhancing Durability in Harsh Environments
13.3 Minimizing Downtime During Repairs - End-User Insights and Industry Demand
1 Oil & Gas Sector Demand Trends
14.2 Water Utilities and Infrastructure Projects
14.3 Industrial Pipeline Applications - Revenue and Pricing Analysis
1 Pricing Trends by Clamp Type
15.2 Regional Price Comparisons
15.3 Revenue Contributions by Industry - Customer Insights and Market Preferences
1 Factors Influencing Purchase Decisions
16.2 Regional Variations in Customer Needs - Distribution Channels and Marketing Strategies
1 Role of Distributors and Supply Chains
17.2 Direct Sales to Industrial Buyers
17.3 Digital Marketing for Repair Clamp Solutions - Innovations in Emergency Repair Clamp Design
1 Smart Clamps with Real-Time Monitoring Features
18.2 Modular Designs for Versatile Applications - Global Trade and Export Analysis
1 Key Exporting and Importing Countries
19.2 Trade Policies and Tariff Impacts - Future Trends in Emergency Pipeline Repair Solutions
1 Use of Smart Materials in Clamp Manufacturing
20.2 AI-Driven Maintenance and Repair Planning
20.3 Expanding Applications in Emerging Industries - Investment and Funding Landscape
1 Private Sector Investments in Repair Solutions
21.2 Public Infrastructure Development Initiatives - Case Studies and Real-World Applications
1 Successful Emergency Repairs Using Clamps
22.2 Lessons Learned from Complex Pipeline Failures - Key Risks and Mitigation Strategies
1 Risks Associated with Suboptimal Clamp Selection
23.2 Strategies for Reducing Repair Times - Sustainability and Lifecycle Management
1 Enhancing the Durability of Repair Clamps
24.2 Lifecycle Management for Long-Term Cost Savings - Market Outlook and Strategic Recommendations (2025-2035)
1 Key Growth Opportunities in Emerging Markets
25.2 Strategic Insights for Manufacturers and End-Users
25.3 Long-Term Trends Shaping the Industry
“Every Organization is different and so are their requirements”- Datavagyanik
Companies We Work With
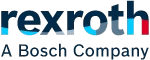
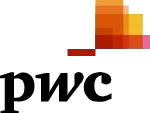
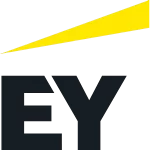
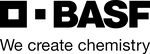
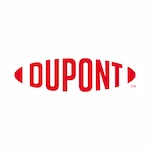

Do You Want To Boost Your Business?
drop us a line and keep in touch
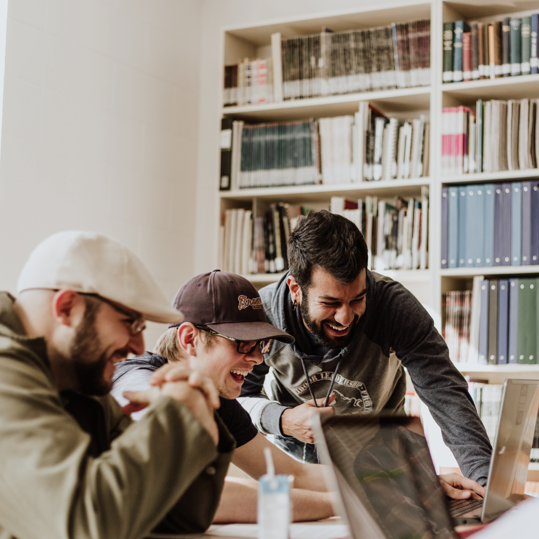