Refractory Material for Iron & Steel Market Size, Production, Sales, Average Product Price, Market Share, Import vs Export
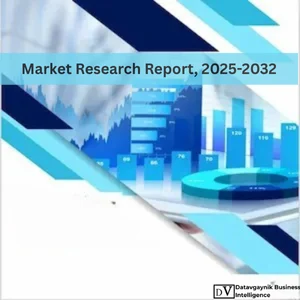
- Published 2025
- No of Pages: 120+
- 20% Customization available
Rapid Expansion in Refractory Material for Iron & Steel Market Driven by Steel Industry Growth
The refractory material for iron & steel market is witnessing rapid growth fueled by the continuous expansion of the global steel industry. Steel production globally has soared past two billion metric tons, with China, India, and Southeast Asia leading this surge. For instance, China’s output alone accounts for nearly half of the world’s steel, highlighting an immense base for refractory consumption. The growing demand for steel in construction, automotive, and infrastructure sectors is directly driving the need for refractory materials. Construction activities are expanding at a steady pace, with infrastructure projects increasing by over 5% annually, thereby pushing demand for high-quality steel, which requires durable refractory linings in furnaces.
Technological Innovations Accelerate Refractory Material for Iron & Steel Market Growth
The refractory material for iron & steel market is significantly influenced by advancements in steelmaking technologies. Electric arc furnaces (EAFs), responsible for about 40% of steel production globally, rely on refractory materials that withstand extremely high temperatures and harsh chemical environments. These materials must endure temperatures beyond 1800°C and resist corrosion from molten slags. Newer processes like hydrogen-based steelmaking also demand advanced refractory products with superior insulation and durability. Countries focused on cleaner steel production, such as Germany and Japan, are investing heavily in these next-gen refractories, driving market growth.
Energy Efficiency Drives Demand in Refractory Material for Iron & Steel Market
Steel manufacturing is highly energy-intensive, making energy efficiency a critical priority. The refractory material for iron & steel market benefits from this shift, as better thermal insulation reduces heat loss by up to 30%, cutting energy consumption significantly. For example, modern steel plants employing advanced refractory linings achieve energy savings of around 10-15%, leading to lower operational costs and enhanced sustainability. This focus on energy efficiency boosts the market as steelmakers seek refractories that improve furnace performance while meeting strict environmental standards.
Sustainability and Recycling Trends Reshape Refractory Material for Iron & Steel Market
Sustainability is reshaping the refractory material for iron & steel market as scrap steel recycling gains prominence. Electric arc furnaces, which produce over 60% of recycled steel worldwide, require refractory materials that can withstand frequent temperature swings and corrosive slag conditions. Emerging economies like India and South Korea are increasing their scrap recycling capacity by more than 7% annually, driving demand for high-performance refractories tailored for these processes. These materials extend furnace life, reduce downtime, and support the global push toward greener steel production.
Premium Steel Demand Fuels Growth in Refractory Material for Iron & Steel Market
The demand for premium steel products, especially in automotive, aerospace, and renewable energy sectors, is pushing the refractory material for iron & steel market forward. High-grade steel manufacturing requires refractories that prevent contamination, maintain thermal stability, and endure rigorous operating conditions. This trend towards specialty steels, such as lightweight alloys for automotive weight reduction or heat-resistant steel for aerospace engines, demands refractories with enhanced performance, thereby expanding the market.
Emerging Economies Amplify Refractory Material for Iron & Steel Market Demand
Emerging economies are key drivers of growth in the refractory material for iron & steel market due to expanding steel production capacities. Countries like India, Brazil, and Southeast Asian nations are rapidly increasing steel output, necessitating more refractory materials. For example, India’s steel production is growing at over 6% annually, propelled by infrastructure and automotive demand. This expansion requires robust refractory products to maintain furnace efficiency and reduce maintenance, increasing market size.
Stringent Environmental Regulations Propel Refractory Material for Iron & Steel Market
Environmental regulations worldwide are becoming more stringent, directly influencing the refractory material for iron & steel market. Steel producers must comply with lower emissions and improved energy efficiency, which requires high-quality refractories that enhance thermal insulation and reduce energy waste. Refractory materials contribute to controlling furnace heat losses and emissions, making them indispensable for sustainable steel production. Regulatory pressure especially in Europe and North America is catalyzing investments in advanced refractory technologies.
Extended Furnace Lifespan and Reduced Maintenance Boost Refractory Material for Iron & Steel Market
Increasing focus on operational efficiency is driving the demand for refractory material for iron & steel market products that extend furnace lifespan and minimize maintenance downtime. High-performance refractories protect steelmaking equipment from damage caused by extreme heat and corrosive materials, leading to fewer shutdowns and reduced repair costs. Steelmakers investing in durable refractory solutions gain competitive advantage through higher productivity, further fueling market demand.
Shift to Electric Arc Furnaces Spurs Specialized Refractory Material for Iron & Steel Market Demand
The growing adoption of electric arc furnaces for steel production, especially in scrap recycling, is a major driver for the refractory material for iron & steel market. EAFs impose intense thermal and chemical stresses on refractories, requiring tailored products with exceptional thermal shock resistance and durability. As EAF capacity increases globally, particularly in Asia and Europe, demand for specialized refractory materials is expanding rapidly.
Innovation in Material Science Elevates Refractory Material for Iron & Steel Market Potential
Advances in refractory material science are opening new opportunities in the refractory material for iron & steel market. Novel compositions combining alumina, magnesia, and carbon fibers improve heat resistance, mechanical strength, and lifespan. For example, composite refractories now enable steel plants to operate at higher temperatures with better energy efficiency. These innovations help manufacturers meet evolving steel production challenges, driving adoption and expanding market scope.
Refractory Material for Iron & Steel Market Size Expands with Diverse Application Segments
The refractory material for iron & steel market size is growing as demand surges across various application segments including blast furnaces, basic oxygen furnaces, ladles, and casting mills. Blast furnace refractories must endure extreme temperatures and chemical attack, while ladle refractories focus on maintaining molten steel temperature and preventing contamination. Each application requires specialized refractory materials, widening the market and providing multiple avenues for growth.
“Track Country-wise Refractory Material for Iron & Steel Production and Demand through our Refractory Material for Iron & Steel Production Database”
-
-
- Refractory Material for Iron & Steel production database for 32+ countries worldwide
- Refractory Material for Iron & Steel sales volume for 32+ countries
- Country-wise Refractory Material for Iron & Steel production capacity, production plant mapping, production capacity utilization for 32+ manufacturers
- Refractory Material for Iron & Steel production plants and production plant capacity analysis by top manufacturers
-
“Track real-time Refractory Material for Iron & Steel Prices, Refractory Material for Iron & Steel price charts for 32+ countries, Refractory Material for Iron & Steel weekly price tracker and Refractory Material for Iron & Steel monthly price tracker”
-
-
- Track real-time Refractory Material for Iron & Steel prices and Refractory Material for Iron & Steel price trend in 32+ countries though our excel-based Refractory Material for Iron & Steel price charts
- Real-time Refractory Material for Iron & Steel price tracker dashboard with 32+ countries
- Complete transparency on Refractory Material for Iron & Steel price trend through our Refractory Material for Iron & Steel monthly price tracker, Refractory Material for Iron & Steel weekly price tracker
-
Geographical Demand Patterns in Refractory Material for Iron & Steel Market
The geographical demand for refractory material for iron & steel market is heavily influenced by regional steel production volumes and technological advancements. Asia Pacific stands out as the largest consumer, fueled by rapid industrialization and infrastructure development in countries such as China, India, and Southeast Asia. For example, China’s steel output exceeds one billion metric tons annually, which drives an estimated 7% yearly increase in refractory material consumption. India’s growing steel production capacity, expanding at more than 6% per year, is intensifying the need for high-performance refractories to support new and upgraded steelmaking facilities. Southeast Asian countries like Vietnam and Indonesia are also emerging as significant markets due to increased steel mill construction and modernization.
In North America, the refractory material for iron & steel market grows steadily at about 3% annually, driven primarily by the United States. The adoption of electric arc furnace (EAF) technology for scrap steel recycling has stimulated demand for refractories that can handle intense thermal cycling. Meanwhile, Europe’s market is shaped by stringent environmental regulations and a push towards sustainable steel production. Germany and Italy are at the forefront, with demand for refractory materials rising by over 5% annually as steelmakers shift towards green technologies and carbon-neutral processes.
Production Capacity and Trends in Refractory Material for Iron & Steel Market
The production of refractory material for iron & steel market is heavily concentrated in the Asia Pacific region, where China leads with more than 60% of global manufacturing capacity. Chinese producers have focused on expanding output of key refractory types such as magnesia, alumina, and carbon-based materials, to meet the surging needs of their vast domestic steel industry. India is rapidly scaling up its production, driven by the country’s expanding steel sector and the desire to reduce import dependence. Japan maintains a strong position in producing high-quality, technologically advanced refractories, supporting its sophisticated steelmaking industry that prioritizes energy efficiency and sustainability.
Europe’s refractory production is characterized by innovation and customization, catering to the demands of a mature but evolving steel market. Countries like Germany and Italy invest in advanced refractory formulations to support emerging steelmaking technologies including hydrogen-based processes and electric arc furnaces. In North America, production focuses on supplying specialty refractory materials to support modern steel plants emphasizing environmental compliance and operational efficiency.
Market Segmentation by Material Type in Refractory Material for Iron & Steel Market
The refractory material for iron & steel market is segmented based on material types that cater to specific steelmaking requirements. Clay-based refractories remain widely used due to their cost-effectiveness and versatility, accounting for a substantial share of furnace linings especially in blast furnace operations. Silica-based refractories are favored for their excellent resistance to thermal shock and are primarily deployed in electric arc furnaces where high-temperature fluctuations are common.
Magnesia-based refractories dominate applications involving basic oxygen furnaces, valued for their durability against corrosive slags. Alumina-based materials are sought after for applications requiring high wear resistance such as ladles, tundishes, and steel casting equipment. Carbon-based refractories are essential in non-oxidizing environments and high-temperature conditions where thermal shock resistance is critical. The diversification across these materials enables steelmakers to optimize furnace performance and longevity while meeting increasing demands for efficiency.
Market Segmentation by Application Driving Refractory Material for Iron & Steel Market Growth
Application-wise, the refractory material for iron & steel market encompasses blast furnaces, electric arc furnaces, basic oxygen furnaces, ladles and tundishes, as well as steel casting and rolling mills. Blast furnace refractories must withstand extremely high temperatures and corrosive environments, supporting iron smelting processes fundamental to steel production. The rising adoption of electric arc furnaces, especially for scrap steel recycling, is expanding demand for refractory materials designed to endure rapid temperature changes and intense electrical currents.
Basic oxygen furnaces rely on magnesia-based refractories that provide resistance to corrosive slags generated during steel refining. Ladle and tundish refractories are critical for maintaining molten steel temperatures and preventing contamination, requiring materials with excellent thermal cycling resistance. In steel casting and rolling mills, refractories ensure smooth operation by protecting equipment from molten steel exposure and mechanical wear. The expansion of each of these applications, particularly driven by trends such as scrap recycling and sustainable production, fuels the overall growth of the refractory market.
Market Segmentation by Product Form in Refractory Material for Iron & Steel Market
The product form segment of the refractory material for iron & steel market includes bricks, monolithics, precast shapes, and fibers. Refractory bricks are the most common and widely used due to their ease of installation and ability to form robust furnace linings. Monolithic refractories, consisting of unshaped castable or ramming mixes, are gaining popularity for their flexibility in application and superior joint integrity, especially in complex furnace geometries.
Precast shapes offer advantages in reducing installation time and ensuring precision fit, making them preferable in specialized steelmaking equipment. Refractory fibers serve crucial roles in insulation and fireproofing, particularly in areas requiring low thermal mass and lightweight solutions such as steel casting and rolling operations. The expanding adoption of monolithics and precast shapes reflects the steel industry’s focus on operational efficiency and rapid maintenance turnarounds.
Refractory Material for Iron & Steel Price Trends Shaping Market Dynamics
The refractory material for iron & steel price trend has been influenced by raw material availability, production costs, and demand-supply dynamics. Over recent years, the market has seen moderate price increases averaging 3-5% annually, driven by rising costs of key inputs such as magnesite, alumina, and carbon materials. For instance, fluctuations in magnesite prices, affected by mining capacity and export policies in major producing countries, directly impact refractory pricing.
The shift toward higher-performance and specialized refractory products also contributes to upward pressure on prices, as these materials often require advanced manufacturing processes and premium raw materials. However, technological improvements and economies of scale, especially in Asia, have moderated price volatility, allowing steelmakers to access cost-effective refractory solutions without compromising quality.
Impact of Regional Price Variations on Refractory Material for Iron & Steel Market
Regional variations in refractory material for iron & steel price trends reflect differences in production infrastructure, raw material proximity, and logistics costs. Asia Pacific generally offers competitive pricing due to abundant raw material resources and large-scale production, enabling Chinese and Indian refractory manufacturers to supply both domestic and export markets at favorable rates.
In contrast, refractory materials in North America and Europe tend to be priced higher, driven by stricter environmental compliance costs and advanced product specifications. However, these markets often prioritize quality and sustainability over cost alone, leading to steady demand for premium refractory solutions despite higher price points. This regional pricing dynamic encourages manufacturers to tailor products and supply chains to meet varying market expectations.
Market Segmentation by End-User Industry in Refractory Material for Iron & Steel Market
The end-user industry segmentation of the refractory material for iron & steel market highlights automotive, construction, energy, aerospace, and heavy manufacturing sectors. Automotive steel demand is rising due to the need for lightweight, high-strength materials, boosting refractory demand for producing specialty steel grades. The construction sector’s steady growth drives demand for reinforced steel and structural steel components, increasing furnace throughput and refractory consumption.
Energy and power generation industries require steel for infrastructure such as wind turbines and nuclear reactors, promoting the adoption of refractory materials in the production of energy-grade steel. Aerospace and defense sectors’ focus on heat-resistant, lightweight alloys further intensifies the need for high-performance refractories capable of supporting complex steel formulations. Heavy industries and manufacturing continue to demand refractory materials that ensure durability and operational continuity in harsh thermal environments.
Future Outlook and Price Trends in Refractory Material for Iron & Steel Market
Looking ahead, the refractory material for iron & steel price trend is expected to be influenced by ongoing raw material cost pressures, increasing demand for sustainable and energy-efficient products, and technological innovations. Price growth of 4-6% annually is anticipated as steelmakers invest in longer-lasting refractory solutions that offer improved thermal insulation and reduced maintenance costs.
Sustainability initiatives and stricter regulations are expected to push refractory manufacturers toward eco-friendly raw materials and low-carbon production methods, potentially impacting cost structures. Nonetheless, increased production efficiencies and expanded manufacturing capacities, particularly in Asia, will help balance price increases and sustain market growth globally.
“Refractory Material for Iron & Steel Manufacturing Database, Refractory Material for Iron & Steel Manufacturing Capacity”
-
-
- Refractory Material for Iron & Steel top manufacturers market share for 32+ manufacturers
- Top 12 manufacturers and top 19 manufacturers of Refractory Material for Iron & Steel in North America, Europe, Asia Pacific
- Refractory Material for Iron & Steel production plant capacity by manufacturers and Refractory Material for Iron & Steel production data for 32+ market players
- Refractory Material for Iron & Steel production dashboard, Refractory Material for Iron & Steel production data in excel format
-
“Refractory Material for Iron & Steel price charts, Refractory Material for Iron & Steel weekly price tracker and Refractory Material for Iron & Steel monthly price tracker”
-
-
- Factors impacting real-time Refractory Material for Iron & Steel prices in 32+ countries worldwide
- Refractory Material for Iron & Steel monthly price tracker, Refractory Material for Iron & Steel weekly price tracker
- Real-time Refractory Material for Iron & Steel price trend, Refractory Material for Iron & Steel price charts, news and updates
- Tracking Refractory Material for Iron & Steel price fluctuations
-
Key Manufacturers Shaping the Refractory Material for Iron & Steel Market
The refractory material for iron & steel market is dominated by a blend of global giants and specialized regional players who collectively drive innovation, production capacity, and market dynamics. Leading manufacturers command significant market shares through diversified product portfolios that cater to various steelmaking processes and application segments. These companies leverage technological expertise and extensive R&D investments to maintain competitive advantages in this highly specialized sector.
Market Share Distribution in Refractory Material for Iron & Steel Market
Within the refractory material for iron & steel market, a few multinational corporations hold a dominant share estimated at over 40% collectively. The remaining market is fragmented among regional producers who focus on localized supply chains and customized refractory solutions. The market share concentration is reflective of the capital-intensive nature of refractory manufacturing and the critical role of quality and performance in steel production.
Top players maintain their market leadership by offering comprehensive refractory product lines that address a wide range of steelmaking needs, from blast furnaces and basic oxygen furnaces to electric arc furnaces and ladle applications. Their ability to innovate with materials that improve thermal efficiency, durability, and sustainability ensures steady demand for their offerings.
RHI Magnesita: A Global Leader in Refractory Material for Iron & Steel Market
RHI Magnesita stands as one of the foremost manufacturers in the refractory material for iron & steel market, commanding a significant global market share. Its portfolio spans magnesia-based refractories, alumina bricks, and carbon-bonded products engineered for high-temperature steelmaking environments. Key product lines such as the Magmax® series and DURACARB® carbon products are renowned for their thermal shock resistance and slag corrosion durability, making them favored choices in blast furnace and electric arc furnace operations.
RHI Magnesita’s ongoing investments in digital manufacturing technologies and sustainability initiatives, including the development of low-carbon refractory materials, bolster its market position. The company’s strategic acquisitions and global production network allow it to serve the growing refractory demand across Asia, Europe, and the Americas efficiently.
Saint-Gobain: Innovation and Sustainability in Refractory Material for Iron & Steel Market
Saint-Gobain’s refractory business contributes robustly to the refractory material for iron & steel market, offering a broad spectrum of products tailored for the steel industry’s evolving requirements. The company’s Rigidex® and MAXIT® refractory lines, known for their high strength and thermal stability, are extensively used in electric arc furnaces, ladles, and basic oxygen furnaces.
Saint-Gobain’s emphasis on research has yielded proprietary refractory formulations that enhance energy efficiency and furnace lifespan. The firm’s commitment to environmental sustainability is evident in its development of eco-friendly refractories that reduce CO2 emissions during production and use. Saint-Gobain’s strategic presence in Europe and North America, combined with expanding footprints in Asia, contributes to its solid share in the refractory material for iron & steel market.
Vesuvius plc: Specialist Solutions Driving Market Share Growth
Vesuvius plc commands a notable position in the refractory material for iron & steel market, specializing in precision-engineered refractory solutions for high-performance steelmaking processes. Its product portfolio includes the Thermotec® range for ladle and tundish applications and the MagnaTherm® magnesia-based bricks designed for basic oxygen furnaces and electric arc furnaces.
Known for its close collaboration with steel producers, Vesuvius emphasizes customized refractory systems that optimize furnace operation and reduce downtime. Its technical expertise in thermal management and slag resistance has earned the company increased market share, particularly in emerging steel markets across Asia Pacific and Latin America.
HarbisonWalker International: Heritage and Innovation in Refractory Material for Iron & Steel Market
HarbisonWalker International (HWI) is a key player in the refractory material for iron & steel market with a long-standing reputation for producing quality refractory bricks and monolithics. The company’s product lines such as the MagnaLite® series and HWI Carbon™ bricks serve critical roles in blast furnaces, ladles, and continuous casting operations.
HWI’s focus on innovation has led to the development of refractory solutions that extend furnace life and improve energy retention. Their expertise in carbon-based refractories supports steelmakers aiming for enhanced operational efficiency. The company’s strong presence in North America and strategic partnerships worldwide contribute to its steady market share.
Imerys Refractory Minerals: Raw Material Supplier Impacting the Market
While not a direct manufacturer of refractory shapes, Imerys Refractory Minerals plays a crucial role in the refractory material for iron & steel market by supplying high-purity raw materials such as alumina, magnesia, and chamotte. The quality of raw inputs directly affects the performance and durability of refractory products, making Imerys a key upstream player. Its materials are widely used by refractory manufacturers, thus indirectly influencing market trends and product innovations.
Other Regional and Emerging Players in Refractory Material for Iron & Steel Market
Several regional players contribute to the refractory material for iron & steel market by serving localized steel industries with customized solutions. Companies such as Orient Refractories in India, Magnezit Group in Russia and Eastern Europe, and Harbin Refractories in China are expanding production capacities and innovating in magnesia-based and carbon refractory technologies. These companies often focus on competitive pricing and agility to capture growing demand in emerging markets, steadily increasing their market shares.
Recent Industry Developments and Market Movements
Throughout the past year, the refractory material for iron & steel market has witnessed notable developments reflecting broader steel industry trends. In early 2024, RHI Magnesita announced the launch of a new low-carbon refractory product line aimed at reducing environmental impact while enhancing furnace efficiency. This innovation aligns with the global push for greener steelmaking and positions RHI Magnesita as a front-runner in sustainable refractory solutions.
In mid-2024, Saint-Gobain expanded its production facilities in Southeast Asia, responding to rising refractory demand driven by increased steel capacity additions in the region. This expansion reflects the growing importance of Asia Pacific as a core market for refractory materials.
Vesuvius plc recently secured a multi-year supply agreement with a major steel producer in India, focusing on advanced refractory linings for electric arc furnaces. This contract underscores the trend of close partnerships between refractory manufacturers and steelmakers to optimize furnace performance and lifecycle.
HarbisonWalker International announced in late 2023 its investment in automation technologies for refractory brick manufacturing, aimed at improving product consistency and reducing production costs. This move highlights ongoing efforts within the industry to enhance manufacturing efficiencies in a competitive market.
Several mergers and acquisitions have reshaped the refractory material for iron & steel market landscape recently. These strategic moves allow leading companies to consolidate their market position, access new geographies, and broaden product portfolios to meet diverse steelmaking needs.
“Refractory Material for Iron & Steel Production Data and Refractory Material for Iron & Steel Production Trend, Refractory Material for Iron & Steel Production Database and forecast”
-
-
- Refractory Material for Iron & Steel production database for historical years, 12 years historical data
- Refractory Material for Iron & Steel production data and forecast for next 12 years
- Refractory Material for Iron & Steel sales volume by manufacturers
-
“Track Real-time Refractory Material for Iron & Steel Prices for purchase and sales contracts, Refractory Material for Iron & Steel price charts, Refractory Material for Iron & Steel weekly price tracker and Refractory Material for Iron & Steel monthly price tracker”
-
-
- Gain control on your purchase and sales contracts through our real-time Refractory Material for Iron & Steel price tracker and Refractory Material for Iron & Steel price trend analysis
- Refractory Material for Iron & Steel weekly price tracker and forecast for next four weeks
- Refractory Material for Iron & Steel monthly price tracker and forecast for next two months
-
Market Scenario, Demand vs Supply, Average Product Price, Import vs Export, till 2035
- Global Refractory Material for Iron & Steel Market revenue and demand by region
- Global Refractory Material for Iron & Steel Market production and sales volume
- United States Refractory Material for Iron & Steel Market revenue size and demand by country
- Europe Refractory Material for Iron & Steel Market revenue size and demand by country
- Asia Pacific Refractory Material for Iron & Steel Market revenue size and demand by country
- Middle East & Africa Refractory Material for Iron & Steel Market revenue size and demand by country
- Latin America Refractory Material for Iron & Steel Market revenue size and demand by
- Import-export scenario – United States, Europe, APAC, Latin America, Middle East & Africa
- Average product price – United States, Europe, APAC, Latin America, Middle East & Africa
- Market player analysis, competitive scenario, market share analysis
- Business opportunity analysis
Key questions answered in the Global Refractory Material for Iron & Steel Market Analysis Report:
- What is the market size for Refractory Material for Iron & Steel in United States, Europe, APAC, Middle East & Africa, Latin America?
- What is the yearly sales volume of Refractory Material for Iron & Steel and how is the demand rising?
- Who are the top market players by market share, in each product segment?
- Which is the fastest growing business/ product segment?
- What should be the business strategies and Go to Market strategies?
The report covers Refractory Material for Iron & Steel Market revenue, Production, Sales volume, by regions, (further split into countries):
- Asia Pacific (China, Japan, South Korea, India, Indonesia, Vietnam, Rest of APAC)
- Europe (UK, Germany, France, Italy, Spain, Benelux, Poland, Rest of Europe)
- North America (United States, Canada, Mexico)
- Latin America (Brazil, Argentina, Rest of Latin America)
- Middle East & Africa
Table of Contents:
Refractory Material for Iron & Steel Market:
- Introduction to Refractory Materials for Iron & Steel Market
- Definition and role of refractory materials in the iron and steel industry
- Importance of refractories in high-temperature applications
- Overview of the global refractory materials market for iron and steel
- Market Dynamics of Refractory Materials for Iron & Steel
- Key drivers of market growth in the iron and steel sector
- Challenges in the production and application of refractories
- Emerging opportunities for innovation and market expansion
- Global Market Overview of Refractory Materials for Iron & Steel
- Historical market trends and key market players
- Market size and revenue projections (2025-2035)
- Global market drivers and influencing factors
- Types of Refractory Materials for Iron & Steel Production
- Acidic refractories (e.g., silica)
- Basic refractories (e.g., magnesia, dolomite)
- Neutral refractories (e.g., alumina, carbon)
- Specialized refractories for high-temperature furnaces
- Applications of Refractory Materials in Iron & Steel Production
- Use in blast furnaces and electric arc furnaces
- Application in ladles, converters, and other steelmaking equipment
- Role of refractories in casting, lining, and heat treatment processes
- Technological Advancements in Refractory Materials for Iron & Steel
- Innovations in refractory production technologies
- Development of high-performance, durable refractories
- Advanced testing and quality assurance methods for refractory materials
- Regional Market Insights for Refractory Materials
- North America: Market growth and technological adoption
- Europe: Key trends in refractory demand and sustainability
- Asia Pacific: Dominance in iron and steel production and refractories consumption
- Market developments in Latin America, Middle East, and Africa
- Market Size, Share, and Forecast (2025-2035)
- Market size estimation and growth projections
- Segment-wise breakdown: materials, applications, and regions
- Future growth opportunities and regional growth drivers
- Competitive Landscape in the Refractory Materials for Iron & Steel Market
- Leading manufacturers and suppliers in the refractory materials industry
- Competitive strategies and market share analysis
- Company profiles and technological capabilities
- Production and Manufacturing of Refractory Materials
- Overview of refractory material production processes
- Raw materials used in manufacturing refractories
- Challenges in scaling up production to meet demand
- Cost Structure and Pricing Analysis
- Breakdown of manufacturing costs: raw materials, labor, and energy
- Pricing trends for refractory materials in the iron and steel market
- Projected price fluctuations and market factors influencing costs
- Supply Chain and Distribution Channels
- Key suppliers of raw materials for refractory production
- Distribution strategies for refractory materials in the global market
- Supply chain challenges and opportunities in a globalized industry
- Environmental Impact and Sustainability in Refractory Production
- Environmental concerns related to refractory production
- Innovations in eco-friendly refractories and sustainable practices
- Industry efforts to reduce carbon emissions and material waste
- Raw Material Sourcing for Refractory Materials
- Key raw materials for refractory production (e.g., magnesite, bauxite, silica)
- Supply chain risks and material sourcing challenges
- Exploration of alternative raw materials and sustainable sourcing practices
- Regulatory and Safety Standards in the Refractory Materials Market
- Industry standards for refractories used in iron and steel production
- Regulatory frameworks and compliance requirements in key markets
- Safety standards for handling and applying refractory materials
- Market Opportunities in Emerging Economies
- Rising demand for steel in developing economies and its impact on refractories
- Opportunities for manufacturers to penetrate new markets in Asia, Africa, and Latin America
- Strategic partnerships and investments in emerging markets
- Challenges and Barriers in the Refractory Materials Market
- Technical challenges in producing high-performance refractories
- Volatility in raw material prices and its effect on market growth
- Competition from alternative materials and technologies
- Consumer Trends and Adoption of Refractory Materials
- Growing demand for high-efficiency and long-lasting refractories
- The impact of industry trends such as automation and energy efficiency
- Shifting consumer preferences in steel production and refractory performance
- Strategic Recommendations for Stakeholders
- Business strategies for manufacturers, suppliers, and distributors
- Recommendations for improving operational efficiency and market penetration
- Future growth areas and investment opportunities
- Conclusion and Future Market Outlook
- Summary of key insights and market trends
- Long-term growth projections for the refractory materials market in iron and steel
- Final thoughts on the evolving landscape and future opportunities
Other recently published reports:
“Every Organization is different and so are their requirements”- Datavagyanik
Companies We Work With
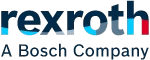
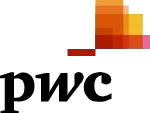
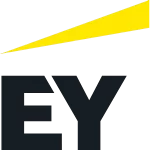
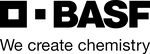
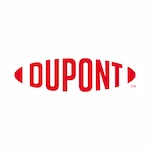

Do You Want To Boost Your Business?
drop us a line and keep in touch
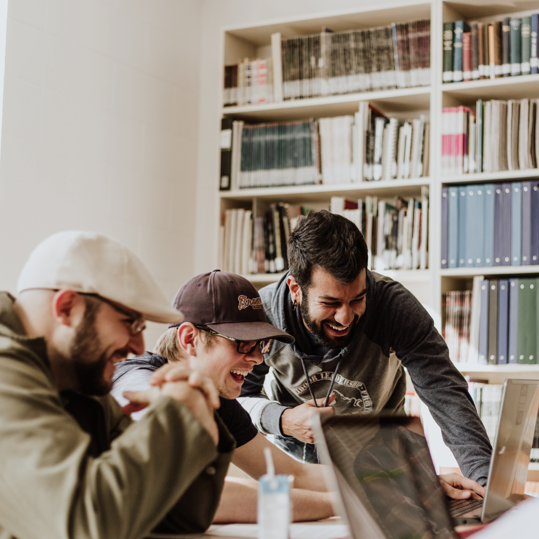