Russia Anti-Corrosion Coatings for Oil Pipelines Market Revenue, Production, Consumption, Average Price, Import vs Export
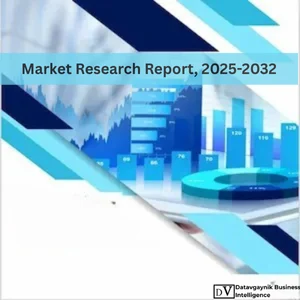
- Published 2025
- No of Pages: 120+
- 20% Customization available
Anti-Corrosion Coatings for Oil Pipelines Market in Russia: An Overview
Russia, as one of the largest producers and exporters of oil globally, heavily relies on an extensive network of pipelines to transport hydrocarbons across its vast territory and to international markets. The durability and efficiency of these pipelines are vital for maintaining uninterrupted oil supply chains. Anti-corrosion coatings play a pivotal role in protecting pipeline infrastructure from degradation caused by environmental factors, chemical exposure, and extreme weather conditions. The Russia anti-corrosion coatings market is a key segment of the country’s energy sector, ensuring the longevity and reliability of oil pipeline systems.
As exploration activities extend into harsh environments such as the Arctic and Siberia, the demand for advanced anti-corrosion coatings is projected to grow substantially. This market presents significant opportunities for manufacturers, suppliers, and service providers aiming to cater to the unique challenges of Russia’s oil pipeline network.
Market Size and Growth Potential
The Russia anti-corrosion coatings for oil pipelines market has been experiencing consistent growth, driven by the expansion of the country’s pipeline infrastructure and the rising emphasis on maintaining operational efficiency. The market size is expected to surpass $1 billion by 2030, with a compound annual growth rate (CAGR) of approximately 5-7% over the next decade.
Key factors contributing to this growth include:
- Expansion of New Pipelines: Russia’s focus on tapping into new oil fields, particularly in Eastern Siberia and the Arctic, is driving the demand for high-performance coatings.
- Aging Infrastructure: Many pipelines in Western Russia and the Volga-Ural region require refurbishment and maintenance, boosting demand for anti-corrosion products.
- Export-Oriented Infrastructure: With Russia serving as a major energy supplier to Europe and Asia, the need to protect pipelines from environmental and operational challenges is critical for sustaining export reliability.
This steady growth trajectory underscores the importance of anti-corrosion coatings in supporting Russia’s energy sector and highlights the market’s potential for long-term investments.
Segmentation of the Russia Anti-Corrosion Coatings Market
The market can be segmented based on various criteria, providing insights into its structure and dynamics:
- By Coating Type:
- Fusion-Bonded Epoxy Coatings (FBE): Widely used for their excellent resistance to corrosion and abrasion.
- Polyurethane Coatings: Known for their durability and flexibility under extreme conditions.
- Polyethylene Coatings: Provide a strong barrier against moisture and chemicals.
- Coal Tar Enamel Coatings: Used for traditional pipeline protection.
- Zinc-Rich Coatings: Offer sacrificial protection against corrosion.
- By Application Method:
- External Coatings: Protect pipelines from environmental factors such as moisture and temperature fluctuations.
- Internal Coatings: Prevent corrosion caused by the flow of crude oil and natural gas.
- By Pipeline Type:
- Transmission Pipelines: Long-distance pipelines transporting crude oil to refineries or export terminals.
- Distribution Pipelines: Local pipelines delivering oil to end-users.
- By Geography:
- Western Russia: High demand for maintenance coatings due to aging infrastructure.
- Eastern Siberia and Arctic: Increasing demand for advanced coatings due to challenging environmental conditions.
- Volga-Ural Region: Steady demand driven by mature oil fields and secondary recovery projects.
- By End-User:
- Oil and Gas Companies: State-owned enterprises like Transneft dominate this segment.
- Pipeline Construction Firms: Companies involved in laying new pipelines.
- Maintenance Service Providers: Firms specializing in refurbishing existing pipelines.
Key Drivers and Market Opportunities
The growth of the Russia anti-corrosion coatings market is propelled by several critical drivers and opportunities:
- Infrastructure Expansion in Harsh Environments: Russia’s push to develop new oil fields in the Arctic and Eastern Siberia has created a demand for coatings that can withstand extreme temperatures, moisture, and chemical exposure.
- Refurbishment of Aging Pipelines: Many of Russia’s pipelines, particularly in Western Siberia and the Volga-Ural region, were built decades ago and require regular maintenance to remain operational.
- Technological Advancements: Innovations in coating materials, such as nanotechnology and hybrid coatings, are improving durability and performance, driving market growth.
- Government Support: State investments in pipeline infrastructure and maintenance projects provide a stable demand for anti-corrosion coatings.
- Export Growth: With pipelines transporting oil to Europe and Asia, ensuring the integrity of these assets is critical for sustaining Russia’s position as a global energy supplier.
These drivers highlight the market’s resilience and the opportunities it presents for businesses to innovate and expand.
Challenges in the Market
Despite its growth potential, the Russia anti-corrosion coatings market faces several challenges:
- Environmental Regulations: Stricter policies aimed at reducing environmental impact require manufacturers to develop eco-friendly and biodegradable coatings, which may increase production costs.
- Geopolitical Factors: Trade restrictions and sanctions on Russia could limit access to advanced coating technologies and raw materials.
- Harsh Operating Conditions: Pipelines in Siberia and the Arctic face extreme weather, necessitating specialized coatings that can endure sub-zero temperatures and high pressures.
- High Initial Costs: Advanced anti-corrosion coatings often involve higher upfront costs, which may deter some operators from adopting them.
- Economic Uncertainty: Fluctuations in global oil prices and demand can impact investments in pipeline infrastructure and maintenance.
Addressing these challenges will require innovation, strategic partnerships, and investments in local manufacturing capabilities.
Regional Insights: Opportunities Across Russia
The geographical diversity of Russia creates unique demands for anti-corrosion coatings:
- Western Russia: As the oldest oil-producing region, Western Russia has a vast network of aging pipelines requiring refurbishment. This creates a steady demand for maintenance coatings such as fusion-bonded epoxy and zinc-rich products.
- Eastern Siberia and Arctic: These regions represent the future of Russia’s oil and gas exploration. The extreme conditions in these areas require advanced coatings that can withstand harsh climates, creating opportunities for manufacturers of high-performance products.
- Volga-Ural Region: Known for its mature oilfields, this region relies on coatings to maintain pipeline integrity and support secondary recovery efforts.
Understanding these regional dynamics enables manufacturers to tailor their offerings and establish a strong presence in the market.
Forecast and Business Strategies
The Russia anti-corrosion coatings market is poised for significant growth, with opportunities for both domestic and international players. Key strategies for success include:
- Investing in Innovation: Developing advanced coating materials, such as hybrid and nanotechnology-based solutions, to address the unique challenges of Russian oil pipelines.
- Focusing on Sustainability: Offering eco-friendly and low-VOC (volatile organic compound) coatings to comply with environmental regulations and appeal to environmentally conscious buyers.
- Localization: Establishing production facilities in Russia to reduce dependency on imports and align with the government’s import substitution policies.
- Collaborating with Key Stakeholders: Partnering with pipeline operators, construction firms, and maintenance providers to deliver tailored solutions.
- Targeting Emerging Regions: Expanding into Eastern Siberia and the Arctic, where demand for specialized coatings is expected to grow.
By adopting these strategies, businesses can capitalize on the market’s growth potential and position themselves as leaders in this critical segment.
Comprehensive Market Segmentation in Russia’s Anti-Corrosion Coatings for Oil Pipelines Market
The anti-corrosion coatings market for oil pipelines in Russia is segmented across various criteria to address the unique challenges and requirements of the country’s vast oil pipeline infrastructure. These segmentations are essential for understanding the market dynamics, identifying growth opportunities, and crafting effective strategies. Below is a detailed list of all possible market segmentations, followed by an in-depth discussion of the most critical ones that define the market’s direction in Russia.
All Possible Market Segmentation
- By Coating Type
- Fusion-Bonded Epoxy (FBE) Coatings: Widely used for external pipeline protection due to their excellent adhesion and durability.
- Polyurethane Coatings: Preferred for their high flexibility and resistance to harsh chemicals.
- Polyethylene Coatings: Provide robust protection against moisture and chemical exposure.
- Coal Tar Enamel Coatings: A traditional option for pipeline protection.
- Zinc-Rich Coatings: Offer sacrificial protection to prevent corrosion.
- Hybrid Coatings: Combine the benefits of multiple coating technologies for enhanced performance.
- Ceramic Coatings: High-performance coatings used in extreme conditions.
- By Application Area
- External Coatings: Applied to the outer surface of pipelines to protect against environmental factors like moisture, temperature changes, and soil corrosion.
- Internal Coatings: Applied to the inner surface of pipelines to prevent corrosion from the transported fluid, such as crude oil or natural gas.
- By Pipeline Type
- Transmission Pipelines: Long-distance pipelines transporting crude oil to refineries or export terminals.
- Distribution Pipelines: Local pipelines delivering oil and refined products to end-users.
- Subsea Pipelines: Offshore pipelines requiring advanced coatings to withstand saltwater corrosion and high pressure.
- By Coating Technology
- Solvent-Based Coatings: Offer good adhesion and flexibility but may face restrictions due to environmental concerns.
- Water-Based Coatings: Environmentally friendly and gaining popularity for their low VOC (volatile organic compound) content.
- Powder Coatings: Provide a durable and seamless finish, often used for fusion-bonded epoxy coatings.
- Hot-Melt Coatings: Used for polyethylene and other thermoplastic coatings.
- By Base Material
- Epoxy-Based Coatings: Known for excellent adhesion and chemical resistance.
- Polyurethane-Based Coatings: Offer flexibility and weather resistance.
- Acrylic-Based Coatings: Provide a cost-effective solution with good weatherability.
- Ceramic-Based Coatings: High-performance coatings for extreme conditions.
- By End-User
- Pipeline Operators: Companies like Transneft, which operate Russia’s extensive oil pipeline network.
- Oilfield Service Providers: Firms involved in the application and maintenance of coatings.
- Construction Companies: Companies building new pipeline infrastructure.
- Government and Regulatory Bodies: Entities focused on ensuring compliance with safety and environmental standards.
- By Region
- Western Russia: Home to older pipelines requiring regular maintenance and refurbishments.
- Eastern Siberia and Arctic: Rapidly growing regions with harsh environmental conditions demanding advanced coatings.
- Volga-Ural Region: Known for its aging infrastructure, driving steady demand for maintenance coatings.
- Southern Russia: Focused on distribution pipelines and export routes.
- By Functionality
- Corrosion Protection: The primary function of most coatings.
- Abrasion Resistance: Important for pipelines subjected to mechanical wear.
- Chemical Resistance: Crucial for pipelines exposed to aggressive chemicals.
- Temperature Resistance: Ensures durability under extreme temperatures, particularly in Arctic regions.
- By Pipeline Material
- Carbon Steel Pipelines: The most common material requiring anti-corrosion coatings.
- Stainless Steel Pipelines: Less susceptible to corrosion but still require coatings for added protection in aggressive environments.
- Composite Pipelines: Demand coatings compatible with their material properties.
Most Important Market Segmentations with Explanation
- By Coating Type
The type of coating used is the most critical segmentation in Russia’s anti-corrosion coatings market due to the diverse environmental and operational challenges faced by the country’s oil pipeline infrastructure:
- Fusion-Bonded Epoxy (FBE) Coatings are the most widely used, particularly for external protection of transmission pipelines. They provide excellent adhesion, abrasion resistance, and durability, making them suitable for Russia’s vast network of long-distance pipelines.
- Polyurethane Coatings are preferred in regions like Eastern Siberia and the Arctic due to their flexibility and resistance to extreme cold temperatures.
- Polyethylene Coatings are commonly used for pipelines exposed to moisture and soil corrosion, offering strong barrier protection.
- Zinc-Rich Coatings are essential for sacrificial protection in aging pipelines, particularly in Western Russia.
This segmentation highlights opportunities for manufacturers to develop advanced coatings tailored to the unique needs of the Russian market.
- By Region
Geographical segmentation is crucial for understanding regional demand patterns:
- Western Russia is home to the oldest oil pipelines, many of which require regular maintenance. The demand for refurbishment coatings like zinc-rich and epoxy-based products is high in this region.
- Eastern Siberia and Arctic are emerging as the fastest-growing markets due to ongoing exploration activities and new pipeline projects. The harsh environmental conditions in these regions necessitate the use of high-performance coatings, such as polyurethane and ceramic coatings.
- Volga-Ural Region has a mix of mature and relatively new pipelines, driving demand for a wide range of coating technologies to support both maintenance and new construction.
- Southern Russia focuses on distribution pipelines, where the demand for cost-effective and durable coatings is high.
This segmentation enables manufacturers to align their product offerings with the specific challenges and opportunities of each region.
- By Application Area
Application-based segmentation helps manufacturers and service providers cater to specific pipeline requirements:
- External Coatings are critical for protecting pipelines from environmental factors like moisture, temperature fluctuations, and soil corrosion. In Russia, external coatings are particularly important for pipelines running through Siberia, where extreme cold and fluctuating temperatures are common.
- Internal Coatings are used to prevent corrosion caused by the flow of crude oil and natural gas. These coatings are essential for pipelines carrying aggressive or high-sulfur crude oil.
This segmentation highlights the need for manufacturers to develop specialized coatings for both internal and external applications, ensuring comprehensive protection.
- By Pipeline Type
The type of pipeline also influences the choice of coatings:
- Transmission Pipelines require durable coatings like fusion-bonded epoxy and polyethylene due to their long-distance nature and exposure to varied environmental conditions.
- Subsea Pipelines demand advanced coatings capable of withstanding saltwater corrosion, high pressure, and mechanical stresses, making ceramic and hybrid coatings ideal for these applications.
This segmentation underscores the importance of advanced coating technologies in ensuring the reliability of Russia’s diverse pipeline infrastructure.
- By End-User
Understanding the end-users of anti-corrosion coatings is essential for targeting specific market segments:
- Pipeline Operators, such as Transneft, are the largest consumers of coatings, focusing on both new construction and maintenance projects.
- Oilfield Service Providers play a critical role in applying and maintaining coatings, driving demand for easy-to-apply and long-lasting products.
This segmentation highlights the need for collaboration between manufacturers, service providers, and pipeline operators to deliver tailored solutions.
Conclusion
The Russia anti-corrosion coatings for oil pipelines market is a dynamic and complex industry characterized by diverse segmentation categories. Among these, segmentation by coating type, region, and application area stands out as the most critical for understanding market dynamics and identifying growth opportunities. By focusing on these key segments, manufacturers and suppliers can align their offerings with the specific needs of the Russian market, ensuring long-term success in this competitive and expanding industry. As the market continues to evolve, driven by technological advancements and infrastructure expansion, businesses that innovate and adapt to the unique challenges of the Russian oil pipeline network will emerge as leaders in this critical sector.
Table of Contents: Anti-Corrosion Coatings for Oil Pipelines Market
- Introduction to Anti-Corrosion Coatings
1.1 Overview and Importance of Anti-Corrosion Coatings for Oil Pipelines
1.2 Scope of the Anti-Corrosion Coatings Market
1.3 Key Applications in the Oil & Gas Industry - Market Segment Analysis
2.1 Market Segmentation by Coating Type (Epoxy Coatings, Polyurethane Coatings, Fusion-Bonded Coatings, etc.)
2.2 Market Segmentation by Application (Onshore Pipelines, Offshore Pipelines)
2.3 Regional Segmentation of the Anti-Corrosion Coatings Market - Revenue Estimates and Forecasts (2019–2030)
3.1 Market Size and Revenue Trends (Historical and Projected)
3.2 Revenue Contribution by Coating Types and Applications - Production Analysis (2019–2030)
4.1 Trends in Anti-Corrosion Coating Production
4.2 Regional Production Insights
4.3 Key Challenges in Coating Production - Market Competition and Key Players
5.1 Overview of Leading Anti-Corrosion Coating Manufacturers
5.2 Market Share of Key Players (2019–2023)
5.3 Competitive Strategies of Major Producers - Manufacturing Insights by Coating Types
6.1 Production Capacity for Key Coating Types
6.2 Domestic vs. International Manufacturers’ Role
6.3 Emerging Players in the Anti-Corrosion Coatings Market - Revenue Market Share by Manufacturers (2019–2023)
7.1 Detailed Revenue Distribution Analysis
7.2 Gross Margins and Pricing Trends - Raw Materials and Production Technology Analysis
8.1 Key Raw Materials Used in Coating Manufacturing
8.2 Advances in Anti-Corrosion Coating Technologies
8.3 Cost Structure of Coating Manufacturing - Export and Import Trends
9.1 Export Volume and Revenue of Anti-Corrosion Coatings (2019–2024)
9.2 Import Dependency and Trends in Coatings
9.3 Trade Balance and Its Impact on Domestic Markets - Consumption Trends by Application
10.1 Consumption in Onshore vs. Offshore Pipelines
10.2 Regional Consumption Insights
10.3 End-Use Industry Demand and Market Share - Production vs. Export Analysis (2019–2024)
11.1 Domestic Production Trends Compared to Export Volumes
11.2 Key Export Destinations for Anti-Corrosion Coatings - Consumption vs. Import Analysis
12.1 Regional Consumption vs. Import Trends
12.2 Impact of Imports on Domestic Pricing - Manufacturing Cost Analysis
13.1 Cost Breakdown of Anti-Corrosion Coating Manufacturing
13.2 Pricing Trends for Key Raw Materials
13.3 Supply Chain and Logistics Analysis - Industrial Chain and Raw Materials Analysis
14.1 Overview of the Anti-Corrosion Coatings Supply Chain
14.2 Key Suppliers of Raw Materials and Additives
14.3 Challenges in Supply Chain Integration - Marketing and Distribution Channels
15.1 Key Distributors of Anti-Corrosion Coatings
15.2 Marketing Strategies for Manufacturers
15.3 Industry Demand and Customer Profiles - Opportunities in the Anti-Corrosion Coatings Market
16.1 Investment Opportunities in Advanced Coating Technologies
16.2 Collaborative Ventures with Global Players
16.3 Growth Potential in Emerging Oil & Gas Regions - Recent Trends in the Anti-Corrosion Coatings Market
17.1 Innovations in Sustainable and Long-Lasting Coatings
17.2 Policy and Regulatory Developments Affecting the Market
17.3 Advancements in Coating Application Technologies - Market Forecast (2024–2030)
18.1 Production Volume and Revenue Forecast
18.2 Consumption Trends and Demand Projections
18.3 Export and Import Forecasts - Conclusion
19.1 Key Takeaways from the Anti-Corrosion Coatings Market Analysis
19.2 Future Outlook and Recommendations for Stakeholders
“Every Organization is different and so are their requirements”- Datavagyanik
Companies We Work With
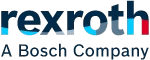
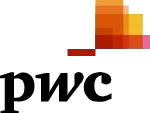
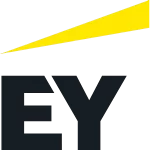
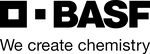
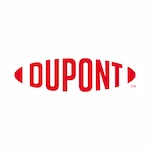

Do You Want To Boost Your Business?
drop us a line and keep in touch
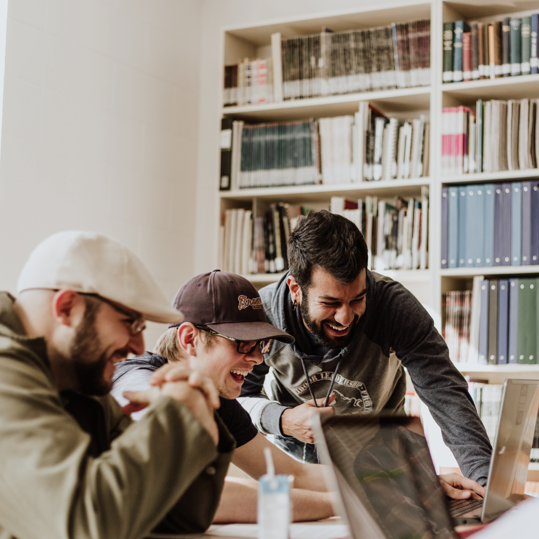