Russia Gas Processing Chemicals Market Revenue, Production, Consumption, Average Price, Import vs Export
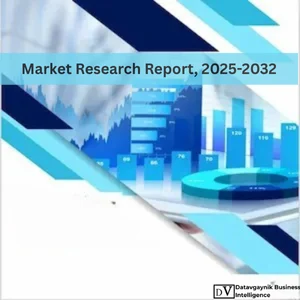
- Published 2025
- No of Pages: 120+
- 20% Customization available
Gas Processing Chemicals Market in Russia: An Overview
Russia, as one of the leading global producers of natural gas, relies heavily on efficient gas processing operations to ensure product quality and meet international market standards. Gas processing chemicals are crucial in separating impurities, conditioning the gas for transport, and maintaining operational efficiency across gas processing plants. These chemicals play a pivotal role in supporting Russia’s energy sector by enhancing the performance and reliability of its extensive gas infrastructure.
As Russia continues to expand its gas production and export capabilities, the demand for advanced gas processing chemicals is expected to grow significantly. This article delves into the structure, market size, opportunities, and trends shaping the Russia gas processing chemicals market.
Market Size and Growth Potential
The Russia gas processing chemicals market has witnessed consistent growth in recent years, driven by the country’s expanding gas production and export network. As of 2023, the market is estimated to be worth approximately $2 billion and is projected to grow at a compound annual growth rate (CAGR) of 5-7% over the next decade. Factors such as the development of new gas fields in Siberia and the Arctic, coupled with rising international demand for liquefied natural gas (LNG), are fueling the growth of this market.
Key contributors to market expansion include:
- Gas Infrastructure Investments: Russia’s ongoing development of gas pipelines, LNG terminals, and processing plants increases the demand for gas processing chemicals.
- International Export Growth: As a major supplier of natural gas to Europe, China, and other global markets, Russia’s focus on meeting stringent quality standards boosts the demand for advanced chemical solutions.
- Environmental Compliance: Stricter environmental regulations are driving the adoption of eco-friendly and biodegradable gas processing chemicals.
Segmentation of the Russia Gas Processing Chemicals Market
The market is segmented across several key criteria, reflecting the diverse applications and requirements of the gas processing industry:
- By Chemical Type:
- Amine-Based Solvents: Used for gas sweetening by removing hydrogen sulfide (H₂S) and carbon dioxide (CO₂).
- Dehydration Chemicals: Includes glycols like monoethylene glycol (MEG) for removing water vapor from gas streams.
- Hydrate Inhibitors: Prevent the formation of gas hydrates in pipelines and processing facilities.
- Corrosion Inhibitors: Protect equipment and pipelines from chemical-induced corrosion.
- Scale Inhibitors: Prevent scaling in gas processing systems caused by mineral deposits.
- Anti-Foaming Agents: Reduce foam formation in processing equipment.
- By Application:
- Gas Sweetening: Removing sour components like H₂S and CO₂ from natural gas.
- Gas Dehydration: Eliminating water vapor to prevent hydrate formation and ensure smooth transportation.
- Flow Assurance: Maintaining the integrity of pipelines and processing systems.
- Processing and Fractionation: Used in separating hydrocarbons into their respective components.
- By Processing Stage:
- Upstream: Chemicals used during extraction and preliminary processing at the wellhead.
- Midstream: Chemicals for pipeline transportation and gas storage.
- Downstream: Chemicals used in refining and LNG production.
- By Region:
- Western Siberia: The largest gas-producing region with significant chemical consumption for sweetening and dehydration.
- Eastern Siberia: Growing demand due to the development of new gas fields.
- Arctic Region: High demand for hydrate inhibitors and corrosion-resistant chemicals due to extreme operating conditions.
- Southern Russia: Focused on gas processing and export facilities.
- By End-User:
- Natural Gas Processing Plants: Primary consumers of gas processing chemicals.
- LNG Facilities: Require advanced chemicals for liquefaction and fractionation.
- Pipeline Operators: Utilize chemicals to ensure flow assurance and prevent pipeline degradation.
Key Drivers and Market Opportunities
The Russia gas processing chemicals market is shaped by several key drivers that present lucrative opportunities for businesses:
- Rising Gas Production and Export Demand: With new gas fields in Siberia and the Arctic coming online, the need for gas processing chemicals is expected to grow substantially.
- Expansion of LNG Infrastructure: Russia’s focus on increasing LNG exports to Asia and Europe is creating a demand for chemicals used in liquefaction and transportation processes.
- Technological Advancements: Innovations in chemical formulations, such as environmentally friendly and highly efficient additives, are driving market growth.
- Environmental Regulations: Compliance with stricter environmental standards is encouraging the adoption of sustainable and biodegradable gas processing chemicals.
- Pipeline Network Expansion: The development of new gas pipelines, such as Power of Siberia 2, boosts demand for chemicals ensuring pipeline integrity and flow assurance.
Opportunities abound for manufacturers and suppliers that invest in research and development to meet these evolving demands and align their offerings with market requirements.
Challenges in the Market
Despite its growth potential, the Russia gas processing chemicals market faces several challenges:
- Geopolitical Pressures: Sanctions and trade restrictions may limit access to advanced chemical technologies and raw materials.
- Economic Uncertainty: Fluctuations in global gas prices can impact investments in gas processing infrastructure and chemical demand.
- Environmental Concerns: The need to balance efficiency with sustainability requires significant investment in research and development.
- Operational Challenges in Harsh Environments: Extreme conditions in regions like the Arctic necessitate the use of specialized chemicals, which can be expensive.
- High Initial Costs: Advanced chemical solutions often involve high upfront costs, which may deter adoption by smaller operators.
Addressing these challenges will require innovation, localization of production, and strong collaboration with key stakeholders in the gas industry.
Regional Insights: Opportunities Across Russia
Russia’s vast geographical expanse and diverse gas production regions create unique opportunities for the gas processing chemicals market:
- Western Siberia: As the largest gas-producing region, Western Siberia drives the majority of demand for gas sweetening and dehydration chemicals. The aging infrastructure in this region also creates opportunities for corrosion inhibitors and scale preventatives.
- Eastern Siberia: The development of untapped gas reserves in this region is fueling the demand for advanced chemical solutions tailored to challenging geologies.
- Arctic Region: Harsh environmental conditions and extreme cold make hydrate inhibitors and corrosion-resistant chemicals critical for Arctic gas operations.
- Southern Russia: Proximity to export terminals and pipeline networks in this region ensures steady demand for chemicals used in processing and transportation.
Understanding these regional dynamics allows manufacturers and suppliers to tailor their offerings and strengthen their presence in the market.
Forecast and Business Strategies
The Russia gas processing chemicals market is poised for steady growth, presenting significant opportunities for manufacturers, suppliers, and service providers. Key strategies for success include:
- Investing in Innovation: Developing advanced formulations, such as biodegradable and multi-functional chemicals, to meet evolving market needs.
- Localizing Production: Establishing manufacturing facilities in Russia to reduce dependency on imports and align with government policies promoting self-sufficiency.
- Collaborating with Key Stakeholders: Partnering with gas producers, pipeline operators, and processing plants to deliver customized solutions.
- Focusing on Sustainability: Launching eco-friendly products that comply with environmental regulations and appeal to environmentally conscious buyers.
- Targeting Emerging Regions: Expanding into high-growth regions like Eastern Siberia and the Arctic to capture new opportunities.
By implementing these strategies, businesses can capitalize on the market’s growth potential and establish themselves as key players in this critical segment.
Comprehensive Market Segmentation in Russia’s Gas Processing Chemicals Market
The gas processing chemicals market in Russia is multi-faceted, reflecting the complexity and scale of the nation’s gas industry. Market segmentation allows businesses to identify key areas of demand, align their products with specific needs, and optimize their strategies for success in this competitive landscape. Below is an exhaustive list of all possible segmentation categories, followed by an in-depth discussion of the most important ones, focusing on their relevance to Russia’s market.
All Possible Market Segmentation
- By Chemical Type
- Amine-Based Solvents: For gas sweetening (removal of hydrogen sulfide (H₂S) and carbon dioxide (CO₂)).
- Dehydration Chemicals: Includes glycols like monoethylene glycol (MEG) and triethylene glycol (TEG) to remove water vapor.
- Hydrate Inhibitors: Prevent the formation of gas hydrates in pipelines.
- Corrosion Inhibitors: Protect pipelines, processing equipment, and storage tanks.
- Scale Inhibitors: Mitigate mineral scaling in gas processing equipment.
- Anti-Foaming Agents: Minimize foam formation during gas processing.
- Biocides: Control microbial growth in processing systems.
- Specialty Chemicals: Tailored solutions for unique challenges, such as gas separation additives.
- By Application
- Gas Sweetening: Removing acidic impurities like H₂S and CO₂ from natural gas to meet market and safety standards.
- Gas Dehydration: Removing water vapor to prevent the formation of hydrates and ensure smooth transportation.
- Flow Assurance: Maintaining pipeline integrity and flow efficiency by preventing blockages.
- Fractionation: Separation of hydrocarbons into their respective components (e.g., methane, propane, butane).
- By Processing Stage
- Upstream: Chemicals used at the wellhead for preliminary gas processing.
- Midstream: Chemicals for pipelines, storage facilities, and gas compression systems.
- Downstream: Chemicals used in gas refining, LNG production, and export facilities.
- By Gas Type
- Natural Gas: The primary focus of Russia’s gas processing industry.
- Shale Gas: Emerging as an important segment with specialized chemical requirements.
- Coalbed Methane (CBM): A niche segment requiring unique processing solutions.
- Associated Gas: Extracted alongside oil and requiring additional processing.
- By Base Material
- Organic Chemicals: Such as amines, glycols, and alcohols.
- Inorganic Chemicals: Such as zinc oxide for gas sweetening or caustic soda for pH control.
- Hybrid Chemicals: Combining properties of organic and inorganic materials for enhanced performance.
- By Region
- Western Siberia: The largest gas-producing region with mature infrastructure.
- Eastern Siberia: A rapidly growing region with untapped gas fields.
- Arctic Region: Demands advanced chemicals due to extreme weather and operational challenges.
- Southern Russia: Focuses on processing and export infrastructure near the Black Sea.
- Far East: Growing demand driven by gas exports to Asia.
- By End-User
- Natural Gas Processing Facilities: The largest consumers of gas processing chemicals.
- LNG Facilities: Require chemicals for liquefaction and storage.
- Pipeline Operators: Use chemicals to ensure flow efficiency and pipeline integrity.
- Oil and Gas Companies: Integrated players managing upstream, midstream, and downstream activities.
- By Functionality
- Sweetening: Removal of sour gases to meet quality standards.
- Dehydration: Preventing the formation of hydrates and corrosion.
- Corrosion Protection: Extending the life of pipelines and equipment.
- Flow Enhancement: Ensuring smooth gas transport.
- Separation: Isolating valuable hydrocarbons for downstream processing.
- By Formulation
- Liquid Chemicals: Easy to transport and apply, commonly used in Russia’s gas industry.
- Solid Chemicals: Preferred for remote locations due to longer shelf life.
- Blended Solutions: Customized formulations tailored to specific operational requirements.
Most Important Market Segmentation with Explanation
- By Chemical Type
The segmentation by chemical type is critical as it addresses the specific needs of Russia’s gas processing operations:
- Amine-Based Solvents: These are essential for gas sweetening in Russia, where natural gas often contains high levels of H₂S and CO₂. This is particularly important for gas fields in Western and Eastern Siberia.
- Dehydration Chemicals: With Russia’s extensive pipeline network and cold climates, removing water vapor to prevent hydrate formation is a key priority. Glycols like MEG are widely used in Arctic operations.
- Hydrate Inhibitors: These are crucial for preventing blockages in pipelines, especially in the Arctic, where extreme cold accelerates hydrate formation.
- Corrosion Inhibitors: Aging infrastructure in Western Siberia requires advanced corrosion inhibitors to maintain operational efficiency.
- Specialty Chemicals: Emerging fields in Eastern Siberia and the Arctic create demand for innovative chemical solutions tailored to complex geologies and operational challenges.
This segmentation highlights the opportunities for manufacturers to develop targeted products that meet the diverse needs of the Russian gas industry.
- By Application
Application-based segmentation is significant as it aligns with the key stages of gas processing in Russia:
- Gas Sweetening: Russia’s natural gas often contains high levels of sour gases, necessitating the extensive use of amine-based solvents and specialty additives.
- Gas Dehydration: Dehydration chemicals are critical for pipelines transporting gas over long distances, particularly in cold climates where hydrate formation is a major concern.
- Flow Assurance: Chemicals that prevent blockages and scaling are essential for ensuring uninterrupted gas transportation in Russia’s vast pipeline network.
This segmentation underscores the importance of aligning chemical solutions with specific operational challenges in gas processing.
- By Region
Geographical segmentation is crucial in understanding regional variations in demand:
- Western Siberia: As Russia’s largest gas-producing region, Western Siberia drives significant demand for gas sweetening and dehydration chemicals.
- Eastern Siberia: The development of new gas fields creates opportunities for advanced chemical solutions tailored to untapped reserves.
- Arctic Region: Extreme conditions in the Arctic necessitate the use of high-performance chemicals, such as hydrate inhibitors and corrosion-resistant additives.
- Southern Russia: The proximity to export terminals and pipeline networks ensures steady demand for chemicals used in processing and transportation.
This segmentation helps manufacturers and suppliers identify regional priorities and develop region-specific strategies.
- By Processing Stage
The segmentation by processing stage provides insights into where chemicals are most heavily utilized:
- Upstream: Chemicals used at the wellhead, such as biocides and scale inhibitors, are essential for maintaining production efficiency.
- Midstream: Pipeline operators in Russia require a variety of chemicals, including corrosion inhibitors and hydrate inhibitors, to ensure smooth gas transportation.
- Downstream: LNG facilities and gas refineries consume significant quantities of specialty chemicals for fractionation and liquefaction processes.
This segmentation highlights the diverse application areas within the gas processing value chain.
- By End-User
End-user segmentation identifies the key stakeholders driving demand for gas processing chemicals:
- Natural Gas Processing Facilities: These are the largest consumers, requiring a wide range of chemicals for sweetening, dehydration, and flow assurance.
- LNG Facilities: As Russia expands its LNG capacity, the demand for advanced chemicals tailored to liquefaction and storage is expected to grow.
- Pipeline Operators: These players rely on chemicals to maintain pipeline integrity and ensure efficient gas transport.
This segmentation provides a clear picture of the primary consumers of gas processing chemicals in Russia.
Conclusion
The Russia gas processing chemicals market is a critical segment of the country’s energy industry, with diverse segmentation categories that reflect the complexity and scale of gas production and processing operations. Among these, segmentation by chemical type, application, and region stands out as the most important for understanding market dynamics and identifying growth opportunities. By focusing on these key segments, manufacturers and suppliers can align their products and strategies with the unique needs of the Russian market, ensuring success in this expanding and competitive industry. As Russia continues to invest in its gas infrastructure and expand its export capacity, the demand for gas processing chemicals is expected to grow, creating significant opportunities for innovation and growth.
Table of Contents: Gas Processing Chemicals Market
- Introduction to Gas Processing Chemicals
1.1 Overview and Importance of Gas Processing Chemicals
1.2 Scope of the Gas Processing Chemicals Market
1.3 Key Applications in the Natural Gas Industry - Market Segment Analysis
2.1 Market Segmentation by Chemical Type (Amine Solutions, Dehydration Chemicals, Corrosion Inhibitors, etc.)
2.2 Market Segmentation by Application (Acid Gas Removal, Dehydration, Hydrocarbon Recovery, etc.)
2.3 Regional Segmentation of the Gas Processing Chemicals Market - Revenue Estimates and Forecasts (2019–2030)
3.1 Market Size and Revenue Trends (Historical and Projected)
3.2 Revenue Contribution by Chemical Types and Applications - Production Analysis (2019–2030)
4.1 Trends in Gas Processing Chemicals Production
4.2 Regional Production Insights
4.3 Challenges in Chemical Production - Market Competition and Key Players
5.1 Overview of Leading Gas Processing Chemical Manufacturers
5.2 Market Share of Key Players (2019–2023)
5.3 Competitive Strategies of Major Producers - Manufacturing Insights by Chemical Types
6.1 Production Capacity for Key Gas Processing Chemicals
6.2 Domestic vs. International Manufacturers’ Role
6.3 Emerging Players in the Gas Processing Chemicals Market - Revenue Market Share by Manufacturers (2019–2023)
7.1 Detailed Revenue Distribution Analysis
7.2 Gross Margins and Pricing Strategies - Feedstock and Production Technology Analysis
8.1 Key Raw Materials Used in Gas Processing Chemicals Manufacturing
8.2 Advances in Chemical Production Technologies
8.3 Cost Structure of Manufacturing - Export and Import Trends
9.1 Export Volume and Revenue of Gas Processing Chemicals (2019–2024)
9.2 Import Dependency and Trends in the Market
9.3 Trade Balance and Its Impact on Domestic Markets - Consumption Trends by Application
10.1 Consumption in Acid Gas Removal, Dehydration, and Other Applications
10.2 Regional Consumption Insights
10.3 End-Use Industry Demand and Market Share - Production vs. Export Analysis (2019–2024)
11.1 Domestic Production Trends Compared to Export Volumes
11.2 Key Export Destinations for Gas Processing Chemicals - Consumption vs. Import Analysis
12.1 Regional Consumption vs. Import Trends
12.2 Impact of Imports on Domestic Pricing - Manufacturing Cost Analysis
13.1 Cost Breakdown of Gas Processing Chemicals Manufacturing
13.2 Pricing Trends for Key Raw Materials and Feedstock
13.3 Supply Chain and Logistics Analysis - Industrial Chain and Raw Materials Analysis
14.1 Overview of the Gas Processing Chemicals Supply Chain
14.2 Key Suppliers of Raw Materials and Additives
14.3 Challenges in Supply Chain Integration - Marketing and Distribution Channels
15.1 Key Distributors of Gas Processing Chemicals
15.2 Marketing Strategies for Manufacturers
15.3 Industry Demand and Customer Profiles - Opportunities in the Gas Processing Chemicals Market
16.1 Investment Opportunities in Advanced Chemical Technologies
16.2 Collaborative Ventures with Global Players
16.3 Growth Potential in Emerging Natural Gas Markets - Recent Trends in the Gas Processing Chemicals Market
17.1 Innovations in Sustainable and Eco-Friendly Chemicals
17.2 Policy and Regulatory Developments Affecting the Market
17.3 Advancements in High-Performance Chemical Technologies - Market Forecast (2024–2030)
18.1 Production Volume and Revenue Forecast
18.2 Consumption Trends and Demand Projections
18.3 Export and Import Forecasts - Conclusion
19.1 Key Takeaways from the Gas Processing Chemicals Market Analysis
19.2 Future Outlook and Recommendations for Stakeholders
“Every Organization is different and so are their requirements”- Datavagyanik
Companies We Work With
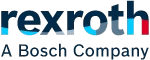
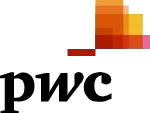
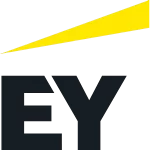
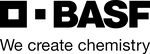
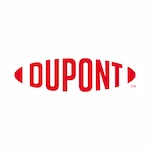

Do You Want To Boost Your Business?
drop us a line and keep in touch
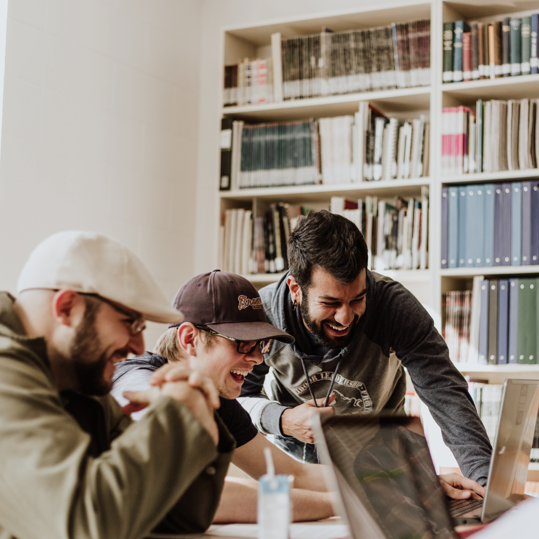