Sulfur-resistant catalyst Market Size, Production, Sales, Average Product Price, Market Share, Import vs Export
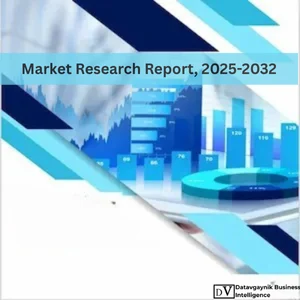
- Published 2025
- No of Pages: 120+
- 20% Customization available
Sulfur-resistant catalyst Market Trends Shaping Industrial Sustainability
The sulfur-resistant catalyst market is rapidly evolving, driven by the increasing necessity to reduce sulfur emissions in industrial processes. For example, refineries globally are processing a growing volume of sour crude oil, which contains sulfur levels exceeding 3%, creating a pressing demand for catalysts that maintain performance without degradation. This market trend is underscored by the global refining capacity expanding at over 2% annually, particularly in Asia Pacific and the Middle East, regions where sour crude utilization is highest. As a result, the sulfur-resistant catalyst market is experiencing robust growth, supported by its critical role in hydrodesulfurization units that enable compliance with stringent sulfur emission standards.
Environmental Regulations Propel Sulfur-resistant catalyst Market Expansion
One of the foremost drivers of the sulfur-resistant catalyst market is the intensifying global regulatory framework targeting sulfur oxide emissions. For instance, the International Maritime Organization’s sulfur cap on marine fuels, implemented in 2020, restricts sulfur content to 0.5%, sharply down from 3.5%. This regulation alone has escalated demand for sulfur-resistant catalysts in refinery hydroprocessing to produce compliant low-sulfur fuels. Similarly, countries across North America and Europe have adopted strict fuel sulfur limits for transportation and industrial applications, mandating catalyst upgrades. These regulations translate into a market growth rate exceeding 6% annually, with refineries investing billions in catalyst technologies that resist sulfur poisoning and extend operational lifetimes.
Increasing Sour Crude Processing Drives Sulfur-resistant catalyst Market Demand
The diversification of crude oil sources has led to an upsurge in sour crude processing, a key factor fueling the sulfur-resistant catalyst market. Sour crude, characterized by sulfur content greater than 1%, constitutes nearly 40% of the global crude mix, with countries like Venezuela, Russia, and the Middle East supplying high volumes. Refineries are increasingly tasked with upgrading or constructing new hydrodesulfurization units to handle these feedstocks effectively.
For example, many refineries in Asia Pacific have expanded capacity by over 5% annually in recent years, directly impacting the sulfur-resistant catalyst market by increasing consumption of catalysts capable of sustaining activity under harsh sulfur-rich conditions. This trend also contributes to cost efficiency by allowing more flexible crude sourcing without sacrificing product quality.
Technological Advancements Fuel Growth in Sulfur-resistant catalyst Market
Innovations in catalyst design are pivotal to the sulfur-resistant catalyst market’s upward trajectory. New-generation catalysts incorporate advanced materials such as nanostructured metals and coated supports, significantly enhancing sulfur tolerance and catalytic activity. For example, the introduction of nickel-molybdenum formulations with optimized pore structures has improved hydrodesulfurization efficiency by up to 15%, reducing catalyst replacement frequency and lowering operational downtime. These technological strides expand the application scope of sulfur-resistant catalysts beyond traditional oil refining into chemical manufacturing, natural gas processing, and emerging renewable energy sectors. Such advancements drive market differentiation and offer competitive advantages, helping manufacturers capture larger shares amid growing demand.
Expansion of Petrochemical and Refining Sectors Boosts Sulfur-resistant catalyst Market Size
The continuous expansion of petrochemical complexes and refineries worldwide directly influences the sulfur-resistant catalyst market size. For instance, emerging economies in Asia, such as India and China, are aggressively increasing refining throughput by over 4% annually to meet rising domestic energy demands. This expansion necessitates robust catalyst systems capable of operating efficiently in sulfur-rich environments. Sulfur-resistant catalysts are critical for processes like hydrodesulfurization and sulfur recovery units that reduce emissions while maintaining throughput. The growing petrochemical sector, producing products like methanol, ammonia, and olefins, also relies heavily on sulfur-resistant catalysts to prevent sulfur poisoning in complex reactions, thus further amplifying market growth opportunities.
Energy Efficiency Initiatives Enhance Demand in Sulfur-resistant catalyst Market
Industrial focus on energy efficiency and cost optimization is intensifying demand for sulfur-resistant catalysts designed to maximize catalyst life and reduce downtime. For example, catalysts with improved sulfur resistance maintain higher activity over longer periods, minimizing frequent shutdowns for replacement and lowering operational expenses. Such efficiencies are particularly critical in large-scale refineries where unscheduled downtime can cost millions daily. Moreover, sulfur-resistant catalysts contribute to improved fuel quality and cleaner emissions, aligning with broader energy transition goals. This market trend reflects a shift towards sustainable industrial practices, with sulfur-resistant catalyst manufacturers investing heavily in R&D to develop products that combine durability with superior performance under harsh processing conditions.
Regional Growth Patterns Highlight Opportunities in Sulfur-resistant catalyst Market
Geographical dynamics play a crucial role in shaping the sulfur-resistant catalyst market. For example, Asia Pacific, led by China and India, is the fastest-growing region due to rapid industrialization, expanding refining capacities, and stringent pollution control norms. Here, sulfur-resistant catalyst consumption is growing at over 8% annually, supported by government mandates to reduce sulfur in fuels and air pollutants. In contrast, North America and Europe focus on upgrading existing refinery infrastructure and adopting advanced catalysts to meet evolving emission standards, sustaining steady market growth. Additionally, Middle Eastern countries, rich in sour crude reserves, are investing in local catalyst production capabilities, further driving the market’s expansion globally.
Increasing Adoption in Renewable Energy and Chemical Processing Expands Sulfur-resistant catalyst Market
Beyond oil refining, the sulfur-resistant catalyst market is expanding into renewable energy and chemical processing sectors. For example, biofuel production processes involving biomass feedstocks often contain sulfur impurities, necessitating catalysts that withstand sulfur-induced deactivation. Similarly, sulfur-resistant catalysts are increasingly applied in hydrogen production and purification systems where sulfur compounds can severely impair catalyst performance. This diversification into clean energy aligns with global decarbonization trends, opening new avenues for market growth. The integration of sulfur-resistant catalysts in chemical industries producing fertilizers, plastics, and pharmaceuticals also exemplifies the market’s broadening application base, supporting consistent demand growth.
Cost-effectiveness and Catalyst Longevity Drive Sulfur-resistant catalyst Market Preference
Cost optimization is a significant factor driving industrial preference for sulfur-resistant catalysts. Catalysts that offer extended operational life reduce the frequency of replacements and associated downtime costs. For instance, enhanced sulfur-resistant formulations can last up to 30% longer than conventional catalysts under equivalent operating conditions, representing substantial savings for large-scale refineries and chemical plants. The economic advantage, combined with compliance to environmental norms, makes sulfur-resistant catalysts indispensable for industries seeking sustainable and profitable operations. This market dynamic is encouraging manufacturers to innovate further, delivering tailored catalyst solutions that meet specific process requirements and sulfur content challenges.
Rising Global Focus on Emission Control Boosts Sulfur-resistant catalyst Market Demand
The global commitment to reducing sulfur oxide emissions is a powerful catalyst for the sulfur-resistant catalyst market. For example, coal-fired power plants and industrial boilers worldwide are incorporating sulfur-resistant catalysts in flue gas desulfurization units to meet tightening air quality standards. This has increased demand for catalysts that maintain performance in high-sulfur environments while effectively converting sulfur compounds into less harmful forms. Urban air pollution concerns and international agreements aimed at lowering acid rain-causing emissions ensure that sulfur-resistant catalysts remain essential across multiple industries, reinforcing the market’s long-term growth potential.
“Track Country-wise Sulfur-resistant catalyst Production and Demand through our Sulfur-resistant catalyst Production Database”
-
-
- Sulfur-resistant catalyst production database for 32+ countries worldwide
- Sulfur-resistant catalyst sales volume for 32+ countries
- Country-wise Sulfur-resistant catalyst production capacity, production plant mapping, production capacity utilization for 32+ manufacturers
- Sulfur-resistant catalyst production plants and production plant capacity analysis by top manufacturers
-
“Track real-time Sulfur-resistant catalyst Prices, Sulfur-resistant catalyst price charts for 32+ countries, Sulfur-resistant catalyst weekly price tracker and Sulfur-resistant catalyst monthly price tracker”
-
-
- Track real-time Sulfur-resistant catalyst prices and Sulfur-resistant catalyst price trend in 32+ countries though our excel-based Sulfur-resistant catalyst price charts
- Real-time Sulfur-resistant catalyst price tracker dashboard with 32+ countries
- Complete transparency on Sulfur-resistant catalyst price trend through our Sulfur-resistant catalyst monthly price tracker, Sulfur-resistant catalyst weekly price tracker
-
Geographical Demand Trends in the Sulfur-resistant catalyst Market
The sulfur-resistant catalyst market displays clear geographical demand patterns shaped by regional industrial priorities and regulatory frameworks. Asia Pacific leads the global demand, accounting for nearly half of total consumption, driven by rapid industrialization and expanding refining capacity. For example, China’s refining throughput has grown steadily by over 7% annually, with a significant portion dedicated to processing high-sulfur crude oils, thus intensifying the need for sulfur-resistant catalysts. Similarly, India’s refining upgrades aligned with stringent emission standards, such as Bharat Stage VI, have accelerated the installation of sulfur-resistant catalysts to meet sulfur content reduction goals. This regional focus on environmental compliance and fuel quality improvement fuels sulfur-resistant catalyst market expansion at rates exceeding 8% annually in Asia Pacific.
Meanwhile, North America sustains robust demand influenced by the rise of shale oil production and continuous refinery modernization. The United States processes sour crude oils with sulfur contents often surpassing 2%, which necessitates the widespread adoption of advanced sulfur-resistant catalysts in hydrodesulfurization units to maintain efficiency and meet regulatory emission targets. Recent refinery upgrades across the U.S. have contributed to sulfur-resistant catalyst market growth averaging around 5% annually. Canada’s petrochemical and natural gas sectors also bolster regional demand, with sulfur-resistant catalysts playing a critical role in emissions control and gas purification.
Europe presents a mature market for sulfur-resistant catalysts, shaped by stringent environmental regulations and a commitment to sustainable energy transition. Countries such as Germany, France, and the Netherlands continue investing in catalyst technologies to comply with tight sulfur emission limits in transportation fuels and industrial processes. Although refinery expansions are modest, replacement and upgrade cycles maintain steady sulfur-resistant catalyst demand, growing at roughly 3-4% annually. The European Union’s Green Deal and focus on renewable fuels drive gradual adoption of sulfur-resistant catalysts in biofuel processing and chemical manufacturing.
The Middle East’s sulfur-resistant catalyst market is expanding in tandem with its large-scale refinery and petrochemical capacity growth. Nations like Saudi Arabia and the UAE process substantial volumes of sour crude oil, requiring highly durable catalysts capable of withstanding extreme sulfur conditions. Investments in refinery capacity expansions and sulfur recovery units have elevated sulfur-resistant catalyst consumption at rates near 6% per year. Furthermore, ongoing efforts to localize catalyst manufacturing in the region aim to reduce import dependency and optimize supply chains.
In Latin America, the sulfur-resistant catalyst market is growing steadily, driven primarily by refinery modernization and increased crude processing complexity. Countries such as Brazil and Mexico face the challenge of upgrading facilities to handle heavier, sulfur-rich feedstocks while meeting evolving environmental regulations. These factors collectively stimulate sulfur-resistant catalyst market growth around 4-5% annually, with increasing investments in both production and import of advanced catalyst solutions.
Production Landscape of the Sulfur-resistant catalyst Market
The sulfur-resistant catalyst market’s production landscape is dominated by technologically advanced regions equipped with strong research and manufacturing capabilities. North America hosts some of the leading catalyst manufacturers, leveraging advanced process technologies and extensive R&D to produce catalysts with superior sulfur tolerance. The U.S. remains a global hub for catalyst innovation, with manufacturers continuously enhancing formulations to improve catalyst life and activity under harsh sulfur exposure.
Europe also represents a key production zone, with countries like Germany and France spearheading sustainable catalyst technologies. European manufacturers emphasize environmental compliance and catalyst regeneration techniques, focusing on reducing waste and extending catalyst usability. This region’s production capacities support both domestic demand and significant export volumes to other global markets, reinforcing the sulfur-resistant catalyst market’s international supply chain.
Asia Pacific, especially China and India, has rapidly scaled sulfur-resistant catalyst production to meet soaring regional demand. Chinese manufacturers have invested heavily in expanding production infrastructure and developing cost-effective catalyst formulations that balance performance with affordability. India’s growing production base focuses on serving both the domestic market and neighboring countries, capitalizing on competitive manufacturing costs. Japan and South Korea contribute specialized catalysts with advanced materials science applications, targeting high-performance niches within the sulfur-resistant catalyst market.
The Middle East is increasingly developing local catalyst manufacturing to support its expanding refining and petrochemical sectors. By fostering public-private partnerships and technology transfers, the region aims to build self-sufficiency in producing sulfur-resistant catalysts, which is critical for reducing import reliance and enhancing supply chain resilience.
Market Segmentation in the Sulfur-resistant catalyst Market
The sulfur-resistant catalyst market is segmented primarily by product type, application, material composition, and end-user industry, each influencing market dynamics differently.
By product type, hydrodesulfurization (HDS) catalysts dominate the market, constituting over 50% of total demand. HDS catalysts are essential in refining processes to remove sulfur from gasoline, diesel, and jet fuel, directly driven by tightening fuel sulfur limits worldwide. Hydrogenation catalysts represent another significant segment, particularly important in chemical manufacturing where sulfur tolerance preserves catalyst activity. Sulfur recovery unit (SRU) catalysts, used in Claus processes for sulfur extraction from hydrogen sulfide gas, are critical in refining and gas processing plants, supporting environmental emission controls.
In terms of application, the oil and gas industry remains the largest consumer of sulfur-resistant catalysts, driven by the necessity to process sour crude oils and produce cleaner fuels. The chemical and petrochemical sector follows, relying on sulfur-resistant catalysts in processes such as ammonia synthesis and methanol production, where sulfur compounds can deactivate conventional catalysts. Other applications include power generation, where sulfur-resistant catalysts contribute to flue gas desulfurization, and automotive sectors utilizing sulfur-tolerant catalytic converters for emission control.
Material composition influences catalyst performance and market segmentation significantly. Nickel-based catalysts are prevalent due to their high sulfur tolerance, commonly applied in hydrogenation and hydrodesulfurization. Cobalt-based catalysts offer excellent resistance at high temperatures, favored in Fischer-Tropsch synthesis and syngas processing. Molybdenum-based catalysts, often combined with nickel or cobalt, provide superior stability under sulfur-rich conditions. Precious metal catalysts, including those based on platinum and palladium, serve niche high-value applications requiring both sulfur resistance and catalytic efficiency.
End-user segmentation reveals refineries as the dominant market segment, leveraging sulfur-resistant catalysts extensively to meet fuel quality and environmental regulations. Petrochemical industries follow closely, utilizing catalysts in cracking, reforming, and synthesis operations. Natural gas processing plants depend on sulfur-resistant catalysts for hydrogen sulfide removal and gas sweetening, while industrial manufacturing sectors, such as fertilizer and metal processing, also contribute notably to market demand.
Sulfur-resistant catalyst Price Trends Influencing Market Dynamics
Sulfur-resistant catalyst price trends are shaped by raw material costs, technological advancements, and regional supply-demand balances. Prices for sulfur-resistant catalysts have experienced moderate upward pressure due to increased demand for high-performance formulations capable of withstanding elevated sulfur concentrations and operating temperatures. For example, catalysts incorporating advanced nanomaterials or precious metals command premium pricing due to their enhanced durability and efficiency.
Raw material volatility, particularly in metals such as nickel, cobalt, and molybdenum, impacts sulfur-resistant catalyst price trends. Fluctuations in these commodity prices can lead to periodic price adjustments in catalyst manufacturing. Additionally, supply chain disruptions, including logistic challenges and geopolitical factors, have occasionally caused short-term sulfur-resistant catalyst price spikes.
Technological progress in catalyst regeneration and recycling has begun to moderate sulfur-resistant catalyst prices by extending catalyst lifespan and reducing the need for frequent replacements. For instance, regenerated catalysts retain over 85% of their original activity, providing cost-effective alternatives that influence overall market pricing.
Regional price variations exist, with sulfur-resistant catalyst prices generally higher in mature markets such as North America and Europe, reflecting stringent quality and environmental compliance requirements. In contrast, Asia Pacific manufacturers offer competitively priced catalysts, balancing performance and affordability, which attracts expanding industrial demand in developing economies.
Economic Factors and Sulfur-resistant catalyst Price Trends
Global economic trends, including fluctuations in crude oil prices and industrial production cycles, directly affect sulfur-resistant catalyst price trends. For example, rising crude prices often incentivize refineries to process heavier, sulfur-rich feedstocks, increasing demand for sulfur-resistant catalysts and supporting price stability or growth. Conversely, periods of low crude prices can constrain refinery capital expenditure, temporarily slowing sulfur-resistant catalyst procurement.
Government incentives promoting cleaner fuels and environmental protection also influence pricing dynamics. Subsidies or tax benefits for upgrading refineries and adopting advanced catalysts can increase market uptake, indirectly impacting sulfur-resistant catalyst prices through demand growth.
Furthermore, increasing competition among catalyst manufacturers, coupled with innovation-driven differentiation, exerts downward pressure on sulfur-resistant catalyst prices, encouraging efficiency improvements and cost reduction strategies.
“Sulfur-resistant catalyst Manufacturing Database, Sulfur-resistant catalyst Manufacturing Capacity”
-
-
- Sulfur-resistant catalyst top manufacturers market share for 32+ manufacturers
- Top 12 manufacturers and top 19 manufacturers of Sulfur-resistant catalyst in North America, Europe, Asia Pacific
- Sulfur-resistant catalyst production plant capacity by manufacturers and Sulfur-resistant catalyst production data for 32+ market players
- Sulfur-resistant catalyst production dashboard, Sulfur-resistant catalyst production data in excel format
-
“Sulfur-resistant catalyst price charts, Sulfur-resistant catalyst weekly price tracker and Sulfur-resistant catalyst monthly price tracker”
-
-
- Factors impacting real-time Sulfur-resistant catalyst prices in 32+ countries worldwide
- Sulfur-resistant catalyst monthly price tracker, Sulfur-resistant catalyst weekly price tracker
- Real-time Sulfur-resistant catalyst price trend, Sulfur-resistant catalyst price charts, news and updates
- Tracking Sulfur-resistant catalyst price fluctuations
-
Leading Manufacturers Shaping the Sulfur-resistant catalyst Market
The sulfur-resistant catalyst market is characterized by a competitive landscape dominated by several key manufacturers who have established global footprints through innovation, technology leadership, and extensive product portfolios. These players leverage advanced research and strategic partnerships to address the rising demand for sulfur-resistant catalysts across refining, petrochemical, and chemical industries.
Among the top manufacturers, Albemarle Corporation holds a significant share of the sulfur-resistant catalyst market. Albemarle’s robust portfolio includes advanced hydrodesulfurization catalysts designed for high sulfur feedstocks, such as their flagship HDS Select series. These catalysts emphasize enhanced sulfur tolerance and prolonged operational life, catering to refineries upgrading to meet ultra-low sulfur fuel regulations. Albemarle’s market share is bolstered by their global production capacity and continuous innovation in catalyst formulations that improve sulfur resistance while optimizing process efficiency.
Johnson Matthey is another dominant player, commanding a substantial portion of the sulfur-resistant catalyst market. The company’s offerings include the Puricor line of catalysts, known for their durability and superior resistance to sulfur poisoning in harsh refinery conditions. Johnson Matthey focuses heavily on integrating nanotechnology and material science breakthroughs to extend catalyst longevity and reduce operational downtime. Their global reach and extensive service network support strong adoption across North America, Europe, and Asia Pacific.
R. Grace & Co. is a major contributor to the sulfur-resistant catalyst market, particularly recognized for its AGR (Advanced Gasification Reforming) catalysts. Grace’s products target both hydrodesulfurization and sulfur recovery applications, designed to maintain activity despite high sulfur concentrations and elevated temperatures. The company’s investment in catalyst regeneration technology and tailored solutions for varying feedstock types strengthens its competitive position and market share.
Honeywell UOP plays a pivotal role in the sulfur-resistant catalyst market through its C-11 and C-21 catalyst lines, which are widely employed in hydroprocessing units. These catalysts are engineered to deliver high sulfur resistance with improved hydrogenation activity, crucial for modern refinery operations. Honeywell’s global presence and collaboration with key refining clients enhance its market penetration and share.
BASF SE is a significant player in the sulfur-resistant catalyst market, offering a comprehensive range of catalysts including their Sulfona series tailored for desulfurization applications. BASF emphasizes sustainable catalyst technologies designed to reduce environmental impact while maintaining robust sulfur tolerance. Their strategic focus on expanding production in Asia and Europe has enabled them to capture growing market segments effectively.
Clariant AG, known for its innovative catalyst development, holds a notable market share with products such as the NTOX and HYDROCAT series designed for enhanced sulfur resistance and improved reaction kinetics. Clariant’s focus on catalytic solutions that extend cycle life and reduce emissions supports strong demand, especially from petrochemical industries seeking to optimize sulfur management.
LyondellBasell Industries, although more diversified, also participates in the sulfur-resistant catalyst market through specialty catalyst formulations used in hydrodesulfurization and hydrogenation processes. Their product offerings emphasize cost-effectiveness combined with sulfur tolerance, targeting emerging markets where affordability is critical.
Sulfur-resistant catalyst Market Share by Manufacturer
The sulfur-resistant catalyst market is relatively consolidated, with the top five manufacturers collectively accounting for more than 70% of the global market share. Albemarle Corporation and Johnson Matthey dominate, each controlling roughly 20-25% of the market, supported by their extensive product lines and global distribution networks. W. R. Grace & Co. holds about 15-18%, while Honeywell UOP and BASF SE command between 10-15% each. Clariant AG and other regional players fill the remaining share, collectively constituting around 10-15%.
The competitive dynamics within the sulfur-resistant catalyst market reflect an emphasis on technological superiority, product customization, and service quality. Manufacturers with strong R&D capabilities consistently outperform peers by launching catalysts that offer higher sulfur resistance, longer lifespan, and compatibility with diverse feedstocks.
Product Lines and Innovation Focus of Key Manufacturers
Albemarle’s HDS Select series exemplifies innovation with catalysts formulated to resist sulfur poisoning and extend service intervals. Their focus on tailoring catalyst properties to various crude qualities allows refineries to optimize hydrodesulfurization without frequent shutdowns.
Johnson Matthey’s Puricor catalysts leverage advanced nanostructured materials to deliver enhanced surface area and active site distribution, translating to superior sulfur resistance and catalytic efficiency. The company continually refines these products to meet evolving emission standards globally.
R. Grace’s AGR catalysts are engineered to tolerate sulfur compounds in gasification and refining environments, maintaining hydrogenation activity over extended periods. Their emphasis on catalyst regeneration technologies reduces waste and operational costs.
Honeywell UOP’s C-11 and C-21 lines integrate proprietary support materials and active metals, balancing hydrogenation performance with sulfur resistance, essential for producing cleaner fuels with reduced sulfur content.
BASF’s Sulfona catalysts target not only sulfur resistance but also sustainability, incorporating materials that lower greenhouse gas emissions during production and use. Their portfolio is expanding into bio-based feedstock applications, reflecting market diversification.
Clariant’s NTOX and HYDROCAT catalysts prioritize longevity and adaptability, designed for various sulfur concentrations and process conditions, supporting petrochemical and refinery clients in maximizing operational uptime.
Recent Industry Developments and Market Player Activities
The sulfur-resistant catalyst market has witnessed significant strategic movements in recent months, underscoring the sector’s vitality and innovation drive.
In early 2025, Albemarle announced the commercial launch of an upgraded hydrodesulfurization catalyst tailored for ultra-high sulfur crude processing, expanding its presence in the Middle East and Asia Pacific regions. This product reportedly improves catalyst life by 20%, addressing refinery demands for operational efficiency.
Johnson Matthey unveiled a collaboration with a major Asian refinery in late 2024 to develop next-generation sulfur-resistant catalysts incorporating proprietary nanomaterials, aimed at enhancing sulfur tolerance and reducing catalyst deactivation rates. The partnership is positioned to accelerate adoption across emerging markets.
R. Grace & Co. recently expanded its manufacturing footprint in Europe to meet increasing demand for sulfur recovery catalysts, complementing its existing portfolio focused on sustainable regeneration processes. This move supports the company’s strategy to strengthen supply chain resilience and reduce lead times.
Honeywell UOP entered a joint development agreement in mid-2024 to integrate advanced catalyst technologies into biofuel production processes, aiming to broaden sulfur-resistant catalyst applications beyond traditional refining.
BASF SE reported progress in scaling its sustainable catalyst production technologies during late 2024, emphasizing green chemistry principles in the manufacture of sulfur-resistant catalysts. This initiative aligns with global decarbonization goals and growing customer demand for environmentally friendly solutions.
Clariant AG announced new investments in research centers focused on catalyst regeneration and lifecycle extension technologies in early 2025, reinforcing its commitment to innovation and sustainability.
This overview highlights the leading manufacturers’ dominance and strategic initiatives shaping the sulfur-resistant catalyst market, illustrating how product innovation, market share, and recent developments interplay to drive future growth.
“Sulfur-resistant catalyst Production Data and Sulfur-resistant catalyst Production Trend, Sulfur-resistant catalyst Production Database and forecast”
-
-
- Sulfur-resistant catalyst production database for historical years, 12 years historical data
- Sulfur-resistant catalyst production data and forecast for next 12 years
- Sulfur-resistant catalyst sales volume by manufacturers
-
“Track Real-time Sulfur-resistant catalyst Prices for purchase and sales contracts, Sulfur-resistant catalyst price charts, Sulfur-resistant catalyst weekly price tracker and Sulfur-resistant catalyst monthly price tracker”
-
-
- Gain control on your purchase and sales contracts through our real-time Sulfur-resistant catalyst price tracker and Sulfur-resistant catalyst price trend analysis
- Sulfur-resistant catalyst weekly price tracker and forecast for next four weeks
- Sulfur-resistant catalyst monthly price tracker and forecast for next two months
-
Market Scenario, Demand vs Supply, Average Product Price, Import vs Export, till 2035
- Global Sulfur-resistant catalyst Market revenue and demand by region
- Global Sulfur-resistant catalyst Market production and sales volume
- United States Sulfur-resistant catalyst Market revenue size and demand by country
- Europe Sulfur-resistant catalyst Market revenue size and demand by country
- Asia Pacific Sulfur-resistant catalyst Market revenue size and demand by country
- Middle East & Africa Sulfur-resistant catalyst Market revenue size and demand by country
- Latin America Sulfur-resistant catalyst Market revenue size and demand by
- Import-export scenario – United States, Europe, APAC, Latin America, Middle East & Africa
- Average product price – United States, Europe, APAC, Latin America, Middle East & Africa
- Market player analysis, competitive scenario, market share analysis
- Business opportunity analysis
Key questions answered in the Global Sulfur-resistant catalyst Market Analysis Report:
- What is the market size for Sulfur-resistant catalyst in United States, Europe, APAC, Middle East & Africa, Latin America?
- What is the yearly sales volume of Sulfur-resistant catalyst and how is the demand rising?
- Who are the top market players by market share, in each product segment?
- Which is the fastest growing business/ product segment?
- What should be the business strategies and Go to Market strategies?
The report covers Sulfur-resistant catalyst Market revenue, Production, Sales volume, by regions, (further split into countries):
- Asia Pacific (China, Japan, South Korea, India, Indonesia, Vietnam, Rest of APAC)
- Europe (UK, Germany, France, Italy, Spain, Benelux, Poland, Rest of Europe)
- North America (United States, Canada, Mexico)
- Latin America (Brazil, Argentina, Rest of Latin America)
- Middle East & Africa
Table of Contents:
- Introduction to Sulfur-Resistant Catalyst Market
- Overview of Sulfur-Resistant Catalysts and Their Importance
- Role of Sulfur-Resistant Catalysts in Industrial Applications
- Historical Development and Market Evolution
- Mechanism of Sulfur Resistance in Catalysts
- How Sulfur Affects Catalysts and Their Performance
- Chemical and Structural Properties of Sulfur-Resistant Catalysts
- Methods of Enhancing Sulfur Tolerance in Catalysts
- Types of Sulfur-Resistant Catalysts
- Metal-Based Sulfur-Resistant Catalysts (Nickel, Platinum, etc.)
- Bimetallic and Multimetallic Catalysts for Enhanced Sulfur Resistance
- Non-metallic and Hybrid Sulfur-Resistant Catalysts
- Nano-structured and Advanced Sulfur-Tolerant Catalysts
- Applications of Sulfur-Resistant Catalysts
- Oil Refining: Hydrodesulfurization and Sulfur Removal
- Petrochemical Production: Catalysis in the Presence of Sulfur
- Environmental Catalysis: Reducing SOx Emissions
- Biodiesel Production and Renewable Energy Applications
- Other Applications in Industrial and Chemical Synthesis
- Market Drivers and Challenges
- Increasing Demand for Cleaner Fuels and Emissions Control
- Regulatory Pressures for Sulfur Content Reduction in Fuels
- Technological Advancements in Sulfur-Resistant Catalysis
- Challenges in Catalyst Durability and High Sulfur Tolerance
- Market Size and Growth Forecast (2025-2035)
- Global Market Overview and Size Estimates
- Regional Market Breakdown and Forecasted Growth
- Trends and Future Outlook in Sulfur-Resistant Catalysts
- Regional Market Insights
- North America: Technological Innovation and Regulatory Impact
- Europe: Sulfur Regulation and Catalysis Demand
- Asia-Pacific: Market Growth and Refining Needs
- Latin America and Middle East & Africa: Emerging Market Opportunities
- Competitive Landscape and Key Market Players
- Leading Manufacturers and Suppliers of Sulfur-Resistant Catalysts
- Market Share and Competitive Positioning
- Key Innovations, Strategic Initiatives, and Partnerships
- Mergers, Acquisitions, and Developments in the Sulfur-Resistant Catalyst Market
- Technological Innovations in Sulfur-Resistant Catalysts
- Advances in Catalyst Composition for Enhanced Sulfur Tolerance
- Use of Nanotechnology and New Materials in Sulfur-Resistant Catalysts
- Innovations in Catalyst Life Cycle and Regeneration
- Production and Manufacturing of Sulfur-Resistant Catalysts
- Raw Materials and Sourcing for Sulfur-Resistant Catalysts
- Manufacturing Processes and Challenges in Catalyst Production
- Scaling Production and Maintaining Catalyst Quality
- Pricing Trends and Market Economics
- Price Dynamics for Sulfur-Resistant Catalysts
- Factors Affecting Catalyst Pricing: Material and Manufacturing Costs
- Economic Impact of Sulfur-Resistant Catalysts on Industrial Operations
- Sustainability and Environmental Considerations
- Sustainable Practices in Sulfur-Resistant Catalyst Production
- Reducing Environmental Impact of Catalysis in Sulfur-Heavy Environments
- Compliance with Environmental Standards and Emission Control
- Regulatory Landscape and Compliance
- Global and Regional Regulations on Sulfur Content in Fuels
- Compliance Standards for Sulfur-Resistant Catalysts
- Industry-Specific Regulatory Requirements for Emission Reductions
- Global Trade and Market Dynamics
- International Trade Trends for Sulfur-Resistant Catalysts
- Key Exporting and Importing Regions for Sulfur-Tolerant Catalysts
- Trade Barriers, Tariffs, and Global Market Access
- Risks and Opportunities in the Sulfur-Resistant Catalysts Market
- Risks Associated with Supply Chain, Raw Materials, and Production
- Market Opportunities for Expansion in Emerging Economies
- Technological Breakthroughs Creating New Market Applications
- Impact of Automation and Digitalization in Catalyst Production
- Automation and Smart Technologies in Sulfur-Resistant Catalyst Manufacturing
- Industry 4.0’s Role in Enhancing Catalyst Efficiency
- Digitalization and Process Optimization in Refining and Petrochemical Catalysis
- Consumer Trends and Demand Drivers
- Consumer Preferences for Low-Sulfur and Cleaner Fuels
- Impact of Sustainability Trends on Sulfur-Resistant Catalyst Demand
- Evolving Needs in the Petrochemical and Refining Industries
- Future Outlook and Projections (2025-2035)
- Long-Term Market Growth and Projections for Sulfur-Resistant Catalysts
- Future Technological Developments in Catalyst Design and Sulfur Resistance
- Emerging Market Trends and Applications in Clean Fuel Production
- Conclusion and Strategic Recommendations
- Key Insights from the Sulfur-Resistant Catalyst Market Analysis
- Strategic Recommendations for Industry Stakeholders and Manufacturers
- Final Thoughts on Market Evolution, Challenges, and Opportunities
Other recently published reports:
“Every Organization is different and so are their requirements”- Datavagyanik
Companies We Work With
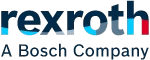
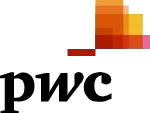
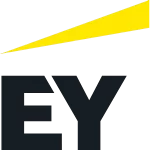
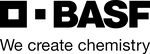
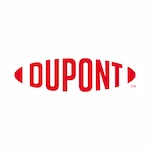

Do You Want To Boost Your Business?
drop us a line and keep in touch
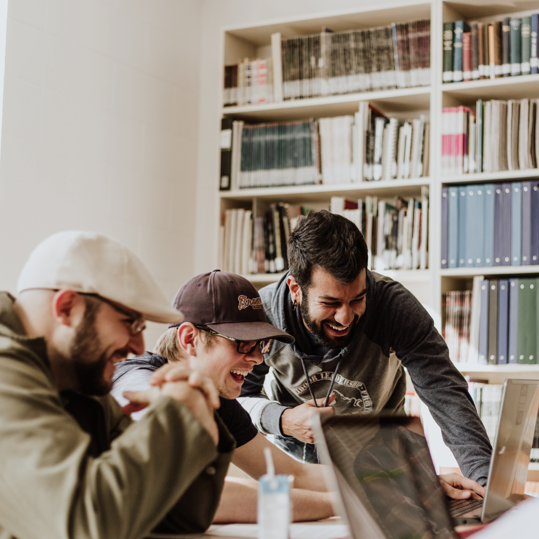