Zinc silicate Market Size, Production, Sales, Average Product Price, Market Share, Import vs Export
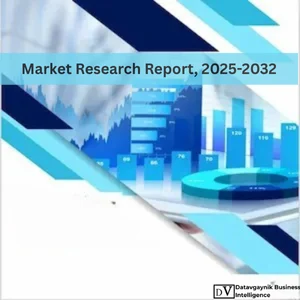
- Published 2025
- No of Pages: 120+
- 20% Customization available
Zinc silicate market driven by surge in high-performance industrial coatings
The zinc silicate market is witnessing robust expansion due to its critical role in industrial coatings, particularly where long-term corrosion resistance is essential. In sectors such as marine, oil & gas, and infrastructure, zinc silicate coatings are rapidly replacing traditional materials due to their superior durability, heat resistance, and non-toxic properties. For instance, zinc silicate is now widely applied in the coating of steel structures exposed to moisture, salinity, and industrial pollutants.
Infrastructure investments across developing and developed economies are a key force behind this surge. With trillions allocated to bridges, tunnels, ports, and offshore platforms, the demand for corrosion-resistant coatings has grown in tandem. Zinc silicate coatings offer a service life of up to 20 years without maintenance in aggressive environments, making them a cost-effective solution for governments and private operators. As protective coating standards become stricter, particularly around volatile organic compound (VOC) content, zinc silicate-based formulations are gaining favor due to their environmental compliance and long-term performance.
Zinc silicate market size supported by ceramic industry’s accelerating output
Another major driver supporting the zinc silicate market size is the rapid evolution of the ceramics industry. Zinc silicate is a fundamental component in ceramic glazes, where it enhances gloss, hardness, and chemical resistance. Ceramic tiles, sanitaryware, and technical ceramics are seeing increasing demand due to global urbanization trends and higher construction activity in both residential and commercial segments.
For example, architectural demand for high-gloss, durable, and decorative tiles in kitchens, bathrooms, and exterior facades has led manufacturers to adopt zinc silicate-based glazes for aesthetic and functional enhancement. In technical ceramics, where dimensional stability, wear resistance, and thermal insulation are critical, zinc silicate’s contributions are irreplaceable. This has led to steady uptake in applications such as circuit boards, heat shields, and chemical reactors. With the global ceramics output growing by millions of tons annually, the zinc silicate market is poised to benefit directly from this expansion.
Rising electronics production boosting zinc silicate market applications
The global electronics sector continues to present new opportunities for the zinc silicate market, particularly through its application in phosphors for light-emitting diodes (LEDs), display screens, and optoelectronics. Zinc silicate’s dielectric properties make it ideal for use in capacitors, insulators, and various passive electronic components. As the demand for high-performance electronic systems in consumer electronics, industrial automation, and telecommunication infrastructure grows, so does the need for advanced materials like zinc silicate.
For instance, the widespread shift to LED lighting systems, which are now a global standard in residential, commercial, and industrial spaces, relies heavily on phosphors incorporating zinc silicate. In LED manufacturing, zinc silicate enables the conversion of blue light into white light efficiently, ensuring energy savings and consistent color rendering. As nations around the world commit to reducing power consumption through smart lighting systems, the adoption of zinc silicate-based phosphor materials will continue to expand, fueling growth in the zinc silicate market.
Zinc silicate market accelerated by demand from rubber and tire industries
The tire and rubber industries are emerging as strong contributors to the zinc silicate market. Zinc silicate is used as a reinforcing filler in rubber compounds, particularly for tires that require enhanced wear resistance, thermal stability, and mechanical strength. As the global vehicle fleet continues to grow, driven by rising automobile sales and replacement tire demand, so too does the need for high-performance rubber additives.
For example, in tire manufacturing, zinc silicate helps extend tire lifespan by improving resistance to abrasion and deformation under high loads. In heavy-duty applications such as off-road vehicles, trucks, and industrial machinery, the material also contributes to heat dissipation and structural reinforcement. With global tire production exceeding two billion units annually and vehicle electrification driving demand for low-resistance, high-durability tires, the zinc silicate market is positioned to capture increasing volumes from rubber manufacturers.
Glass manufacturing innovations expanding zinc silicate market footprint
The glass manufacturing sector represents another high-growth area for the zinc silicate market, particularly in the production of specialty glasses for electronics, optics, and laboratory use. Zinc silicate improves the thermal shock resistance, hardness, and transparency of glass, making it suitable for high-end applications where durability and optical clarity are paramount.
Smartphone screens, microscope lenses, optical fibers, and solar panel covers increasingly incorporate zinc silicate-enhanced glass to achieve both aesthetic and technical performance. In laboratory environments, glassware must withstand frequent thermal cycling and chemical exposure, and zinc silicate additives meet these requirements while maintaining transparency and structural integrity. As technological progress drives demand for stronger, more versatile glass products, the consumption of zinc silicate in this segment continues to rise, strengthening the overall market.
Zinc silicate market gains from growth in energy-efficient lighting
Energy efficiency mandates and consumer preferences for sustainable technologies are catalyzing demand for zinc silicate in lighting applications. The shift from traditional incandescent and fluorescent lighting to LED systems has positioned zinc silicate as a vital material in the production of phosphor layers. These layers are responsible for transforming ultraviolet or blue light into usable visible light, and zinc silicate offers the performance stability required for high-efficiency lighting.
In commercial buildings, public infrastructure, and even smart homes, lighting systems now rely on materials that offer longevity, color stability, and energy performance. Zinc silicate’s contribution to luminescent materials makes it a preferred choice in this context. Additionally, innovations in display technology for televisions, smartphones, and tablets are fueling demand for new phosphor blends, many of which continue to include zinc silicate for brightness and longevity.
Nanotechnology advancements creating new zinc silicate market segments
Research and innovation in nanotechnology are creating new application segments for the zinc silicate market. At the nanoscale, zinc silicate exhibits unique optical, electrical, and mechanical properties, making it suitable for use in biomedical devices, catalytic systems, and advanced sensors. In particular, zinc silicate nanoparticles are being explored for drug delivery systems, bio-imaging, and environmental remediation.
For example, in catalytic converters and gas sensors, nano zinc silicate offers enhanced surface area and reactivity, enabling more efficient chemical processes. In medicine, its biocompatibility and controlled reactivity allow it to be integrated into diagnostic tools and drug carriers. The expanding scope of nanomaterials in high-tech and healthcare sectors represents a future-oriented growth frontier for the zinc silicate market.
Environmental compliance supporting shift toward zinc silicate-based solutions
As industries globally face tighter environmental regulations, particularly around heavy metal content in coatings and manufacturing materials, the zinc silicate market is benefiting from its classification as a safer, non-toxic alternative. Unlike lead- or chromate-based coatings, zinc silicate offers strong protective capabilities without the ecological and health hazards associated with legacy materials.
Green building certifications, such as LEED and BREEAM, are also driving demand for eco-friendly coatings, which is pushing paint and coating manufacturers to reformulate their products with zinc silicate. In industrial environments, the shift toward low-VOC, sustainable materials aligns with zinc silicate’s properties, making it an increasingly essential ingredient across environmentally regulated markets.
Track Country-wise Zinc silicate Production and Demand through our Zinc silicate Production Database
-
-
- Zinc silicate production database for 28+ countries worldwide
- Zinc silicate sales volume for 32+ countries
- Country-wise Zinc silicate production capacity, production plant mapping, production capacity utilization for 28+ manufacturers
- Zinc silicate production plants and production plant capacity analysis by top manufacturers
-
Track real-time Zinc silicate Prices, Zinc silicate price charts for 28+ countries, Zinc silicate weekly price tracker and Zinc silicate monthly price tracker
-
-
- Track real-time Zinc silicate prices and Zinc silicate price trend in 28+ countries though our excel-based Zinc silicate price charts
- Real-time Zinc silicate price tracker dashboard with 28+ countries
- Complete transparency on Zinc silicate price trend through our Zinc silicate monthly price tracker, Zinc silicate weekly price tracker
-
Zinc silicate market witnessing sharp regional diversification in demand
The zinc silicate market has evolved into a regionally diversified ecosystem, with demand patterns shifting rapidly based on industrial maturity, regulatory frameworks, and manufacturing capabilities. Asia Pacific remains the largest and fastest-growing consumer of zinc silicate, propelled by rising investments in construction, automotive, electronics, and renewable energy sectors. Countries like China, India, and Japan are not only high-volume consumers but also major producers of zinc silicate, enabling integrated supply chains and cost-efficient scaling.
For example, China’s dominance in global infrastructure and electronics production has led to a surge in demand for corrosion-resistant coatings and phosphor materials, both of which rely heavily on zinc silicate. India’s push toward self-reliant manufacturing and smart city development has driven its zinc silicate consumption in paints, industrial coatings, and tile production. Meanwhile, Japan’s advanced electronics and automotive sectors continue to depend on high-purity zinc silicate for LED applications and specialty ceramics.
North America zinc silicate market growing through industrial coatings and electronics
In North America, the zinc silicate market is gaining momentum, particularly in sectors focused on high-performance coatings, LED lighting systems, and optoelectronic devices. The United States, with its vast marine infrastructure and aging bridges, is actively replacing legacy coatings with zinc silicate-based alternatives that offer enhanced durability and environmental compliance. For example, the rehabilitation of over 45,000 structurally deficient bridges is expected to fuel the demand for protective coatings over the next decade, contributing directly to zinc silicate consumption.
Additionally, the North American LED lighting market, valued at over USD 12 billion, continues to expand in response to energy efficiency mandates. Zinc silicate is critical to LED phosphor production, and the region’s focus on domestic semiconductor manufacturing under the CHIPS Act is expected to further increase demand for dielectric materials like zinc silicate.
European zinc silicate market focused on sustainable materials innovation
Europe’s zinc silicate market is characterized by strong regulatory push for sustainable and low-toxicity materials across construction, coatings, and electronics sectors. Germany, France, and the United Kingdom are at the forefront of this movement. For instance, Germany’s automotive and machinery industries are actively integrating zinc silicate-based coatings for improved resistance to environmental stress and wear.
The European Union’s REACH regulations have accelerated the adoption of environmentally safe compounds, with zinc silicate gaining traction as a preferred substitute to lead- and chromate-based coatings. In France, the ceramics industry’s emphasis on artistic tiles, porcelain, and smart glazes has created a niche but high-value demand for zinc silicate. The UK’s growing focus on offshore wind energy and marine protection systems also translates into expanding zinc silicate usage in corrosion-resistant coatings.
Emerging markets fueling new zinc silicate market growth corridors
Emerging markets across Latin America, the Middle East, and Africa are playing an increasingly vital role in the zinc silicate market. Rapid urbanization, industrialization, and infrastructure investments are the primary growth drivers. For instance, Brazil and Mexico are witnessing strong demand for zinc silicate in construction coatings and tire manufacturing, where it improves rubber durability and chemical resistance.
In the Middle East, infrastructure projects under national development plans in Saudi Arabia, the UAE, and Egypt are incorporating eco-friendly coatings for environmental compliance, opening up opportunities for zinc silicate-based materials. South Africa’s growing automotive and glass industries have also begun integrating zinc silicate in specialty coatings and reinforcement applications.
Zinc silicate market segmented by application and end-use sector
The zinc silicate market is segmented across several core application areas, each contributing uniquely to its expansion. Coatings and paints remain the largest segment, accounting for over 35% of the global zinc silicate demand. This is due to the material’s high-performance anti-corrosive and heat-resistant properties. For example, offshore oil rigs, refineries, and petrochemical plants require protective systems that can resist harsh weather and chemical exposure—conditions under which zinc silicate outperforms traditional coatings.
Ceramics and glass applications represent another significant portion of the market, estimated at around 25% of total consumption. Zinc silicate provides gloss retention, hardness, and resistance to acids and thermal shocks in both construction and laboratory-grade glass. With the global technical ceramics market projected to grow above 6% CAGR, zinc silicate is poised to remain a vital ingredient in high-specification ceramic formulations.
In electronics and semiconductors, zinc silicate’s usage is rapidly growing due to its relevance in LED phosphors, capacitors, and optical devices. As demand for high-luminance display systems and energy-efficient lighting continues to rise, this segment is expected to expand significantly in both volume and value. Rubber and tire applications currently hold around 15% market share, primarily driven by the automotive sector’s demand for heat-resistant and reinforced rubber formulations.
Zinc silicate market segmentation by form and processing method
The zinc silicate market also segments by product form—primarily powder and granules—and by production technique, namely the direct and indirect methods. Zinc silicate powder dominates the market, as it offers better dispersion properties for use in coatings, glazes, and phosphor applications. It is the preferred format for electronics manufacturers and paint formulators seeking consistent performance.
The granule form is largely used in glass and ceramic manufacturing, where uniform melt flow and control over grain size are essential. The direct method of production, involving the high-temperature reaction of zinc oxide and silica, is more commonly used for large-scale and cost-effective output. However, the indirect method, using zinc salts and silica, yields higher purity zinc silicate that is essential for applications in semiconductors and LED technologies.
Zinc silicate price trend shaped by raw material volatility and energy costs
The zinc silicate price trend has shown moderate fluctuations over the past three years, driven primarily by changes in raw material availability and energy costs. Zinc oxide and silica, the two primary inputs, have both experienced price volatility due to mining regulations, supply chain disruptions, and energy inflation.
For instance, the average zinc silicate price ranged between USD 2,400 and USD 2,800 per metric ton in 2023, depending on grade and purity. Higher-purity variants for electronic applications command premiums of up to 30% due to their stricter manufacturing specifications. The zinc silicate price trend is also influenced by environmental compliance costs, especially in regions where emission controls and safety standards necessitate additional processing steps.
In energy-intensive countries such as China and India, electricity price hikes have impacted furnace-based production methods, leading to periodic upward movements in zinc silicate prices. On the other hand, regions with integrated refining and chemical clusters, such as Germany and Japan, have been able to stabilize output and partially absorb price shocks.
Global zinc silicate price dynamics linked to import-export shifts
Global trade dynamics have a significant impact on the zinc silicate price trend. Countries like China, which dominate global exports, are capable of influencing international pricing through adjustments in export duties, domestic subsidies, or raw material prioritization. For example, in 2022, temporary restrictions on zinc oxide exports led to supply tightening in Southeast Asia and Europe, pushing zinc silicate prices up by over 12% in some regions.
Import-dependent nations, especially in the Middle East and Latin America, are particularly sensitive to these shifts. The zinc silicate price in these markets often includes transportation, import duties, and purity surcharges, making regional price discrepancies common. Conversely, Japan and South Korea, which maintain stable internal production and focus on high-value applications, tend to maintain more consistent zinc silicate pricing.
Outlook for zinc silicate market pricing and future supply chain adjustments
Moving forward, the zinc silicate price trend is expected to remain moderately upward in the short term due to sustained demand from electronics, automotive, and coatings sectors. However, the long-term outlook may stabilize as more regions localize production, reduce reliance on raw material imports, and invest in energy-efficient manufacturing methods.
For instance, Southeast Asia is emerging as a competitive hub for zinc silicate production due to low labor costs, growing technical expertise, and government-backed incentives for industrial materials. As regional producers scale up, global pricing competition could intensify, placing downward pressure on the zinc silicate price in the medium term.
In conclusion, the zinc silicate market continues to evolve as a dynamic, application-rich industry. Regional demand, end-use diversification, technological integration, and global pricing forces are collectively shaping its growth trajectory. As industries worldwide pursue sustainability, durability, and energy efficiency, the role of zinc silicate as a strategic material is more prominent than ever.
Zinc silicate Manufacturing Database, Zinc silicate Manufacturing Capacity
-
-
- Zinc silicate top manufacturers market share for 28+ manufacturers
- Top 10 manufacturers and top 17 manufacturers of Zinc silicate in North America, Europe, Asia Pacific
- Zinc silicate production plant capacity by manufacturers and Zinc silicate production data for 28+ market players
- Zinc silicate production dashboard, Zinc silicate production data in excel format
-
Zinc silicate price charts, Zinc silicate weekly price tracker and Zinc silicate monthly price tracker
-
-
- Factors impacting real-time Zinc silicate prices in 28+ countries worldwide
- Zinc silicate monthly price tracker, Zinc silicate weekly price tracker
- Real-time Zinc silicate price trend, Zinc silicate price charts, news and updates
- Tracking Zinc silicate price fluctuations
-
Leading manufacturers shaping the global zinc silicate market
The zinc silicate market is dominated by a combination of global chemical giants and specialized material producers, each playing a critical role in meeting diverse industry demands. These manufacturers cater to application-specific requirements across coatings, ceramics, electronics, and glass manufacturing, often supported by dedicated product lines and tailored formulations.
Among the top manufacturers, companies such as Ferro Corporation, 3M Company, Heubach Group, Zochem Inc., and Reade Advanced Materials are considered market leaders due to their extensive portfolios, global reach, and focus on innovation.
Ferro Corporation driving zinc silicate market presence in coatings and ceramics
Ferro Corporation has established a strong foothold in the zinc silicate market through its advanced ceramic and pigment divisions. The company offers zinc silicate formulations specifically designed for high-performance glazes and enamels used in architectural ceramics, cookware, and sanitaryware. Its Opticolor product line incorporates zinc silicate as a key component, delivering durability, color stability, and heat resistance.
Ferro’s zinc silicate materials are also employed in industrial coatings for infrastructure applications, contributing to long-term protection against environmental degradation. With global production facilities and a wide distribution network, Ferro holds a significant share of the zinc silicate market, particularly in the ceramics and coatings segments.
3M Company leveraging advanced materials for electronics and phosphors
3M, a leader in advanced materials, plays a key role in the zinc silicate market through its range of electronic-grade silicate compounds. The company’s zinc silicate-based phosphors are used in LED lighting systems, electronic displays, and energy-efficient screens. These formulations are engineered for high luminosity, long lifespan, and consistent optical performance.
In addition to electronics, 3M also integrates zinc silicate in specialty coatings designed for chemical processing and power generation equipment. The company’s proprietary surface modification technologies enhance the bonding efficiency and corrosion resistance of zinc silicate-based coatings. 3M maintains a strong position in the high-purity zinc silicate market segment, especially for electronic and optoelectronic applications.
Heubach Group expanding market share through eco-friendly coating solutions
Heubach Group has emerged as a key player in the zinc silicate market, focusing on pigment technologies and corrosion protection systems. The company’s Heucosil product line features zinc silicate-rich anti-corrosion pigments that are used extensively in marine, bridge, and oil & gas applications. These coatings are recognized for their superior resistance to salt spray and chemical exposure.
Heubach’s emphasis on eco-friendly and VOC-compliant formulations has gained traction in Europe and North America, where regulatory pressures favor non-toxic alternatives. The company’s vertically integrated production and R&D capabilities position it as a frontrunner in supplying sustainable zinc silicate-based coatings across major industrial sectors.
Zochem Inc. contributing to zinc silicate market through zinc oxide innovations
Zochem Inc., one of North America’s largest zinc oxide producers, plays an indirect yet critical role in the zinc silicate market. As a primary supplier of high-purity zinc oxide, Zochem supports downstream manufacturers that convert zinc oxide into zinc silicate through both direct and indirect synthesis methods.
By providing ultra-fine, low-impurity zinc oxide grades, Zochem enables production of high-performance zinc silicate used in phosphors, ceramics, and coatings. The company’s strategic supply agreements with coating manufacturers across the United States and Canada contribute to its influence on zinc silicate availability and quality, despite not producing zinc silicate as a final product.
Reade Advanced Materials leading in specialty zinc silicate grades
Reade Advanced Materials is known for its ability to supply customized zinc silicate grades for niche applications. The company offers both powder and granular forms tailored to user-specific technical requirements. Its zinc silicate products are widely used in high-purity electronics applications, display screens, and LED manufacturing.
Reade also supplies zinc silicate for thermal barrier coatings in industrial furnaces, aerospace components, and chemical reactors. The company’s flexibility in batch sizes and emphasis on quality control have positioned it as a preferred supplier for R&D labs and manufacturers needing application-specific zinc silicate solutions.
Zinc silicate market share by manufacturers
The zinc silicate market share is currently fragmented, with top-tier players collectively accounting for approximately 55%–60% of the global supply. Ferro Corporation and Heubach Group each hold estimated shares of 15%–18%, driven by their dominance in ceramic coatings and corrosion protection markets. 3M Company commands roughly 10% of the global share, focused heavily on high-end electronic and optical applications.
Mid-size companies such as Reade Advanced Materials and regional suppliers contribute around 20% to 25%, targeting customized and high-purity product niches. Meanwhile, raw material suppliers like Zochem influence the value chain despite not producing zinc silicate directly, due to their control over feedstock quality and pricing.
This distribution indicates a balanced mix of large-scale industrial producers and niche suppliers, reflecting the diverse nature of zinc silicate applications. As market demand shifts toward energy-efficient and environmentally compliant products, market shares are expected to favor companies with strong R&D capabilities and adaptable production lines.
Recent developments in the zinc silicate market and industry announcements
The zinc silicate market has witnessed several notable developments in recent months, reflecting growing industrial activity and innovation.
In January 2024, Heubach Group announced the launch of its next-generation zinc silicate anti-corrosion pigment line under the Heucosil-X series. These products are designed for harsh marine environments and feature improved particle dispersion and faster drying times. The new line is expected to capture additional market share in Southeast Asia and the Middle East.
In March 2024, 3M reported increased production capacity for zinc silicate-based phosphor compounds at its Minnesota facility. This expansion was in response to higher global demand for LED lighting systems and advanced display technology, particularly from automotive and smart home manufacturers.
Ferro Corporation, in April 2024, revealed a strategic partnership with a Southeast Asian ceramics producer to co-develop zinc silicate-enriched decorative glazes. This partnership is projected to increase Ferro’s presence in the Asia Pacific region, where ceramic tile production is forecasted to rise by over 8% annually.
Meanwhile, Reade Advanced Materials introduced a pilot project in May 2024 offering nano-structured zinc silicate powder for biomedical sensor applications. The project targets high-precision uses in healthcare and defense technologies and signals the emergence of new application verticals within the zinc silicate market.
These updates illustrate the dynamic nature of the zinc silicate market, where manufacturers are leveraging both product innovation and geographic expansion to stay competitive. As technological and regulatory landscapes evolve, the market is expected to favor agile players that can quickly adapt their offerings to emerging industrial requirements.
Zinc silicate Production Data and Zinc silicate Production Trend, Zinc silicate Production Database and forecast
-
-
- Zinc silicate production database for historical years, 10 years historical data
- Zinc silicate production data and forecast for next 10 years
- Zinc silicate sales volume by manufacturers
-
Track Real-time Zinc silicate Prices for purchase and sales contracts, Zinc silicate price charts, Zinc silicate weekly price tracker and Zinc silicate monthly price tracker
-
-
- Gain control on your purchase and sales contracts through our real-time Zinc silicate price tracker and Zinc silicate price trend analysis
- Zinc silicate weekly price tracker and forecast for next four weeks
- Zinc silicate monthly price tracker and forecast for next two months
-
Market Scenario, Demand vs Supply, Average Product Price, Import vs Export, till 2035
- Global Zinc silicate Market revenue and demand by region
- Global Zinc silicate Market production and sales volume
- United States Zinc silicate Market revenue size and demand by country
- Europe Zinc silicate Market revenue size and demand by country
- Asia Pacific Zinc silicate Market revenue size and demand by country
- Middle East & Africa Zinc silicate Market revenue size and demand by country
- Latin America Zinc silicate Market revenue size and demand by
- Import-export scenario – United States, Europe, APAC, Latin America, Middle East & Africa
- Average product price – United States, Europe, APAC, Latin America, Middle East & Africa
- Market player analysis, competitive scenario, market share analysis
- Business opportunity analysis
Key questions answered in the Global Zinc silicate Market Analysis Report:
- What is the market size for Zinc silicate in United States, Europe, APAC, Middle East & Africa, Latin America?
- What is the yearly sales volume of Zinc silicate and how is the demand rising?
- Who are the top market players by market share, in each product segment?
- Which is the fastest growing business/ product segment?
- What should be the business strategies and Go to Market strategies?
The report covers Zinc silicate Market revenue, Production, Sales volume, by regions, (further split into countries):
- Asia Pacific (China, Japan, South Korea, India, Indonesia, Vietnam, Rest of APAC)
- Europe (UK, Germany, France, Italy, Spain, Benelux, Poland, Rest of Europe)
- North America (United States, Canada, Mexico)
- Latin America (Brazil, Argentina, Rest of Latin America)
- Middle East & Africa
Table of Contents:
Zinc Silicate Market
- Introduction to Zinc Silicate
- Chemical Properties and Structural Composition
- Industrial Applications and Functional Benefits
- Evolution of Zinc Silicate in Various Industries
- Market Overview and Industry Landscape
- Current Market Scenario and Historical Growth Trends
- Key Market Drivers, Challenges, and Opportunities
- Emerging Technological Advancements Impacting the Market
- Global Market Size and Forecast (2024-2035)
- Market Valuation and Revenue Trends
- Growth Potential in Key Industrial Sectors
- Regional and Global Demand-Supply Analysis
- Production Methods and Technological Innovations
- Manufacturing Techniques for Zinc Silicate
- Efficiency Improvements and Cost-Effective Production Strategies
- Sustainability and Environmental Impact Considerations
- Product Segmentation and Market Categorization
- High-Purity Zinc Silicate for Industrial Use
- Zinc Silicate-Based Coatings and Paints
- Zinc Silicate in High-Performance Ceramics
- Nano-Engineered Zinc Silicate for Specialty Applications
- Application-Based Market Demand and Growth Potential
- Corrosion-Resistant Protective Coatings
- Refractory Materials and Heat-Resistant Applications
- Glass, Ceramics, and Structural Components
- Industrial Lubricants and Anti-Wear Additives
- Other Emerging Industrial and Commercial Uses
- Regional Market Analysis and Expansion Trends
- North America: Industrial Growth and Market Demand
- Europe: Regulatory Compliance and Technological Developments
- Asia-Pacific: Major Manufacturing Hubs and Export Trends
- Latin America: Investment Opportunities and Market Penetration
- Middle East & Africa: Industrialization and Market Potential
- Competitive Landscape and Key Market Players
- Profiles of Leading Zinc Silicate Manufacturers
- Market Share and Strategic Positioning
- Recent Developments, Mergers, and Collaborations
- Supply Chain and Logistics Analysis
- Raw Material Sourcing and Procurement Challenges
- Distribution Networks and Market Accessibility
- Impact of Trade Policies on Global Supply Chains
- Pricing Analysis and Market Profitability
- Pricing Trends Across Different Regions
- Cost Breakdown in Zinc Silicate Production
- Market Margins and Profitability Trends
- Regulatory and Environmental Considerations
- Industry Standards for Zinc Silicate Manufacturing and Usage
- Environmental Impact and Sustainability Practices
- Compliance with International Safety Regulations
- International Trade and Market Accessibility
- Global Export-Import Data and Trade Flow
- Key Exporting and Importing Countries
- Tariff Structures and Market Entry Strategies
- Consumer Behavior and Market Demand Trends
- Industry-Specific Consumption Patterns
- Shifts in Preferences Toward High-Performance Zinc Silicate
- Future Market Trends and Emerging Consumer Preferences
- Investment Opportunities and Business Expansion Strategies
- Potential Growth Areas for Zinc Silicate Market Expansion
- Mergers, Acquisitions, and Strategic Alliances
- Risk Assessment and Market Entry Challenges
- Market Risks and Constraints
- Supply Chain Disruptions and Raw Material Volatility
- Economic and Geopolitical Uncertainties Affecting Market Growth
- Regulatory Challenges and Compliance Risks
- Future Market Outlook and Strategic Recommendations
- Long-Term Market Forecast and Industry Innovations
Other recently published reports:
“Every Organization is different and so are their requirements”- Datavagyanik
Companies We Work With
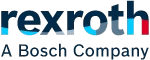
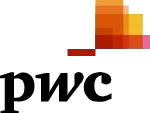
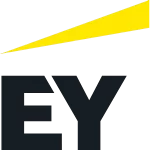
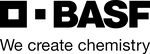
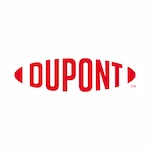

Do You Want To Boost Your Business?
drop us a line and keep in touch
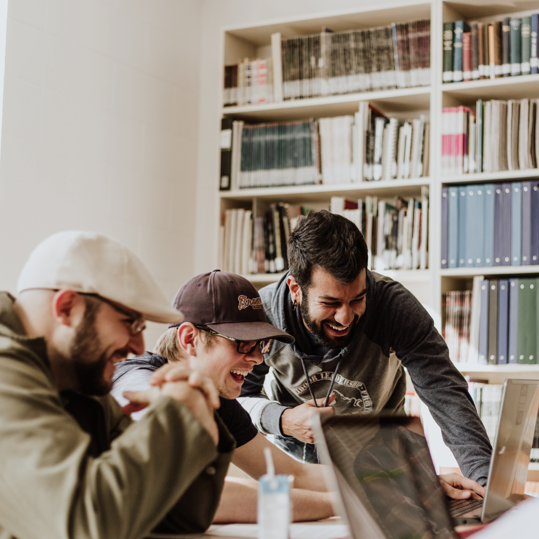