Catalytic Reforming Reactors Market Size, Production, Sales, Average Product Price, Market Share, Import vs Export
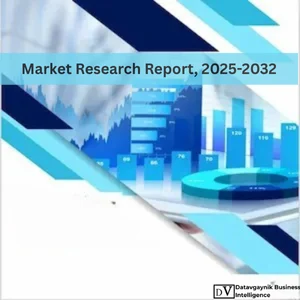
- Published 2025
- No of Pages: 120+
- 20% Customization available
Rising Demand for High-Octane Fuel Driving the Catalytic Reforming Reactors Market
The Catalytic Reforming Reactors Market is undergoing substantial transformation, led by an accelerating global need for high-octane gasoline and aviation fuels. These fuels are essential in meeting the performance and emissions requirements of modern internal combustion engines. For example, in 2023, India’s gasoline consumption surged by over 10 percent compared to the previous year, driven by growing personal vehicle ownership and expanding road networks. Similarly, the United States continues to lead in gasoline consumption, accounting for nearly 20 percent of global demand.
Catalytic reforming is the refining process responsible for converting low-octane naphtha into high-octane reformate, which is then blended into gasoline. This process is impossible without catalytic reforming reactors, which have become indispensable to refineries aiming to maximize fuel quality. The Catalytic Reforming Reactors Market is therefore directly benefiting from the continued demand for cleaner, more efficient transportation fuels.
Refinery Modernization Accelerating Growth in the Catalytic Reforming Reactors Market
Aging refinery infrastructure in developed economies such as the United States, Germany, and Japan is undergoing widespread modernization to meet evolving fuel quality regulations and efficiency benchmarks. According to Datavagyanik, over 60 percent of European refineries are over 30 years old and require technological upgrades to remain competitive.
Catalytic reforming reactors are at the core of these modernization efforts, especially as they allow for cleaner fuel production while improving the yield of high-value petrochemical feedstocks. In North America, refinery upgrade projects valued at more than 15 billion USD are currently underway, a large portion of which is allocated to integrating advanced reactor technologies. These investments are not only ensuring compliance with environmental mandates but also enhancing overall refinery economics. ‘
Datavagyanik also covers related markets such as the Reforming & Isomerization Catalysts Market. Exploring these markets offers a broader view of the industry landscape and how adjacent sectors influence the main topic.
Catalytic Reforming Reactors Market Tied to Surge in Petrochemical Demand
The Catalytic Reforming Reactors Market is witnessing heightened demand due to the expanding global petrochemical sector. Reformate, a major product of the catalytic reforming process, serves as a critical feedstock for producing benzene, toluene, and xylene (BTX) — the foundational building blocks for plastics, synthetic fibers, and resins.
For instance, the global market for benzene alone is expected to reach 87 billion USD by 2030, growing at a CAGR of over 4 percent. Much of this growth is concentrated in Asia Pacific, where countries like China and South Korea are rapidly scaling up petrochemical capacities. Refineries in these regions are significantly increasing the deployment of catalytic reforming reactors to keep pace with this demand.
Environmental Regulations Boosting Cleaner Fuel Production via Catalytic Reforming Reactors
Stricter emissions standards in both developed and emerging markets are accelerating the shift towards cleaner fuels. The European Union’s Renewable Energy Directive and the United States Environmental Protection Agency’s Tier 3 regulations are just two examples of frameworks pushing refineries to reduce sulfur and aromatic content in fuels.
Catalytic reforming reactors play a crucial role in producing reformate with high-octane ratings and lower undesirable compounds. For instance, French and German refiners have committed over 2 billion USD in clean fuel upgrades by 2026, largely through the installation of energy-efficient catalytic reforming units. As countries align with global sustainability goals, the Catalytic Reforming Reactors Market is increasingly positioned as a strategic asset in refinery compliance and transformation efforts.
Catalytic Reforming Reactors Market Benefiting from Hydrogen Co-Production
One of the most compelling benefits of catalytic reforming is the production of hydrogen as a byproduct. Hydrogen is essential in hydrocracking and hydrotreating processes, which are central to producing ultra-low sulfur diesel and removing contaminants from fuel streams.
The Catalytic Reforming Reactors Market is gaining traction as refineries seek to reduce their dependence on external hydrogen sources. For example, in South Korea, leading refiners such as SK Innovation are leveraging catalytic reforming units not only for high-octane fuel production but also to integrate on-site hydrogen recovery systems. This integration boosts refinery efficiency, reduces operating costs, and aligns with global decarbonization initiatives.
Catalytic Reforming Reactors Market Size Expanding with Emerging Market Refinery Projects
The Catalytic Reforming Reactors Market Size is being significantly shaped by large-scale refinery developments across emerging markets. Countries such as India, Vietnam, Nigeria, and Saudi Arabia are investing heavily in refining infrastructure to meet domestic and export fuel needs. For instance, India plans to increase its refining capacity from 250 million metric tons per annum (MMTPA) to 400 MMTPA by 2030, creating robust demand for catalytic reforming systems.
Datavagyanik highlights that over 35 new refining projects across the Asia-Pacific and Middle East regions are currently in various stages of development. Each of these projects requires catalytic reforming reactors as part of their core process design. As these countries prioritize fuel self-sufficiency and aim to move up the value chain through petrochemical integration, the Catalytic Reforming Reactors Market is projected to see sustained growth.
Technological Innovations Elevating Efficiency in the Catalytic Reforming Reactors Market
The Catalytic Reforming Reactors Market is also being reshaped by advancements in catalyst composition and reactor design. Technologies such as continuous catalytic reforming (CCR) systems enable uninterrupted catalyst regeneration, enhancing reactor uptime and throughput. Platinum-based bimetallic catalysts, including platinum-rhenium and platinum-iridium combinations, are now standard in many large-scale installations for their durability and high conversion efficiency.
Leading technology providers from the United States, Japan, and Germany are introducing next-generation reactors that reduce energy consumption by up to 15 percent and extend catalyst life by 20 to 30 percent. These developments are particularly attractive to refineries seeking to reduce operational expenditure and environmental impact, making innovation a central driver of the Catalytic Reforming Reactors Market.
Shift Towards Aromatics Production Increasing Catalytic Reforming Reactors Market Demand
Another significant trend shaping the Catalytic Reforming Reactors Market is the increasing demand for aromatics, especially in the packaging, automotive, and textiles industries. Aromatic compounds like benzene and toluene are essential for the synthesis of polymers, rubber, and solvents.
China’s aromatic production capacity surpassed 60 million tons in 2023, and is projected to grow by another 25 percent within five years. This massive expansion is creating parallel demand for catalytic reforming reactors, which provide a reliable and cost-efficient method of generating high-purity aromatics from naphtha. The Middle East is also emerging as a strategic hub, with countries like the United Arab Emirates integrating catalytic reforming capabilities within their downstream petrochemical ecosystems.
Automotive Sector Growth Driving Long-Term Catalytic Reforming Reactors Market Outlook
Despite the rise of electric mobility, internal combustion engines still dominate global vehicle sales, especially in developing regions. In 2023, over 68 million internal combustion engine vehicles were sold globally, and gasoline vehicles represented over 75 percent of this volume.
The Catalytic Reforming Reactors Market stands to benefit directly from this trend, as refiners must produce larger volumes of high-octane gasoline to meet growing automotive fuel demand. Countries in Africa, Southeast Asia, and Latin America are reporting double-digit growth in vehicle sales, reinforcing the long-term need for reforming capacity enhancements in local refineries.
Catalytic Reforming Reactors Market Size Underpinned by Global Refining Expansion
The Catalytic Reforming Reactors Market Size is firmly supported by global investments in refining capacity expansion. According to Datavagyanik, global refining capacity is projected to grow by over 5 million barrels per day by 2030. Much of this growth is coming from strategic developments in Asia Pacific, the Middle East, and Africa.
For example, the Al-Zour refinery in Kuwait and the Dangote Refinery in Nigeria, two of the largest greenfield projects globally, have incorporated advanced catalytic reforming reactors into their designs. These investments reflect the critical importance of catalytic reforming in modern refinery configurations, ensuring both product quality and operational efficiency.
“Track Country-wise Catalytic Reforming Reactors Production and Demand through our Catalytic Reforming Reactors Production Database”
-
-
- Catalytic Reforming Reactors production database for 28+ countries worldwide
- Catalytic Reforming Reactors Powder sales volume for 32+ countries
- Country-wise Catalytic Reforming Reactors production capacity and production plant mapping, production capacity utilization for 28+ manufacturers
- Catalytic Reforming Reactors production plants and production plant capacity analysis for top manufacturers
-
Asia Pacific Dominates Global Demand in the Catalytic Reforming Reactors Market
The Asia Pacific region is currently the epicenter of global growth in the Catalytic Reforming Reactors Market. With nations like China and India accounting for nearly 35 percent of global refining capacity expansions, the demand for catalytic reforming technologies has intensified. China alone added over 1.2 million barrels per day of new refining capacity between 2021 and 2024, driven by its ambitious energy security goals and petrochemical self-sufficiency agenda. Datavagyanik highlights that over 70 percent of newly commissioned refineries in Asia are integrating catalytic reforming reactors as standard components.
India’s refining sector is similarly scaling up, with domestic gasoline demand projected to grow at a CAGR of 6.5 percent through 2030. This growth is powered by rising automotive penetration, which reached nearly 35 vehicles per 1,000 people in 2023 — a figure expected to double within a decade. As refineries move to increase reformate output and reduce aromatic content in fuels, the Catalytic Reforming Reactors Market is expected to expand in tandem across the region.
North America Catalytic Reforming Reactors Market Driven by Technology Upgrades
The Catalytic Reforming Reactors Market in North America is being driven more by modernization than new capacity additions. In the United States, over 80 percent of existing refineries are undergoing phased upgrades to comply with the Environmental Protection Agency’s Tier 3 standards. These regulations mandate sulfur content in gasoline to be reduced to 10 parts per million, a target achievable through the use of advanced catalytic reforming reactors.
For instance, major refineries in Texas and Louisiana have replaced older semi-regenerative units with Continuous Catalytic Reforming (CCR) systems that allow for uninterrupted catalyst regeneration and increased hydrogen yield. Datavagyanik confirms that CCR installations in the U.S. increased by 18 percent between 2019 and 2023, reflecting the industry’s pivot toward operational efficiency and regulatory compliance.
Canada also presents strong potential, with Alberta’s growing petrochemical sector creating fresh demand for reformate feedstocks. Refineries in Western Canada are investing in modular catalytic reforming units to supply BTX aromatics for domestic chemical manufacturing, boosting the overall Catalytic Reforming Reactors Market size in the region.
Europe’s Catalytic Reforming Reactors Market Propelled by Decarbonization Mandates
The European Catalytic Reforming Reactors Market is being shaped by strict emissions reduction targets and an urgent need to upgrade aging refinery infrastructure. Countries such as Germany, France, and the Netherlands are integrating next-generation reforming technologies to align with the European Union’s Fit for 55 policy, which aims to cut greenhouse gas emissions by 55 percent by 2030.
For example, German refiners are leading the transition to hydrogen-integrated catalytic reforming units that enable greater energy recovery and lower carbon emissions. In France, refineries are prioritizing catalytic systems that can operate at reduced pressure while maximizing aromatic yield — a critical requirement given the country’s rising demand for plastics, adhesives, and resins. The Catalytic Reforming Reactors Market in Europe is thus being redefined not just by production goals, but by sustainability benchmarks.
Middle East Expanding Catalytic Reforming Reactors Market Through Mega Refining Complexes
The Middle East is fast becoming a global refining powerhouse, with large-scale integrated projects reshaping the Catalytic Reforming Reactors Market landscape. Saudi Arabia, the United Arab Emirates, and Kuwait are investing in refinery-petrochemical integration, and catalytic reforming plays a central role in these blueprints.
Saudi Aramco’s Jazan and Ras Tanura refineries are among the largest adopters of catalytic reforming reactors in the Gulf region. Datavagyanik reports that over 500,000 barrels per day of refining capacity added in the Gulf Cooperation Council (GCC) countries between 2020 and 2024 included catalytic reforming components. The aim is to increase local production of gasoline and aromatics while reducing dependency on imports.
The region’s high availability of naphtha feedstock, coupled with its ambition to dominate BTX exports, makes it a critical growth zone for the Catalytic Reforming Reactors Market over the next decade.
Africa and Latin America: Emerging Frontiers for the Catalytic Reforming Reactors Market
Africa and Latin America represent untapped yet promising geographies for the Catalytic Reforming Reactors Market. Countries like Nigeria, Angola, and Egypt are investing in refining capacity to reduce reliance on fuel imports. Nigeria’s Dangote Refinery, with a planned capacity of 650,000 barrels per day, has incorporated advanced catalytic reforming units to supply both domestic and export markets with high-octane fuels and aromatics.
In Latin America, Brazil and Mexico are accelerating refinery upgrades under national energy independence programs. Pemex, for instance, is focusing on semi-regenerative catalytic reforming systems for existing refineries to produce cleaner gasoline. Datavagyanik indicates that Latin American demand for reformate feedstocks will grow at 4.2 percent annually until 2030, enhancing the region’s significance in the global Catalytic Reforming Reactors Market.
Global Production Hubs Defining Supply in the Catalytic Reforming Reactors Market
Production of catalytic reforming reactors is concentrated in regions with high engineering capabilities such as the United States, Germany, Japan, and South Korea. The U.S. remains the largest exporter of CCR systems, while Germany leads in modular, semi-regenerative units optimized for European refineries.
China has also emerged as a strong player, particularly in producing cost-competitive reforming reactors for regional and African markets. South Korea and Japan contribute significantly to high-performance catalyst supply chains, enabling enhanced yields and longer reactor life cycles. This global manufacturing footprint ensures that the Catalytic Reforming Reactors Market remains both diversified and resilient, especially amid supply chain disruptions and geopolitical tensions.
Segmentation of the Catalytic Reforming Reactors Market by Reactor Type
The Catalytic Reforming Reactors Market is segmented primarily by reactor type, each serving distinct refinery configurations and operational needs. Continuous Catalytic Reforming (CCR) reactors are widely used in high-capacity refineries due to their ability to operate without shutdowns and regenerate catalysts in real-time. These systems represent over 60 percent of new installations globally.
Semi-regenerative reforming reactors are typically deployed in medium-scale refineries where periodic shutdowns are manageable. These units are more cost-effective but offer lower flexibility compared to CCR systems. Cyclic reforming reactors, though less common, are used where hydrogen recovery is a top priority, such as in specialized petrochemical applications.
This segmentation is crucial as it enables refiners to align reactor type with throughput targets, feedstock quality, and energy efficiency goals, thereby influencing the overall Catalytic Reforming Reactors Market dynamics.
Catalytic Reforming Reactors Market Segmentation by Feedstock and Application
Naphtha remains the dominant feedstock in the Catalytic Reforming Reactors Market due to its high aromatic and hydrogen content. Straight-run gasoline is also processed in some facilities aiming for specific reformate compositions. The choice of feedstock has a direct impact on reactor configuration, catalyst selection, and product yield.
From an application standpoint, the Catalytic Reforming Reactors Market is driven by three main segments: high-octane gasoline production, petrochemical feedstock generation, and hydrogen co-production. For example, reformate accounts for nearly 35 percent of global BTX production, underscoring the importance of catalytic reforming in chemical value chains.
Hydrogen produced during reforming is increasingly being repurposed within the same refinery to fuel hydrocracking and hydrotreating units, making reformers central to integrated refinery operations. This functional versatility is a key growth lever for the Catalytic Reforming Reactors Market.
Catalytic Reforming Reactors Price Trend Influenced by Raw Material and Technology Costs
The Catalytic Reforming Reactors Price Trend has shown a steady upward movement over the last five years, primarily due to rising costs of key materials like platinum, rhenium, and iridium used in catalysts. Platinum prices rose from approximately 950 USD/oz in 2020 to over 1,100 USD/oz by the end of 2023, directly impacting the Catalytic Reforming Reactors Price.
Moreover, the push for energy-efficient, low-emission reactor systems has increased demand for advanced technologies, which come at a premium. For instance, a CCR unit with integrated hydrogen recovery and waste heat recovery systems can cost 15 to 25 percent more than a standard semi-regenerative unit. Datavagyanik notes that average Catalytic Reforming Reactors Price has increased by 8 to 10 percent since 2019, and this trend is expected to continue, especially as sustainability features become mandatory.
Labor shortages and extended lead times for high-grade alloys and control systems are also contributing factors to Catalytic Reforming Reactors Price Trend volatility. However, manufacturers are responding with modular reactor offerings and localized production models to mitigate cost pressures and maintain market competitiveness.
“Catalytic Reforming Reactors Manufacturing Database, Catalytic Reforming Reactors Manufacturing Capacity”
-
-
- Catalytic Reforming Reactors top manufacturers market share for 28+ manufacturers
- Top 8 manufacturers and top 18 manufacturers of Catalytic Reforming Reactors in North America, Europe, Asia Pacific
- Production plant capacity by manufacturers and Catalytic Reforming Reactors production data for 28+ market players
- Catalytic Reforming Reactors production dashboard, Catalytic Reforming Reactors production data in excel format
-
Leading Manufacturers Dominating the Catalytic Reforming Reactors Market
The Catalytic Reforming Reactors Market is shaped by a group of globally recognized manufacturers that have established strong technological leadership and operational footprints. These companies drive innovation in catalyst formulation, reactor design, and integrated system engineering, offering solutions tailored to refinery scale, feedstock types, and regulatory demands.
Among the most prominent players in the Catalytic Reforming Reactors Market are UOP (a Honeywell company), Axens, Haldor Topsoe, Johnson Matthey, Lummus Technology, KBR Inc., and China Petroleum Engineering & Construction Corporation (CPECC). These companies collectively account for the majority share of new catalytic reforming reactor installations globally.
Each of these manufacturers offers proprietary product lines and reactor systems designed for specific refining applications, from high-octane gasoline production to petrochemical feedstock generation and hydrogen recovery.
UOP (Honeywell) Leading with Continuous Reforming Systems
UOP remains a market leader in the Catalytic Reforming Reactors Market, holding the largest market share globally. The company’s CCR Platforming™ technology is one of the most widely adopted continuous catalytic reforming systems in the world. This technology enables refiners to achieve continuous catalyst regeneration, optimize reformate yield, and co-produce large volumes of hydrogen. With over 250 units installed worldwide, UOP’s dominance in CCR systems is firmly established across both mature and emerging markets.
UOP’s reactor systems are often integrated into large refining and petrochemical complexes, especially in North America, the Middle East, and Asia. Their modular design approach and compatibility with a range of feedstocks make them a preferred choice for greenfield refinery projects and modernization initiatives alike.
Axens Expanding Share in the Catalytic Reforming Reactors Market
Axens, headquartered in France, has emerged as a strong competitor with its Octanizing™ semi-regenerative and CCR reforming solutions. The company has captured a significant share of the Catalytic Reforming Reactors Market in Europe and Asia Pacific, particularly among refineries focused on aromatic production for the plastics and textile industries.
Axens specializes in catalyst-technology integration and has developed high-performance bimetallic catalysts that extend operational life and minimize coke formation. Their systems are widely used in regions with strict emission standards and in facilities prioritizing fuel-grade reformate production. Axens has reported growing market penetration in India, South Korea, and Southeast Asia, where refinery expansions are accelerating.
Haldor Topsoe Delivering Advanced Catalyst Solutions
Haldor Topsoe, a Denmark-based technology provider, holds a key position in the Catalytic Reforming Reactors Market through its focus on catalyst innovation. While not a reactor hardware supplier per se, the company plays a vital role in shaping operational performance by offering high-activity platinum-based and bimetallic catalysts for both semi-regenerative and CCR reforming systems.
Topsoe’s ReforMax® catalyst line is widely used across European and Asian markets and is valued for its resistance to deactivation and high hydrogen yield. The company’s growing collaborations with reactor manufacturers have helped extend its indirect market share in large integrated refinery projects.
Johnson Matthey Strengthening Catalyst Market Position
Johnson Matthey, a UK-based leader in precious metal technologies, is a major catalyst supplier in the Catalytic Reforming Reactors Market. The company’s PRISM™ and ACTIV™ series of reforming catalysts are used in CCR and cyclic reforming units to improve selectivity and reduce regeneration frequency.
With a growing focus on environmental compliance and energy efficiency, Johnson Matthey has seen increased demand for its customized catalyst formulations from refiners in the Middle East and South America. The company’s strong presence in catalyst supply chains has contributed to its robust position in the market.
KBR Inc. and Lummus Technology Pushing Modular Reactor Design
KBR Inc. and Lummus Technology are notable for their engineering and technology-driven approach in the Catalytic Reforming Reactors Market. KBR’s offerings include customized reforming units integrated within larger hydroprocessing and petrochemical packages. The company’s focus on modular reactor systems is especially suited for refineries in remote locations or those requiring fast-track installations.
Lummus Technology, recently spun off as an independent entity, is ramping up its footprint in Asia and the Middle East by offering compact, energy-efficient reforming systems optimized for both high-octane fuel and aromatic production. The company’s streamlined reactor designs have gained traction in refinery expansions targeting downstream chemical integration.
China Petroleum Engineering & Construction Corporation (CPECC) Scaling in Asia
CPECC is rapidly gaining ground in the Catalytic Reforming Reactors Market, particularly in Asia and Africa. Leveraging China’s expansive refining sector and cost-effective engineering solutions, CPECC delivers turnkey catalytic reforming reactor projects that are price-competitive and tailored to regional fuel standards.
The company’s reactor systems have been installed in several new refineries in China, Pakistan, and sub-Saharan Africa. CPECC’s integration capabilities and local manufacturing advantages are helping it grow market share among cost-sensitive clients focused on fuel independence and domestic petrochemical output.
Catalytic Reforming Reactors Market Share by Manufacturer
In terms of market share, UOP commands approximately 40 to 45 percent of the global Catalytic Reforming Reactors Market, due to its early mover advantage, extensive client base, and performance-proven technologies. Axens follows with a share of 20 to 25 percent, strengthened by its strong European presence and expanding Asian footprint.
Johnson Matthey and Haldor Topsoe collectively hold around 15 to 20 percent market share, particularly in the catalyst supply domain. The remainder is divided among regional players and engineering firms such as KBR, Lummus, and CPECC, each holding between 5 and 10 percent, with significant growth potential in emerging markets.
Market share dynamics are expected to shift gradually as modular, low-emission, and hydrogen-optimized reactors gain wider adoption and as developing countries commission more grassroots refinery projects.
Recent Industry Developments in the Catalytic Reforming Reactors Market
Recent developments in the Catalytic Reforming Reactors Market have reflected a strong focus on emissions control, integration with petrochemical units, and geopolitical diversification of supply chains.
In October 2023, Axens announced the commissioning of a new Octanizing™ reforming unit in India’s largest private-sector refinery, aimed at boosting reformate output by 400,000 tons annually to meet both gasoline and aromatics demand.
In January 2024, Honeywell UOP finalized a long-term partnership with a Middle Eastern energy firm to supply its CCR Platforming™ systems across five upcoming refineries. This move is expected to increase UOP’s installed base in the GCC by nearly 20 percent by 2026.
Meanwhile, Johnson Matthey in February 2024 expanded its catalyst manufacturing capacity in Germany to meet growing demand from European refiners upgrading to low-carbon operations. The expansion includes a new production line for PRISM™ reforming catalysts with higher thermal stability and lower precious metal content.
KBR Inc., in March 2024, secured a major EPC contract for a catalytic reforming project in North Africa, marking its entry into a region with rising refinery construction activity and demand for modular, high-efficiency systems.
These developments reflect a broader shift in the Catalytic Reforming Reactors Market toward tailored, region-specific solutions and long-term strategic collaborations between technology providers and refiners.
“Catalytic Reforming Reactors Production Data and Catalytic Reforming Reactors Production Trend, Catalytic Reforming Reactors Production Database and forecast”
-
-
- Catalytic Reforming Reactors production database for historical years, 10 years historical data
- Catalytic Reforming Reactors production data and forecast for next 7 years
-
Market Scenario, Demand vs Supply, Average Product Price, Import vs Export, till 2035
- Global Catalytic Reforming Reactors Market revenue and demand by region
- Global Catalytic Reforming Reactors Market production and sales volume
- United States Catalytic Reforming Reactors Market revenue size and demand by country
- Europe Catalytic Reforming Reactors Market revenue size and demand by country
- Asia Pacific Catalytic Reforming Reactors Market revenue size and demand by country
- Middle East & Africa Catalytic Reforming Reactors Market revenue size and demand by country
- Latin America Catalytic Reforming Reactors Market revenue size and demand by
- Import-export scenario – United States, Europe, APAC, Latin America, Middle East & Africa
- Average product price – United States, Europe, APAC, Latin America, Middle East & Africa
- Market player analysis, competitive scenario, market share analysis
- Business opportunity analysis
Key questions answered in the Global Catalytic Reforming Reactors Market Analysis Report:
- What is the market size for Catalytic Reforming Reactors in United States, Europe, APAC, Middle East & Africa, Latin America?
- What is the yearly sales volume of Catalytic Reforming Reactors and how is the demand rising?
- Who are the top market players by market share, in each product segment?
- Which is the fastest growing business/ product segment?
- What should be the business strategies and Go to Market strategies?
The report covers Catalytic Reforming Reactors Market revenue, Production, Sales volume, by regions, (further split into countries):
- Asia Pacific (China, Japan, South Korea, India, Indonesia, Vietnam, Rest of APAC)
- Europe (UK, Germany, France, Italy, Spain, Benelux, Poland, Rest of Europe)
- North America (United States, Canada, Mexico)
- Latin America (Brazil, Argentina, Rest of Latin America)
- Middle East & Africa
Table of Contents:
-
- Introduction to Catalytic Reforming Reactors
1.1 Overview of Catalytic Reforming Process
1.2 Role of Catalytic Reforming Reactors in Refining - Types of Catalytic Reforming Reactors
2.1 Fixed-Bed Catalytic Reforming Reactors
2.2 Moving-Bed Catalytic Reforming Reactors
2.3 Semi-Fixed and Fluidized-Bed Reactors - Key Components of Catalytic Reforming Reactors
3.1 Reactor Vessel and Catalyst Bed
3.2 Regeneration Systems
3.3 Heat Exchangers and Separation Units
3.4 Control and Monitoring Systems - Catalytic Reforming Process
4.1 Mechanism of Catalytic Reforming
4.2 Role of Catalysts in Reforming Reactions
4.3 Optimization of Reaction Conditions and Product Yield - Applications of Catalytic Reforming Reactors
5.1 Gasoline Production and Upgrading
5.2 Aromatics and Petrochemical Production
5.3 Hydrogen Production and Refining
5.4 Environmental Applications in Fuel and Chemical Manufacturing - Market Overview of Catalytic Reforming Reactors
6.1 Market Size, Growth Trends, and Forecasts (2019–2035)
6.2 Market Drivers: Technological and Economic Factors
6.3 Challenges and Barriers in Market Expansion - Technological Innovations in Catalytic Reforming Reactors
7.1 Advances in Catalyst and Reactor Design
7.2 Innovations in Energy Efficiency and Process Control
7.3 Integration of Digitalization and AI for Optimization - Market Segmentation by Type of Reactor
8.1 Fixed-Bed Reactors Market Trends
8.2 Moving-Bed Reactors and Their Growing Demand
8.3 Semi-Fixed and Fluidized-Bed Reactors Applications - Market Segmentation by End-Use Industry
9.1 Oil and Gas Refining
9.2 Petrochemical Industry
9.3 Hydrogen Production and Energy Storage
9.4 Specialty Chemicals Manufacturing - Competitive Landscape in Catalytic Reforming Reactors Market
10.1 Leading Manufacturers and Key Players
10.2 Market Share Analysis and Competitive Strategies
10.3 Mergers, Acquisitions, and Strategic Partnerships - Cost Structure and Economic Impact
11.1 Capital Investment and Operating Costs
11.2 Cost-Efficiency of Catalytic Reforming Systems
11.3 Economic Viability of Reactors for Different Applications - Challenges in Catalytic Reforming Reactor Operations
12.1 Catalyst Deactivation and Regeneration Issues
12.2 Operational Efficiency and Yield Optimization
12.3 Environmental and Regulatory Challenges - Environmental and Sustainability Impact
13.1 Reducing Emissions and Waste in Reforming Processes
13.2 Innovations for Sustainable Catalyst Management
13.3 Adapting to Environmental Regulations for Cleaner Production - Regulatory Compliance and Standards
14.1 Global Standards for Catalytic Reforming Reactors
14.2 Local and Regional Compliance Guidelines
14.3 Safety Standards and Best Practices in Reactor Operation - Performance and Efficiency Metrics
15.1 Measuring Catalyst Efficiency and Reactor Throughput
15.2 Energy Consumption and Heat Integration
15.3 Maximizing Hydrogen Yield and Quality - Customization of Catalytic Reforming Reactors
16.1 Tailoring Reactors for Specific Feedstocks and Products
16.2 Custom Designs for Low-Emission and High-Efficiency Production
16.3 Modular and Scalable Reactors for Various Capacities - Integration with Other Refining Processes
17.1 Synergies with Hydroprocessing and Distillation Systems
17.2 Integration with Hydrotreating and Hydrogenation Units
17.3 Enhancing Refining Efficiency through Process Optimization - Technological Trends in Catalytic Reforming Reactors
18.1 Emerging Catalyst Technologies and Reactions
18.2 Use of Artificial Intelligence and Machine Learning in Process Control
18.3 Next-Generation Reactors for Sustainable Operations - Investment and Financing Trends in the Market
19.1 Capital Investment in Refining Infrastructure
19.2 Financing Models for Catalyst and Reactor Development
19.3 Risk Management Strategies in Reactor Projects - Global Market Dynamics for Catalytic Reforming Reactors
20.1 Global Demand for High-Quality Fuels and Chemicals
20.2 Impact of Oil Price Volatility on Refining and Reactor Investments
20.3 Technological Shifts and the Rise of Renewable Feedstocks - Substitute and Alternative Technologies in Refining
21.1 Exploring Alternatives to Catalytic Reforming
21.2 Membrane and Distillation Technologies as Substitutes
21.3 Hybrid Approaches to Catalytic Reforming - Future Outlook for Catalytic Reforming Reactors Market
22.1 Forecasting Market Trends and Developments (2025–2035)
22.2 Emerging Opportunities and Technological Advancements
22.3 Growth Opportunities in Emerging Economies - Case Studies of Catalytic Reforming Reactor Applications
23.1 Successful Implementation in Large Refineries
23.2 Case Study: Innovations in Small-Scale Refining Projects - Strategic Recommendations for Market Participants
24.1 Business Strategies for New Market Entrants
24.2 Growth Strategies for Established Reactor Manufacturers - Conclusion and Key Insights
25.1 Summary of Market Trends and Insights
25.2 Actionable Recommendations for Industry Stakeholders
- Introduction to Catalytic Reforming Reactors
“Every Organization is different and so are their requirements”- Datavagyanik
Companies We Work With
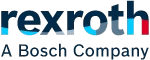
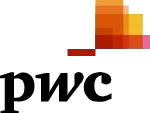
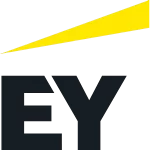
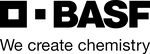
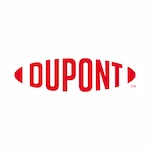

Do You Want To Boost Your Business?
drop us a line and keep in touch
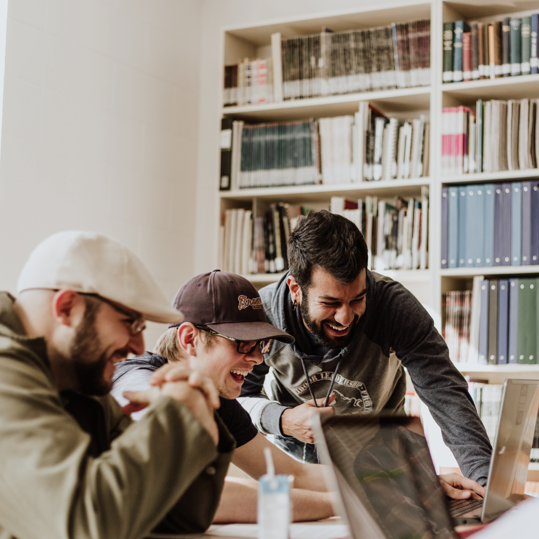