Global Anti-friction coatings Market Size, Production, Sales, Average Product Price, Market Share, Import vs Export
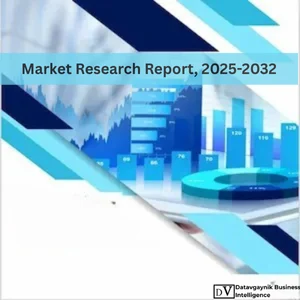
- Published 2025
- No of Pages: 120+
- 20% Customization available
Rising Energy Efficiency Focus Driving Anti-friction Coatings Market Expansion
The Anti-friction coatings market is experiencing substantial traction due to the increasing emphasis on energy efficiency across industrial sectors. In sectors such as automotive, manufacturing, and aerospace, energy losses from mechanical friction are significant contributors to operational inefficiencies. Anti-friction coatings reduce these losses by minimizing surface resistance, directly improving the energy performance of machinery and equipment. For instance, in high-speed production lines, the application of molybdenum disulfide (MoS2) or polytetrafluoroethylene (PTFE) coatings has been shown to reduce frictional losses by up to 40%, extending the life of moving components and lowering energy consumption. As energy efficiency remains a key pillar of sustainability frameworks across manufacturing economies, demand in the Anti-friction coatings market is poised to increase steadily.
Automotive Electrification Fueling Demand in the Anti-friction Coatings Market
With global electric vehicle (EV) sales projected to cross 25 million units by 2030, the role of anti-friction coatings in the automotive industry is becoming more critical than ever. The Anti-friction coatings market is witnessing strong momentum from the rising shift toward e-mobility, where drivetrain systems, battery casings, and motor components demand high-performance coatings that reduce wear and improve efficiency.
For example, the use of diamond-like carbon (DLC) coatings in EV gear systems has improved torque transmission efficiency by reducing surface contact stress. Traditional internal combustion engine (ICE) vehicles also continue to drive growth in the Anti-friction coatings market as manufacturers aim to comply with stricter emission norms by improving fuel economy through reduced friction in pistons, valves, and bearings.
Datavagyanik also covers related markets such as the Low Friction Coatings Market, the Low Friction Polymer Coatings Market, and the Anti-ice Coatings Market. Tracking these sectors reveals parallel dynamics and helps anticipate shifts likely to affect the primary market.
Industrial Machinery Sector Supporting Consistent Anti-friction Coatings Market Demand
The industrial machinery segment accounts for a significant share of the Anti-friction coatings market due to its reliance on heavy-duty equipment and high-speed moving components. In manufacturing plants, mining operations, and construction equipment, anti-friction coatings play a vital role in reducing wear and extending maintenance intervals. For example, in injection molding machines and packaging robots, MoS2 and PTFE coatings enable high cycle rates with minimal lubrication requirements. The increasing deployment of Industry 4.0 technologies, robotics, and automation is also driving the integration of high-precision coated components, ensuring smooth motion control and operational reliability. As a result, the industrial machinery sector continues to be a dependable revenue contributor for the Anti-friction coatings market.
Growth in Aerospace and Defense Enhancing Anti-friction Coatings Market Potential
The aerospace industry demands materials capable of withstanding extreme temperatures, high loads, and corrosive environments. The Anti-friction coatings market benefits from this need as aerospace OEMs adopt coatings for turbine blades, actuation systems, landing gears, and fuel system components. For example, ceramic-based anti-friction coatings are employed in jet engine components to reduce galling and maintain dimensional stability under thermal stress. Furthermore, defense applications are contributing significantly to market expansion, with military-grade equipment requiring long-lasting friction-reducing coatings for mission-critical reliability. As global aerospace and defense expenditure crosses USD 2 trillion annually, anti-friction coating manufacturers are capitalizing on specialized formulations that enhance endurance and system longevity.
Medical Devices and Healthcare Applications Adding New Verticals to the Anti-friction Coatings Market
The Anti-friction coatings market is increasingly diversifying into the healthcare sector, driven by the growing use of coated components in medical devices. Applications range from surgical instruments to wearable health devices and catheters. For instance, PTFE-based coatings in catheters reduce friction during insertion, improving patient comfort and reducing complications. The rise in minimally invasive surgeries and the growing geriatric population are fueling the need for precision medical components that operate smoothly under continuous use. As healthcare spending continues to rise globally, reaching nearly 10% of GDP in most developed economies, the Anti-friction coatings market is well-positioned to tap into this emerging demand vertical.
Electronics Miniaturization Contributing to Higher Coating Adoption
Consumer electronics and precision devices form another important growth node within the Anti-friction coatings market. As devices shrink and internal components become more compact, the requirement for ultra-thin, high-performance coatings grows. Applications in this segment include connectors, switches, mobile phone sliders, and cooling fan assemblies. For example, PTFE-coated switches have demonstrated increased lifespan and reliability in humid environments, making them ideal for smartphones and IoT devices. As the global electronics market surpasses USD 3 trillion in annual sales, the Anti-friction coatings market is witnessing parallel growth through integration into next-generation devices that require consistent, low-resistance mechanical operations.
Renewable Energy Transition Creating Structural Growth in the Anti-friction Coatings Market
Wind turbines, solar panel tracking systems, and hydropower components represent critical application areas where friction-reducing coatings are essential. The Anti-friction coatings market is capitalizing on this shift toward renewables by offering solutions that extend the operational life of equipment in remote or high-load environments. For instance, the use of DLC coatings in wind turbine gearboxes has reduced maintenance downtime by up to 30%, resulting in higher energy output and lower operating costs. With global investments in renewable energy infrastructure projected to reach USD 2 trillion by 2030, anti-friction coating technologies are expected to become a key enabler of sustainable energy systems.
E-commerce and Automated Logistics Expanding Anti-friction Coatings Market Application Scope
The growth of e-commerce and just-in-time logistics has resulted in the widespread deployment of conveyor systems, automated sorting equipment, and robotic packaging units. The Anti-friction coatings market is seeing increased adoption in these segments to ensure continuous, high-speed operations with minimal maintenance. For example, the application of MoS2 coatings in conveyor rollers has enabled smoother operation and improved handling precision in high-volume logistics centers. As global parcel volumes exceed 200 billion annually, the logistics industry’s reliance on anti-friction technologies is becoming a consistent source of demand for market participants.
Innovation in Coating Materials Transforming Anti-friction Coatings Market Landscape
The Anti-friction coatings market is undergoing a technological evolution with the development of new material chemistries and surface treatment processes. Beyond traditional PTFE and MoS2, advanced composites and hybrid formulations are being introduced that offer a superior combination of hardness, lubricity, and environmental compliance. For example, nanoparticle-infused DLC coatings now enable extended wear resistance and improved thermal stability in automotive and aerospace components. This material innovation is also expanding application areas, such as in 3D-printed components and lightweight materials, where conventional lubricants are ineffective. As manufacturers seek to differentiate through performance, innovation is emerging as a key competitive lever in the Anti-friction coatings market.
Sustainability and Compliance Requirements Boosting Eco-friendly Solutions in the Anti-friction Coatings Market
Global environmental regulations and corporate sustainability commitments are reshaping purchasing behavior across industries. The Anti-friction coatings market is witnessing a clear trend toward water-based, solvent-free, and non-toxic coating solutions. For example, in the European market, where REACH compliance is critical, companies are transitioning from solvent-borne PTFE coatings to water-based alternatives without compromising on performance. Similarly, biodegradable coatings are being explored in short-lifecycle applications, such as packaging machinery. As companies align their operations with ESG goals, anti-friction coating suppliers that can deliver sustainable, compliant formulations are gaining a competitive edge.
Growing Emphasis on Equipment Reliability Reinforcing the Anti-friction Coatings Market
For industries operating in high-output environments, equipment uptime is directly linked to profitability. The Anti-friction coatings market is gaining traction as businesses adopt predictive maintenance models that depend on extending the service life of critical components. For instance, mining and heavy construction equipment coated with high-load-bearing MoS2 can operate longer between overhaul cycles. In the energy sector, coatings are being used to maintain consistent turbine performance in variable-load conditions. As industries move toward smart factory models with integrated condition monitoring, demand for reliable, wear-resistant coating technologies is expected to intensify.
Anti-friction Coatings Market Size Outlook Supported by Multi-industry Adoption
The Anti-friction coatings market size is anticipated to grow at a high single-digit CAGR over the forecast period through 2032, driven by multi-sector demand and material innovations. The diverse application spectrum across automotive, aerospace, healthcare, electronics, and energy ensures a resilient growth trajectory. While developed markets like North America and Western Europe will continue to lead in innovation, Asia Pacific is expected to dominate in consumption due to its expanding industrial and manufacturing footprint. With increasing investment in sustainable technologies, the Anti-friction coatings market size is poised to surpass historic benchmarks and become a key component in future-ready industrial ecosystems.
“Track Country-wise Anti-friction coatings Production and Demand through our Anti-friction coatings Production Database”
-
-
- Anti-friction coatings production database for 27+ countries worldwide
- Anti-friction coatings Powder sales volume for 31+ countries
- Country-wise Anti-friction coatings production capacity and production plant mapping, production capacity utilization for 27+ manufacturers
- Anti-friction coatings production plants and production plant capacity analysis for top manufacturers
-
North America Anti-friction Coatings Market: Innovation-Led Demand
The North America Anti-friction coatings market continues to demonstrate strong growth, driven by technological maturity and advanced application development across automotive, aerospace, industrial machinery, and healthcare sectors. The United States accounts for the largest share in the region, with widespread adoption of anti-friction coatings in electric vehicle (EV) manufacturing, high-performance defense systems, and precision medical devices.
For instance, DLC coatings are increasingly used in the EV drivetrain systems manufactured in Michigan and California. Canada also shows growing demand due to its mining and oil & gas industries requiring surface treatments for harsh conditions. In North America, demand is also being supported by reshoring efforts and investment in sustainable production, positioning the Anti-friction coatings market as a strategic enabler of energy-efficient industrial development.
Europe Anti-friction Coatings Market: Regulatory Pressure and Green Manufacturing Driving Adoption
The Europe Anti-friction coatings market is expanding rapidly due to strict environmental regulations and a growing focus on energy efficiency in manufacturing. Countries such as Germany, France, and the UK lead the market due to their strong automotive and aerospace industries. For example, Germany’s leadership in automotive engineering drives widespread use of anti-friction coatings to reduce CO₂ emissions and enhance vehicle performance. In France, aerospace firms increasingly deploy ceramic and MoS2 coatings for turbine components, supporting fuel efficiency and part longevity. Eastern Europe, including Poland and the Czech Republic, is emerging as a high-growth zone due to industrial expansion and foreign direct investment in manufacturing. The European Anti-friction coatings market is distinguished by high penetration of eco-friendly, REACH-compliant coatings.
Asia Pacific Anti-friction Coatings Market: Manufacturing Base and EV Growth Accelerating Demand
Asia Pacific represents the largest and fastest-growing regional Anti-friction coatings market, fueled by expansive manufacturing operations, rising electronics output, and a surge in EV production. China accounts for the lion’s share of demand, with coatings heavily used in automotive assembly lines, robotics, and consumer electronics. For instance, MoS2 coatings are applied to actuators and valve trains in domestic car brands and global automotive joint ventures across Chinese provinces like Guangdong and Shanghai.
In Japan, the focus is on high-performance coatings for aerospace and semiconductor equipment, with firms integrating PTFE and DLC coatings in low-tolerance components. India’s Anti-friction coatings market is rapidly expanding on the back of government-driven manufacturing initiatives and increasing domestic EV production. Southeast Asia, led by Thailand and Vietnam, is seeing growing usage of coatings in logistics equipment and electronics due to the rise of regional export hubs.
Middle East Anti-friction Coatings Market: Energy Sector as Core Driver
The Middle East Anti-friction coatings market is characterized by demand from oil & gas, petrochemical, and infrastructure sectors. In Saudi Arabia and the UAE, anti-friction coatings are used in high-pressure valves, pumps, and pipeline components, reducing maintenance frequency and improving uptime. For instance, in desert pipeline applications, PTFE coatings provide corrosion resistance and operational stability under fluctuating temperatures. The development of EV assembly facilities and renewable energy projects under Saudi Arabia’s Vision 2030 is also expected to stimulate demand for high-durability coatings in future applications. The region’s Anti-friction coatings market is increasingly diversifying as it transitions from hydrocarbon dependency to industrial self-reliance.
Latin America Anti-friction Coatings Market: Growing Demand from Automotive and Packaging Sectors
Latin America shows promising potential in the Anti-friction coatings market, particularly in Brazil and Mexico. Brazil’s automotive and agriculture equipment sectors use anti-friction coatings extensively in engine parts, drive shafts, and hydraulic components. Mexico, a key manufacturing hub for North American OEMs, is driving demand for anti-friction coatings through its export-oriented vehicle production. Additionally, food and beverage processing and packaging sectors in the region are increasingly deploying coatings to improve machinery uptime. With industrial automation gaining momentum across Latin America, the Anti-friction coatings market is expected to grow at a steady pace.
Africa Anti-friction Coatings Market: Early-stage Adoption with Growth Pockets in Mining and Energy
Africa’s Anti-friction coatings market remains nascent but is gaining ground in regions such as South Africa, Nigeria, and Egypt. These markets are driven by demand in mining, infrastructure, and oil production. For instance, mining conveyor systems and crushing equipment in South Africa increasingly employ MoS2 and ceramic coatings to prolong component lifespan under high mechanical stress. Egypt’s investments in renewable energy and logistics are also generating opportunities for coatings used in turbines and high-speed conveyor systems. As infrastructure and industrialization continue to evolve across the continent, anti-friction coating solutions are expected to expand their footprint.
Anti-friction Coatings Market Segmentation by Application and Substrate
The Anti-friction coatings market is segmented across key applications including automotive, aerospace, industrial machinery, healthcare, energy, and electronics. Within automotive, drivetrain systems, piston rings, gears, and EV battery components represent high-volume usage areas. In aerospace, anti-friction coatings are critical for turbine blades, bearings, and actuator systems. The industrial machinery segment uses coatings for robotics, gear assemblies, packaging lines, and die-casting equipment.
In terms of substrate, metals such as steel, aluminum, and titanium represent the primary base materials. Coatings applied to metals provide wear resistance and reduce surface fatigue. Plastics are another major substrate, especially in medical and electronics applications, where sliding and wear surfaces require improved performance. Ceramics, used in aerospace and high-temperature environments, are also increasingly being coated with advanced anti-friction formulations.
Anti-friction Coatings Market Segmentation by Coating Type
The Anti-friction coatings market includes key formulations such as:
- Polytetrafluoroethylene (PTFE): Used in automotive parts and food-grade machinery for its non-stick and low-friction properties.
- Molybdenum Disulfide (MoS2): Applied in aerospace, oil & gas, and industrial machinery for high-load and high-pressure environments.
- Diamond-like Carbon (DLC): Deployed in high-performance automotive and medical components where ultra-low friction and extreme hardness are required.
- Ceramic-based Coatings: Ideal for high-temperature and corrosive environments, common in turbines and power generation systems.
- Graphite and Hybrid Coatings: Used in niche, dry-lubrication environments, particularly in packaging and electronics.
Anti-friction Coatings Price Trend and Regional Pricing Analysis
Anti-friction coatings price varies by region, material composition, application, and volume. In general, PTFE-based coatings are priced between USD 15–30 per kilogram, while MoS2 coatings are in the range of USD 25–45 per kilogram depending on purity and formulation. DLC coatings, due to their advanced processing and hardness, often range from USD 100–300 per kilogram, reflecting their usage in specialized applications.
In Asia Pacific, particularly China and India, Anti-friction coatings prices are lower due to local raw material sourcing and high-volume manufacturing. In contrast, Europe and North America exhibit a higher Anti-friction coatings price due to stringent regulatory compliance (such as REACH and EPA standards) and reliance on advanced formulations. For example, the Anti-friction coatings price in Germany for aerospace-grade DLC coatings can reach up to USD 350 per kilogram, compared to USD 120–150 in South Korea for similar specifications.
The Anti-friction coatings price trend is currently influenced by volatility in raw material costs, particularly fluoro-polymer resins, molybdenum compounds, and synthetic carbon sources. Price fluctuations in crude oil also indirectly affect the cost structure of hydrocarbon-based coatings. As sustainability pressures mount, bio-based and water-based anti-friction coatings are being introduced at competitive pricing, aiming to replace solvent-borne variants. While these sustainable options carry a slight premium today, increased adoption and economies of scale are expected to normalize their prices over the next five years.
Global Production Hubs in the Anti-friction Coatings Market
The Anti-friction coatings market’s production ecosystem is heavily centered in Asia Pacific, North America, and Europe. China leads global production in volume terms, supported by a vast manufacturing base, lower labor costs, and access to raw materials. Japan and South Korea dominate high-precision, high-performance coatings, catering to electronics, medical, and aerospace sectors.
The United States houses major production facilities for anti-friction coatings targeting defense, automotive, and industrial automation. In Europe, Germany and France lead in R&D-driven production with specialized lines for energy-efficient and REACH-compliant coatings. India is emerging as a mid-cost, high-growth production base, exporting to Middle Eastern and African markets.
Trade flows show strong export activity from Asia to North America and Europe, especially for mass-market coatings like PTFE and MoS2. Conversely, high-performance DLC coatings are often produced in developed economies and exported to emerging markets where precision engineering capabilities are still developing.
Outlook on Anti-friction Coatings Price Trend and Regional Shifts
The Anti-friction coatings price trend over the next decade is expected to stabilize, with downward pressure from increased automation, local sourcing, and improved coating deposition technologies. However, high-end formulations like DLC and ceramic hybrids will maintain premium pricing due to their specialized nature and regulatory compliance demands.
Regional shifts in production, particularly toward Southeast Asia and Eastern Europe, will also create new pricing dynamics. For instance, Vietnam’s rise as a coating application hub for electronics could lower regional prices due to scale advantages. Simultaneously, environmental taxes and carbon pricing in Europe could marginally raise Anti-friction coatings prices unless offset by innovation in green chemistries.
As demand rises across diverse sectors—from EVs to industrial robots to wind turbines—the Anti-friction coatings market will be shaped by a blend of regional industrial policies, sustainability transitions, and technological upgrades. Let me know when you’re ready for the final section covering manufacturers and their market share.
“Anti-friction coatings Manufacturing Database, Anti-friction coatings Manufacturing Capacity”
-
- Anti-friction coatings top manufacturers market share for 27+ manufacturers
- Top 8 manufacturers and top 17 manufacturers of Anti-friction coatings in North America, Europe, Asia Pacific
- Production plant capacity by manufacturers and Anti-friction coatings production data for 27+ market players
- Anti-friction coatings production dashboard, Anti-friction coatings production data in excel format
Competitive Landscape and Manufacturer Market Share in the Anti-friction Coatings Market
The Anti-friction coatings market is highly consolidated at the top, with a few major players holding substantial market share globally. These companies have established strong distribution networks, proprietary coating technologies, and diversified product portfolios tailored to multiple end-use industries such as automotive, aerospace, electronics, and energy.
- DuPont (formerly Dow)
DuPont holds a significant position in the global Anti-friction coatings market, primarily through its renowned Teflon™ coating line. The company’s fluoropolymer-based PTFE coatings are widely applied in automotive engine parts, food processing equipment, and electronic components. DuPont’s dominance stems from its long-standing material science leadership and consistent innovation in non-stick and friction-reducing technologies. Its coatings business accounts for a major share of anti-friction solutions in North America and Europe. - PPG Industries
PPG Industries is a major contributor to the Anti-friction coatings market, with strong offerings in automotive and industrial machinery segments. The company’s SermaGard® and Xylan® product lines are well-recognized for corrosion resistance and low-friction performance. PPG’s coatings are widely applied in automotive drivetrain assemblies, aerospace fasteners, and renewable energy components. Its strength lies in its global manufacturing footprint and integration with OEM clients. - Whitford Corporation (a subsidiary of PPG)
Whitford, known for its high-performance fluoropolymer coatings, is another dominant player in the Anti-friction coatings market. Its Xylan® series features prominently across industrial applications where lubrication, wear resistance, and temperature stability are essential. Following its acquisition by PPG, Whitford expanded its reach into advanced applications including surgical instruments and electronics. - Henkel AG & Co. KGaA
Henkel is a key player in the Anti-friction coatings market, leveraging its Loctite® brand to deliver solid film lubricants, molybdenum disulfide-based solutions, and specialty formulations. These coatings are widely used in high-load-bearing automotive parts, aerospace bolts, and precision engineering equipment. Henkel is particularly strong in Europe and Asia Pacific, catering to high-tech manufacturing sectors. - FUCHS Group
FUCHS is known for its comprehensive range of specialty lubricants and coatings, including CASSIDA® and LUBRODAL® lines. The company offers MoS2-based anti-friction coatings for automotive, die-casting, and forging industries. FUCHS has made significant inroads into emerging markets, particularly in India, where industrial machinery and renewable energy equipment coatings have seen rising demand. - Acheson Industries (A Henkel Company)
Acheson, operating under Henkel, supplies conductive and anti-friction coatings under brands like DAG® and Emralon®. These products are widely used in electrical contacts, plastic-metal interface components, and aerospace actuators. Its graphite-based dry film lubricants are noted for their excellent stability under vacuum and extreme temperatures, giving Acheson a niche leadership position in aerospace and defense applications. - Bechem Lubrication Technology
Germany-based Bechem is an important contributor to the Anti-friction coatings market, offering products such as Berucoat and Berulit series. These coatings are favored for industrial assembly lines, textile machinery, and chain drives. Bechem’s technological expertise in boundary lubrication and surface film formation places it among the premium suppliers in European markets. - Endura Coatings
Endura specializes in custom-engineered anti-friction coatings that are widely used in oil and gas, food processing, and defense. Its proprietary Endura® 1100 and 1300 series include MoS2, PTFE, and hybrid ceramic-polymer formulations. The company focuses on high-end applications that require resistance to abrasion, chemicals, and extreme operating conditions, making it a key player in North America. - Curtiss-Wright Surface Technologies
Through its Everlube® brand, Curtiss-Wright provides high-performance anti-friction coatings for aerospace, defense, and heavy machinery. These coatings are specified by global aerospace manufacturers for use in critical components such as turbine bearings and landing gear systems. The company’s specialization in MIL-spec and OEM-certified coatings gives it a strong foothold in regulated markets.
Anti-friction Coatings Market Share by Manufacturers
Based on recent market performance and strategic positioning, the Anti-friction coatings market share is distributed among major players as follows:
- DuPont (including legacy Dow products): Approx. 18–20%
- PPG Industries (including Whitford): Approx. 15–17%
- Henkel (including Acheson): Approx. 13–15%
- FUCHS Group: Approx. 6–8%
- Bechem, Curtiss-Wright, Endura, and others: Collectively 20–25%
- Regional and specialty manufacturers (Asia Pacific, Eastern Europe): Approx. 15–20%
This distribution reflects a moderately consolidated market, with top companies focusing on high-value, OEM-integrated product lines, while regional players cater to volume-driven industrial demand.
Recent Developments and Industry News in the Anti-friction Coatings Market
- March 2024 – PPG Industries announced a USD 70 million expansion of its coatings plant in Ohio, USA. The move is aimed at increasing the production capacity for its Xylan® anti-friction coatings to serve automotive and renewable energy sectors amid rising EV demand.
- January 2024 – Henkel launched a new generation of water-based, low-VOC anti-friction coatings under the Loctite® EcoShield line. These coatings target European customers facing stricter environmental compliance standards.
- November 2023 – DuPont introduced an upgraded formulation of Teflon™ PTFE with higher temperature resistance and improved deposition control for semiconductor processing equipment and advanced medical devices.
- September 2023 – FUCHS Group completed the acquisition of a specialty coating manufacturer in Vietnam to strengthen its footprint in the Southeast Asia Anti-friction coatings market, capitalizing on rising demand in automotive and electronics sectors.
- July 2023 – Curtiss-Wright Surface Technologies signed a strategic supply agreement with a major US-based aerospace OEM to provide Everlube® coatings for next-generation aircraft platforms. The agreement is expected to drive a multi-year increase in volume.
- May 2023 – Bechem Lubrication launched Berucoat AF 728, a MoS2 and graphite-based hybrid coating designed for heavy-duty industrial gears and actuators exposed to high loads and contaminants.
These developments highlight the ongoing emphasis on sustainability, regional manufacturing resilience, and product innovation, which are shaping the future trajectory of the Anti-friction coatings market. With demand increasing across automotive electrification, energy infrastructure, and smart manufacturing, companies with robust R&D pipelines and tailored customer engagement are expected to sustain competitive advantage in the years ahead.
“Anti-friction coatings Production Data and Anti-friction coatings Production Trend, Anti-friction coatings Production Database and forecast”
-
-
- Anti-friction coatings production database for historical years, 10 years historical data
- Anti-friction coatings production data and forecast for next 7 years
-
Market Scenario, Demand vs Supply, Average Product Price, Import vs Export, till 2035
- Global Anti-friction coatings Market revenue and demand by region
- Global Anti-friction coatings Market production and sales volume
- United States Anti-friction coatings Market revenue size and demand by country
- Europe Anti-friction coatings Market revenue size and demand by country
- Asia Pacific Anti-friction coatings Market revenue size and demand by country
- Middle East & Africa Anti-friction coatings Market revenue size and demand by country
- Latin America Anti-friction coatings Market revenue size and demand by
- Import-export scenario – United States, Europe, APAC, Latin America, Middle East & Africa
- Average product price – United States, Europe, APAC, Latin America, Middle East & Africa
- Market player analysis, competitive scenario, market share analysis
- Business opportunity analysis
Key questions answered in the Global Anti-friction coatings Market Analysis Report:
- What is the market size for Anti-friction coatings in United States, Europe, APAC, Middle East & Africa, Latin America?
- What is the yearly sales volume of Anti-friction coatings and how is the demand rising?
- Who are the top market players by market share, in each product segment?
- Which is the fastest growing business/ product segment?
- What should be the business strategies and Go to Market strategies?
The report covers Anti-friction coatings Market revenue, Production, Sales volume, by regions, (further split into countries):
- Asia Pacific (China, Japan, South Korea, India, Indonesia, Vietnam, Rest of APAC)
- Europe (UK, Germany, France, Italy, Spain, Benelux, Poland, Rest of Europe)
- North America (United States, Canada, Mexico)
- Latin America (Brazil, Argentina, Rest of Latin America)
- Middle East & Africa
Table of Contents:
Anti-Friction Coatings Market
- Introduction to Anti-Friction Coatings
1 Overview and Significance in Modern Industries
1.2 Key Properties and Benefits of Anti-Friction Coatings
1.3 Primary End-Use Sectors - Classification of Anti-Friction Coatings
1 Solid Lubricant-Based Coatings
2.2 Oil-Based Coatings
2.3 Water-Based Coatings
2.4 Hybrid Formulations - Global Anti-Friction Coatings Market Landscape (2020-2035)
1 Market Trends and Growth Opportunities
3.2 Revenue Analysis by Region
3.3 Market Evolution and Technological Advancements - Regional Analysis of the Anti-Friction Coatings Market
1 North America: Trends and Opportunities
4.2 Europe: Market Dynamics and Key Players
4.3 Asia-Pacific: Rising Demand in Emerging Economies
4.4 Latin America: Market Potential and Challenges
4.5 Middle East & Africa: Adoption Trends - Anti-Friction Coatings: Application Insights
1 Automotive and Transportation
5.2 Aerospace and Defense
5.3 Industrial Machinery and Equipment
5.4 Energy and Power Generation
5.5 Other Applications - Competitive Landscape and Market Share Analysis
1 Overview of Major Global Manufacturers
6.2 Competitive Strategies and Collaborations
6.3 Market Share Distribution and Forecast - Production and Supply Chain Overview
1 Overview of Production Processes
7.2 Supply Chain Structure and Key Stakeholders
7.3 Challenges in Global Distribution - Technological Innovations in Anti-Friction Coatings
1 Latest Developments in Coating Technologies
8.2 Eco-Friendly and Sustainable Solutions
8.3 Integration of Nanotechnology - Raw Material Analysis
1 Key Raw Materials Used in Production
9.2 Supply Dynamics and Pricing Trends
9.3 Dependence on Regional Suppliers - Market Segmentation and Forecast Analysis
1 Segmentation by Product Type
10.2 Segmentation by End-Use Industry
10.3 Growth Forecasts by Segment (2023-2035) - Trade and Economic Impact Analysis
1 Import-Export Trends by Region
11.2 Trade Barriers and Tariff Structures
11.3 Impact of Global Economic Changes on the Market - Consumer Insights and Demand Drivers
1 Emerging Preferences and Trends
12.2 Impact of Sustainability on Consumer Choices
12.3 Regional Consumption Behavior - Marketing, Distribution, and Sales Channels
1 Role of Distributors and Retail Networks
13.2 Impact of Digital Marketing and E-Commerce
13.3 Key Strategies for Market Penetration - Industrial Chain Analysis
1 Mapping of the Industrial Ecosystem
14.2 Key Contributors to the Value Chain
14.3 Future Evolution of the Chain - Regulatory and Environmental Factors
1 Key Regulatory Policies by Region
15.2 Impact of Environmental Regulations on Production
15.3 Compliance Challenges and Solutions - Market Challenges and Risks
1 Economic and Geopolitical Risks
16.2 Supply Chain Disruptions
16.3 Technological Barriers - Future Outlook and Strategic Recommendations
1 Market Opportunities in Emerging Regions
17.2 Investment Recommendations for Key Stakeholders
17.3 Vision for the Anti-Friction Coatings Industry (2035)
“Every Organization is different and so are their requirements”- Datavagyanik
Companies We Work With
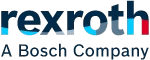
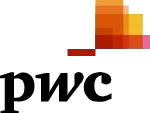
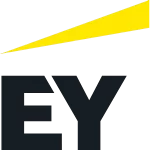
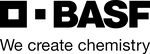
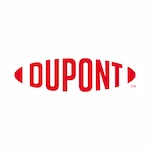

Do You Want To Boost Your Business?
drop us a line and keep in touch
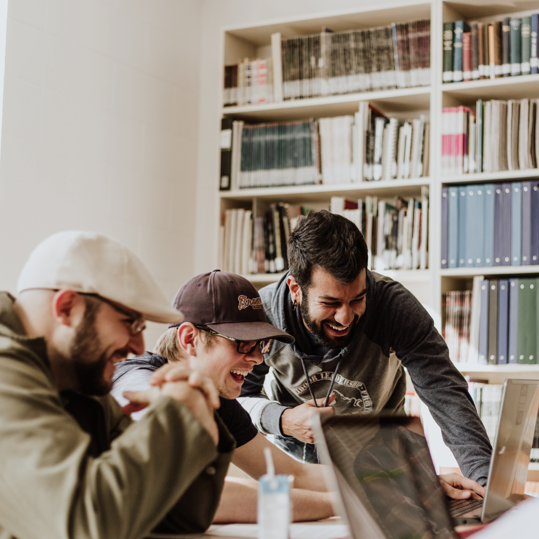