Chiller Epoxy Coating Market Size, Production, Sales, Average Product Price, Market Share, Import vs Export
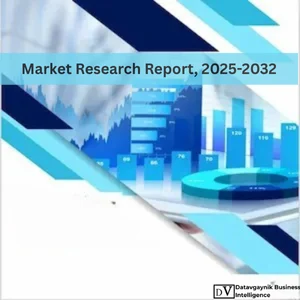
- Published 2025
- No of Pages: 120+
- 20% Customization available
Global Chiller Epoxy Coating Market: Rising Demand from Industrial and HVAC Infrastructure
The Chiller Epoxy Coating Market is witnessing a substantial surge in global demand, driven by the rapid expansion of industrial infrastructure and the growing emphasis on efficient HVAC systems. For instance, as global commercial construction spending exceeded USD 5.8 trillion in 2024, the need for durable and corrosion-resistant coatings for chillers has scaled accordingly. Chillers are critical components in commercial buildings, data centers, hospitals, and manufacturing plants, and epoxy coatings are indispensable for enhancing their operational efficiency and extending lifecycle. This demand has translated into a robust compound annual growth rate (CAGR) of over 7.2% for the Chiller Epoxy Coating Market, particularly across regions with rapid urban development and industrialization.
Energy-Efficient Cooling Solutions Driving the Chiller Epoxy Coating Market
One of the strongest drivers in the Chiller Epoxy Coating Market is the global transition toward energy-efficient cooling systems. Epoxy coatings improve thermal transfer by minimizing fouling and scaling in chiller coils, thus maintaining peak thermal conductivity over time. For example, buildings using coated chillers have reported a 12–15% improvement in energy efficiency. As global energy consumption by HVAC systems continues to account for over 40% of total building energy use, these coatings offer a direct path to both environmental compliance and cost savings. In turn, epoxy coatings are increasingly viewed not just as protective barriers, but as performance-enhancing components in energy-sensitive sectors.
Datavagyanik also covers related markets such as the Petrochemical Chiller Systems Market, the Epoxy Polymers Market, and the Epoxy Resin Market. They create a more holistic picture of the ecosystem in which the primary topic exists, including technological shifts and market demands.
Corrosion Resistance and Durability Fueling Chiller Epoxy Coating Market Growth
In industries exposed to high moisture, aggressive chemicals, and fluctuating temperatures, equipment reliability hinges on corrosion prevention. The Chiller Epoxy Coating Market benefits immensely from this requirement. For instance, pharmaceutical and food processing sectors—which collectively represent over USD 2.1 trillion in annual global revenues—operate within stringent hygiene and operational standards. Epoxy coatings protect chillers in these environments, significantly reducing downtime and the need for frequent equipment replacements. In harsh marine and offshore applications, where saltwater exposure accelerates degradation, epoxy-coated chillers last up to 40% longer than non-coated alternatives. This kind of durability is increasingly becoming non-negotiable across high-capital industries.
Data Center Expansion Enhancing the Scope of Chiller Epoxy Coating Market
The expansion of data centers globally is another compelling growth vector for the Chiller Epoxy Coating Market. As of 2024, the global data center construction market surpassed USD 270 billion and is projected to grow at over 8% CAGR. Chillers are central to maintaining optimal thermal environments in server facilities, and any reduction in cooling efficiency can lead to costly downtimes. Epoxy coatings used in chillers ensure stable performance by minimizing internal corrosion and thermal inefficiency, critical for high-load environments like hyperscale data centers. The increasing installation of edge computing infrastructure in urban locations further amplifies the market’s upward trajectory.
Sustainability Regulations Reshaping the Chiller Epoxy Coating Market
Stricter environmental policies around VOC (Volatile Organic Compound) emissions and industrial waste management are reshaping product formulations within the Chiller Epoxy Coating Market. Regulatory frameworks such as the EU’s Green Deal and U.S. EPA regulations are pushing manufacturers to innovate low-VOC, water-based, and bio-based epoxy coatings. For example, over 55% of new formulations introduced in the market in 2023 were compliant with low-VOC standards. These shifts are not merely about compliance but also align with consumer and business expectations around sustainable building materials. As a result, companies investing in green coating technologies are not only capturing regulatory alignment but also market preference.
“Track Country-wise Chiller Epoxy Coating Production and Demand through our Chiller Epoxy Coating Production Database”
-
-
- Chiller Epoxy Coating production database for 20+ countries worldwide
- Country-wise Chiller Epoxy Coating production capacity and production plant mapping
- Chiller Epoxy Coating production plants and production plant capacity analysis for key manufacturers
-
Technological Advancements Accelerating Chiller Epoxy Coating Market Innovation
The Chiller Epoxy Coating Market has seen rapid technological evolution, particularly with the integration of nanotechnology, self-healing materials, and antimicrobial additives. For example, coatings using nano-silica compounds have demonstrated up to 3x improvement in chemical resistance and adhesion properties compared to conventional epoxy coatings. In healthcare environments, antimicrobial epoxy coatings have reduced biofilm formation on chillers by over 60%, proving especially valuable in hospitals and pharmaceutical plants. These innovations are enabling coatings to perform multiple functions—protection, hygiene maintenance, and thermal management—thus expanding the market’s applicability across critical industries.
Industrial and Manufacturing Sector Expansion Boosting Chiller Epoxy Coating Market
Industrial growth across sectors such as automotive, chemicals, electronics, and food processing is significantly bolstering demand in the Chiller Epoxy Coating Market. In particular, the global automotive manufacturing industry, valued at over USD 3.4 trillion, requires robust chiller systems for assembly plants and testing facilities. Similarly, the specialty chemicals sector, which has grown by 5.5% annually over the past three years, demands high-performance chillers capable of withstanding corrosive environments. Epoxy coatings in such settings not only prevent chemical attacks but also provide insulation, enabling chillers to function optimally under aggressive operational conditions.
High-Performance Coatings Transforming the Competitive Landscape
The push for performance coatings with multifunctional attributes is redefining competitive strategies in the Chiller Epoxy Coating Market. Leading manufacturers are prioritizing R&D investments in self-cleaning, thermal-insulating, and quick-curing formulations. For example, new epoxy systems with hybrid silicone-modified structures have improved heat resistance by 20–30%, making them suitable for extreme climate zones and high-load industrial applications. Additionally, coatings with embedded smart sensors that monitor wear and temperature in real-time are moving from labs to market pilots. These high-performance offerings are not only differentiating brands but are also commanding premium pricing in B2B markets.
Urbanization and Commercial Infrastructure Development Driving Market Expansion
As urbanization accelerates—especially in regions like Asia Pacific, where over 700 million people are expected to move into cities by 2035—the demand for cooling systems in high-rise buildings, malls, airports, and hospitals is set to soar. This directly fuels growth in the Chiller Epoxy Coating Market. For instance, in 2024 alone, over 1.5 billion square meters of new commercial construction was undertaken globally. Each facility requiring centralized HVAC systems creates multiple chiller application points. Protective coatings are essential not only for efficiency but also for reducing the maintenance burden in these high-use public and commercial buildings.
Retrofitting and Upgradation: A Lucrative Segment in Chiller Epoxy Coating Market
A significant portion of demand in the Chiller Epoxy Coating Market is emerging from retrofitting projects aimed at upgrading older HVAC systems. For example, nearly 35% of installed chillers in North America are over 15 years old, presenting a prime opportunity for epoxy coating applications that enhance energy efficiency and extend usable life. Facility managers and property owners are increasingly choosing coatings as a cost-effective alternative to full equipment replacement. This trend is especially pronounced in developed markets where infrastructure is aging but sustainability mandates discourage wasteful disposal.
Conclusion: Structural Momentum Anchoring the Chiller Epoxy Coating Market
From energy efficiency mandates to industrial durability needs, the Chiller Epoxy Coating Market is being propelled by multi-sectoral forces. Its role as an enabler of performance, sustainability, and cost reduction across HVAC systems makes it a strategic investment area. The convergence of technological innovation, regulatory push, and end-user demand is not only expanding market size but also redefining product expectations. As industries evolve and urban spaces grow denser, epoxy-coated chillers will form the backbone of resilient and efficient cooling infrastructure worldwide.
North America Leading Innovation and Adoption in Chiller Epoxy Coating Market
The United States and Canada are positioned as global leaders in the Chiller Epoxy Coating Market, not only due to their advanced industrial base but also their emphasis on sustainability and innovation. For example, over 68% of commercial HVAC systems installed in U.S. federal buildings are now retrofitted or built with coated chillers. These coatings are critical in achieving long-term energy efficiency, meeting stringent Environmental Protection Agency (EPA) regulations, and reducing HVAC lifecycle costs. In addition, leading North American manufacturers are integrating nanotechnology into epoxy coatings to enhance chemical resistance and thermal stability—features that are essential in pharmaceutical and semiconductor facilities.
Canada, though smaller in terms of industrial capacity, is witnessing increased investments in smart buildings and green infrastructure, which directly supports the Chiller Epoxy Coating Market. With government incentives for energy-efficient retrofits, epoxy-coated chillers are becoming a standard in new commercial developments. The growing presence of data centers, particularly in Toronto and Vancouver, further underscores the importance of high-performance coatings to maintain critical cooling efficiency.
Europe’s Regulatory Push Accelerating Demand in Chiller Epoxy Coating Market
Europe’s leadership in environmental regulation is significantly accelerating the adoption of sustainable solutions in the Chiller Epoxy Coating Market. Countries such as Germany, France, and the United Kingdom have enacted policies mandating the use of low-VOC materials in industrial applications, creating a strong shift toward water-based and bio-based epoxy coatings. For example, Germany alone accounted for more than 22% of Europe’s total chiller epoxy coating consumption in 2024, primarily driven by its automotive and pharmaceutical industries.
France is showing a rapid uptake in public and private sector facilities aiming for LEED or BREEAM certifications. In these green-certified projects, epoxy coatings that contribute to energy efficiency and reduced emissions are favored, directly benefitting the Chiller Epoxy Coating Market. Meanwhile, the UK’s booming data infrastructure—now home to over 500 mid-sized and hyperscale data centers—continues to demand thermally efficient, corrosion-resistant coatings for HVAC systems.
Asia Pacific Emerging as a Global Production and Consumption Hub in Chiller Epoxy Coating Market
Asia Pacific has become the fastest-growing region in the Chiller Epoxy Coating Market, backed by massive industrial expansion and the regional focus on manufacturing competitiveness. China leads in both production and consumption, with over 45% of new commercial building projects in 2024 using epoxy-coated chillers. The rise of advanced manufacturing parks and mega data centers in provinces such as Guangdong and Jiangsu has triggered extensive demand for long-lasting and energy-efficient cooling solutions.
India, meanwhile, is experiencing a strong surge in domestic production of chiller epoxy coatings. Local manufacturers are responding to the booming HVAC demand in sectors like food processing and pharmaceuticals—industries that are projected to grow at 9–11% annually. For instance, in India’s pharmaceutical hubs such as Hyderabad and Ahmedabad, temperature-sensitive production environments require highly durable, antimicrobial epoxy coatings.
South Korea and Japan are contributing high-end innovation in the Chiller Epoxy Coating Market, particularly in the area of self-healing and nano-enhanced coatings. These advanced formulations are being adopted in cleanroom facilities, semiconductor fabs, and healthcare centers, where performance and hygiene are critical.
Middle East and Africa Prioritizing Durable Cooling Systems in Chiller Epoxy Coating Market
The Chiller Epoxy Coating Market in the Middle East and Africa is gaining traction due to the region’s extreme climate and infrastructural developments. For example, in Gulf Cooperation Council (GCC) countries like Saudi Arabia and the UAE, where ambient summer temperatures routinely exceed 45°C, epoxy coatings are vital for maintaining chiller integrity under thermal stress. These countries are also investing heavily in hospitality and commercial real estate, such as smart cities and luxury resorts, all of which require high-efficiency HVAC systems.
In Africa, nations like South Africa, Kenya, and Nigeria are gradually increasing their reliance on epoxy-coated chillers, especially in healthcare, food processing, and industrial zones. Local demand is being met through both imports and emerging domestic production capabilities focused on cost-effective, long-lasting coating solutions.
Latin America Witnessing Growth in Infrastructure and Chiller Epoxy Coating Demand
Latin America’s expanding commercial infrastructure is creating fresh demand in the Chiller Epoxy Coating Market. Brazil and Mexico are leading this transformation, with significant investments in smart buildings, cold chains, and industrial refrigeration systems. In Brazil, epoxy coatings are used extensively in food storage and retail chains, where temperature consistency and equipment durability are non-negotiable.
Mexico’s industrial hubs, particularly in the automotive and electronics sectors, are also investing in coated HVAC systems to ensure resilience and performance under variable climate conditions. Furthermore, as regulatory frameworks mature across Latin America, there is a noticeable shift from solvent-based to water-based and low-VOC epoxy coatings.
“Chiller Epoxy Coating Manufacturing Database, Chiller Epoxy Coating Manufacturing Capacity”
-
-
- Chiller Epoxy Coating top manufacturers market share
- Top five manufacturers and top 10 manufacturers of Chiller Epoxy Coating in North America, Europe, Asia Pacific
- Production plant capacity by manufacturers and Chiller Epoxy Coating production data for market players
- Chiller Epoxy Coating production dashboard, Chiller Epoxy Coating production data in excel format
-
Market Segmentation by Coating Type Fueling Diverse Chiller Epoxy Coating Market Applications
The Chiller Epoxy Coating Market is segmented by type into solvent-based, water-based, and powder epoxy coatings. Each category is finding strong demand across specific applications. Solvent-based coatings, for instance, continue to dominate heavy industrial environments due to their strong adhesion and high resistance to abrasion and chemicals. These are extensively used in petrochemical and chemical plants, especially in regions with less stringent VOC regulations.
Water-based epoxy coatings are rapidly gaining favor in developed economies due to environmental mandates. These coatings are particularly relevant in healthcare, education, and food processing facilities where low emissions and hygiene are crucial. For example, water-based chiller epoxy coatings are now specified in more than 60% of hospital HVAC installations in Europe and North America.
Powder epoxy coatings, known for their superior durability and ease of application, are increasingly used in pre-coated chiller components. These coatings are widely favored in OEM production environments where mass-scale, uniform, and energy-efficient coatings are essential.
Application-Based Segmentation Highlighting Critical Demand Areas in Chiller Epoxy Coating Market
Segmenting the Chiller Epoxy Coating Market by application reveals the most dynamic growth zones. HVAC and refrigeration systems account for the largest share, driven by global building construction and retrofitting trends. These systems require reliable coatings to maintain efficiency and minimize operational disruptions caused by corrosion or fouling.
The chemical processing industry is another key application area, especially in regions with a large concentration of refineries and specialty chemical plants. These facilities require epoxy coatings that resist aggressive chemicals while ensuring thermal control in chiller components.
In the food and beverage sector, demand is rising due to heightened regulatory scrutiny and the requirement for temperature precision. Chiller epoxy coatings used in this sector must also offer resistance to bacterial growth and moisture ingress. For instance, epoxy-coated chillers have been adopted in over 75% of new dairy and beverage facilities in South Asia.
End-User Segmentation Demonstrating Diverse Demand in Chiller Epoxy Coating Market
The Chiller Epoxy Coating Market is segmented by end-user into industrial, commercial, and residential sectors. The industrial sector dominates with the highest consumption, particularly in manufacturing, petrochemical, and electronics industries. These sectors often operate in harsh environments and require coatings that enhance equipment resilience and reduce unplanned downtimes.
The commercial sector, encompassing malls, hotels, hospitals, and office complexes, represents a fast-growing segment. With the global push for green buildings and smart infrastructure, chiller epoxy coatings are being integrated into HVAC systems to meet energy benchmarks and compliance standards.
Although the residential sector holds a smaller share, it is expanding, especially in high-rise urban developments across Asia and Latin America. In these projects, central HVAC systems are coated with eco-friendly epoxies that meet building codes focused on air quality and emission standards.
Technology-Based Segmentation Advancing Innovation in Chiller Epoxy Coating Market
Technological innovation is reshaping the Chiller Epoxy Coating Market, with segmentation into conventional, nanotechnology-based, and smart epoxy coatings. Conventional epoxy coatings remain in widespread use for general industrial applications due to their cost-effectiveness and reliability.
Nanotechnology-based coatings, however, are quickly gaining traction, particularly in high-tech industries such as aerospace, semiconductor manufacturing, and pharmaceuticals. These coatings offer enhanced barrier protection, self-healing abilities, and superior heat resistance, making them ideal for mission-critical chiller systems.
Smart epoxy coatings, which include antimicrobial, anti-static, and self-cleaning properties, are increasingly used in hospitals, food processing, and cleanroom environments. These coatings improve hygiene, reduce contamination risk, and contribute to compliance with international health and safety standards.
Geographical Diversification Driving Strategic Expansion in Chiller Epoxy Coating Market
The global dispersion of demand across continents is creating an urgent need for geographically diversified production strategies in the Chiller Epoxy Coating Market. Manufacturers are investing in local production units and distribution networks to overcome supply chain challenges and meet regional standards.
For instance, companies operating in Asia are leveraging cost advantages and rapid urbanization to scale exports to the Middle East and Africa. Meanwhile, North American firms are focusing on product innovation and sustainability to strengthen their position in the premium segment.
As local regulatory frameworks mature and industrial needs evolve, regional customization of formulations is becoming a competitive differentiator. The ability to align with geography-specific demands—whether in terms of climate resistance, chemical tolerance, or eco-credentials—is driving market leadership and long-term brand loyalty.
Major Manufacturers Dominating the Chiller Epoxy Coating Market
The chiller epoxy coating market is supported by a strong lineup of global manufacturers that offer specialized product lines designed to meet the unique demands of industrial and commercial cooling systems. These companies have invested in advanced coating technologies, expanded production capacity, and aligned with sustainability requirements to remain competitive in this rapidly evolving landscape.
PPG Industries
PPG Industries is a key player in the chiller epoxy coating market, known for its wide range of industrial coatings. The company’s PPG PSX epoxy line is widely used for high-durability applications, including chiller components exposed to aggressive environmental conditions. These coatings offer excellent corrosion resistance, chemical stability, and thermal protection. PPG has a strong presence across North America, Europe, and Asia, and continues to innovate with low-VOC and water-based epoxy coatings tailored for HVAC and refrigeration systems.
AkzoNobel
AkzoNobel is another major manufacturer contributing significantly to the chiller epoxy coating market with its Intergard and Resicoat product ranges. The Resicoat line, in particular, is known for high-performance epoxy powder coatings used in heat exchangers, condensers, and evaporators. These coatings offer excellent adhesion, wear resistance, and thermal efficiency. AkzoNobel’s ongoing commitment to sustainability and circularity has led to the development of epoxy coatings with improved lifecycle performance and minimal environmental impact.
Sherwin-Williams
Sherwin-Williams holds a leading position in the chiller epoxy coating market through its Protective & Marine Coatings division. The company’s Dura-Plate and Macropoxy lines are specifically formulated for industrial chillers, HVAC systems, and metal surfaces that demand superior corrosion protection. These coatings have gained wide adoption in pharmaceutical plants, food processing facilities, and marine applications. Sherwin-Williams also emphasizes environmentally friendly coatings, with a growing portfolio of low-emission products.
Jotun Group
Jotun’s presence in the chiller epoxy coating market is marked by its Jotamastic and Penguard ranges, which are designed to withstand extreme industrial environments. These coatings are commonly applied on condenser coils and chiller exteriors in high-humidity, saltwater, or chemical exposure conditions. Jotun has built a strong presence in the Middle East, Asia Pacific, and Europe, serving industrial facilities, commercial infrastructure, and energy sectors where robust chiller performance is essential.
Axalta Coating Systems
Axalta is actively expanding in the chiller epoxy coating market through its Alesta and Nap-Gard product families. Nap-Gard epoxy powder coatings, in particular, are used for thermal and corrosion protection of HVAC system components. These coatings are engineered to provide superior resistance to high-pressure, high-temperature, and chemically aggressive environments. Axalta is also leading in the development of eco-conscious formulations with reduced environmental impact.
Valspar (now part of Sherwin-Williams)
As a legacy brand under Sherwin-Williams, Valspar’s Industrial Coatings division continues to influence the chiller epoxy coating market. Valspar offers a variety of epoxy coatings tailored for thermal conductivity and corrosion resistance. These coatings are widely used in manufacturing facilities, food storage units, and commercial buildings where long-term equipment reliability is a priority. Valspar’s product development continues to focus on efficiency, quick cure times, and compliance with regulatory standards.
Kansai Paint Co., Ltd.
Kansai Paint is expanding its footprint in the chiller epoxy coating market, particularly in Asia. The company’s epoxy coating systems are formulated for chillers used in energy plants, automotive factories, and electronics facilities. Kansai’s products are recognized for excellent mechanical strength, heat resistance, and anti-fouling properties. The company is also exploring self-healing and antibacterial epoxy coatings for use in cleanroom and food-grade environments.
Berger Paints
Berger Paints serves the chiller epoxy coating market primarily in India and Southeast Asia, providing durable coatings for industrial HVAC systems. Berger’s Epilux epoxy product line is known for its corrosion resistance and performance under humid and chemical-laden conditions. These coatings are used in commercial real estate, cold storage, and institutional projects. Berger is investing in eco-friendly product development and expanding its distribution network to meet rising demand.
Nippon Paint Holdings
Nippon Paint is increasingly active in the chiller epoxy coating market, focusing on industrial and marine applications. Its Nippe series includes a range of epoxy coatings designed for heavy-duty performance in harsh environmental conditions. Nippon Paint is also investing in water-based epoxy technology and hybrid formulations that combine epoxy with polyurethane to improve flexibility and durability.
RPM International Inc.
RPM International operates in the chiller epoxy coating market through subsidiaries such as Carboline and Rust-Oleum. Carboline’s epoxy systems are particularly suited for chemical plants, HVAC systems, and structural steel protection. The company’s Fusion Bonded Epoxy (FBE) coatings are widely used for metal chiller components due to their excellent adhesion and corrosion resistance. RPM’s network across North America and Europe allows it to serve large infrastructure and industrial clients.
Hempel Group
Hempel is a globally recognized name in the industrial coatings sector, and it plays a significant role in the chiller epoxy coating market with products like Hempadur. These coatings offer high film-build capabilities, enabling protection of chillers exposed to salt spray, chemical fumes, and mechanical abrasion. Hempel has a strong market presence in offshore oil and gas, shipping, and heavy industries—all sectors where reliable cooling systems are essential.
BASF Coatings
BASF has introduced epoxy coatings as part of its broader performance materials business. Although not as heavily focused on HVAC systems, BASF’s industrial epoxy formulations are gaining traction in the chiller epoxy coating market, particularly in large-scale energy and manufacturing facilities. The company’s research into thermally conductive and low-friction coatings is aligned with market demands for enhanced chiller performance and heat transfer efficiency.
Asian Paints PPG Pvt Ltd
A joint venture between Asian Paints and PPG Industries, this entity offers epoxy solutions tailored for the Indian subcontinent. The company’s product lines cater to industrial chillers in food processing, textile, and power generation sectors. With a focus on affordable, high-performance coatings, Asian Paints PPG is becoming a regional leader in the chiller epoxy coating market.
“Chiller Epoxy Coating Production Data and Chiller Epoxy Coating Production Trend, Chiller Epoxy Coating Production Database and forecast”
-
-
- Chiller Epoxy Coating production database for historical years, 10 years historical data
- Chiller Epoxy Coating production data and forecast for next 7 years
-
Recent Industry Developments and News Highlights in the Chiller Epoxy Coating Market
January 2024 – AkzoNobel launched its next-generation Intergard 2800 series, a low-VOC epoxy coating targeting HVAC applications. This formulation enhances thermal insulation while complying with new EU environmental standards.
March 2024 – Jotun Group announced expansion of its India manufacturing plant to meet rising demand in South Asia for industrial and HVAC coatings. The plant includes new R&D capabilities focused on powder epoxy coatings.
June 2024 – Sherwin-Williams introduced Macropoxy 920, a fast-curing, solvent-free epoxy coating designed for rapid deployment in retrofitting projects. It has already been adopted in several U.S. federal building renovations.
August 2024 – Axalta Coating Systems unveiled a smart epoxy coating embedded with sensor technology to monitor corrosion and surface temperature in real time. It is undergoing pilot testing in several data centers in Europe.
October 2024 – BASF Coatings entered a research partnership with a semiconductor manufacturer in Japan to develop antimicrobial and thermally conductive epoxy coatings for precision cooling applications.
These developments reflect the pace at which the chiller epoxy coating market is evolving to meet modern industrial demands. With advanced product launches, regional expansions, and sustainability initiatives shaping the competitive landscape, the market is entering a phase of strong innovation and global alignment. Let me know if you’d like the final outlook and challenges section next.
Market Scenario, Demand vs Supply, Average Product Price, Import vs Export, till 2035
- Global Chiller Epoxy Coating Market revenue and demand by region
- Global Chiller Epoxy Coating Market production and sales volume
- United States Chiller Epoxy Coating Market revenue size and demand by country
- Europe Chiller Epoxy Coating Market revenue size and demand by country
- Asia Pacific Chiller Epoxy Coating Market revenue size and demand by country
- Middle East & Africa Chiller Epoxy Coating Market revenue size and demand by country
- Latin America Chiller Epoxy Coating Market revenue size and demand by
- Import-export scenario – United States, Europe, APAC, Latin America, Middle East & Africa
- Average product price – United States, Europe, APAC, Latin America, Middle East & Africa
- Market player analysis, competitive scenario, market share analysis
- Business opportunity analysis
Key questions answered in the Global Chiller Epoxy Coating Market Analysis Report:
- What is the market size for Chiller Epoxy Coating in United States, Europe, APAC, Middle East & Africa, Latin America?
- What is the yearly sales volume of Chiller Epoxy Coating and how is the demand rising?
- Who are the top market players by market share, in each product segment?
- Which is the fastest growing business/ product segment?
- What should be the business strategies and Go to Market strategies?
The report covers Chiller Epoxy Coating Market revenue, Production, Sales volume, by regions, (further split into countries):
- Asia Pacific (China, Japan, South Korea, India, Indonesia, Vietnam, Rest of APAC)
- Europe (UK, Germany, France, Italy, Spain, Benelux, Poland, Rest of Europe)
- North America (United States, Canada, Mexico)
- Latin America (Brazil, Argentina, Rest of Latin America)
- Middle East & Africa
Table of Contents:
- Introduction to the Chiller Epoxy Coating Market
- Overview of Chiller Epoxy Coatings and Their Importance
- Evolution of Chiller Epoxy Coating Production Technologies
- Industrial Applications and Market Relevance
- Market Scope and Segmentation of Chiller Epoxy Coating Market
- By Coating Type (Solvent-Based, Water-Based, Powder Epoxy)
- By Application (Industrial Chillers, Commercial Chillers, HVAC Systems)
- By Industry (Food & Beverage, Healthcare, Data Centers, Manufacturing, Others)
- By End-User (OEMs, Aftermarket Coatings)
- Key Trends Driving the Chiller Epoxy Coating Market (2025-2040)
- Innovations in Chiller Epoxy Coating Production Technologies
- Adoption of High-Performance Corrosion-Resistant Coatings
- Growing Demand for Energy-Efficient and Anti-Fouling Epoxy Coatings
- Regional Analysis of the Chiller Epoxy Coating Market
- Market Growth in North America, Europe, Asia-Pacific, Latin America, and MEA
- Impact of Regulatory Standards on Chiller Epoxy Coating Production
- Opportunities in Developing Markets for Epoxy Coatings
- North America Chiller Epoxy Coating Market
- Increasing Demand from HVAC and Industrial Cooling Sectors
- Key Manufacturers and Their Expansion Strategies
- Growth of Sustainable and High-Durability Coating Solutions
- Europe Chiller Epoxy Coating Market
- Impact of Stringent Environmental Regulations on Coating Production
- Technological Innovations in Anti-Corrosion Chiller Epoxy Coatings
- Competitive Market Landscape and Key Players
- Asia-Pacific Chiller Epoxy Coating Market
- Expanding Industrial and Commercial Infrastructure
- Growth of Chiller Epoxy Coating Production in China, India, and Japan
- Increasing Investment in HVAC Coating Solutions
- Latin America Chiller Epoxy Coating Market
- Emerging Demand in Manufacturing and Cold Storage Industries
- Expansion of Local Production and Market Penetration
- Challenges and Opportunities for Global Suppliers
- Middle East & Africa Chiller Epoxy Coating Market
- Demand for High-Temperature and Corrosion-Resistant Coatings
- Market Growth in Oil & Gas, Data Centers, and Industrial Cooling Applications
- Long-Term Investment Opportunities for Chiller Epoxy Coating Manufacturers
- Manufacturing and Production Processes in Chiller Epoxy Coating Industry
- Key Raw Materials Used in Chiller Epoxy Coating Production
- Advances in Coating Formulations and Application Techniques
- Quality Control and Performance Testing Standards
- Competitive Landscape of Chiller Epoxy Coating Manufacturers
- Leading Companies and Their Market Strategies
- Partnerships, Acquisitions, and Product Development Trends
- Innovations Driving Competitive Advantage
- Supply Chain and Production Analysis of Chiller Epoxy Coating Market
- Global Raw Material Sourcing and Distribution Channels
- Challenges in Production Scaling and Supply Chain Efficiency
- Role of Automation in Chiller Epoxy Coating Production
- Revenue Market Share of Chiller Epoxy Coating Companies (2025-2040)
- Financial Performance of Key Players
- Market Share Breakdown by Coating Type and End-User Industry
- Future Investment and Expansion Trends
- Technological Innovations in Chiller Epoxy Coating Production
- Development of Self-Healing and Smart Epoxy Coatings
- AI and IoT Integration in Chiller Epoxy Coating Application
- Future Prospects in Nanotechnology-Based Epoxy Coatings
- Cost Structure and Pricing Trends in Chiller Epoxy Coating Market
- Raw Material Pricing and Its Market Impact
- Strategies for Cost Reduction in Coating Production
- Price Differentiation Between Premium and Standard Epoxy Coatings
- Export and Import Analysis of the Chiller Epoxy Coating Market
- Global Trade Patterns and Emerging Export Markets
- Regulatory Standards for International Distribution
- Key Regions Driving Import and Export Growth
- Consumer Demand and Market Trends in Chiller Epoxy Coatings
- Changing Preferences in Industrial and Commercial Sectors
- Growing Adoption of Eco-Friendly and High-Performance Coatings
- Role of Aesthetic and Functional Coatings in Market Expansion
- Future Outlook for Chiller Epoxy Coating Market (2025-2040)
- Forecasted Market Growth and Key Opportunities
- Innovations in Energy-Efficient and Sustainable Epoxy Coatings
- Strategic Recommendations for Industry Stakeholders
- Challenges and Risks in the Chiller Epoxy Coating Market
- Supply Chain Disruptions and Raw Material Shortages
- Regulatory Compliance and Environmental Concerns
- Market Competition and Technological Barriers
- Conclusion and Strategic Insights
- Key Takeaways from Market Research and Industry Trends
- Opportunities for Growth in Chiller Epoxy Coating Production
- Long-Term Business Strategies for Market Players
“Every Organization is different and so are their requirements”- Datavagyanik
Companies We Work With
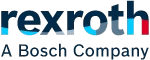
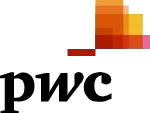
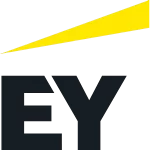
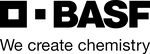
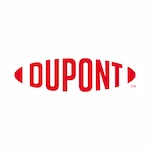

Do You Want To Boost Your Business?
drop us a line and keep in touch
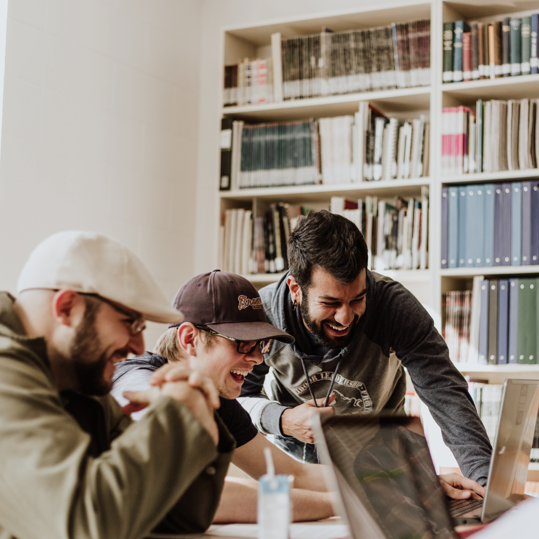